Blog
Automotive manufacturing keeps up with future demand
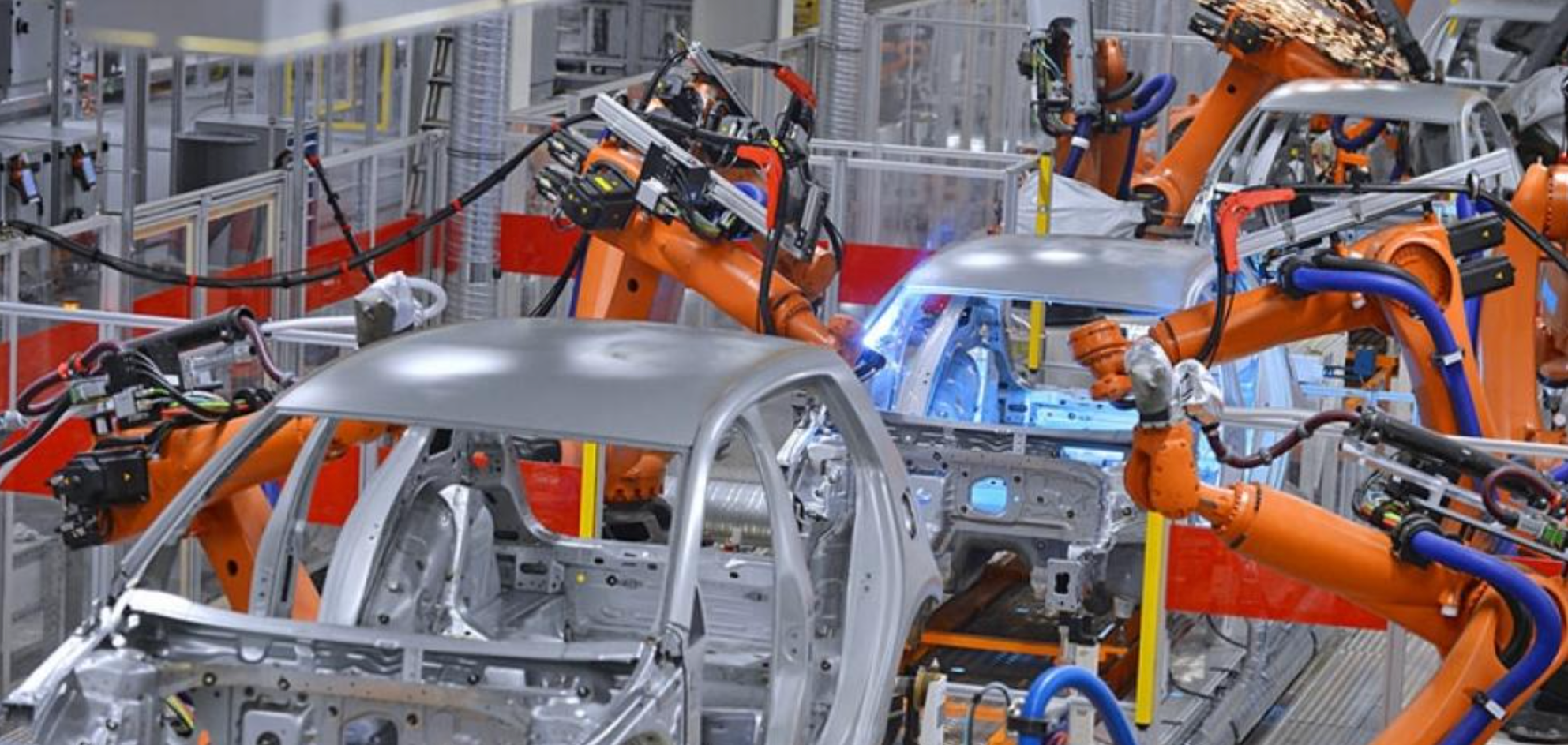
Original post by David Stain at Zebra Technologies.
The future of automotive manufacturing in the UK automotive is set to increase by a third, to two million vehicles a year by 20201. And as the IoT and new technologies take hold, the way these vehicles are designed, produced, distributed and used will change fundamentally.
As ever, plant owners will have to maintain productivity and supply chain efficiency, but as automotive demand increases for customized and connected vehicles, the challenges will be around managing process time and product assortment.
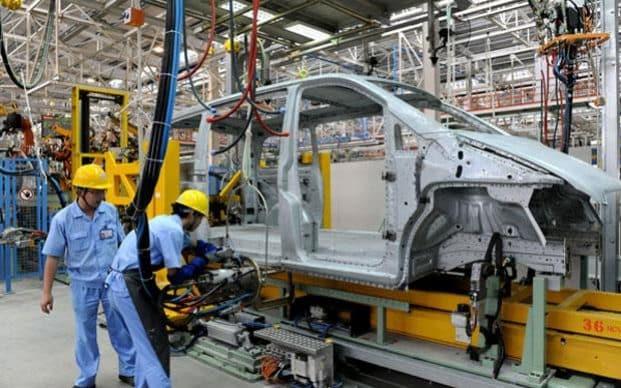
Photo credit: The Telegraph
From a consumer perspective, hands-free steering and remote control parking signify the movement towards future automated driving, where the connected vehicle looks after its own safety, leaving passengers to amuse themselves with increasingly sophisticated in-car entertainment. At the same time, services such as Uber and BlaBlaCar point the way to car-sharing services, with Ford research showing that in the UK alone, this could grow by 23% between 2013 and 2025. Among owners, expectations will be high, with demand for premium vehicles built to order, low on emissions and fuel consumption, and high on personalised specification.
For manufacturers and industry suppliers, then, the challenge is not only to know what the vehicle of the future will comprise, but to pre-empt the technology and the implications throughout the supply chain and production processes.
The future of automotive manufacturing is an evolution, not an overnight achievement
In an ideal world, factory owners would be able to construct bespoke facilities, factories of the future, to carry out fully automated production as orders roll in. In reality, business will continue within the limits of existing operations, adapted to accommodate the latest technologies. And transformation doesn’t have to be an all-or-nothing affair put in place overnight. For larger organisations and smaller suppliers, it’s about incremental change given existing knowledge and assets, about adapting towards best practice by embracing new materials and new ideas, rather than going all-out for radical transformation and failing.
So where to start? If the vision is of fully connected, personalised automotive vehicles, then getting there will mean managing product assortment in an equally connected way. To minimise storage costs and manufacture on-demand, just-in-time production and supply chain is essential.
This is possible only with visibility of the entire supply chain, upstream and downstream, and the knowledge of where everything is at any given point, including components, people, equipment, freight and finished goods. Adoption of cyber-physical models such as IoT and Industrie 4.0 support this evolution, with people, processes and technology fully aligned.
With real-time data turned into actionable information, operators have what they need to make better decisions resulting in more efficient production that meets demand and eliminates wastage of time, money and materials.
We call this Enterprise Asset Intelligence, incorporating the full supply chain visibility that enables organisations to streamline processes and move towards optimal production. Auto ID and mobile technology, deployed with a stage and gate strategy through the manufacturing process, provide visibility, certainty and measurable metrics in real-time, with technology-enabled, mobile workers managing production to align with the precise needs of the supply chain.