Blog
Forklift free manufacturing: Is it for you?
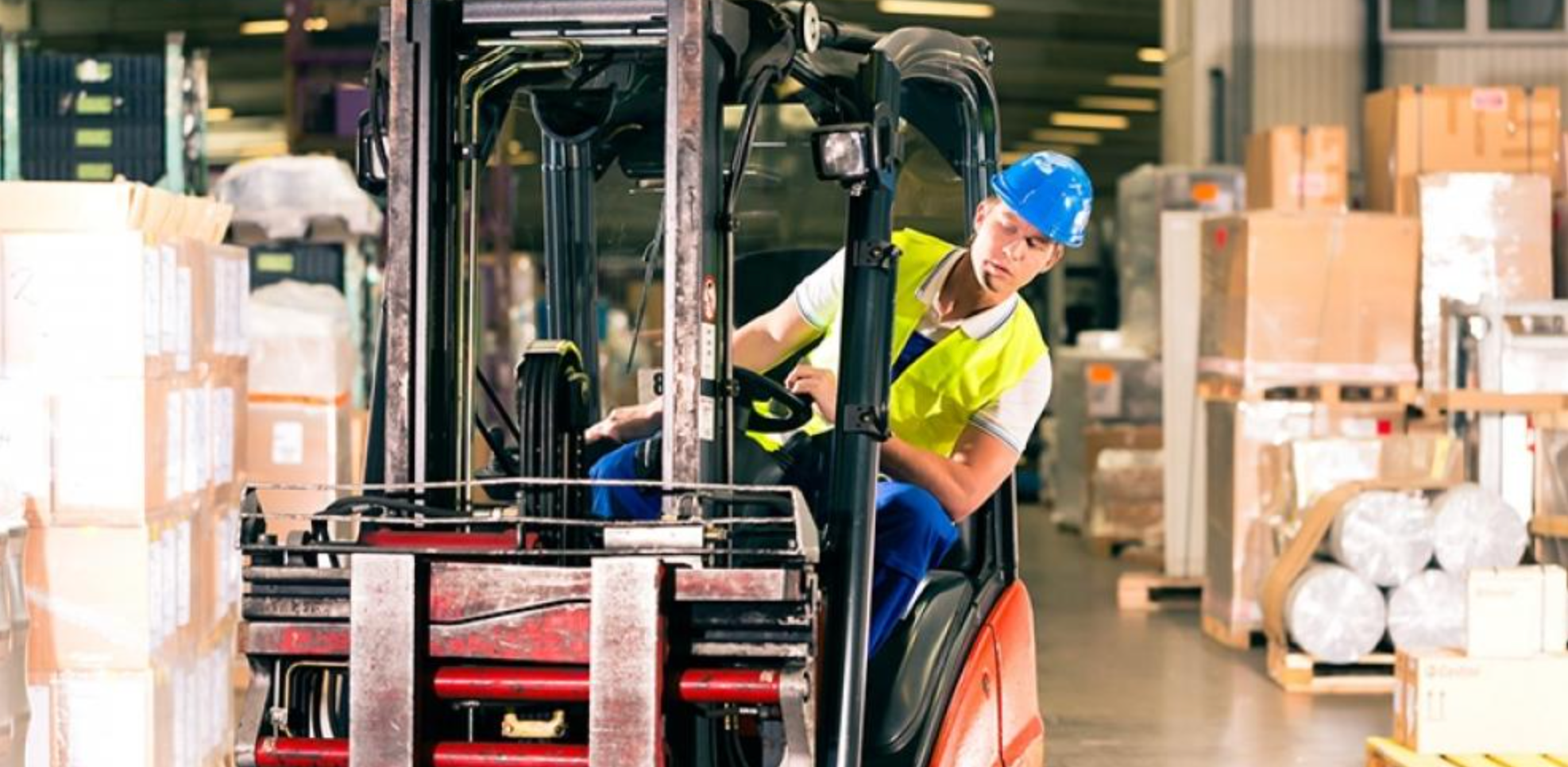
Fork-free manufacturing is a fast growing ideology that removes fork trucks from the material handling equation. Favouring the use of carts and dollies to move materials to the line, fork-free also opens the floor to emerging equipment like autonomous mobile robots to take on material handling jobs. You may be thinking, “but forklifts have been the standard for over half a century, why fix what isn’t broken?” Lean manufacturing best practices have a lot to do with it, as do safety and cost reductions. This trifecta has become more relevant than ever before in a market that is forcing manufacturers to think smarter and faster if they want to remain competitive.
