Blog
7 advantages of one-piece flow in manufacturing
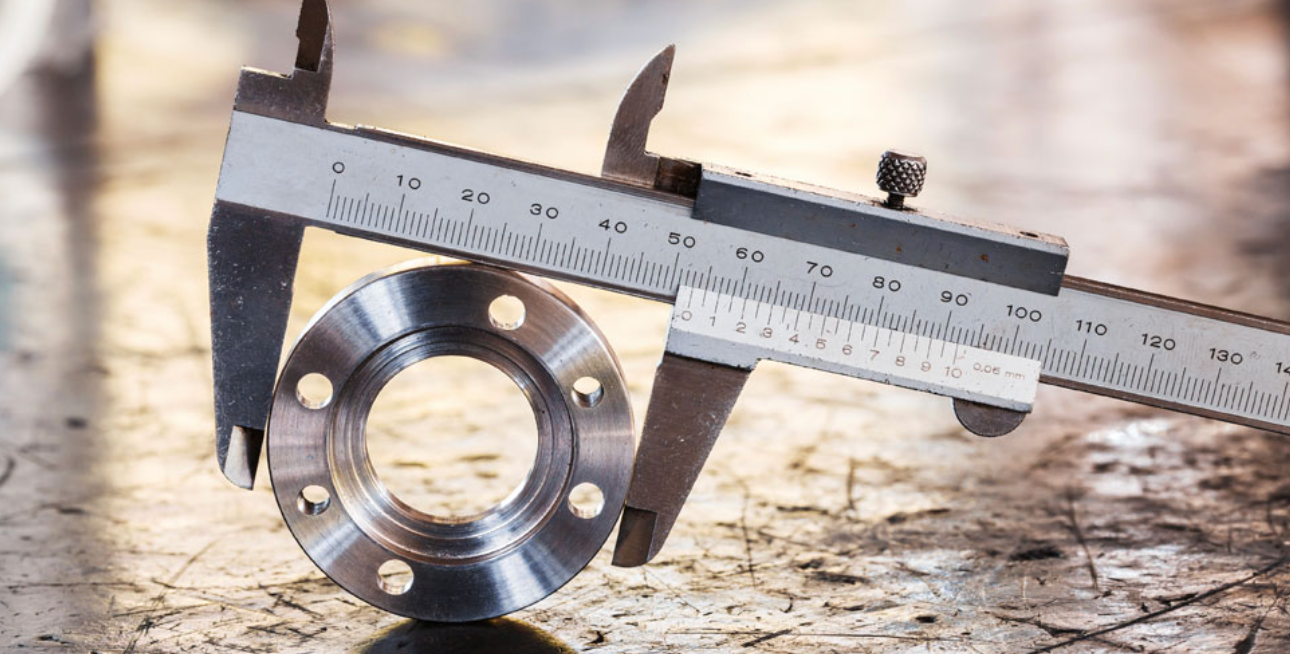
One of the most fundamental elements of creating a lean environment is operating with one-piece-flow. To think of processing one unit at a time can send a shudder through an organisation if this isn’t the norm, especially if the plant is set up and accustomed to batch production. However, when incorporated properly into your workflow and paired with the right technology to support the process, one-piece-flow manufacturing can yield significant benefits quickly.
