Blog
Boosting material handling productivity with centralized AMR integrations

Autonomous mobile robots (AMRs) achieve next-level efficiency when they are powered by a sophisticated software suite that is capable of centrally integrating with your facility’s existing software, hardware and other material handling equipment. Centralized integrations enhance operational productivity by ensuring different automation systems work together to create a fully connected operation. This simplifies monitoring and management, reduces the need for manual intervention, and ensures smooth communication between AMRs and other systems.
When you select an AMR provider that centralizes integrations, not only will you streamline deployment setup, you will also enhance daily operational efficiency and reduce downtime. Below are three integrations your chosen vendor should provide.
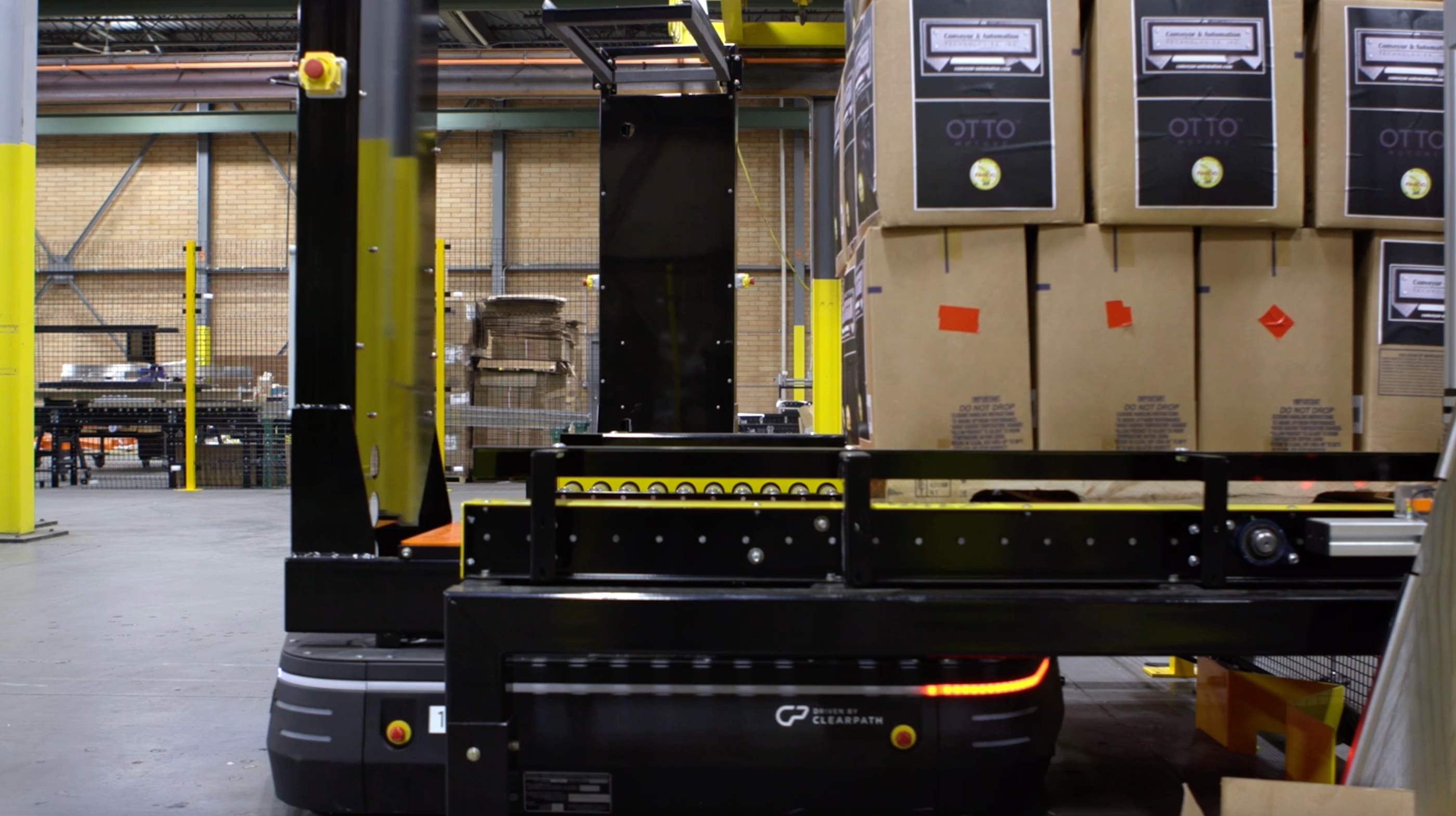
Video 1: An overview of how centralized AMR integrations transform material handling.
