Blog
Improving materials handling and warehouse ROI through automation
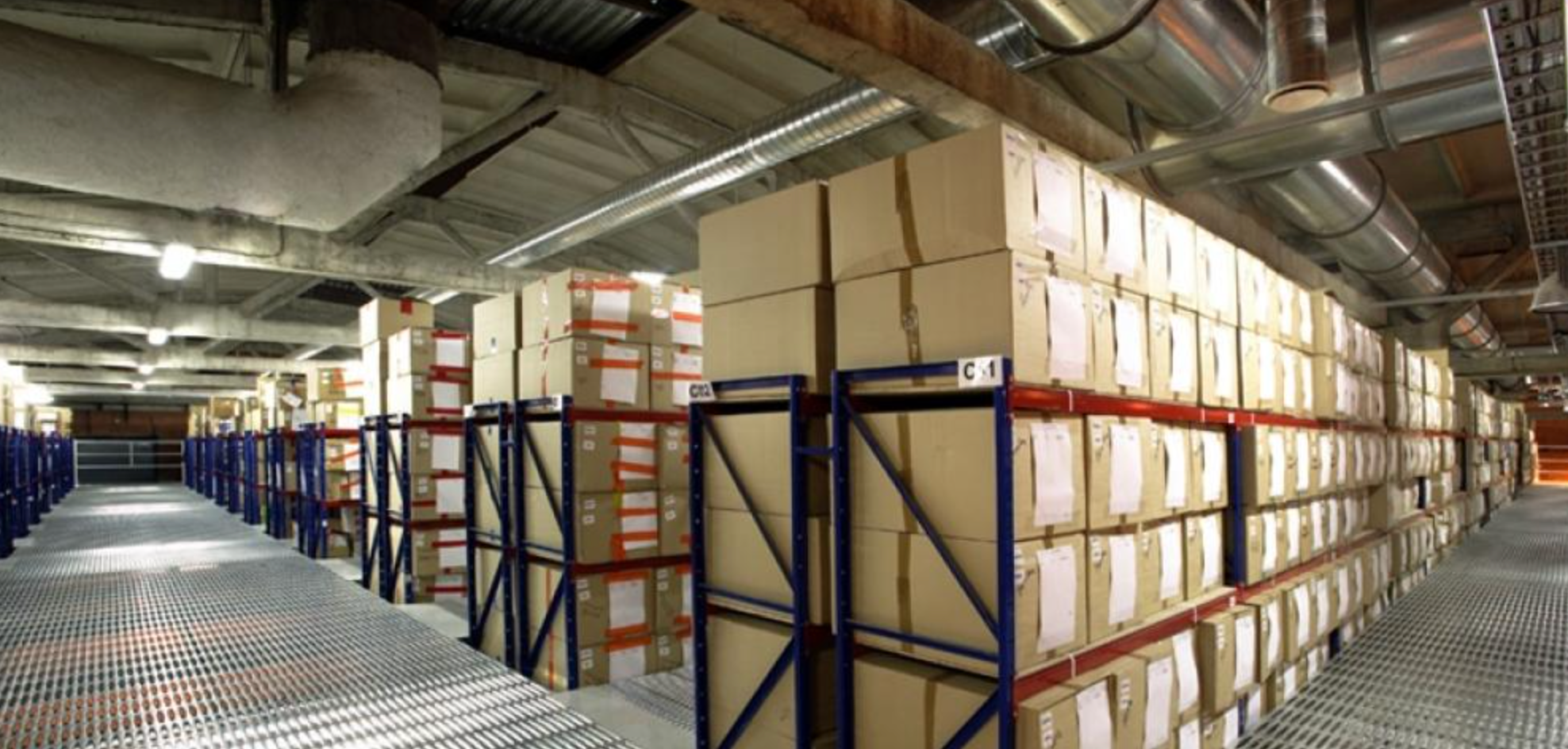
Every warehouse is concerned with operating costs, and automation is one way to reduce expenses and increase efficiency. Automated warehouse operations can lead to increased productivity, better material flow, decreased costs, and provide an improved return on investment. How your company views ROI might depend on how much automation is in your warehouse or distribution center.
Cost considerations in materials handling
Some companies are hesitant to invest in automation in their facilities because of the cost. This is understandable. But, the typical payback period for automated warehouse operations for materials handling equipment is around five years. That seems like a long time. But if the automation drives up the ROI for warehouse costs to the maximum amount, this is completely justifiable.
