Blog
Improving supply chain agility with autonomous material transport
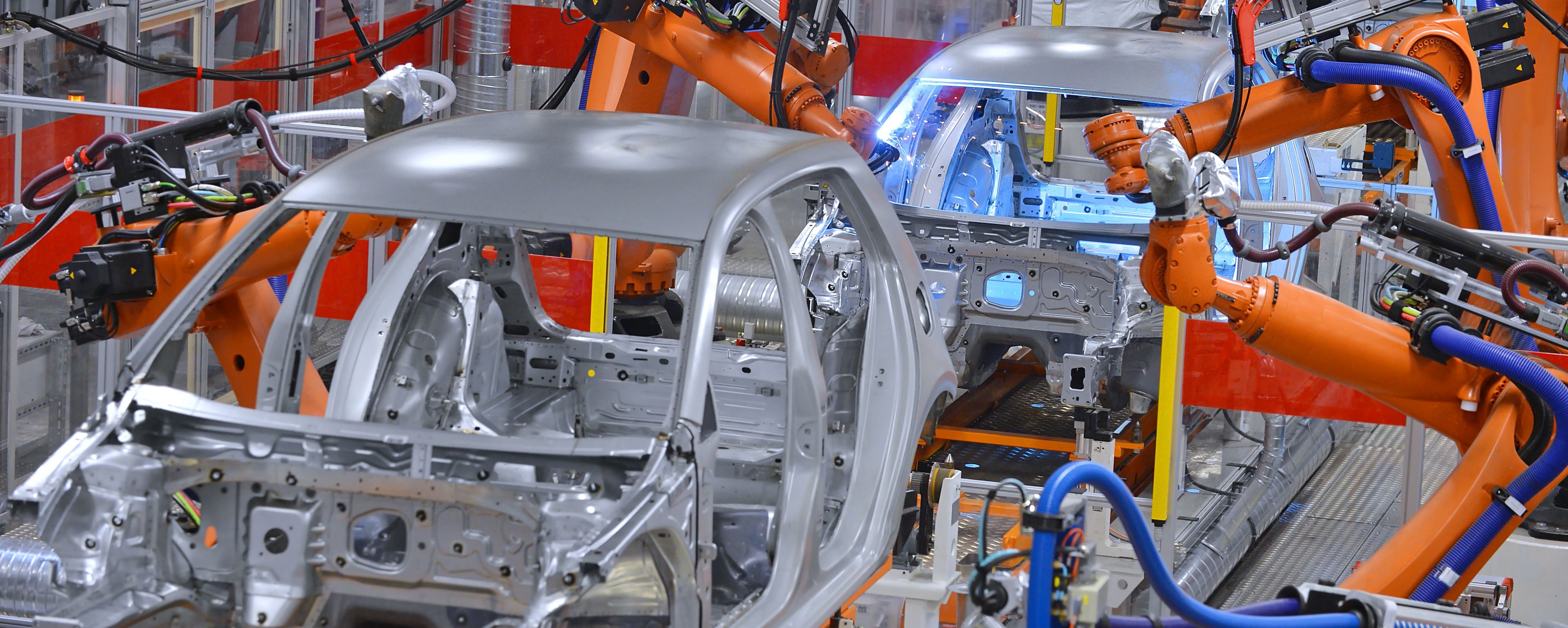
Exceptionally agile companies can process more materials and manufacture products faster than competitors. In fact, according to Plant Magazine’s 2024 Advanced Manufacturing Outlook Report, the top four reasons for implementing Industry 4.0 technologies include lowering the cost of operations, reducing downtime, improving throughput and increasing the quality of the product. In order to be more agile, and move toward a smart, connected factory, most manufacturers surveyed in the report (55%) are spending their budget on robotics and automation, more than any other Industry 4.0 technology.
Within robotics and automation, automated material transport is a key solution that can support the agility needed in supply chains to keep up with competitors. There are two main types of automated material transportation: Automated Guided Vehicles (AGVs) and Autonomous Mobile Robots (AMRs).
Supply chain managers have used AGVs for approximately 15 years. However, AMRs are becoming a commanding force, with the market for AMRs in manufacturing expected to grow about 30% per year over the next five years, according to Interact Analysis.
AMRs don’t require fixed infrastructure, can navigate autonomously around obstacles and respond to real-time environmental changes. If an AGV encountered a barrier, the vehicle would remain stuck until a human intervenes.
AMRs bring materials to the right place at the right time
AMRs use LiDAR sensors and 3D cameras to map their surroundings, detect how far away objects are and replan paths so they can safely (and autonomously) navigate around obstacles. This is one of the ways AMRs ensure they reach their destination in the most efficient manner without the need for physical navigation methods.
In order to meet market demands for faster delivery times and more customized products, Sunview Patio Doors implemented AMRs to improve flexibility and efficiency. 16 months after deployment, Sunview had moved 2.5 million pounds of patio doors with zero safety incidents, while achieving ROI.
