LEAN manufacturing: A solution for lean materials handling
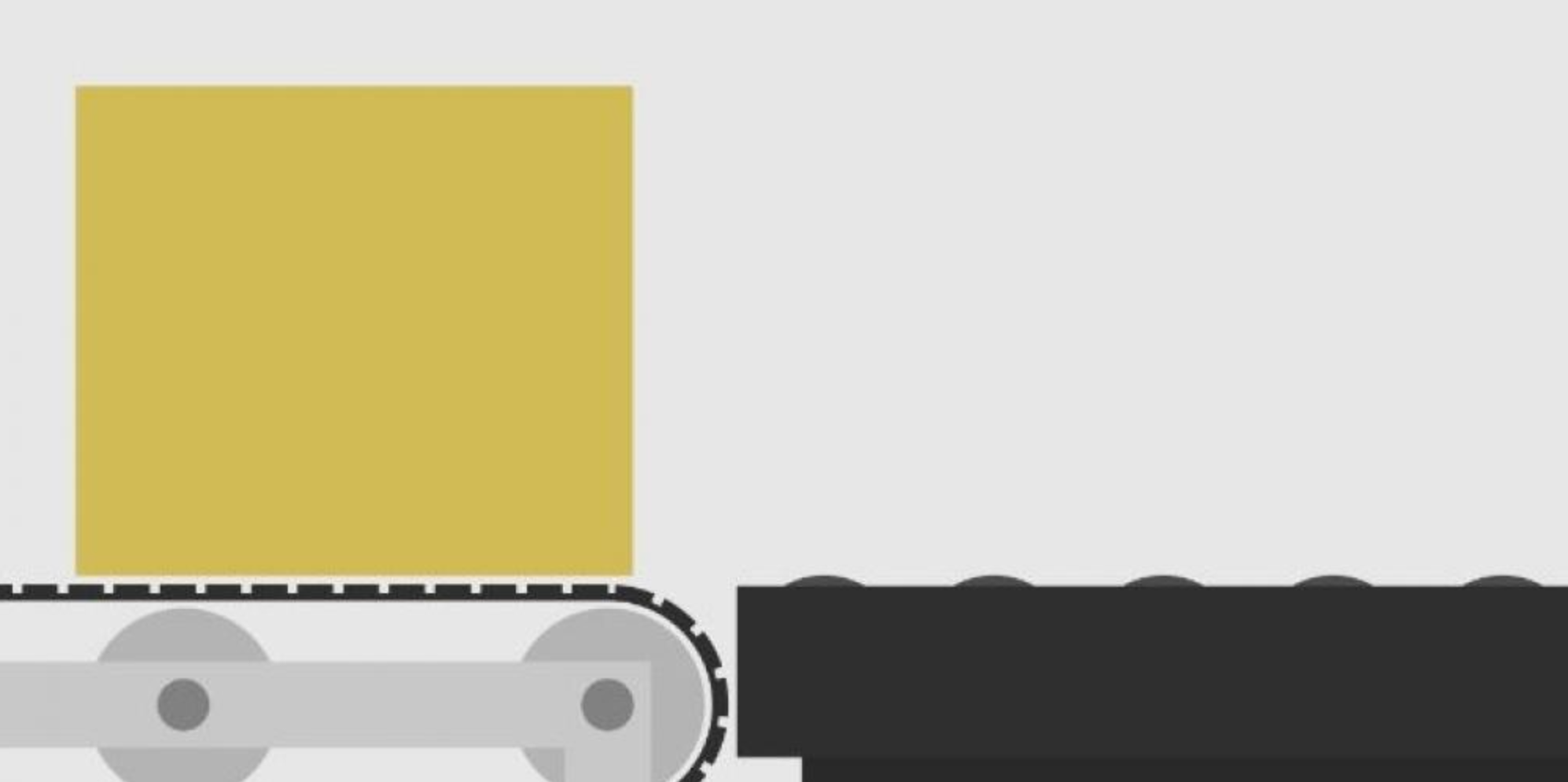
Sometimes we forget that lean manufacturing is a process and not a final destination - it can be easy to think that way. Your manufacturing operation achieved an improvement of “X” by uncovering significant areas of waste while productivity increased by “Y.” You may be pleased with this accomplishment, but the truth of it is, more change is on the way. This will require finding more waste while producing greater efficiencies.
Many drivers in today’s marketplace point to a need for improved efficiency, often through processes and principles. We all are aware of increasing global competition. But have you considered the consumer? When Henry Ford’s Model T rolled off the assembly line, Ford was quoted as saying, “A customer can have any color they want, so long as it’s black.” This approach worked for Ford 100 years ago. Modern consumers demand more—more choices, more options, and more variations.
The Change on the Manufacturing Assembly Line
As a result, manufacturers responded first by building more factories to produce the variations of each product. Then technology improved. So did competition, creating more demand for manufacturers to produce more products in different configurations and models at competitive cost. Now, it’s all housed in the same facility, even the same assembly line; it is known as “Just in Sequence.”
Multiple products manufactured on the same assembly line changes the flow of raw materials and components. The old model of bringing multiple loads of material to build the same product is fast becoming a distant memory. Today, manufacturers utilize shorter production runs using smaller quantities of material to deliver more variety more frequently. This is the new model for manufacturing in a lean world.
Unfortunately, support practices aiding movement of raw materials and components to the assembly line have not kept pace with the model. Lean manufacturing relies on an efficient flow of materials, components and finished product. Delivering a pallet with 80 items when only 30 are required violates the principles of lean. However, there are more issues.
Challenges of providing lean materials handling
Because multiple products are manufactured on the same line, more (and different) raw materials are needed faster to meet demands for shorter production runs and faster changeovers. Instead of using one pallet of materials, the line requires several. This means more frequent pickup and delivery of materials.
Adding more employees to fix the problem defeats the efficient use of personnel. Labor costs increase. It also leaves more employees navigating already congested aisles, leading to a greater potential for accidents and injury.
Another alternative currently used is automating material handling. AGVs reduce aisle congestion and improve efficiency somewhat. However, a reliance on 60-year-old technology reduces the flexibility needed for moving materials. Most AGV operate using two basic navigation methods:
- Following a path using a magnetic strip on or embedded in the floor Programming specific routes into the vehicle’s memory
- Neither allows for deviation from a fixed path. A lack of route flexibility magnifies the issue when aisle blockage occurs, forcing the AGV until someone removes the blockage, delaying delivery.
Autonomous Paradigm Shift

OTTO 100 is part of the OTTO line of autonomous mobile robots for material transport.
To eliminate these issues and still maintain a path towards continuous lean improvement, a paradigm must take the lead. Autonomous mobile robots offer an efficient option. Unlike earlier (and current) versions of AGVs, autonomous mobile robots (AMRs) are not bound to a fixed path. These vehicles learn multiple routes within a facility and adapt to changing situations, much like people. So when an obstacle blocks its path, the AMR goes around it or modifies its route to ensure on-time material delivery.
The navigation system for an autonomous mobile robot is enabled entirely in its software. Therefore, when production lines or facility layouts change, the ability to update material flow is a painless operation because all it requires is a click of the button within the software application - rather than tearing out fixed infrastructure, which is required for most traditional material handling solutions including conventional Autonomous Guided Vehicles (AGVs).
Here at Clearpath, we’ve developed the first autonomous mobile robot that is designed exclusively to align with lean material handling. It moves the principles of lean manufacturing forward by ensuring a continuous flow of product while allowing employees to work more productively.