Blog
How to set up a lean factory that works
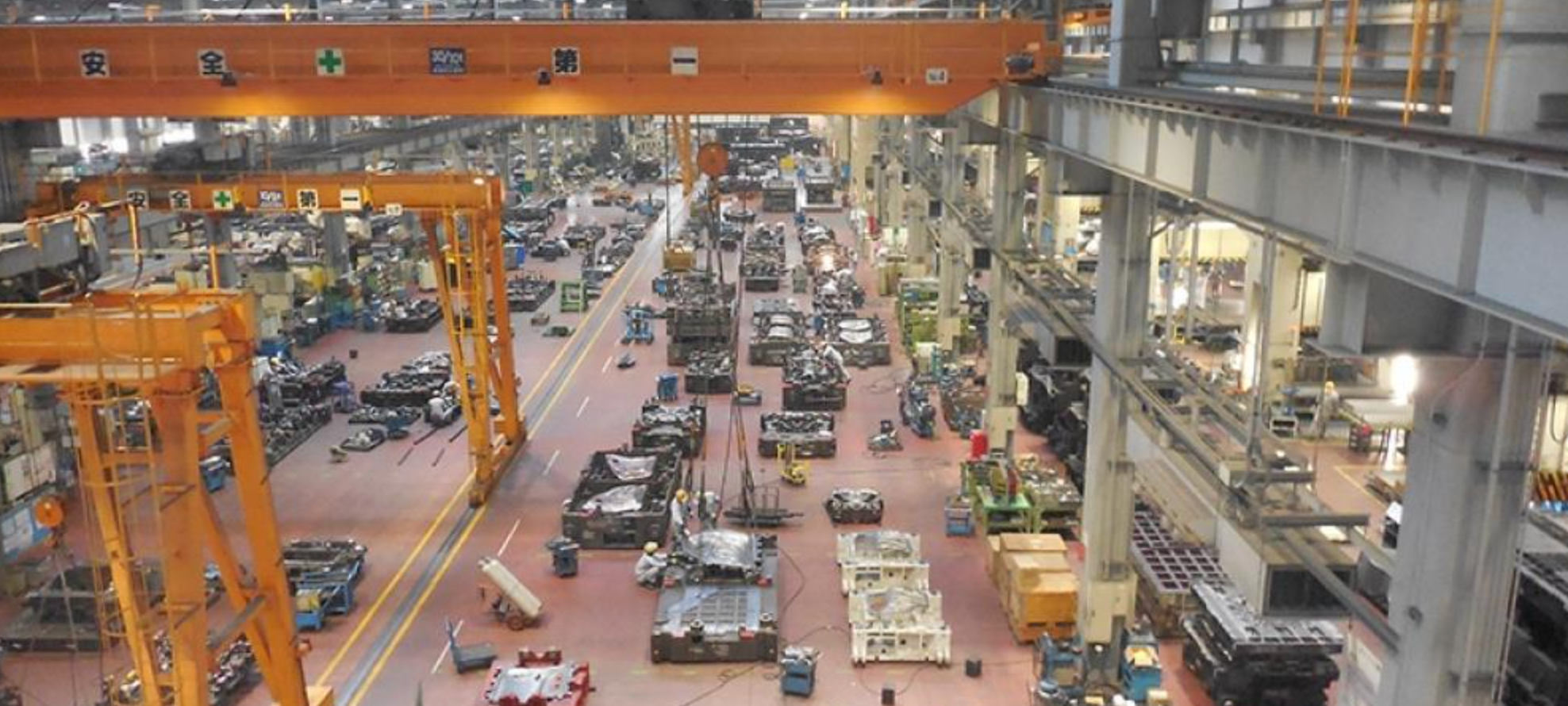
[Original post on Industry Week]
Lean manufacturers have a leg up on speeding products to market, reducing costs and keeping customers happy. In this overview, I’ll share how to engineer, set up and manage the project for a lean factory that works for your specific requirements.
Why set up a lean factory?