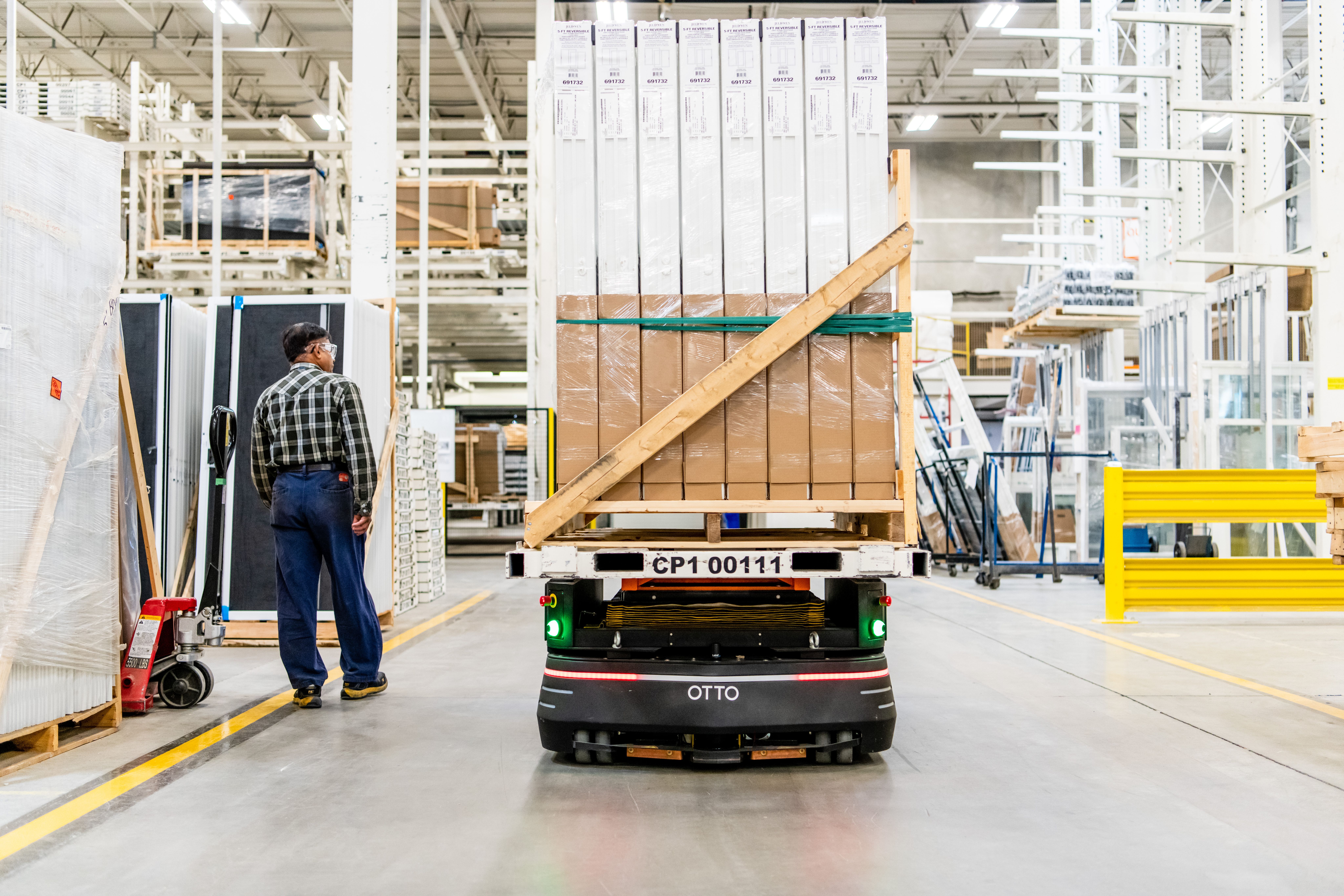
Image 1: OTTO 1500 AMR delivering patio doors at Sunview Patio Doors.
[This AMR] runs like a bus, from stop to stop, the vehicle picks up and delivers product on demand - it fulfills a need that no other material handlers, quite frankly, could.
Kurt Oberparleiter
VP of Operations, Sunview Patio Doors
Integrated material transport streamlines operations
Automated material transport solutions with integration capabilities make processes more streamlined as machines work together to achieve goals. AMRs should be able to integrate with your existing conveyors and stands for seamless material transfer. For example, at an automotive plant in Mississippi, AMRs transported tires to assembly line workers, integrating with existing facility equipment to autonomously unload tires onto conveyors.
Many companies also offer APIs that streamline machine-to-machine communications. When an apparel logistics company invested in an automated material transport solution with integration support, the business anticipated more than tripling its daily output.
Automated material transport reduces unnecessary inventory
Excessive inventory can compromise a supply chain’s agility when additional supplies create clutter. Research indicates that the most agile supply chain companies rotate their inventories an average of 23 days faster than less-agile peers.
AMRs can provide workers with pre-assembled bags of parts that are delivered exactly when needed, preventing a buildup of lineside inventory.
Packages of parts work well for supply chains handling thousands of components each day, such as in the automotive industry. The automotive sector is among the industries that are increasingly investing in industrial robots, as agility in this industry is extremely important due to new customization options becoming increasingly available.
AMRs unlock human potential
Automation technologies are built to enable humans to engage in mentally stimulating tasks that use skills AMRs simply do not have, such as critical thinking, while repetitive, dangerous or dull work is left to the robots. This shift in human potential increases agility in the supply chain, and makes your company a more attractive place to work.
Robots are only doing the jobs that humans shouldn't have been working on in the first place. These are known as the dirty, dangerous and dull jobs.
Robotic Industries Association
According to a report by the World Economic Forum, AMRs will actually create more jobs, rather than replace them, as humans will move toward more higher-value positions. The report states that at least 12 million new jobs will be created as a result of automation by 2025.
Implementing AMRs will allow companies to improve supply chain agility, making them more receptive to market changes and increasing consumer expectations so they can keep up with their competitors.