By using automated material handling to achieve one piece flow, the elimination of waste occurs in a variety of areas. Here are seven advantages* that can be gaged from successful implementation of a lean one piece flow production process:
1. Improves quality and fewer defects in manufacturing
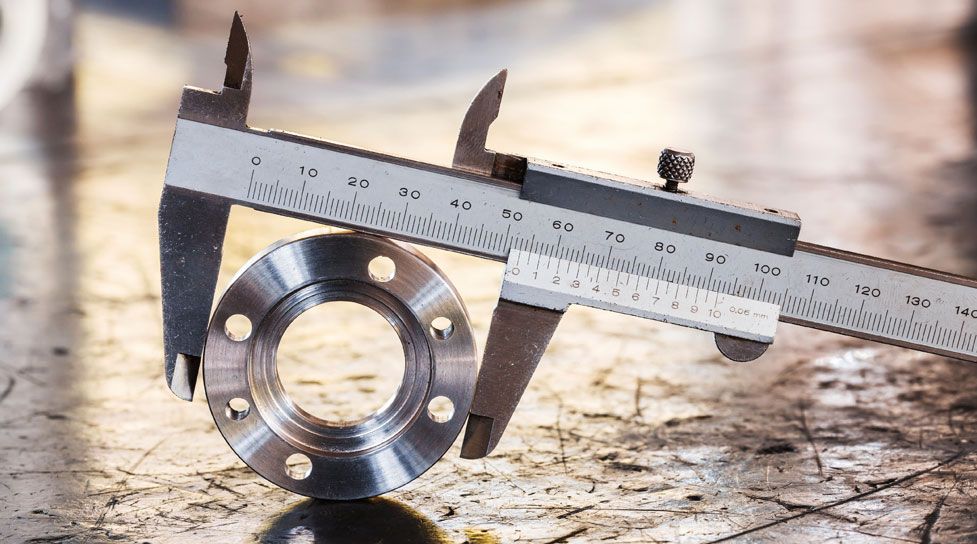
Photo credit: mfgtalkradio.com
Batch production is beneficial in certain instances, but the risk of defects is significantly higher since more inventory needs to be moved, counted, stored, and picked. With a one-piece-flow process, defects - or quality concerns - only impact a single part. Therefore, plant operators aren’t required to dedicate man-hours for testing other material in the same production run for quality issues. Rather, operators can traceback workflow for the single piece and determine corrective actions to ensure the problem won’t reoccur.
2. Reduces inventory
Each operation will only need to produce what is needed by the next operator. When followed properly and leveraging the capabilities of automated material handling, the process will eliminate any opportunity to build ahead and fall into delays.
3. Requirement for less space
As inventory levels are reduced, less space and manpower is required to manage (receive, count, stock, store, pick and delivery) it. One piece flow results in workcells with optimized equipment layout so a single operator can oversee many pieces of the equipment with minimal motion.
4. Enhances overall manufacturing flexibility
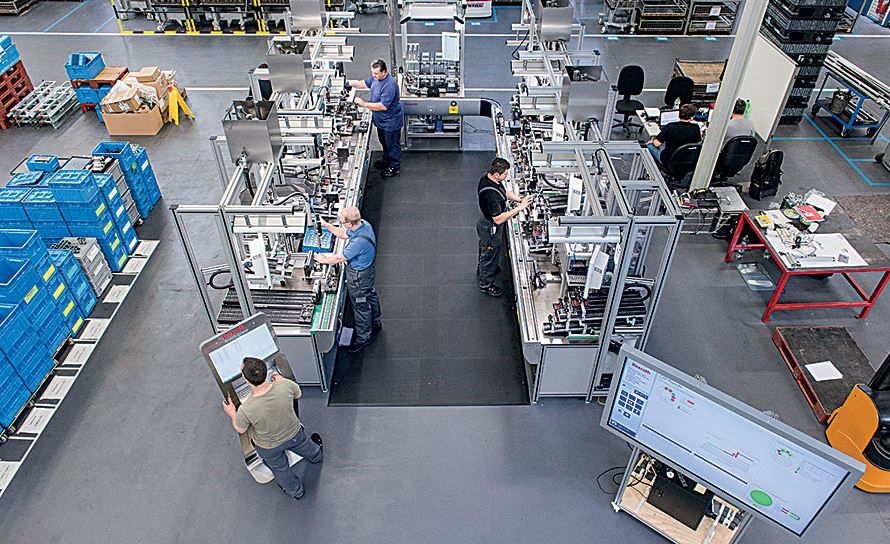
Photo credit: Assembly Magazine
Less inventory on the floor will allow lead times to drop, thereby providing more time to react to customer orders.
5. Makes identifying future Kaizen easier
Defects and WIP inventories will decrease, while issues on the shop floor will become visibly noticeable. If problems relate to takt time or WIP, for instance, it will quickly become apparent and changes can be made immediately to address them.
6. Ensures a safer work environment
Less inventory means less clutter, which provides opportunity to improve layout of equipment in the work station and the layout of the cells.
7. Improves employee morale
Production problems are identified immediately, giving workcell operators more ownership in their production area.