The expanding role of robotics in manufacturing
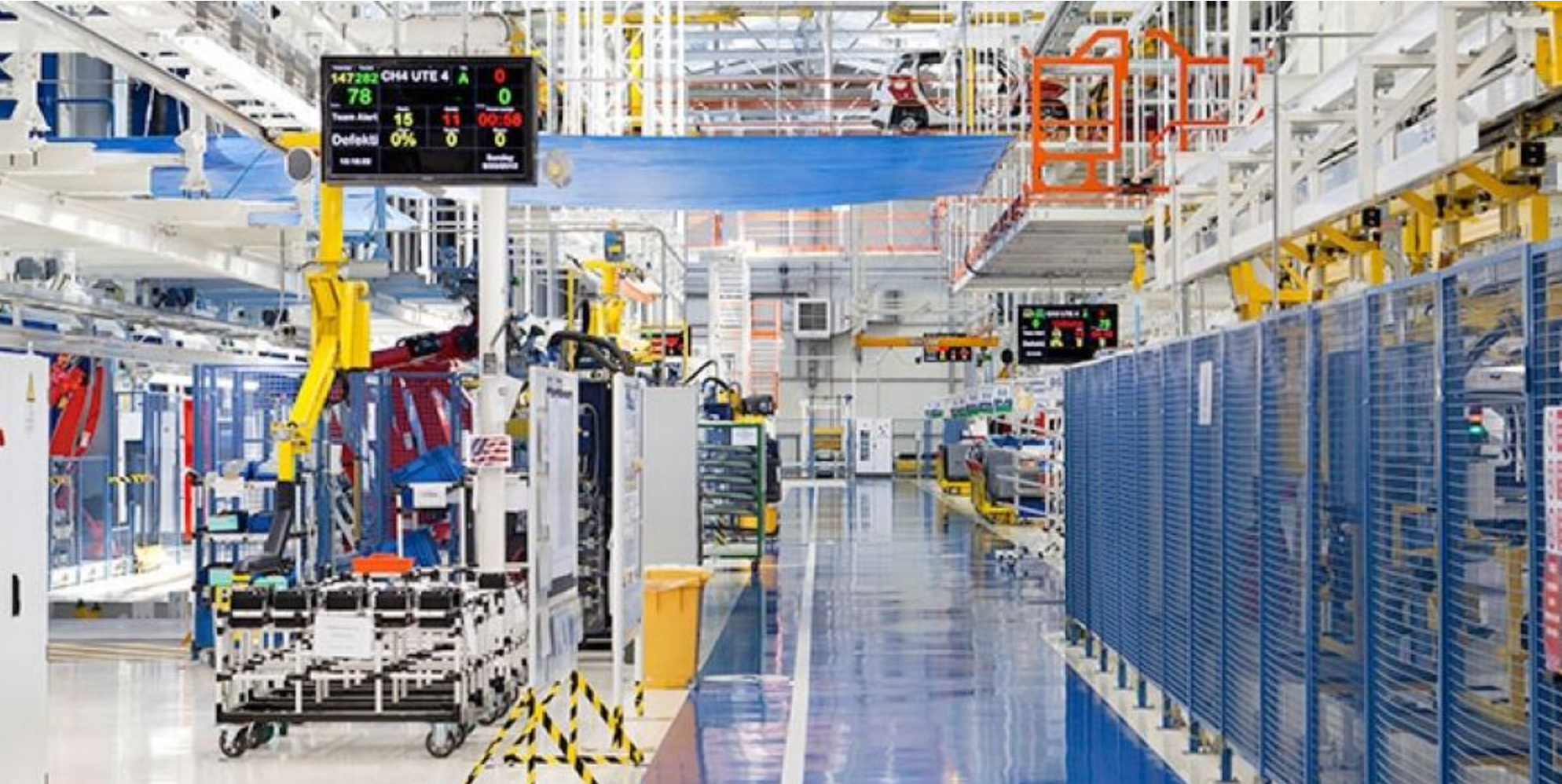
Since their first use in die casting 50-plus years ago, robots have spread throughout manufacturing. Today they perform a wide range of duties in many different industries. Thanks to advances in sensor technologies and software, the list of applications for robotics in manufacturing keeps growing.
Some of the newest and most intriguing robots are found in factories, warehouses and distribution centers. Many use conventional industrial manipulators and Cartesian-style robots, but there’s also a new breed of machine on the scene – the autonomous mobile robot (AMR). They share underlying technology with their stationary cousins but differ greatly in their intended role.
