Blog
How to build a value stream map
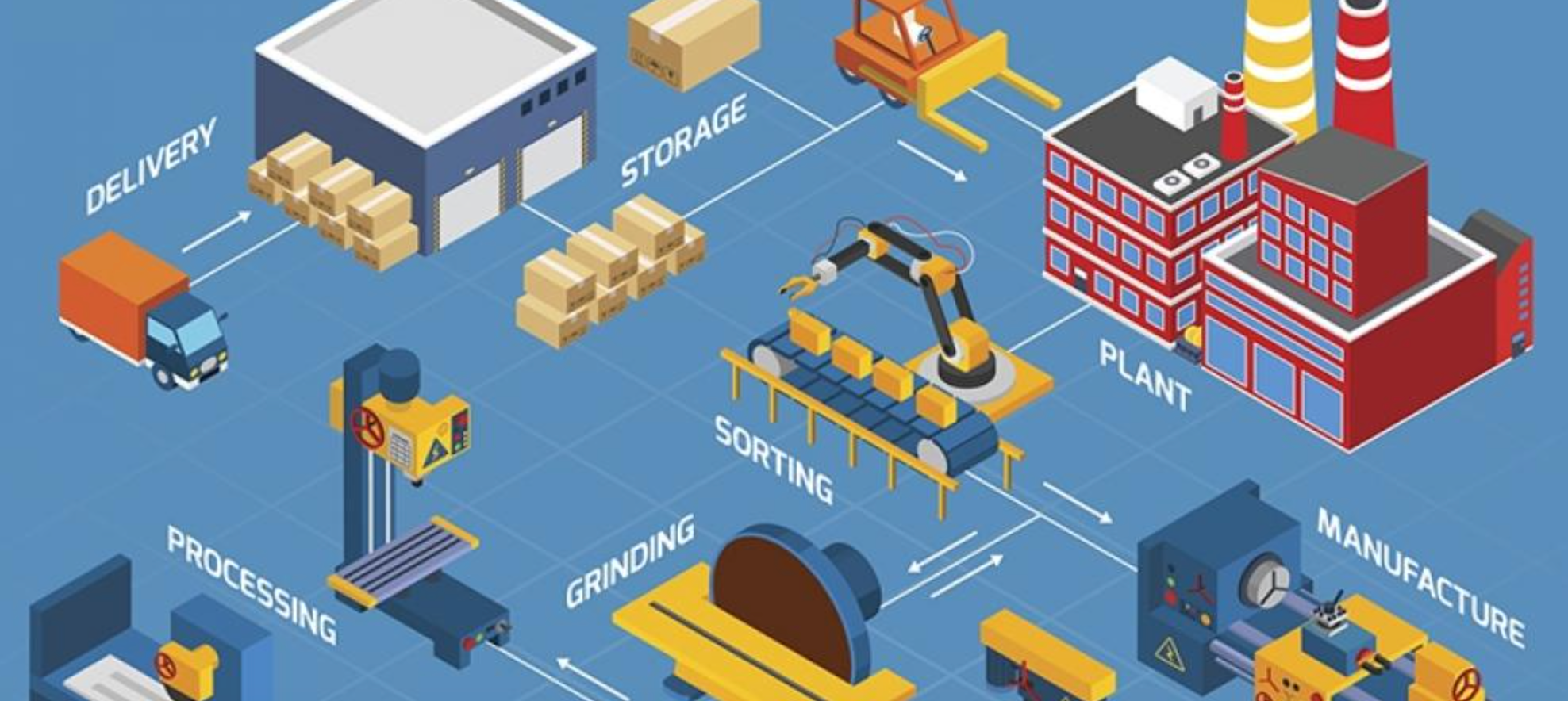
Value Stream Mapping (VSM) is a planning activity used to determine opportunities for a leaner workflow. The value stream is a set of all actions necessary to bring the product to the customer. It analyzes the current state, which is then used to design a future state that will move the product through the supply chain in the leanest way possible. A VSM is a fundamental lean-management method that enables organizations of any size, in any industry, the ability to operate lean and do more with less. What opportunities can be found from completing a VSM and how do you create one? Read on!
