Blog
How industry 4.0 material handling technology impacts critical KPIs
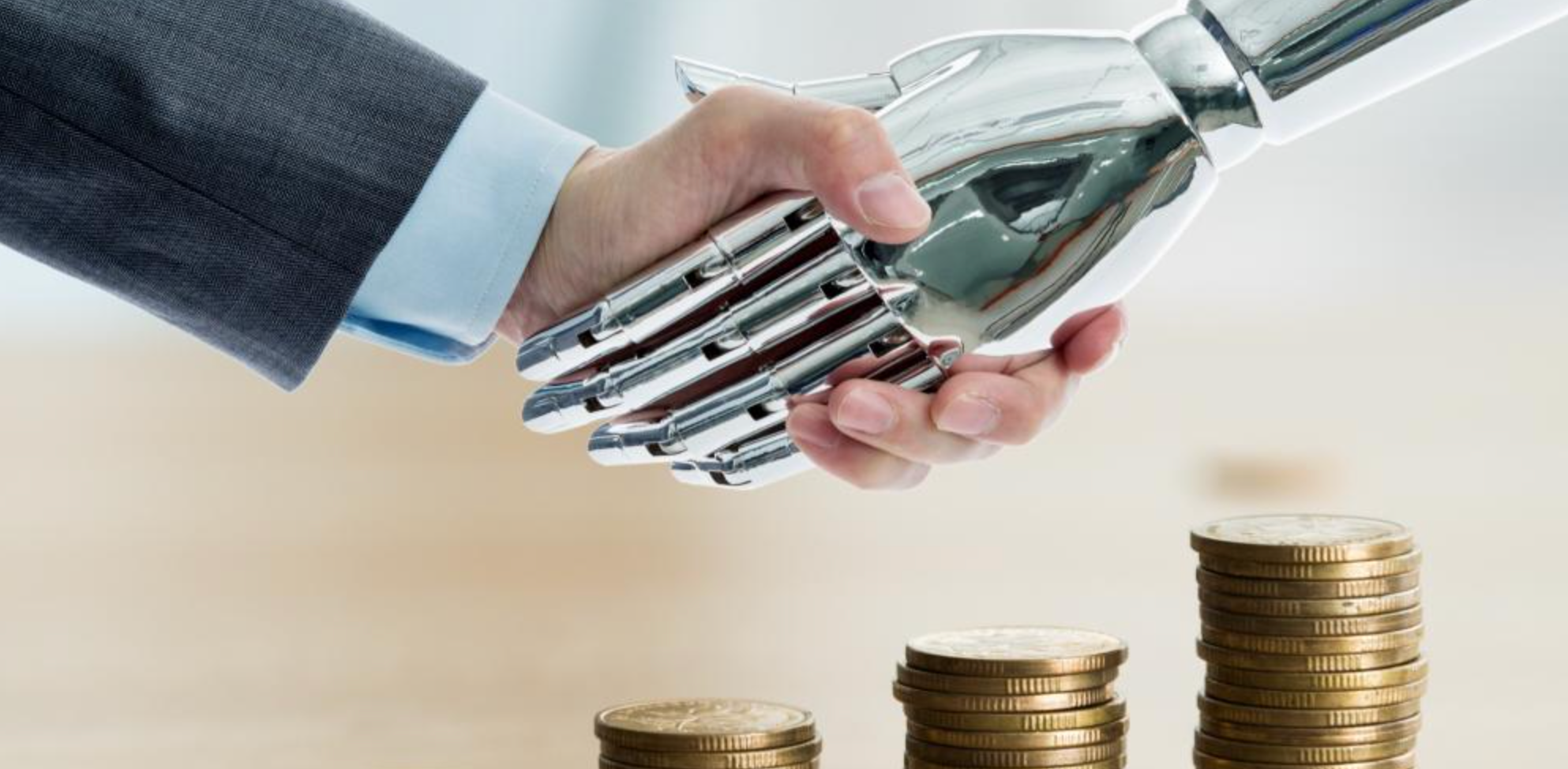
Material handling in warehouses and factories is an inefficiency often forgotten about, or completely ignored, in the manufacturing industry. However, material handling is an essential variable cost to consider, as it accounts for, on average:
- 25% of the workforce
- 55% of the factory floor, and
- 30-70% of the total cost of a good.
Inefficiencies in material handling can be extremely costly, but there is a solution: automation.
How can efficient material handling positively impact your critical KPIs?
Efficient material handling impacts numerous KPIs in your plant. Efficient material handling results in better material flow to cells in the assembly line, and ensures the packing and shipping line is not overwhelmed at the end of each day. Automation can also replenish workstations faster by delivering the right material, at the right time, to the right spot, while ensuring the worker in the workstation does not have to leave their cell to perform such a dull task.
