Blog
Interoperability is key to lean manufacturing in Industry 4.0
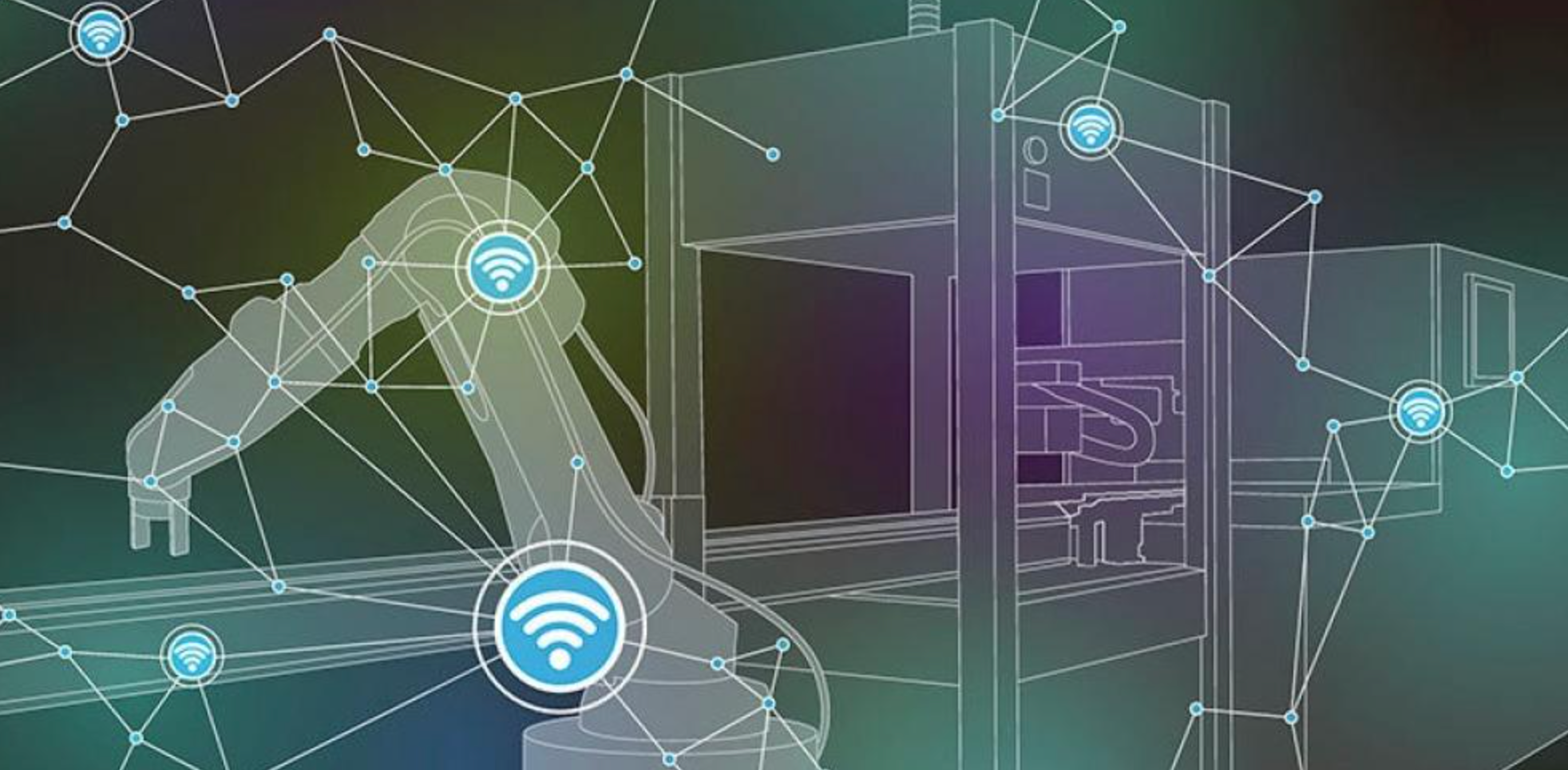
Today, improving manufacturing requires more than simply finding ways to operate faster and reduce expenses. Modern manufacturing is about being smarter. This is where the importance of interoperability, a core concept to Industry 4.0, and the exchange of data throughout a connected factory becomes key to improving manufacturing operations.
Interoperability is defined in the manufacturing industry as the electronic communication and management of data through the Internet of Things (IoT). It has emerged to become an important component of the modern factory and Industry 4.0 – even if some manufacturers have lagged with their adoption.
Why is interoperability important?
Interoperability involves accessing real-time data that leads the way to a new approach for how companies can improve their production operations. It allows manufacturing partners (including customers, suppliers, and other departments) and their machines to share information accurately and quickly. The result is more effective, resulting in more reliable operations.
The goal of Industry 4.0 is to achieve low-cost production efficiencies while leveraging automation. In this new paradigm, supply chain and material handling processes also become integrated across the company, creating a lean manufacturing system that is efficient and flexible – all helped by the open communication enabled by the IoT and data interoperability.
The challenges of adoption
An obvious obstacle to interoperability is the challenge of connecting different business process systems, or for smaller companies, the lack of any systems at all. It’s no surprise that some manufacturing industries, such as automotive and aerospace, are leaders when it comes to using connected technologies. In fact, Frost & Sullivan’s “Automotive 4.0” report states that 55% of large and small automotive OEMs and SMEs have already started investing in digitizing their plants. With time, the improvements with automation and information flow will continue to trickle down to other industries.
And despite the hurdles, interoperability between devices and assets is being used by increasingly more factories. Seeing the benefits, many are modernizing their plants and facilities to have a standardized methods of communication, data, analysis, and security. The drive for true connectivity has even become a common denominator for cloud-based industrial equipment, with machine learning capabilities across connected devices now a reality.
Data collection for lean operations
Interoperability and the IoT are obvious enablers for data collection and its better use by manufacturers. Many are investing heavily in tools for leveraging and analyzing this newfound asset. At the core of interoperability is the ability for users to access information from multiple sources in one seamless application.
The end use of this information as a management tool can extend beyond just operating efficiency on the factory floor – but extend to benefits related to other areas like inventory management and supply chain optimization. Available and free flowing information is a powerful tool for companies who have made this connection.
Manufacturing companies who’ve established the infrastructure for enabling data interoperability are able to better serve their customers and optimize their operations – with the added benefit of a broader visibility across their entire business.
Interoperability is not just about connecting machines. It’s a method of supporting better decision making that improves how manufacturers operate. Better yet, this is still a young concept and continuing to evolve. Technology will only serve to make establishing interoperability for manufacturers easier, and its benefits greater.