Blog
3 ways autonomous mobile robots can improve your safety culture

Workplace safety has been a prevalent concern for the manufacturing industry, one which has been heightened as a result of the COVID-19 crisis. With approximately half the American workforce still physically going to work, they are risking COVID exposure to ensure essential products and services are available. Protective measures have been put in place to minimize the risk of the virus spreading within workplaces but those measures are not always effective.
Today, Autonomous Mobile Robots (AMRs) are part of the efforts being used to safeguard employees within manufacturing facilities. Here are three ways AMRs can improve workplace safety on the manufacturing floor:
1. Supporting necessary social distancing measures
Reducing direct human contact through social distancing measures have become extremely important since the COVID-19 crisis and manufacturers are trying to adapt to the guidelines that are deemed mandatory in order to keep their operations running. Typically, manual material movement jobs like humans pushing products to the next station, building and inspecting parts and forklifts picking up and dropping off goods all require close contact of workers. However, Autonomous Mobile Robots (AMRs) eliminate unnecessary contact in and between work cells and therefore, can reduce the risk of shut down due to COVID-19 by keeping workers safe.
Autonomous deliveries are bringing supplies to people as they adopt social distancing. Automated workstations are speeding up the work of pharmaceutical companies. Automation is on the front lines of this battle.
Robotic Industries Association
Smithfield Foods, a pork plant in South Dakota, has to shut down operations for at least two weeks due to a COVID-19 outbreak at their Sioux Falls facility. The Sioux Falls facility accounts for 4% to 5% of the United States' pork production, costing the company millions, and impacting the nation's food supply.
Smithfield Foods is not the only supply chain at stake, however. The Institute for Supply Management reported that 95% of organizations predict that they will be or have already been impacted by supply chain disruptions as a result of the crisis. Using mobile robotics to increase safe social distancing measures in facilities can help limit the impact of the crisis.
2. Reducing repetitive strain injuries
While implementing robotics in warehouses can help promote employee social distancing, they can also help reduce direct, physical injuries resulting from manual material movement. In manufacturing, workers move and lift heavy objects every day. The repetitive nature of many warehouse tasks can lead workers to make mistakes that can result in worker or product harm. In fact, the repetitive nature of manual material handling accounts for 2 of the top 5 ways people working in warehouses get injured.
Implementing safer mobile robotics also has a profound impact on ROI because reducing risk to workers also reduces worker compensation payments, medical expenses, and costs for legal services. While materials handling may not seem dangerous at first thought, it's actually the leading cause of compensable injuries in the American workplace.
Consequently, mobile robotics also allows labourers to focus on more complex, fulfilling and rewarding tasks while they handle the dull, repetitive work. In an industry where 23% of unplanned downtime results from human error, this autonomy is nearly invaluable.
If a job is repetitive and boring, human workers tend to make a mistake, whereas robots can do these things the same way time after time.
Frank Hearl
Chief of Staff, The National Institute for Occupational Safety and Health (NIOSH)
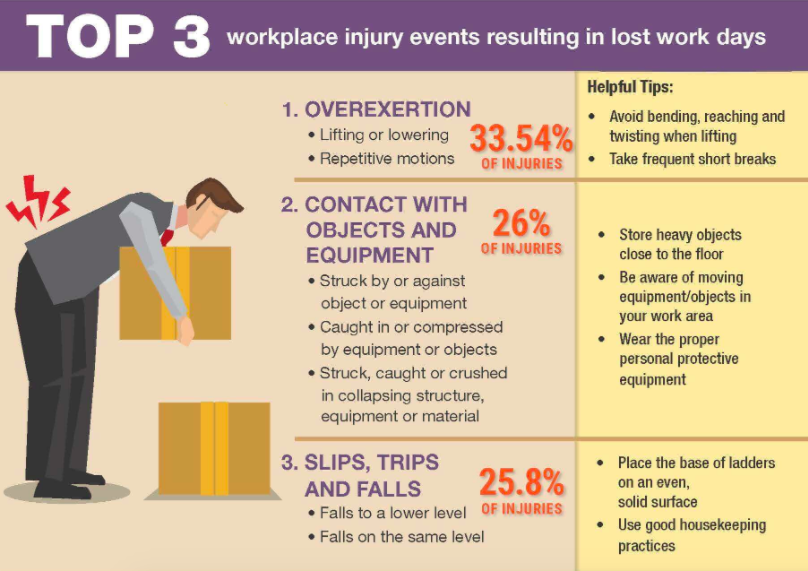
Image 1: The repetitive stress injuries caused by lifting or lowering objects repetitively during manual material movement account for over 33% of worker injuries.
3. Limiting contact with dangerous machinery
Along with physical injuries resulting from the repetitive nature of materials movement, workers are also at risk of injury due to the many manually-operated forklifts found in most warehouses. While forklifts are the most common material handling technology used in the food and beverage processing industry, they are also one of the most dangerous material handling technologies.
With nearly 35,000 serious injuries resulting from forklifts each year, and a 90% chance of a serious accident occurring during their 8-year average lifespan, these machines are one of the leading threats to warehouse safety. Using mobile robotics for autonomous material handling instead lessens the risk of employee injury or death and its associated costs.
Additionally, autonomous material handling doesn't require human operators, meaning operations can continue 24/7, even when workers cannot be present, such as during our current global pandemic. For example, HIROTEC America uses mobile robotics to work towards their vision of lights-out 24/7 manufacturing and ensure a zero-operator area in their spare parts production.
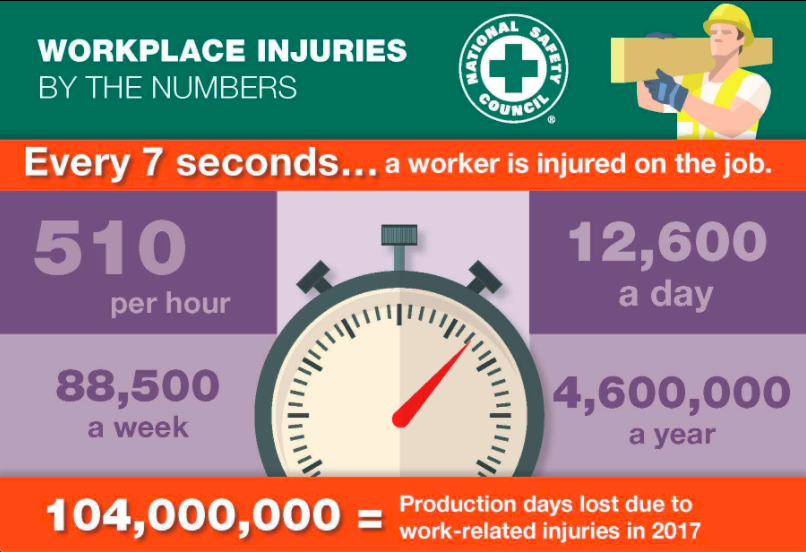
Image 2: Workplace injuries occur every 7 seconds, and mobile robotics can help lessen the number of injuries, keeping your employees safe and your business moving.
Implementing mobile robotics
Manufacturing is, at times, a dangerous industry, but it doesn't have to be. While AMRs have historically been deployed to help manufacturers reduce costs, improve safety and improve productivity, they are now part of the efforts being used to safeguard employees within manufacturing facilities. After the most pressing safety needs of COVID-19 are addressed, like maintaining employee safety, AMRs will play an important role in the digital transformation that is needed for supply chains to become more resilient in a post-COVID world.
Learn more about how we can support physical distancing within your workplace by reducing the need for staff to move from cell to cell.