Blog
Continuous improvement isn't enough: Industry 4.0 sets new bar
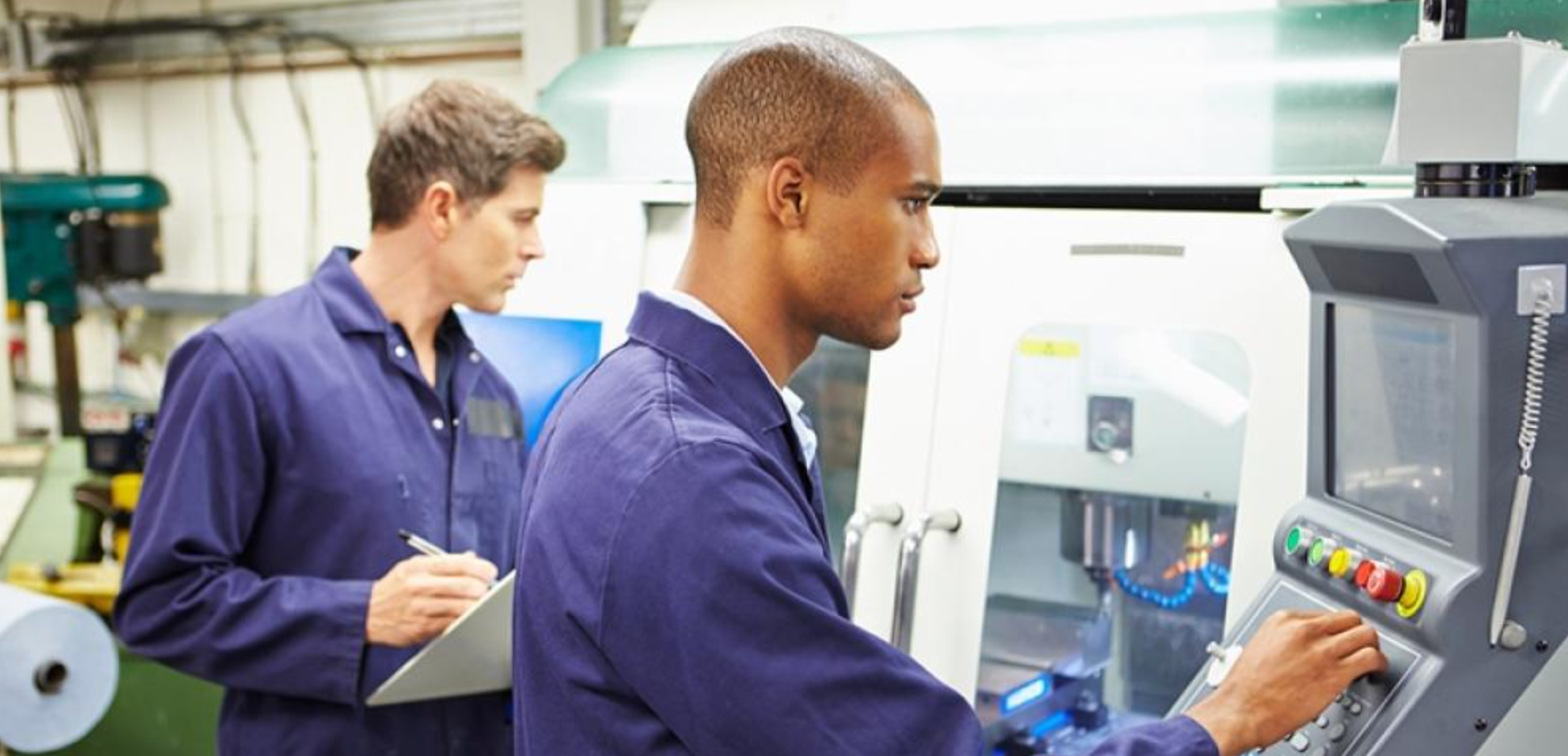
Industry 4.0 provides manufacturers with opportunities to transform digitally and uncover value within their operations. It leverages internet-connected technologies to improve existing processes and deploy continuous improvement activities by centralizing operational data to deliver real-time and actionable information. If you can understand holes in existing processes, you can better place efforts to resolve outstanding issues.
What is continuous improvement?
Continuous improvement allows manufacturers to optimize what they already know about their operations, but Industry 4.0 creates a production environment that may uncover hidden opportunities within an existing process. It is also redefining the manufacturing supply chain by transforming manufacturers’ relationships with their customers, and their customers’ experience with end products. This will force manufacturers to realize that continuous improvement has a glass ceiling; that existing processes can plateau and eventually realize diminishing returns on investment that lead only to incremental changes.
These shifts are being accomplished through higher levels of integration and connectivity in the digital manufacturing landscape. Industry has moved from push to pull business models, where modular products are unified with post-delivery services. Industry 4.0 connects a product to its producer even after it has left the plant, creating a digital footprint that allows companies to capture data, analyze it and learn from it to continuously improve across their entire supply chain.
