Blog
How High Performance Safety maximizes throughput AND safety in AMR deployments
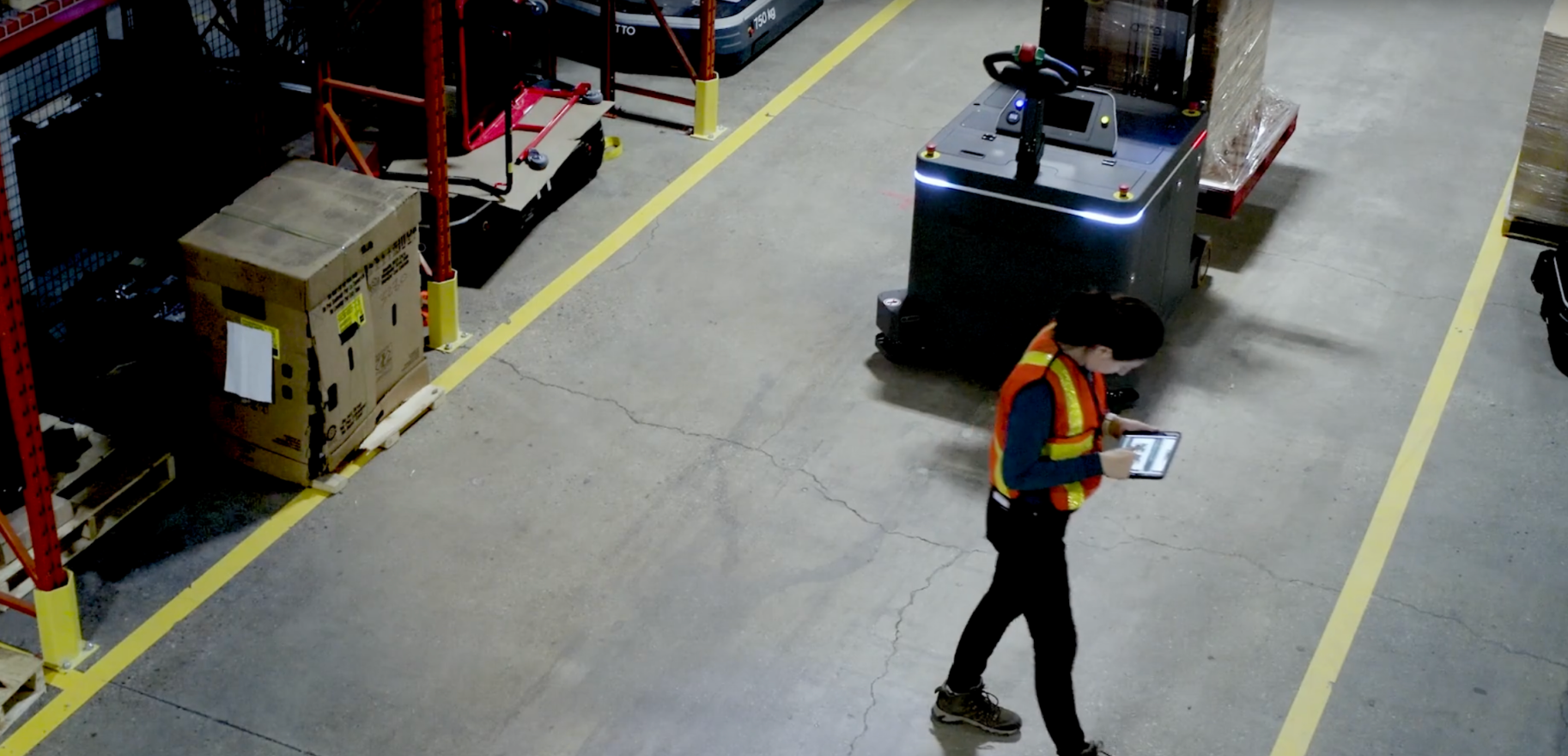
Manual material handling is inefficient and unsafe. It consumes approximately 25% of the workforce, 55% of the room and 87% of the time of production in a factory. More importantly, it can be extremely dangerous, with 1 in 6 workplace deaths involving a forklift.
This is why manufacturers have been automating material handling with autonomous mobile robots (AMRs) for decades. While safety is paramount, manufacturers are also concerned with achieving high throughput to increase ROI. Eliminating the tradeoff between speed and safety is the key to unlocking the full potential of an AMR deployment in dynamic manufacturing environments. This is achieved through what OTTO calls “High Performance Safety.”
Not only does the technology improve worker safety by enabling them to focus on less physically demanding tasks, it also shortens time to market and helps manufacturers win more customers while ensuring business continuity.
Operators have been sharing that they no longer struggle to get out of bed because of back or leg pain; they are sleeping better at night because they aren't sore from stacking boxes. They are able to play with their children and pets again because their bodies are fresher when their days end.
