Blog
Hiring qualified workers remains industry’s top challenge
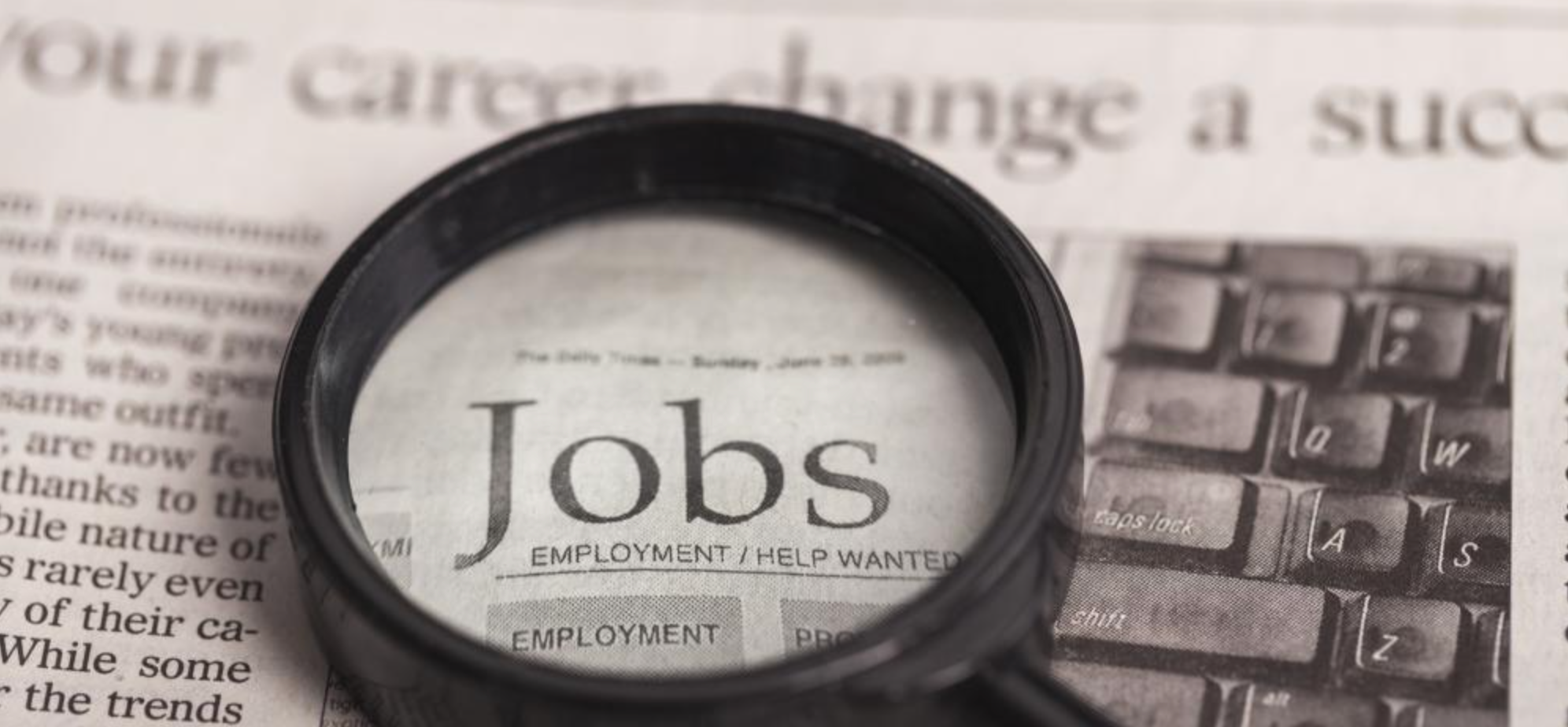
Ahead of other worthy contenders like customer demand for lower prices, faster response times, competitive pressure, and forecasting, manufacturers named “hiring qualified workers” as their top challenge in the 2019 Material Handling Institute (MHI) Annual Industry Report.
Unemployment rates are at historic lows in the US and abroad. May 2019 saw a 49-year low of 3.6 percent in the US, which just barely rose to 3.7 percent in June. Meanwhile, baby boomers are just starting to retire, a trend that will affect labor dynamics for years to come. These factors have made it difficult for industries like manufacturing to retain the talent they need.