Labor cost
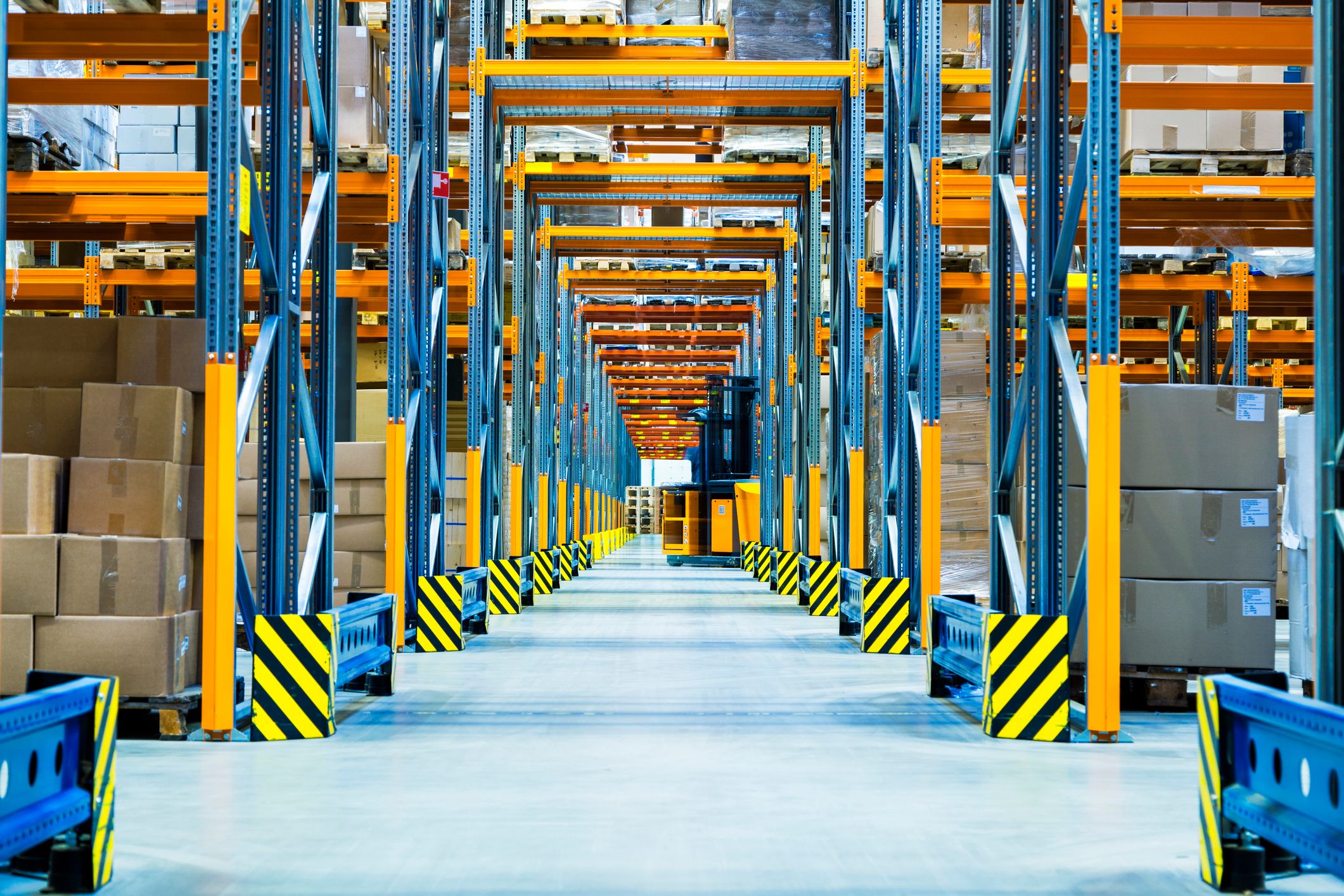
Labor costs are usually a warehouse’s largest expense, accounting for up to 50% of a facility’s total operating costs. Moving product from one area to another takes a lot of effort and manual labor time. Automated materials handling equipment minimizes the number of human touches throughout the product’s cycle through the warehouse and reduces the time it takes to transport materials.
In addition to the direct labor savings and increased productivity, there are indirect savings that only come with automated materials handling, such as lost time due to routine breaks, vacation time, training, and the cost of insurance and workers’ compensation. Automated equipment allows for work to be done consistently around the clock, with no need to break from the repetition.
Positive cash flow
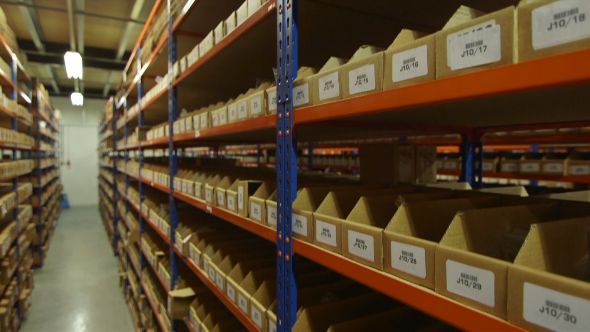
photo credit: envato.com
Over the course of the equipment’s life is when the impact on labor costs becomes apparent. The actual automation piece (autonomous mobile robot, robot, etc.) only represents about one-third of the total cost of installation, which includes the design, tooling, integration and programming. All of those accessorial costs are figured into the initial cost of the system.
Once the system is paid off, now you begin to see the savings generated by the low-cost “labor” of the automated vehicle. For example, an automated system that replaces two manual laborers per shift at $50,000 per year per operator is a significant plus to the bottom line.
Maintenance is a necessity, and there are costs for the replacement of worn parts and preventive servicing. This nominal amount will stay in the expenses column for about 10 years, or until the automation system needs to be refurbished or replaced.
Long-term investment
The investment in automation is not a short-term gain. Productivity will improve immediately, but the real savings of automation shows over time. Automation in the warehouse is a long-term strategic decision to create a competitive advantage. The service life of the automated handling equipment and the duration of the automation project figure into the potential ROI. Considering how much automation your operation needs will help to save unnecessary costs.