Blog
The move to a connected factory
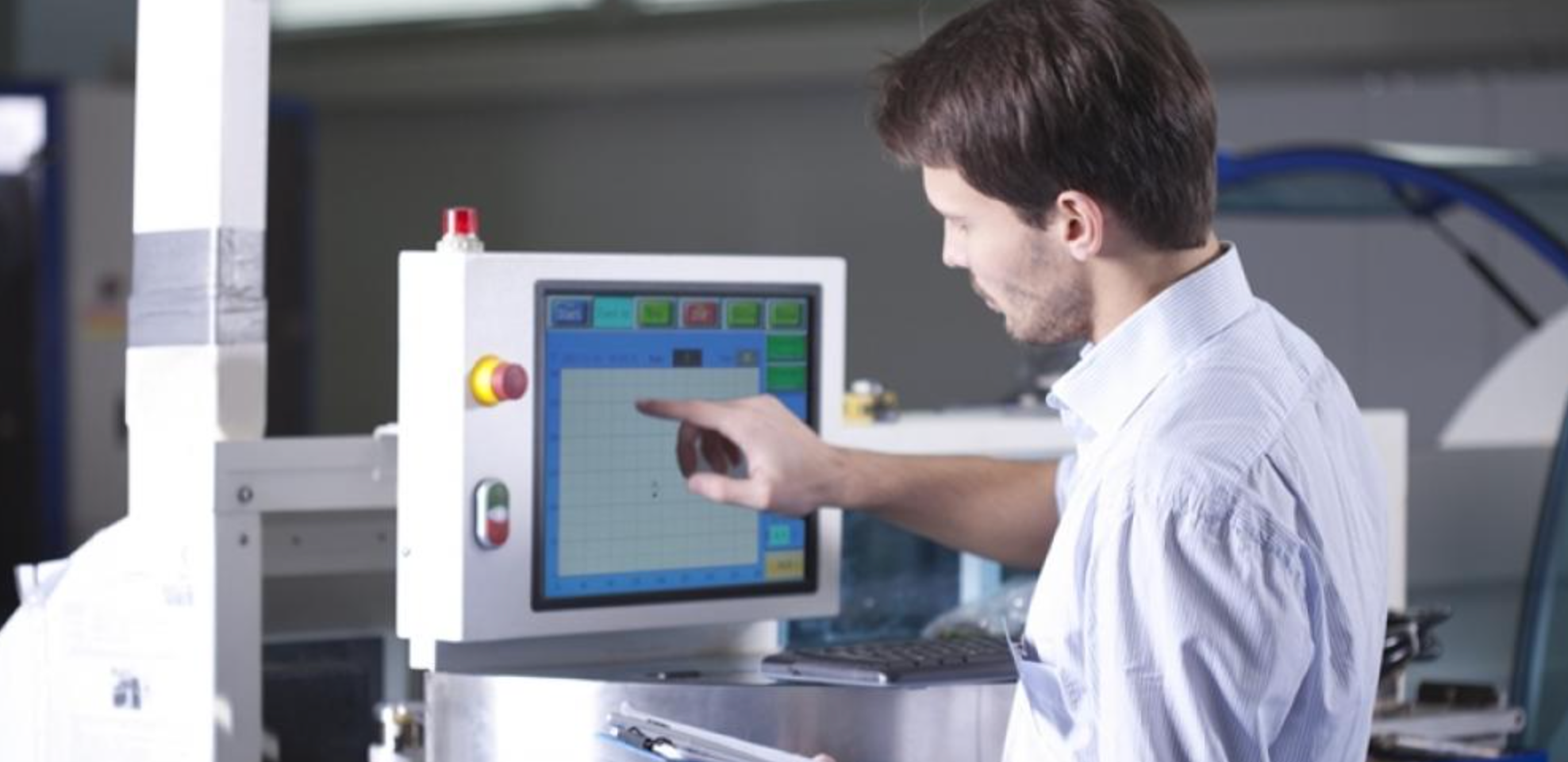
Many of today’s customers want customized products, which does not always make for a cost-efficient manufacturing process. Automation technology allows businesses to meet customers’ demands by integrating the entire process from receiving the orders to delivery confirmation. This integrated approach is known as a connected factory, or Industry 4.0. Manufacturers are able to analyze data to troubleshoot issues, find bottlenecks, and reduce costs with the implementation of a connected manufacturing.