According to a study by Deloitte and The Manufacturing Institute, 4.6 million new manufacturing jobs are projected to be created by 2028, but 2.4 million of them could go unfilled because of a skilled-labor shortage. This phenomenon—termed “the skills gap”—is currently the top challenge within the 2.5 trillion-dollar industry.
It makes sense that 91% of companies listed “hiring qualified workers” as somewhat, very, or extremely challenging in the new MHI Industry Report. This is one of the biggest reasons why manufacturing companies are looking to implement automation solutions: to assist their workforces, especially during peak demand periods.
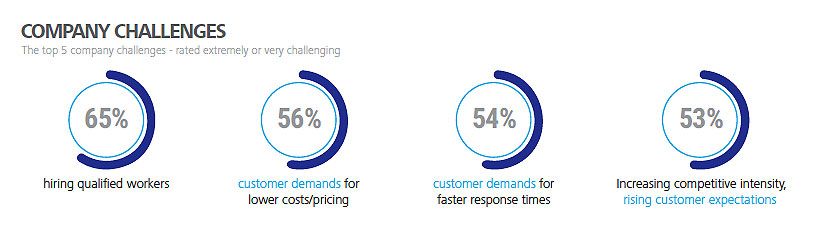
Figure 1: Companies ranked hiring qualified workers as their number-one challenge in new MHI Industry Report.
Rather than replacing workers with robots, it’s important to note that manufacturers are generally seeking to enable increasingly scarce supply chain workers to take on higher-value work—the kind of work only humans are capable of doing.
The current generation wants the opportunity to be creative and solve challenging problems. They are not infatuated with the mundane. They want the flexibility to leverage their unique understanding of NextGen supply chains.
Randy Bradley
University of Tennessee
Automation allows workers to focus on higher value-added tasks by replacing the dull or repetitive tasks like material movement.
For example, Alibaba—a Chinese e-commerce company—employees walked as many as 27,924 steps in a 7.5 hour shift before implementing automation in their facility. Now, employees have seen a 91% reduction in the amount they walk, allowing them to remain working on their area of expertise during shifts.
While automation helps solve the industry's top challenge, hiring qualified workers, it is also able to do the repetitive and dull tasks for much cheaper than paying over-qualified workers for the same tasks.
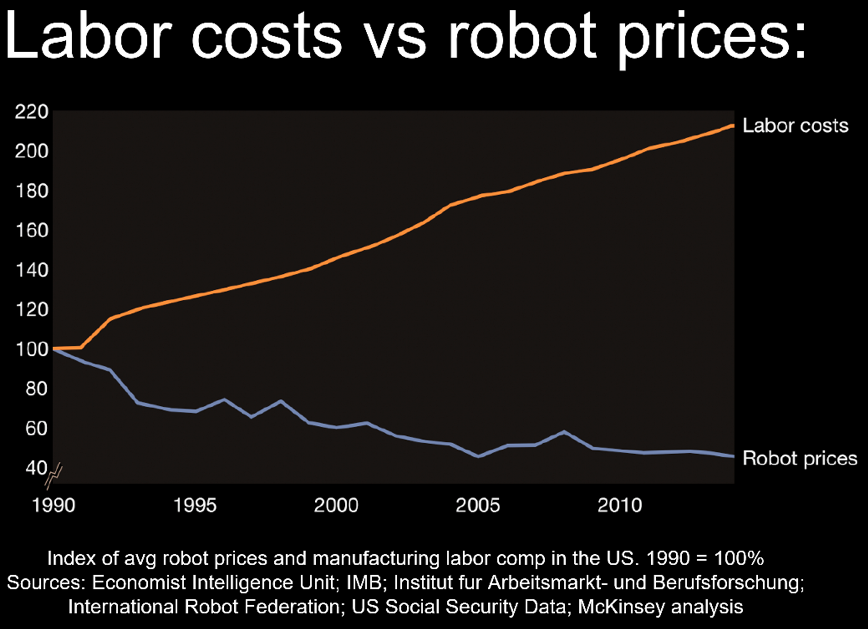
Figure 2: Automating repetitive and dull tasks within a job allows paid workers to focus their efforts on higher value-added tasks.
Adding robots to operations does not replace human jobs, as humans have skill sets untouchable by robots. However, automating necessary, but simple, tasks within an operation is more beneficial for companies' bottom line than paying humans to step away from their value-added tasks.