With high volumes and a limited variety of units to manufacture, the automotive industry has long been the biggest user of robotic solutions. However, usage in electronics (the second-largest market) continues to grow, as it does in metal, rubber and plastics, food processing, and even pharmaceuticals, all thanks to advances in robotics technology.
New Applications for Robotics in Manufacturing
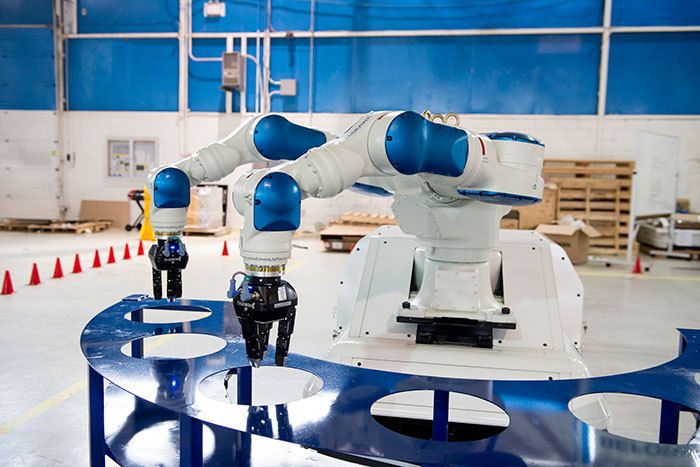
Early robots moved end-of-arm tooling through space, following a programmed path. With no ability to deviate or react to unexpected events, they needed highly structured environments. This limited their use to very high-volume applications such as automobile body-in-white welding and painting. The past decade has seen a number of significant advancements:
- The addition of 2-D and 3-D vision systems for locating parts or features in space. With these, there is less of a requirement for precise placement of objects in the work envelope, and the system can handle a product family rather than a single item.
- Force sensing allows control over side loads, enabling applications such as trimming of cast or molded edges and precise assembly work.
- Delta robots are able to perform pick-and-place-type movements at very high speeds, for packaging applications.
- Collaborative robotics in manufacturing (i.e. cobots). Using power- and force-limiting technologies plus sophisticated area sensors eliminates the need for the cage that often separates robots from human workers. This lets robots and humans work together on complex tasks such as assembly.
- Autonomous mobile robots. An evolution from autonomous guided vehicles (AGV) traditionally used in industrial centers, AMRs use vision technologies and proprietary algorithms to navigate through environments such as factories and warehouses.
Warehouse and Distribution Center Challenges
Receiving and order-fulfillment processes have been predominantly manual tasks. The variety of product formats has made automation expensive, if not putting it out of reach completely. But just as in the factory, manual warehouse operations suffer problems such as:
- High error rate.
- High wastage. (Cartons and other packaging are dropped or mishandled, damaging contents.)
- Ergonomic problems. Repeated lifting and twisting causing a range of musculoskeletal disorders.
Complicating matters, many manufacturers and distributors in recent years have changed their logistics strategy. Rather than assembling and transporting homogeneous pallets of products, there’s growing demand for ship-to-store, or direct-to-store, delivery of “aisle-aligned” pallets. This shifts in-store work to the warehouse or distribution center, where the cost of order fulfillment is rising.
Expanding the Role for Robotics in Manufacturing
Robotic palletizing isn't new, but it’s something that has traditionally occurred with uniform, similarly-sized packages. With today’s market demands for customization, mixed pallets now require robotic systems to have vision to determine package size, and end-of-arm tooling to suit various sizes and materials, plus sufficient reach and payload. Software allows either preplanning of pallet build or reacts in real time as packages are received into the robot cell.
Moving packages around warehouses is where autonomous mobile robots (AMRs) come in. Available in a range of sizes and payloads, these mobile vehicles that don’t require infrastructure to navigate are designed to integrate with pallets, spanning configurations that include a lift with pick and drop off stations, conveyors, cart engagement, or top plate for pallets. These different configurations mixed with onboard intelligence and dynamic path planning allow the AMR to transport pallets to the right place, at the right time.
Unlike their predecessors (re: the AGV), AMRs do not navigate by means of QR codes, magnetic tape, or cables fixed in strategic locations. Rather, they utilize sensors, onboard intelligence and mapping software that enable them to find their way through the warehouse. The OTTO solution is a prime example of the modern autonomous mobile robot solution for warehouses.
Early robots were best suited to high-volume, low-variety applications, but that’s changing with new sensor technology and software, which in turn enables use in new applications. Robots consequently are found in an ever-growing range of industries, and increasingly in the warehouse too.