Advantages of forklift-free: Lean manufacturing, safety, cost
Lean manufacturing
Falling profit margins and competition are putting increased pressure on the adoption of lean manufacturing practices. Forklift free programs can contribute value in areas related to the reduction of inventory, improvement of material flow, reduction of line-side handling equipment and floor space, improved operator ergonomics, cycle efficiency and the reduced need for coordination between forklifts and operators for replenishment of stock. For any operator, one of the key advantages is the reduction of inventory and wasted space. Fork-free allows operators to replenish material as it is used, rather than keeping excess material on the production floor, which can be completed manually, through cart operators bringing parts to the floor only when they are needed, or using automated material handling systems like the OTTO 100 autonomous mobile robots that do the job on demand.
Safety
American Machinist writes, “Each year in the United States, nearly 100 workers are killed and another 20,000 are seriously injured in forklift-related incidents. Forklift overturns are the leading cause of fatalities involving forklifts, and represent about 25 percent of all forklift related deaths.” The Occupational Safety and Health Administration report that the average life of a forklift is 8 years, and there is a 90% chance of a serious accident over the course of its life. 70-80% of the accidents occur to the pedestrians around the truck. Going fork-free would immediately change this outlook for your plant. Not ready for fork-free throughout your facility? Statistics can be drastically improved by creating fork-free zones.
Cost Reductions
With fewer incidents, comes fewer insurance claims, which equates to less costs. Furthermore, looking strictly at equipment costs, operators can expect to reduce and potentially eliminate forklift lease and maintenance costs when implementing forklift free processes. Not to mention, operating costs of material handling equipment are also drastically reduced. An old industry axiom states that, on the average, over the life of a forklift, only 20 percent of its cost is ownership. Approximately 80 percent of total forklift costs are operating costs.
4 Tips on how to get started with fork-free
James Skyrm is the Lean & Continuous Improvement Engineer at Poclain Hydraulics Inc. and spoke at ProMat 2017 on the topic. He explained, “It’s feast or famine - in order to reduce downtime and keep lines flowing, manufacturers end up carrying more personnel and forklifts. Therefore they incur more cost and more carbon footprint. If you sit on the floor and observe forklift functionality, you’ll see that they will only carry 30-40% capacity due to inventory levels and demand on the floor.”
Upon making these observations at his own facility, James implemented a forklift free initiative at Poclain and provided four areas that need to be considered when looking at revamping an operation:
1. Know your business
There is a lot of data and information that you don’t know, but you thought you knew - don’t be discouraged. The ERP doesn’t (and can’t) capture everything. Start by compiling information about your parts by following them through the workflow, from supplier to customer. Document the packaging type, boxes, weights of parts, how they are delivered to the assembly line, work order quantities for those parts, etc., so you have full visibility of the material transport process. This is the first step in implementing a “Plan for Every Part” methodology.
2. Ask questions
As you begin to understand your operation inside-out, ask in-depth questions and gather insights. Understand how much walking is performed when moving a part, or how long it takes to load/unload a pallet from an autonomous mobile robot or tugger. It’s also important to ask questions surrounding areas outside of material handling to the line, such as ‘are put-away flows optimized?’ and ‘is the kitting process documented?’ and ‘how much equipment or personnel is required?’ These insights help you determine the complete workflow, timing of tasks, and recognize which areas qualify to be fork-free.
3. Determine zones
In most cases, it’s unreasonable for an operation to go completely fork-free immediately, so start with a future approach looking 3-4 years out. The end goal may be to be completely fork-free throughout the facility, but in the meantime, determine which areas will remain forklift zones, and which areas can be designated as completely fork-free zones. By doing so, lean manufacturing improvements can be made in phases, while personnel can adjust to new workflows.
4. Culture shift
Going from a forklift to a forklift-free facility is a bit change. It’s important to educate your employee base on why you’re making the change, where the advantages will lie and how it will impact - and in turn benefit - them personally. Just as much as you will need to understand how people will be moving materials and interacting with tuggers or autonomous mobile robots, personnel will need to be aware of this too and have appropriate training.
The fork-free movement is early in its years, but for early-adopters of the practice like James, results are apparent and impactful immediately. By asking questions, gaining full visibility into the operation and embracing an Industry 4.0 mentality to change, facilities of any size can revolutionize what it means to be lean through a fork-free approach.