For example, a manufacturer of air compressors would no longer sell its equipment directly, and instead drive revenues by charging customers for the air their plants consume. Compressors equipped with wifi-connected sensors at a customer’s site would, for example, monitor the flow of compressed air and adjust output based on data reports on historical use. This delivers benefits to both supplier and customer. For the supplier, output data would allow them to further optimize their offerings (air compressors in this case) to deliver its services even more competitively and grow their business, while the customer benefits from lower compressed air consumption to lower costs and reduce energy use.
By connecting products to a producer even after they’ve left a plant, the manufacturer is able to grow a digital backbone that delivers actionable information, the ability to analyze it and then learn from it to continuously improve across its entire supply chain. Doing so will be critical as manufacturers uncover new ways to compete globally. Indeed, 72% of North American manufacturing enterprises say their use of data analytics with Industry 4.0 technologies will improve customer relationships and intelligence along the product life cycle, according to a PwC report.
Embracing digitization
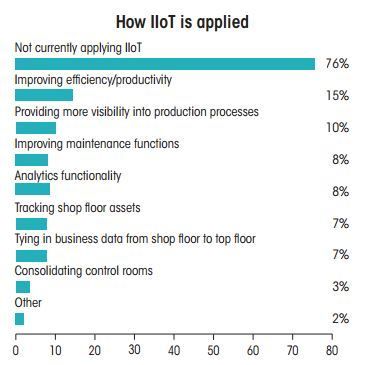
Photo credit: Manufacturers' Outlook 2017, PLANT Magazine
Despite the well-documented advantages of Industry 4.0 and the Industrial Internet of Things, manufacturers have been slow to adopt these technologies, particularly among Canadian companies. According to PLANT magazine’s Manufacturers’ Outlook 2017 report, 76% of 526 respondents are not applying Industry 4.0 principles to their operations. Only 10% said they are using Industry 4.0 to deliver more visibility into their production processes. More telling, perhaps, is that only 24% plan to improve productivity with Lean, Six Sigma and continuous improvement strategies this year, while 55% will not do anything related to those programs. And 28% are not currently measuring shop floor data, while 30% indicate they’re doing so manually.
Manufacturers that are slow to adopt risk getting lost in a world where the digitization of the global industry is accelerating. Risks include:
Limited or delayed communication within the supply chain network; or fallbacks in technology or processes when accommodating consumer needs for product differentiation.
Industry 4.0 will disrupt companies, and their current processes, in a number of ways. But this technological revolution will also provide opportunity to improve operational effectiveness strategies that challenge traditional business models. Those manufacturers that leverage advanced technologies across their value chains will gain significant competitive advantage to meet the changing and demanding needs of their customers.
Continuous improvement is rooted in the identification of opportunities that streamline process performance and reduce waste. It’s been popularized by programs such as lean, Kaizen and agile manufacturing. For example, Kaizen and Kanban systems can be combined to allow for continuous improvement through visualization of workflow.
Industry 4.0 technologies have the ability to democratize that data and make it actionable to all personnel involved in monitoring and continuously improving processes. It’s allowing users to demand new solutions that deliver access and visibility to critical data and analytics.
An example: a facility could use autonomous mobile robots to deliver materials dynamically from a point of origin to a point of destination. As the vehicles move through the facility, they collect data, including number of trips made, throughput, time of each trip, and average delivery times. This data is then available real-time to the user so they can gain immediate visibility into the performance of their facility.
Furthermore, plant operators working for the same company could potentially access data at other plants, across multiple sectors through automated reports to compare data, benchmark results, and make immediate inquiries or changes upon instant insights. In the realm of continuous improvement, that means Industry 4.0 optimizes information and data points into actionable outcomes.
Web-enabled systems also allow manufacturers to enhance their lean efforts. Considering the autonomous mobile robot example, wasted motion is eliminated by centrally coordinating the motion of shop floor vehicles through a “connected” system, so only the materials in use are in motion.
Data analytics and digital trust are foundations of Industry 4.0, and according to PwC that means end-to-end digitization of physical assets and integrating them into digital ecosystems alongside value chain partners delivers the ability to generate, analyze and communicate data logically. Doing so will bring the key attributes of Industry 4.0, and the competitive advantages associated with it, to fruition through digitization and the integration of vertical and horizontal value chains, the digitization of product and service offerings and digital business models.
The lines that once separated the physical and digital manufacturing worlds are becoming increasingly blurred. But leveraging Industry 4.0-powered technology allows manufacturers to enhance traditional lean and continuous improvement principles necessary to navigate the sector’s ongoing digital transformation.
Original post on PLANT magazine.
Written by Simon Drexler, Director of Products at OTTO Motors.