A lean factory, or lean-oriented production layout, creates a seamless flow of people, material and information. Well-designed lean factories prevent the build-up of inventory and excess equipment. Lean layouts facilitate visual management. They provide a safe, clean environment to expedite work, regardless of the finished goods being produced. Lean environments can have a positive effect on workforce morale. And it’s all about effective use of time. It is easier to clean and straighten the worksite when there’s little in the way of excess equipment, tooling, and inventory. A well-designed layout will contribute to the ease of maintaining a safe and effective workplace. And, if it’s easier to maintain, it will be maintained!
Two approaches to lean with similar issues
Some companies choose to align operations into a value-stream layout within the same facility. This is called a brownfield approach. Others choose to move into a completely new facility, a greenfield approach. While the greenfield approach is preferable to most everyone, it’s not always practical or affordable. Greenfields have their own series of pitfalls. While it is almost easier to have new machinery installed in a new plant, that’s rarely the case. Can you accelerate the production process to create a window of down time to move equipment? Can you outsource some of the production to another facility or supplier?
Here we’ll discuss the brownfield approach, as it’s more typical and can be more challenging.
Regardless of the location and goals, your lean factory team must consider important operational and policy issues. They must establish and follow concepts that are relevant to your situation. And they must use the right implementation tools.
1. Get the right people
The project team will be tasked to re-engineer one or more facilities to support your company’s vision of a lean enterprise. The project team should be led by your lean leader. There are three ‘sub teams’ for the effective lean factory initiative: The core team dedicated to the full time project, the support team and senior leadership. [more details here].
2. Develop a tollgate process for the project
Many lean companies use the tollgate method. It focuses on a specific, standardized approach to project management, such as new product design, or in our case, a significant re-structuring of operations.
While a comprehensive discussion could be initiated regarding the tollgate process, let’s take a “learn as we go” approach for this article. I’ve provided examples below of how a tollgate process works. Customize each of the tollgates to meet your specific facility or process requirements.
A minimum recommended list of tasks will need to be completed for each tollgate, with descriptions of those tasks. You may find it’s necessary to add tasks specific to your company’s operations. Be sure to include an element of safety in all tollgates. What’s a safe practice on a machine shop floor would be unnecessary in an administrative office.
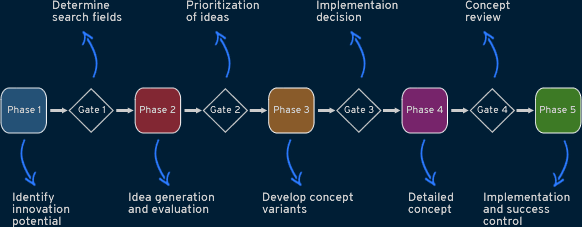
Photo credit: Tech Blue Innovation Center
The tollgates are milestones, with prescribed elements that must be complete by the tollgate meeting date. If any task is not complete, then the project is delayed until that task is complete and ready for review.
Tollgate meetings may overlap – one project may be at tollgate 2, but another might be nearing completion and the review for a tollgate 5 might take place at the same review meeting. Full attendance of the review team is essential for tollgate meetings. There’s no ‘catch-me-up later’ opportunities for the project’s successful on-time, on-budget completion.
Tollgate meetings are a great way to ping the C-suite and stay in touch with senior management. Are there any plans for growth or product expansion? Does the team have enough substantial direction to undertake a continuous flow assembly process, or will the company want to retain the stepped or phased assembly process? Will the company be in-sourcing any processes? Will any insourced process be outsourced? This two-way information exchange is essential to the tollgate meeting.
The tollgate method is the disciplined approach to a project plan. This plan must have dates and milestones for the production surge; the infrastructure upgrades and improvements, and a sequence for the machinery moves. Training, orientation and familiarization for the workforce that has not yet participated in the process is important – and now, timely.
Work resolutely to the plan. If something is delayed, can you work around it? Should the plan be revised for another series of equipment moves? Or, is the delay a showstopper? Risks need to be identified up front so when a situation arises, the plan proceeds seamlessly with little time lost. Each task within the tollgate checklist should be assessed for risk, whether it’s a schedule, cost or technical element. Questions should be anticipated and alternatives should be prepared in advance of each tollgate meeting.