A Fortune 500 food & beverage manufacturer on AMRs improving worker safety
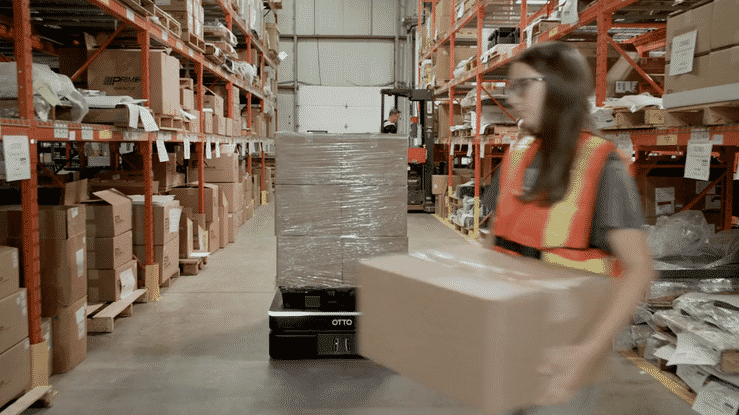
Image 1: High Performance Safety maximizes average speed without compromise to safety.
What is High Performance Safety?
High Performance Safety is the balance of maximum productivity (speed) and uncompromised safety to deliver higher average speed. Speed and safety are generally at odds with each other, and the challenge for AMR vendors is to maximize both, confidently. This is particularly important at scale, as there can be significant cumulative productivity loss when average speed is lowered, impacting ROI.
Being very, very safe is easy. You make big fields and you make the robot drive slow. Driving very, very fast is easy. Robots are good at it, but [then] they’re not safe. How do you do both? How do we tackle that balance, that design challenge?
Adrian Ennis
Senior Product Manager, OTTO by Rockwell Automation
To achieve High Performance Safety, OTTO uses “fieldsets”: predefined configurations or parameters that govern the behavior and operation of the robot within its environment. Essentially, fieldsets help the robot operate safely, avoiding collisions with obstacles or humans, adhering to speed limits, and reacting properly to unexpected situations.
These parameters are informed by safety-rated hardware, including:
- LiDAR sensors, which act as the robot’s eyes and are tied directly to the robot’s safety circuit and braking system
- 3D cameras for obstacle detection under and overhanging objects during navigation as well as pallet tracking
- Specialized sensors to ensure safe payload acquisition, stability and placement as well as to recognize sudden pallet shifts (specific to OTTO Lifter)
How do OTTO AMRs utilize High Performance Safety to maximize speed and safety?
OTTO has introduced adaptive fieldsets to optimize average speed. Adaptive fieldsets work similar to adaptive headlights on a performance car. The fieldsets shift and extend out in the direction the robot is turning, giving the robot improved visibility in the direction of travel and preventing slow downs around corners, people and obstacles.
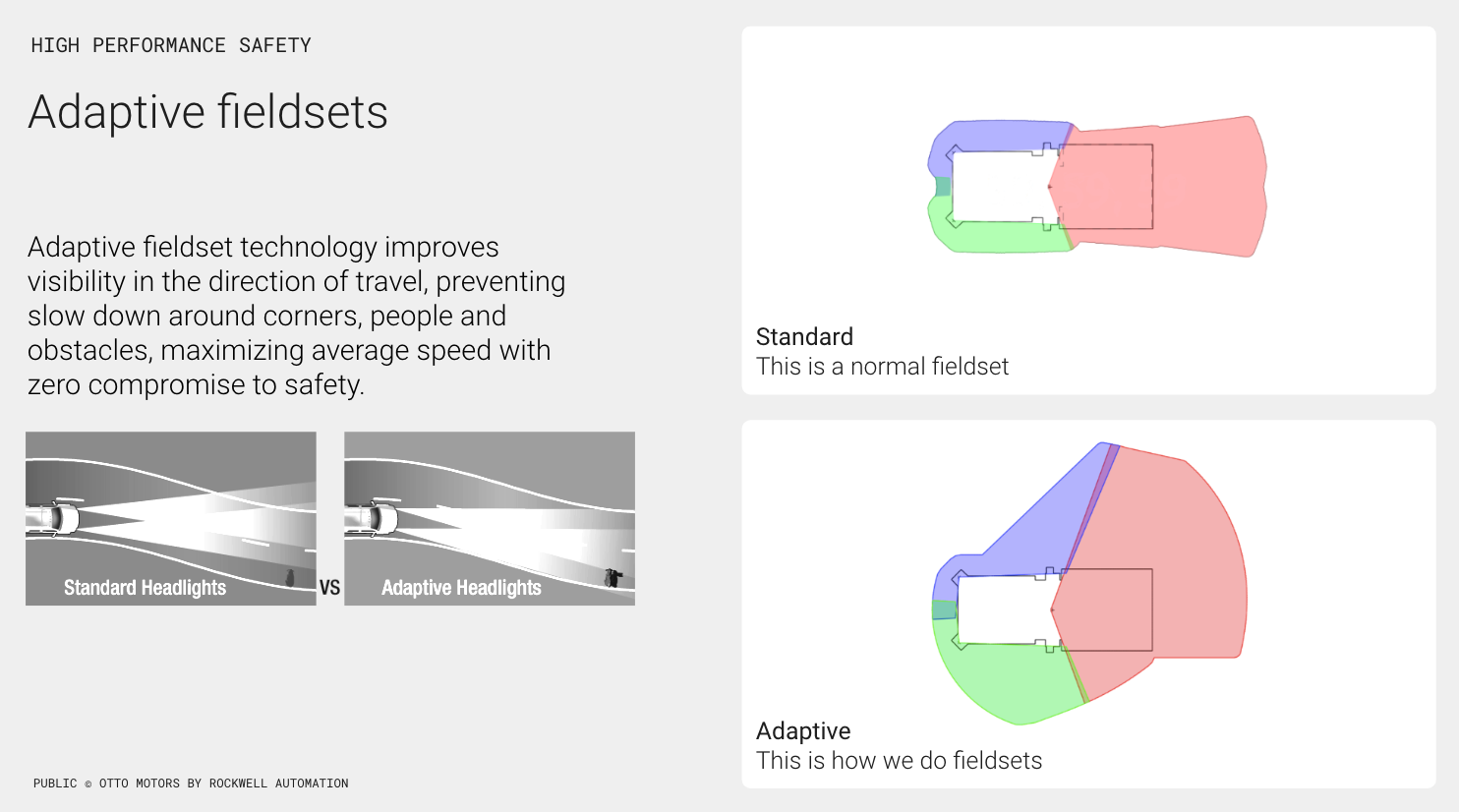
Image 2: Adaptive fieldsets as defined in the webinar “How to maximize throughput AND safety in your AMR deployment.