1. Ensure continuous productivity by connecting with your existing software
Your chosen vendor’s fleet management software should integrate with your business management systems, including your WMS, MES, and ERP, to trigger work for the AMRs. These tasks are managed through Open APIs, which facilitate communication by receiving and sending commands to ensure the right part gets to the right place at the right time. For example, business requirements may demand that a pallet comes off the conveyor every 30 seconds. By integrating this information with the fleet management software, an AMR workflow can be automatically triggered every 30 seconds, ensuring continuous productivity.
Often, when connecting the business management systems to a fleet management software, substantial custom coding is required. By selecting an advanced software that offers pre-built APIs, this requirement will be reduced, enabling you to start moving materials within days, not weeks.
To reduce setup time and simplify deployment, sophisticated software will already have much of this coding built in, capable of assigning the right robot for the right mission, finding the most efficient route, and opportunistically charging, for example. A centrally integrated system will only require you to program a trigger for mission dispatch, which can be done manually from a tablet, a computer, a button, or a pre-defined schedule. By significantly cutting overhead with extensive built-in API options, manufacturers will minimize manual work and ensure smooth operations.
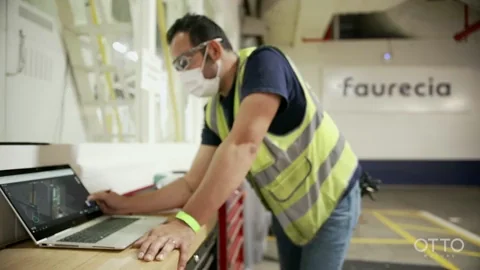
Video 2: Dispatching a mission on a laptop, tablet, and from a button.
The most sophisticated AMR vendors will offer publicly documented example code for typical scenarios.
Users can test mission creation, troubleshoot issues, and copy code directly into their integration systems, reducing setup even further and offering a practical test bed for experimentation.
2. Improve safety by communicating with existing PLCs
The fleet management software you select should also be able to communicate with your existing PLCs, without the need for additional sensors. Typically, all attachments on AMRs will have sensors, and all endpoints in a facility, like conveyors, will have them too. These sensors help the robots understand when and how to transfer a payload. In some cases, AMR vendors opt to add additional sensors to their robots, attachments, and endpoints to compensate for the complexities of integrating with existing PLCs. While this approach can simplify deployment in the short term, each sensor added means more infrastructure and setup time during deployment, and as you scale the solution, this problem worsens.
The vendor you select should have an appliance proxy that directly communicates with existing PLCs in your facility, eliminating the need to install additional sensors.
This reduces setup time, simplifies integration and ensures payload transfers are safe. For example, if there’s a misalignment between the AMR’s attached conveyor and the facility’s fixed conveyor, and the PLCs do not catch this, causing the belt to keep rolling, damage can be caused to the product, the facility’s equipment, and most importantly, a nearby operator. The appliance proxy will provide a real-time communication channel between the facility PLC and the attachment’s PLC to transfer payloads safely and efficiently.
