Blog
How the industrial IoT drives productivity in factories
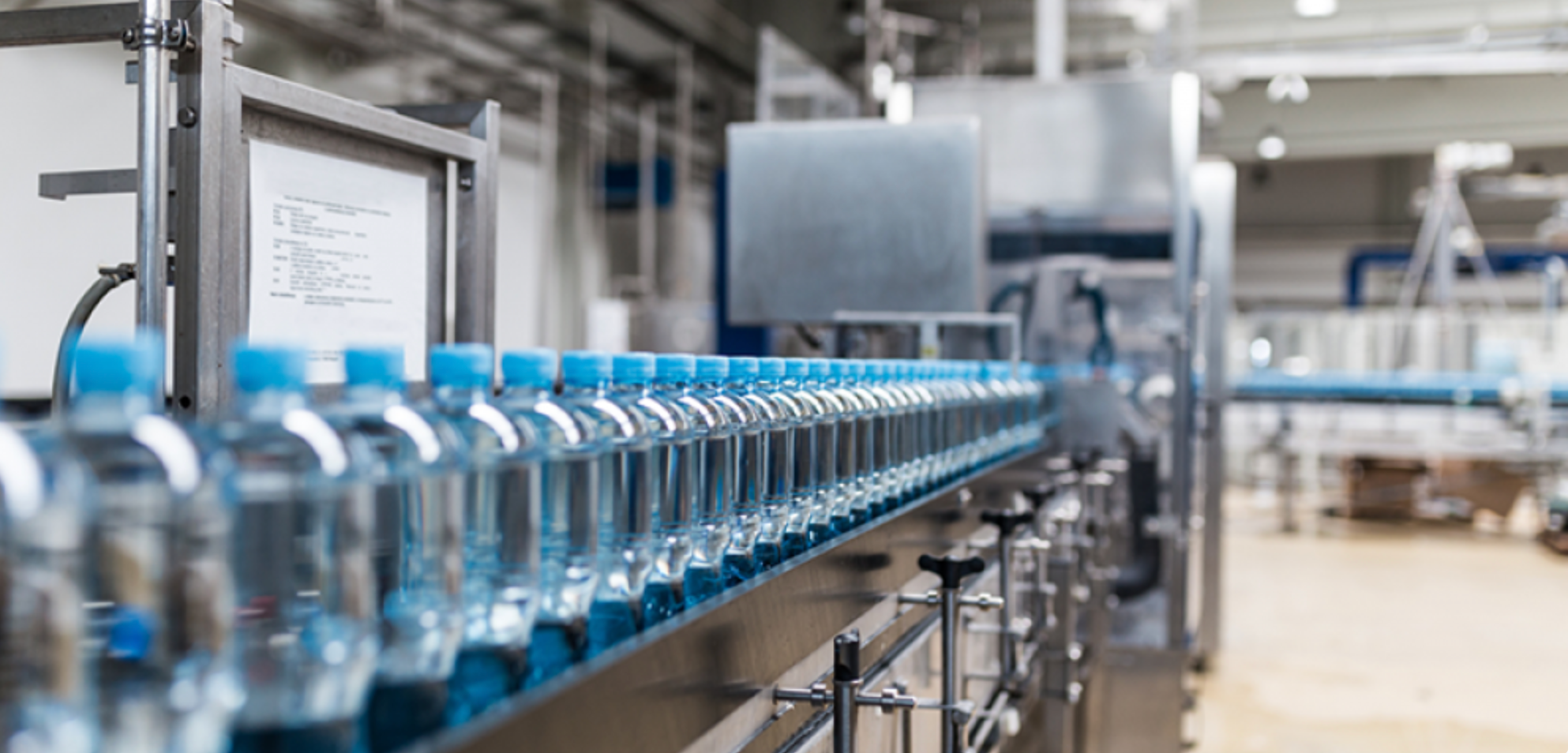
Technologies that offer connectivity and utilize the IoT (Internet of Things) are able to collect and report a tremendous amount of data. As factory operators are continuously looking to solve for advancements, the first question to ask is “what do I know about my operation,” and then “what do I need to know to make effective changes?” Operators must collect and review data today so it can be leveraged as they move into the future. If you’re not yet collecting data, it’s time to start!
Normalize, analyze and validate using the industrial IoT
The old database rule of normalize, analyze, validate is fading fast. In today’s world, there is no normal - we live in an iterative process where the only constant is change. With burgeoning technologies, operators can now engage in agile, flexible processes. We can utilize algorithms that take disparate databases and compare them instantaneously. These capabilities provide you with an opportunity to collect data today, use it as you move into the future, and determine which operational improvements can be made. Consider the following questions to understand the type of data you collect and how you are applying it within your operation:
- How do you apply analytics to your current operation?
- How do you review data and determine if - and how - processes can be automated?
- How are your mobile assets being used and how can you make better use of them?
Not yet collecting data?