What is a connected factory?
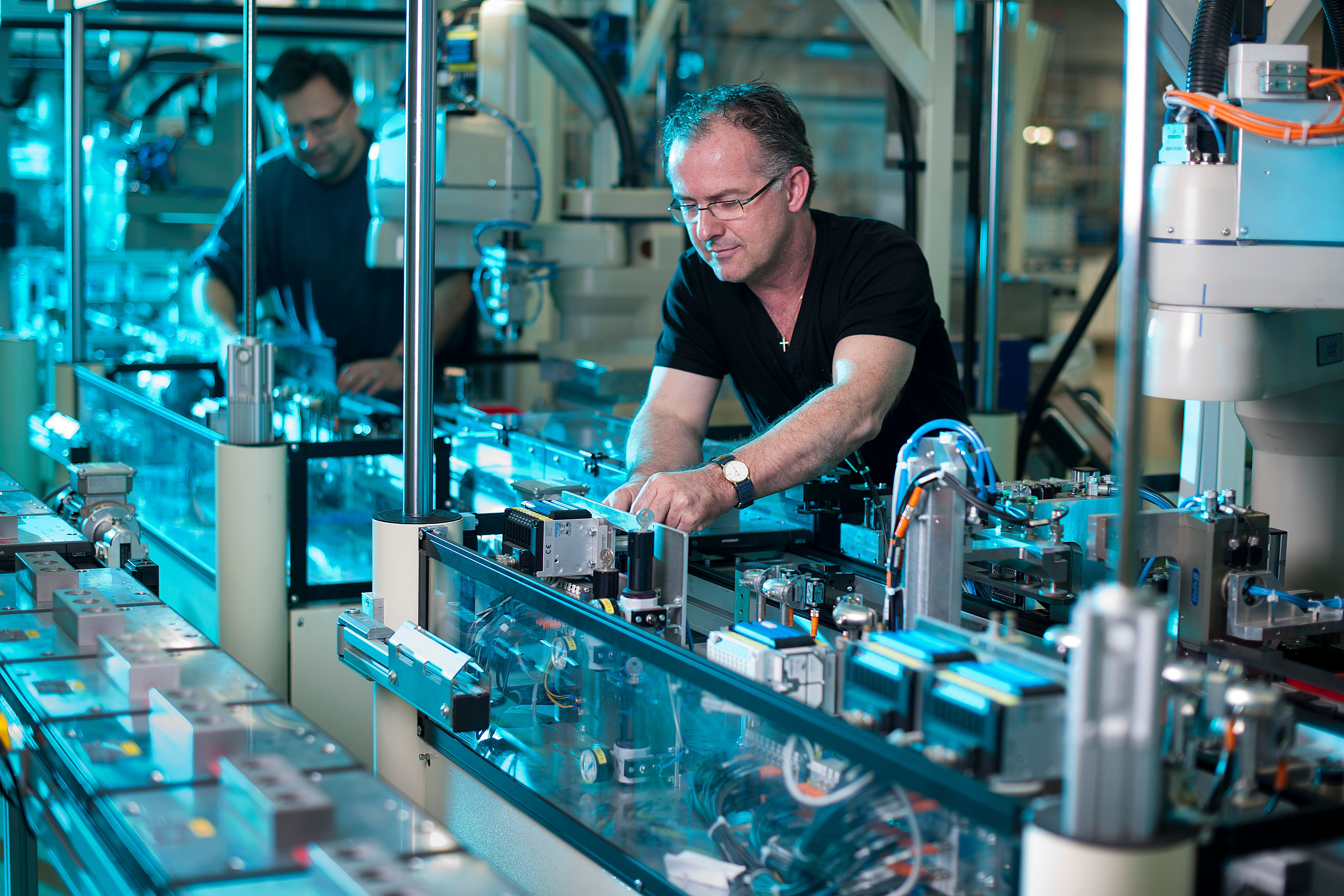
photo credit: htsm.nn.nl
Automation has always been used in factories, even at a simple level. A connected factory goes beyond simple automation and self-optimizes performance across a broad network while autonomously run production processes. A connected or smart factory uses a constant stream of data to adapt to changing demands within an organization in a fully integrated and flexible system. The automated workflows, real-time tracking and scheduling, and optimized energy consumption increases uptime while simultaneously reducing costs and waste.