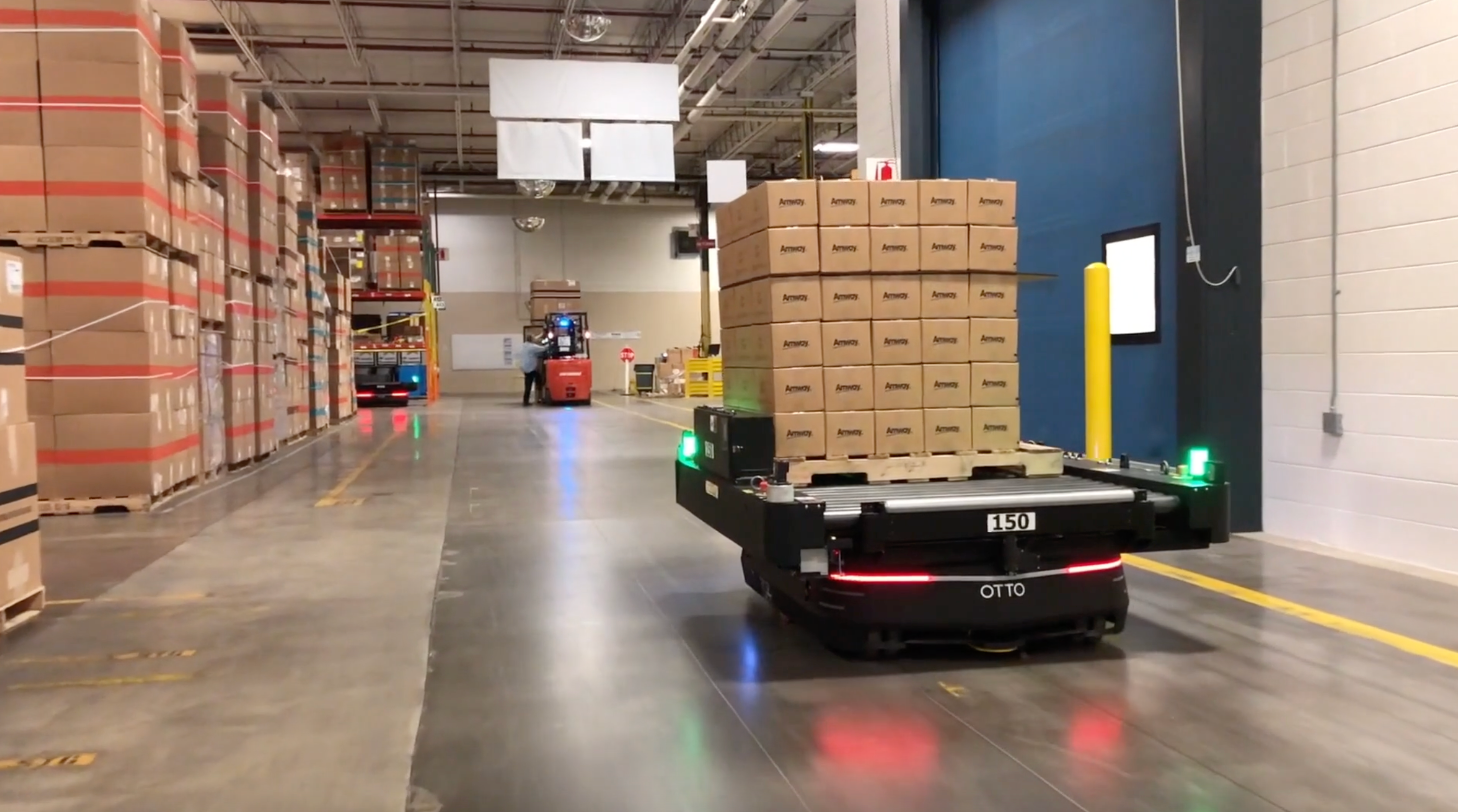
Video 3: PLC integration in action at Amway, a consumer packaged goods company that used AMRs to transport finished goods from the production line to the shrink wrap, then to shipping.
3. Collaborate seamlessly with other material handling systems
Facilities often require different material handling solutions across their operation to meet unique goals. The chosen software should enable your facility to collaborate with different vendors on different workflows.
Your vendor should be capable of communicating with other material handling robots, such as AGVs and AMRs from other vendors.
For example, through an on-board VDA5050 connector, OTTO can interpret information from a supported third-party fleet manager to establish a common interface, without custom integration work.
As one of the first AMR providers to support the VDA5050 interoperability standard, OTTO helps manufacturers reduce integration costs, improve flexibility and increase productivity by enabling the use of multiple material handling solutions in one facility.