For example, King’s Hawaiian, a California-based bakery and restaurant, experienced the benefits of automating material handling in their storage facility. After adding new management, control system software and making use of several types of robotics and automation technology, the bakery was able to merge two separate facilities into one big facility.
The facility’s capacity increased by 5,500 pounds of finished food per hour—an 85% improvement. Through automation, King’s Hawaiian also completely eliminated the risk of forklift damage to the freezer, an issue that had been previously plaguing the bakery’s storage facility.
With optimal material flow, you can also reduce the risk of injuries, improving safety and maintaining your KPIs.
Over 37% of fatal accidents involving industrial trucks reported by OSHA in 2019 were caused by a forklift.
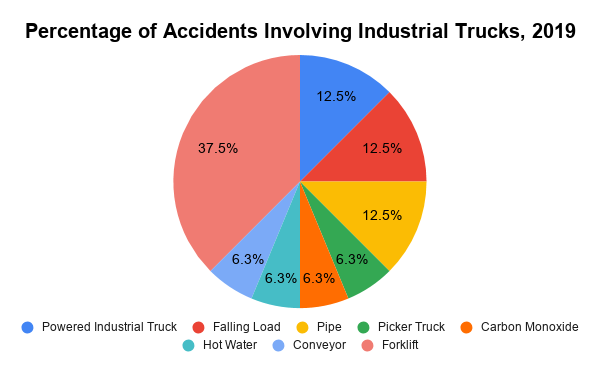
Chart 1: 37.5% of accidents so far in 2019 have been from forklifts, as reported by the U.S. Department of Labor: Occupational Safety and Health Administration
It’s also not uncommon for employees to get hurt while pushing and moving materials around the production floor. In fact, storage and manual lifting and handling of materials are two of the top five ways people working in warehouses get injured. In 2017 alone, there were 12,750 cases of warehouse workers taking days away from work due to injury.
Proper material handling eliminates these risks and positively impacts your critical KPIs by putting employees back to work and away from the dangers of manual material handling.
AMR technology boosts material handling efficiencies for modern manufacturers
The future of material handling is autonomous mobile robot (AMR) technology. AMRs can automate numerous applications and while being extremely flexible—all without replacing jobs.
1. They have numerous applications
Autonomous mobile robots for warehouses and manufacturing facilities, such as OTTO AMRs, can help you automate your facility’s delivery and pick up, kitting and picking, long hauls, lineside delivery, pull calls by an operator, and more. Walmart plans to automate many applications within their facility, including using AMRs to transport goods from one warehouse to another in Bentonville, Arkansas.
We are working with city and state officials to obtain the approval we need to operate and plan to start the pilot program this summer with the aim being to learn about the logistics of adding AVs into our ecosystem, operation and process changes, and more opportunities to incorporate this emerging technology.
Molly Blakeman
Spokeswoman, Walmart
2. They are flexible
AMRs are more beneficial than AGVs (Automated Guided Vehicles) in that they don’t use fixed, defined paths to move around, nor do they halt the operation when encountering an obstacle. AMRs use onboard sensors, machine learning and AI to navigate spaces efficiently and safely. AMRs can also change their routes in real-time to dynamically avoid any unexpected roadblocks.
For example, HIROTEC America combined the Yaskawa Motoman dual-arm robotic manipulator with the OTTO 1500 AMR in order to work with near-zero supervision, and achieve lights-out manufacturing.
The 24/7 operation achieved by Hirotec America would not possible with AGVs, as they cannot account for unpredicted obstructions and have to come to a halt until the issue is resolved, which requires additional personnel on the floor at all times.

Figure 1: While AMRs can detect and avoid obstacles in real-time, AGVs remain halted until a worker can remove the obstruction on its path.
3. They don't replace jobs
Employees refrain from straining and higher-risk jobs involving material handling, and instead focus on more creative, higher-value added jobs. AMRs don’t replace humans, but instead, make them more efficient, productive and excited about their tasks. An AMR automates the dull, repetitive task of moving materials on the warehouse floor, so humans can focus on their manufacturing specialities during more hours of the day. Instead of replacing jobs, AMRs simply take on the tasks that workers are too skilled to do.
Additionally, one of the most common challenges manufacturers are continually facing is increasing labor costs and a shrinking labor force, with a projected decline of 640,700 jobs in the manufacturing industry by 2028. Automation can help fill the jobs that are difficult to hire for.
With 75% of the global workforce being comprised of millennials by 2025, it is also important to consider work preferences in order to attract more workers to the manufacturing industry. Millennials consistently rank manufacturing and logistics as their least preferred career, because they consider the industry boring and outdated. Through automation, companies can attract more young workers to their jobs while creating greater efficiency in operations.