Advantages of creating a value stream map
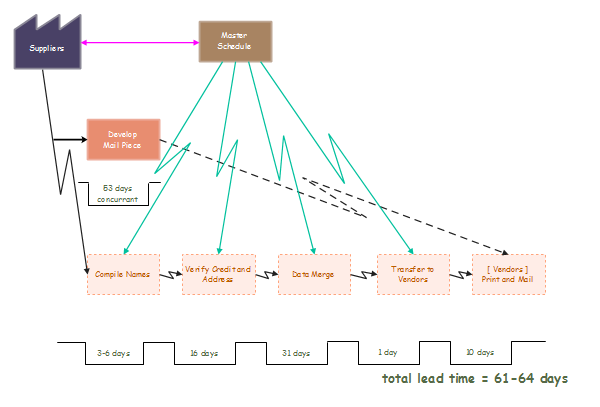
Photo source: edrawsoft.com
A Value Stream Map provides insight so manufacturers can change their existing facility layouts and systems for material handling, inventory control, purchasing and scheduling. By doing so, they’re able to reduce the total throughput times of orders and current levels of work in process (WIP) inventories. This, in essence, is lean thinking which defines waste as “all activities that consume resources (add costs to the product) but contribute zero value to the customer.”* Value in lean is really value for the customer - it can be easy to forget this because we constantly focus on how things work best for us as a manufacturer. Aside from the benefits available to your customer (ie: faster delivery times, more competitive costs), creating a VSM generates a number of other advantages including:
- It’s quick and easy to learn
- It's an inexpensive tool that brings a group of key stakeholders together, therefore involving the larger workforce in your lean improvement program
- It helps portray the process from the start of the production process to the end
- It helps determine bottlenecks within your workflow
- It helps find waste within the process
How to create a value stream map
Here’s a high level overview** of what you need to create a value stream map:
1. Define the process boundaries. In other words, decide the limits of your map. Most value stream maps are conducted from supplier through to customers within an organization.
2. When getting started with creating a value stream map, it’s best to begin mapping a group of products or services that have similar processing. Start with your high growth, high volume product family which might give you the biggest bang for your buck.
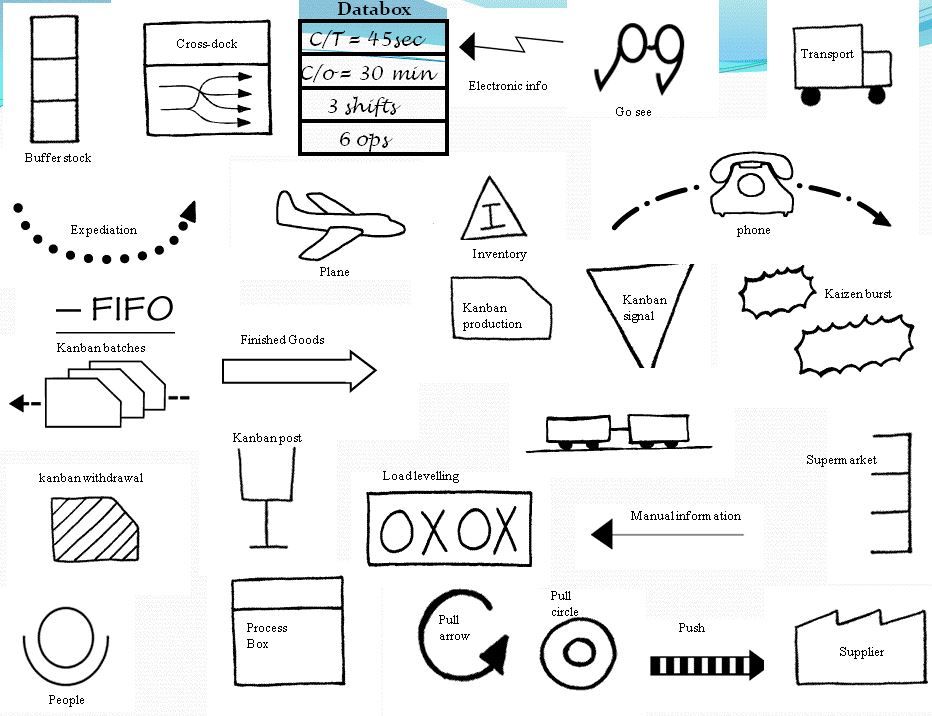
Photo source: leanmanufacturingtools.org
3. Determine the VSM symbols that are going to be used in your plan and ensure all team members have an understanding of the symbols. They should be easy to interpret.
4. Get a cross functional team together who will manage the current state analyses and the implementation of the future state.
5. Complete the current state mapping. This can take several hours or days depending on the process. Walk through the current process in full, and documenting it.
6. Analyze and assess the current state value stream map to decide the opportunities that will enhance flow by eliminating waste.
7. Once opportunities are determined, apply lean principles to create a future state value stream map that yields less waste. The future state should show higher productivity, shorter lead times and better quality than the current state. This becomes the blueprint - or plan for improvement - along with the written plan,
8. Motivate the team to start working to implement the future state value stream map. Dependent on the scope of the project, implementation may take anywhere from 6 months to 18 months.
Tip: Don’t overlook the low hanging fruit of material handling
A VSM takes a critical look at the entire workflow; this includes material handling, which could be easy to overlook at first glance because KPIs are not typically affiliated to it. A 2010 report by Thomas Davich called “Material Handling Solutions: A look into Automated Robotics” found that 30-70% of a goods’ cost can be attributed to its material handling. The issue here is that material handling does not make the company money or, as the value chain map is to determine, does not provide additional value to the customer. How is your operation moving material and how often? Automating the process could provide opportunity to eliminate wastes and create a leaner workflow.
*Irani & Zhour, “Value Stream Mapping of a Complete Product” http://lib.asprova.com/images/stories/lean/lean-manufacturing/pdf/Value_Stream_Mapping_of_a_Complete_Product.pdf
** EMS Consulting Group. “Value Stream Mapping” https://www.youtube.com/watch?v=HKxL_S47yJg