Features of a connected factory
No two connected factories will look the same or have the same features. These factories connect processes and materials so that the data that is generated can be used to make real-time decisions. Certain equipment have smart sensors to constantly pull data to reflect current conditions.
The connected factory is flexible in the sense that technology can be implemented and changed to fit the organization’s needs. For example, Autonomous Mobile Robots (AMRs) can be installed into existing facilities with very little modifications needed to the current operating structure. They are easy to deploy and update thanks to their natural feature navigation and obstacle avoidance capabilities.
Benefits of a connected factory
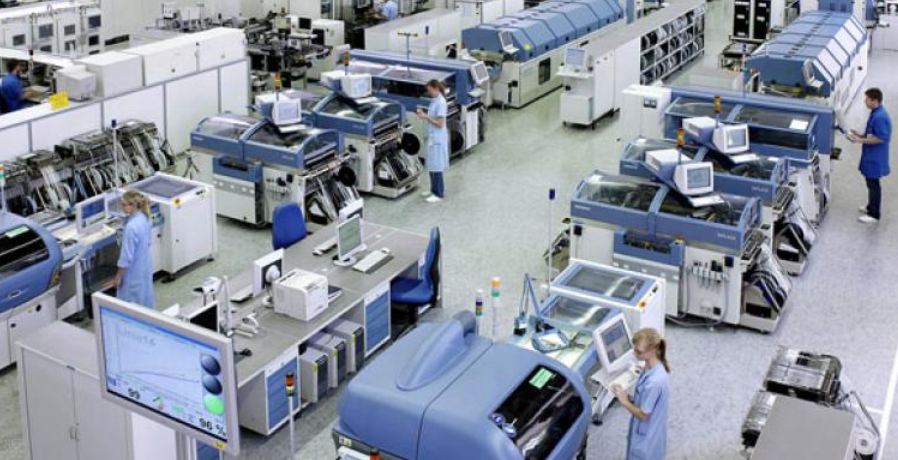
photo credit: industryweek.com
The benefits of a connected factory are not only contained to the production process itself. For example, shorter lead times increase customer satisfaction who are receiving product on time or even early. Advantages of a connected factory include:
· Higher Productivity- Since smart factories can operate 24/7 and have lower direct labor costs, there is a large investment savings.
· Increased Flexibility- Smart factories are designed for different manufacturing configurations and demand fluctuation. This provides optimal operation flexibility.
· Better Safety- Automation of tasks such as sorting, picking, packing, transporting, and delivering allows for humans to concentrate on safer tasks.
· Better Quality- A connected factory can detect quality issues faster and can identify the reason for them.
· Lower Cost- Optimization leads to more cost-efficient processes, including inventory control, better hiring decisions, and improved sourcing of needs.
There is no single best way of moving to a connected factory. By looking at the entire picture of their current systems and procedures, manufacturing companies can start with small components and scale quickly. Since the connected factory is flexible, manufacturers can invest in the technology that will fit their needs first. And the investment is well worth it as the connected factory enables logistics managers to identify and fix problems throughout the supply chain to improve profitability, lower costs, and increase customer satisfaction.