Blog
LEAN manufacturing: Changing excess inventory from too much to just right
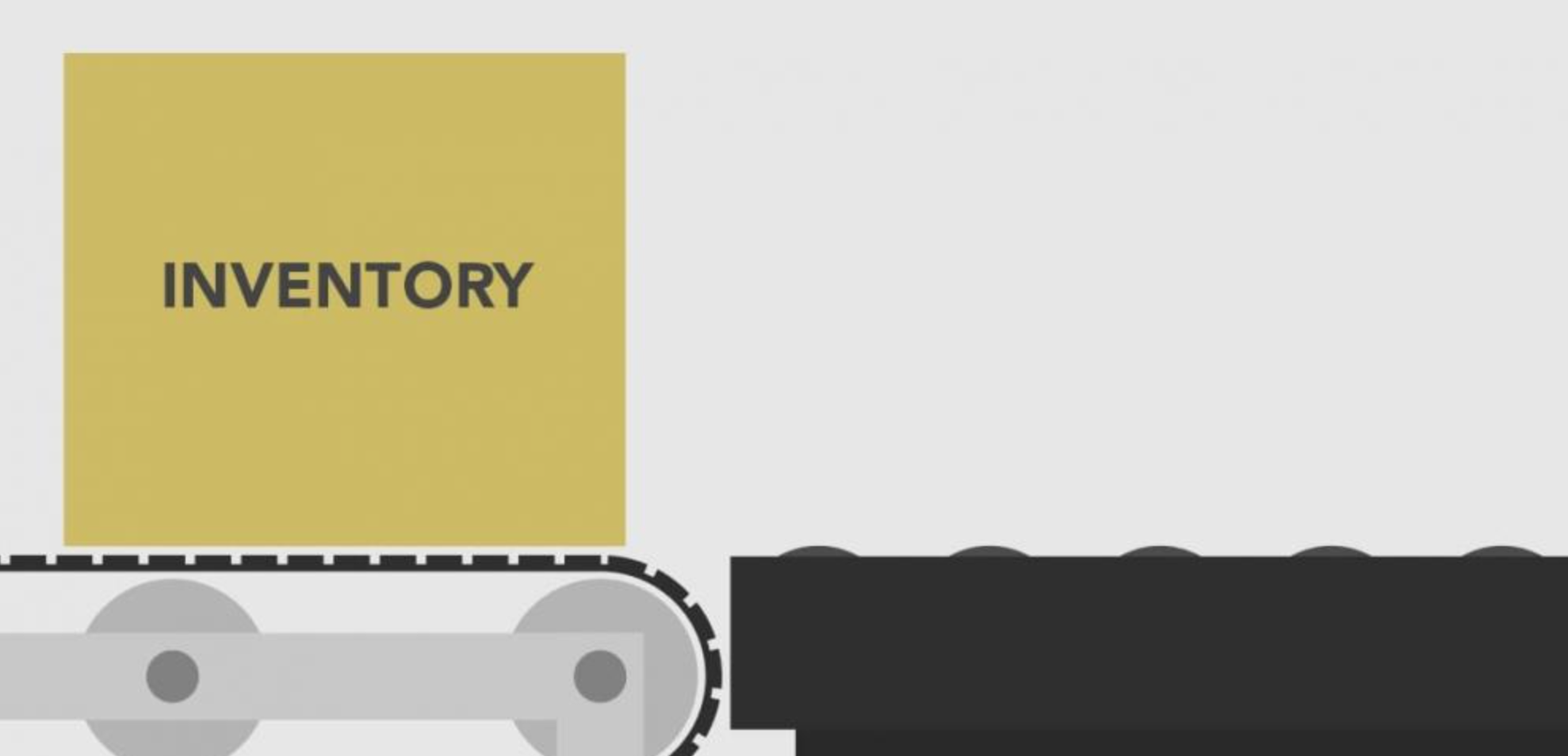
You have likely heard of the phrase “too much of a good thing.” One may ask if it is possible to have too much of a good thing. Well, consider this example: in Canada and many portions of the northern United States, strawberries are seasonal. Many people enjoy strawberries and I am one of them. So when they arrive at the local supermarket on sale and limitless in quantities available, I for one take advantage of it.
Three days and seven quarts later, I’ve had my fill of strawberries. In addition to an upset stomach, I also notice the remaining quarts are going bad. Welcome to the waste of excess inventory. Excess inventory on the manufacturing line also is too much of a good thing. It stems from a level of insecurity. In order to meet takt times, manufacturers typically prefer to have excess inventory on the line as a means of preventing a total shutdown because the right parts were not available.
This security blanket creates a number of issues, particularly as multiple product models and shorter production runs become the norm.
Changing manufacturing demand creates excess inventory
Shorter production runs and multiple configurations of products do not work well in traditional manufacturing settings. Shorter runs require less material on the line. Most manufacturers still bring a full pallet to the line when needing only a third of the material on the pallet. As multiple product models flow through the assembly line, more pallets with parts for each model fill the work cell. These are necessary to accommodate quick changeovers on the line.
The result is a high level of chaos. Aisles become more congested as traffic bringing (and returning) material to the line increases. Workers must use more steps to access the correct component for each model. The possibility of workers attaching the wrong material for the product model increases. Finally, safety issues rise. The good news is it is possible to reduce excess inventory and still meet production goals. Changes to the manufacturing line combined with recent technology innovations in automated material transport make this possible. As discussed in our post on waiting, the basic manufacturing line is sequential. In its purest form, this line does not allow for multiple product models going down the line without causing delays. This also creates excess inventory on the line.
Reducing excess inventory on the line
Manufacturers can achieve significant reductions in excess inventory by implementing a parallel operation for product variations. This moves additional components for assembly to one station working parallel to the main line, easing inventory issues and congestion. The introduction of autonomous mobile robots (AMRs) is another key factor in reducing excess inventory.
The main reason manufacturers keep more materials on the line is fear; they fear the line will shut down because a part isn’t available. The human or traditional AGV responsible for getting the parts to the line can often cause delays. AMRs, however, can help alleviate this issue. Unlike an AGV, AMRs are not restricted to a fixed path. AMRs incorporate technology similar to that found in the Google car. It plans the best route to the manufacturing line. Aisle blockage won’t slow it down because the AMR’s sensors react in real time to detect and plan around any obstacle ensuring just in time delivery.
Furthermore, delays caused by worker issues such as illness, worker shortages or rising wages are no problem for the AMR. The AMR allows for better utilization of human talent while it provides efficient and cost effective material transport.Less congestion, no delays, reduced safety issues and most importantly, a significant reduction of the excess inventory muda. That’s what an AMR offers. Learn how autonomous mobile robots can improve your operation and LEAN initiatives in the Factory of the Future webinar below.
Subscribe to our newsletter
Stay in the loop on product news, case studies, upcoming events and more.