It’s only protecting the space that it needs to. It doesn't have to protect the other side of [itself], which is irrelevant because it’s not driving that direction.
Adrian Ennis
Senior Product Manager, OTTO by Rockwell Automation
Since introducing adaptive fieldset technology, the average speed of OTTO AMRs has increased by 50%, and the cost to manufacturers has decreased by 33%.
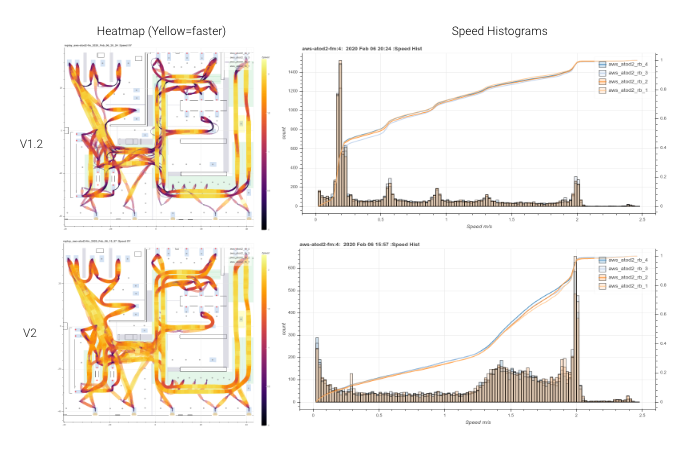
Image 3: A comparison of standard fieldsets (V1.2) and adaptive fieldsets (V2), demonstrating how the latter increases time spent at higher speeds, which in turn increases the AMR’s average speed.
Now, OTTO is introducing a new feature called “fieldset switching” to enhance robot efficiency by reducing the fieldset footprint when it is not carrying a payload. This will enhance High Performance Safety as smaller fieldsets enable faster speed while maintaining the same level of safety.
High Performance Safety doesn’t stop at safety-rated hardware; proactive, safety-aware software steps in to decide which fieldset to enforce—with a payload or without. Then, it generates the most efficient route to its destination based on the size of its fieldset and the traffic rules that have been assigned. By anticipating safety requirements, software helps maximize average speed without sacrificing safety.
There is a necessary final step to make sure that the AMR in question is able to make the most of the fieldsets it is using. Our autonomy stack—our software—is able to understand the shape of every field that the LiDARs will be enforcing. We take that extra step because we want our autonomy stack—when it is generating new paths, when it is tracking itself along a path—to understand how the hardware is going to react. Software is never going to let hardware do anything stupid. It’s fundamental for how we approach this.
Adrian Ennis
Senior Product Manager, OTTO by Rockwell Automation
High Performance Safety in action
High Performance Safety has been implemented across manufacturing facilities worldwide operating with OTTO AMRs to improve productivity without compromising on safety.
One such example is at Mauser Packaging Solutions (Mauser), a global packaging leader with over 180 facilities worldwide. While supporting Mauser’s 24/7 operation, OTTO AMRs safely work alongside their operators to move plastic rigid containers from the conveyor to the stretch-wrapper.
After implementing two OTTO AMRs equipped with adaptive fieldset technology, Mauser was able to improve throughput by 6 times, without compromising on safety.
When we introduced the OTTOs [into our facility], we didn’t have to worry about people getting hurt.
Dinesh Naidu
Plant Manager, Mauser
High Performance Safety is crucial to maximizing throughput while maintaining safety in material handling operations. OTTO hardware and software work together to maximize average speed while prioritizing the safety of employees, the facility and other equipment. Learn more in the webinar.
Subscribe to our newsletter
Stay in the loop on product news, case studies, upcoming events and more.