Or perhaps you are, but you’re not leveraging it. Consider which forces are affecting your decisions to collect data. As an operator who knows that continuous improvement isn’t enough, you strive for greater supply chain efficiency and visibility. To drive these deliverables, keep in mind that:
- Logistics provides much of the customer experience
- Regulatory pressures within your industry create ripple effects throughout the operation with each change (the food and beverage industry, for example, updates regulations regularly)
- Labor shortage, retention and rates are highly variable factors within your operation and have the ability to significantly impact productivity
Within these key drivers, break down questions that relate to operational performance and success; deconstruct key performance indicators from those questions to determine the pieces of information - or data - that’s required to enlighten the organization. Data from the industrial IoT allows you to look at items such as quality control, fulfillment, throughput, efficiency, and speed. It gives you a 360-degree view of your operation.
Using autonomous mobile robots to track data on the factory floor
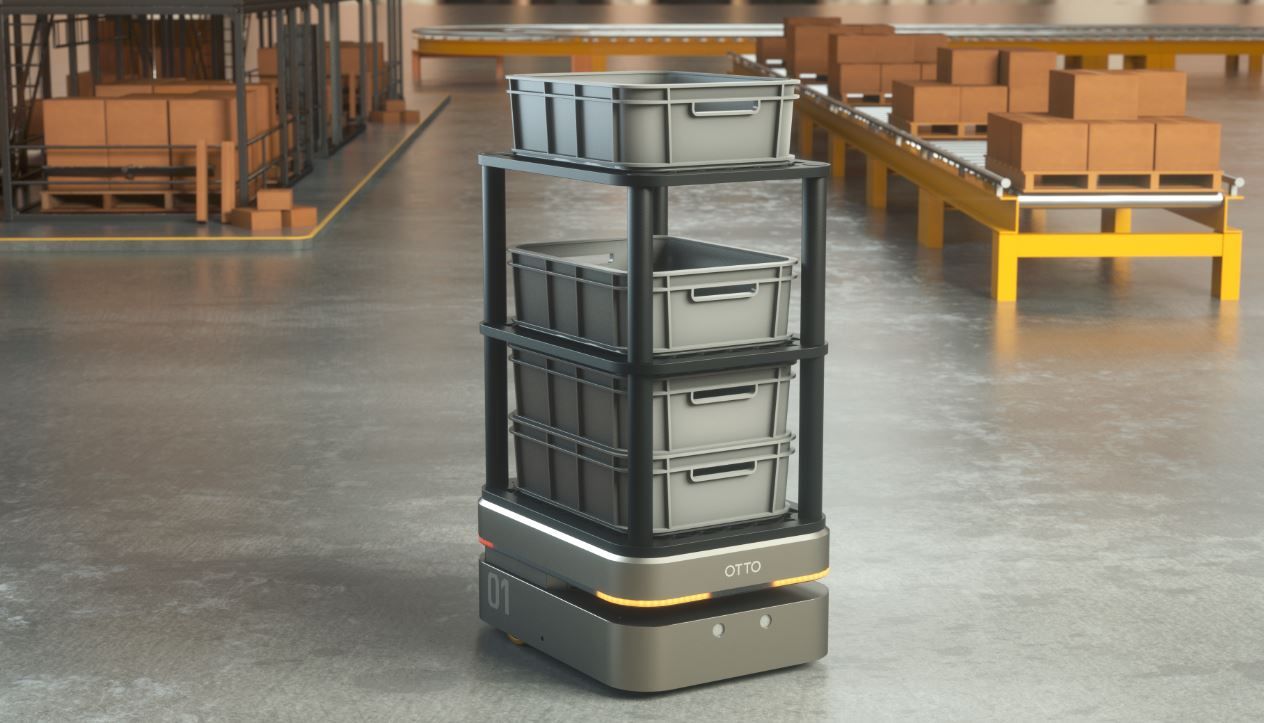
The OTTO 100 autonomous mobile robot used for light-load material transport, and connected to the industrial IoT.
Data provides you with the basis for supply chain optimization. You can optimize assets between distribution channels, from tracking systems on your autonomous mobile robots used for moving materials, to the tracking systems on the delivery systems moving to the final destination outside the factory - from the first mile to the last mile. The autonomous mobile robot is in itself a mobile data collection device, and it is connected to the industrial IoT. It is the one thing that moves throughout your entire operation daily. It gives you ability to pull information from all over your plant, track performance of materials moving in and out of your facility, and communicate data back into your repository so you can see how your systems are operating together. Specific reports that can be pulled from the data collected using autonomous mobile robots for autonomous material movement allow you to determine:
- The number of maintenance calls required on equipment
- The right size of the fleet based on usage
- Idle time and impacts to manage labor
- Layout adjustments
- Understanding requirements during seasonal periods and peak times
In essence, this data will allow you to complete reverse spaghetti tracking so you can back-track the flow of materials and its interactions throughout the plant.
Benefits of connectivity and IoT on the factory floor
With this data base of information, you can evaluate which processes can move from human-decision making to automated decision-making. Data will help you understand what can be automate and how much you can automate over the long term. More capability is becoming available every day it seems, but the ‘Smart Factory’ with industrial IoT won’t happen overnight. Start small, and make the most of existing IoT investments in your facility, then build to greater capability overtime.