Blog
The Heijunka system for better materials management
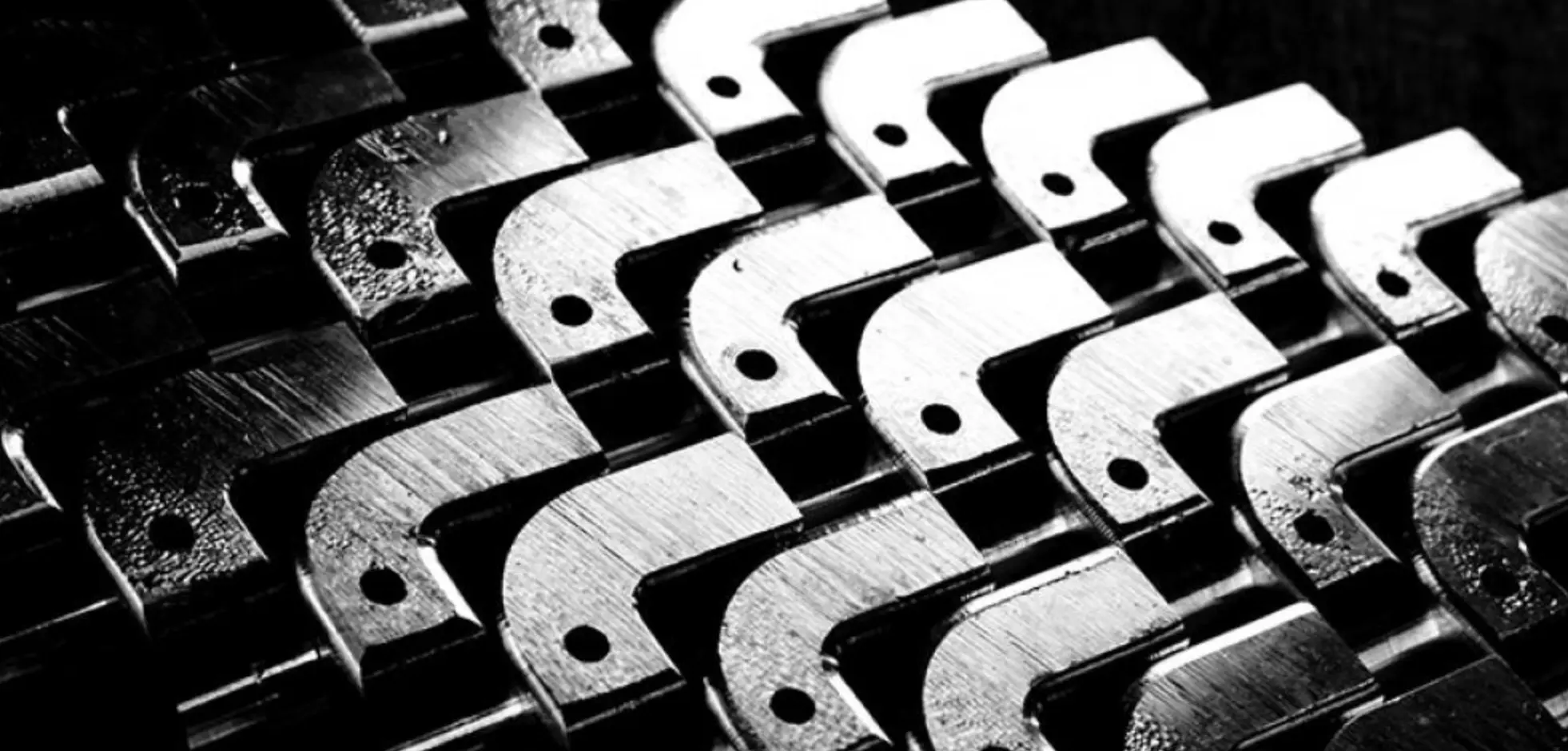
When one part of the production process is delayed, it can cause a ripple effect throughout a manufacturing facility. A prime example of how this type of disruption can occur is when the function of materials management fails. Clearly then, organizations that control materials handling during production operate optimally in other areas of their facility. Levelling production is an effective technique companies use for meeting the product demands of the manufacturing process, while continuing to run an efficient operation.
What is a Heijunka system?
Heijunka is a lean manufacturing concept in which production is smoothed, or levelled. This would be easy if demand remained the same all the time, however, for most companies it fluctuates daily for any number of reasons. Heijunka ensures that there are no fluctuations in production no matter the demand, all while reducing waste and meeting customer requirements. Levelling can be done by product type or volume, either one can result in significant efficiencies and savings.
Manufacturing processes
With Heijunka, the use of raw materials remains balanced. Since having the correct raw materials is the key first step in manufacturing, getting this right affects the entire process. When the exact amount of raw materials are on hand on a daily basis, there are minimal delays in production, transportation, or final customer delivery. The correct amount of raw materials going in leads to the correct amount of output to the other connected processes in a facility.
Smaller batches
A non-lean production process may run large batches of a single product to keep lines of production going and achieve economies of scale. Once these large runs are completed, the work in progress goods are often left until production is ready to move them to the next step. This is inefficient, with unused product sitting for a day, or over a week. Heijunka recommends smaller batches so the entire process continues to run smoothly, not just the production line.
Surplus items
One of the most frustrating tasks for a materials manager to deal with is surplus items - what’s to be done with materials that will never be sold? It is a huge inefficiency and cost. Since there is no over or under production with Heijunka, there are no surplus items that need to find a home, or be written off.
Pull system
A pull system is one where resources and materials are replaced only when they are used and one of the founding principles of Heijunka. So, materials are not bought when they are not needed, even at a very low price to stockpile for later. Since overall levels of materials stock are lower, there is little waste in transporting or stocking the items in the warehouse. This system works well for materials that are readily available, however, specialized parts and materials may take longer to source.
Upstream effects
A manufacturing facility will usually add inventory if their upstream suppliers do not deliver on time or do not delivery good quality raw materials. This adds to the stress level of employees having to source this material, and the inventory going unused for too long. Inventory is also added if customers have irregular demand patterns, or if there are quality or production issues internally.
Smoothing production through a Heijunka system ensures that all areas of production will run with few delays or interruptions. This benefits companies by not only improving materials management, but helps other functions within the facility by ensuring a more consistent and reliable flow of finished product.
Executing Heijunka with automated materials handling
OTTO is a flexible automated materials handling system that adapts to companies’ production schedule, freeing it from fixed automation and making changeover day to day or hour to hour simple. This ensures reliable delivery of goods on a production cadence better than relying on manual labour or inflexible fixed material handling infrastructure that is difficult and expensive to change. OTTO makes automated material handling a competitive advantage that reaches into every area of the production floor, allowing plants to operate optimally throughout their facility.