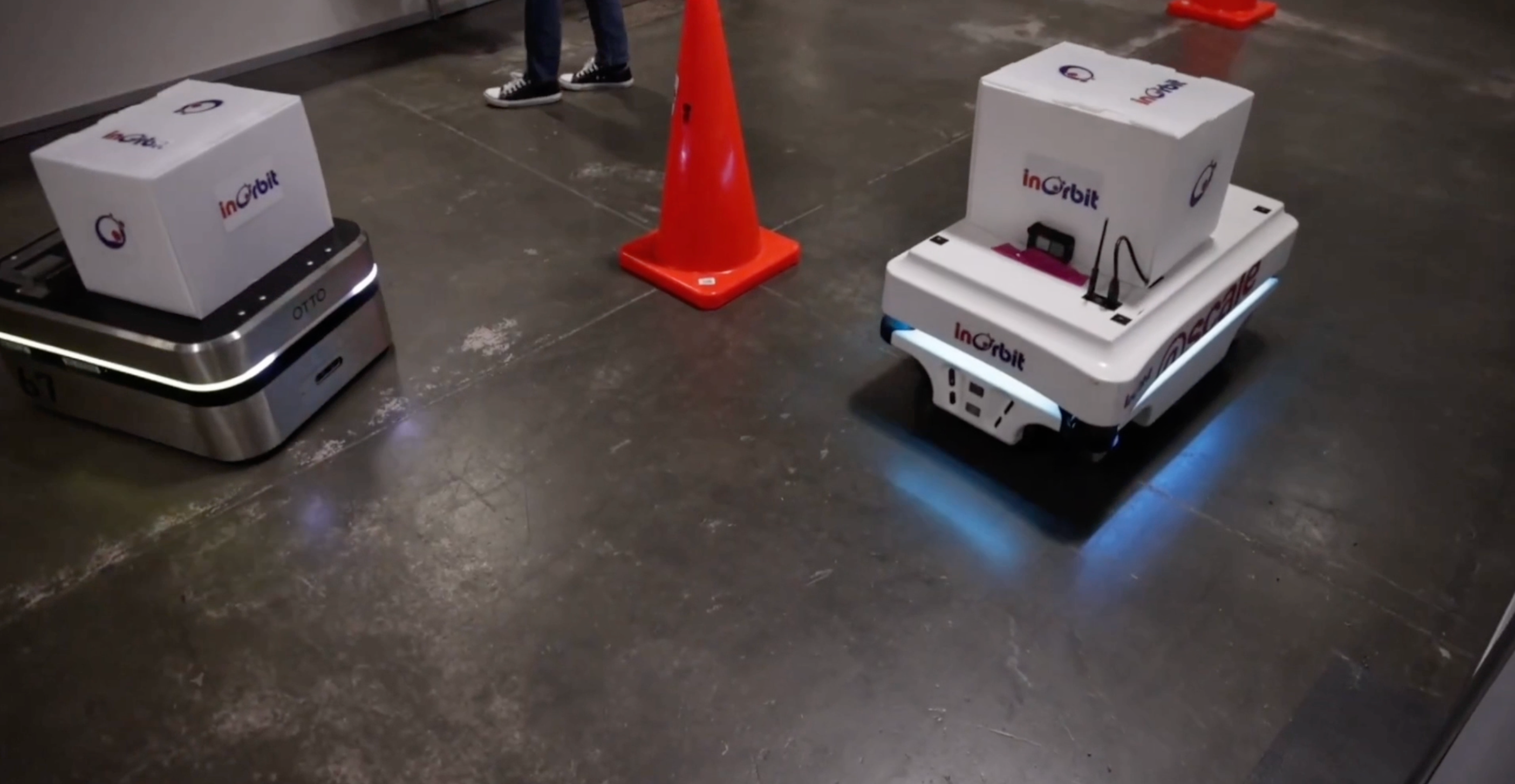
Video 4: Demonstrating the standard in action. In this video, A VDA5050-compliant AMR, OTTO 100, is remotely controlled by a third-party controller from InOrbit. In order to reduce disruption to traffic flow, the AMR is instructed to temporarily halt via a VDA5050 command and is soon released to resume its task when the AGV is clear of the aisle.
Seamless facility integration is helping leading manufacturers achieve next-level efficiency. To learn more about the importance of simple integration and other key considerations when evaluating AMR software, watch the webinar, “The essential role of software for successful AMR deployments.”
Subscribe to our newsletter
Stay in the loop on product news, case studies, upcoming events and more.