Blog
Inventory storage: Opportunity for lean material handling
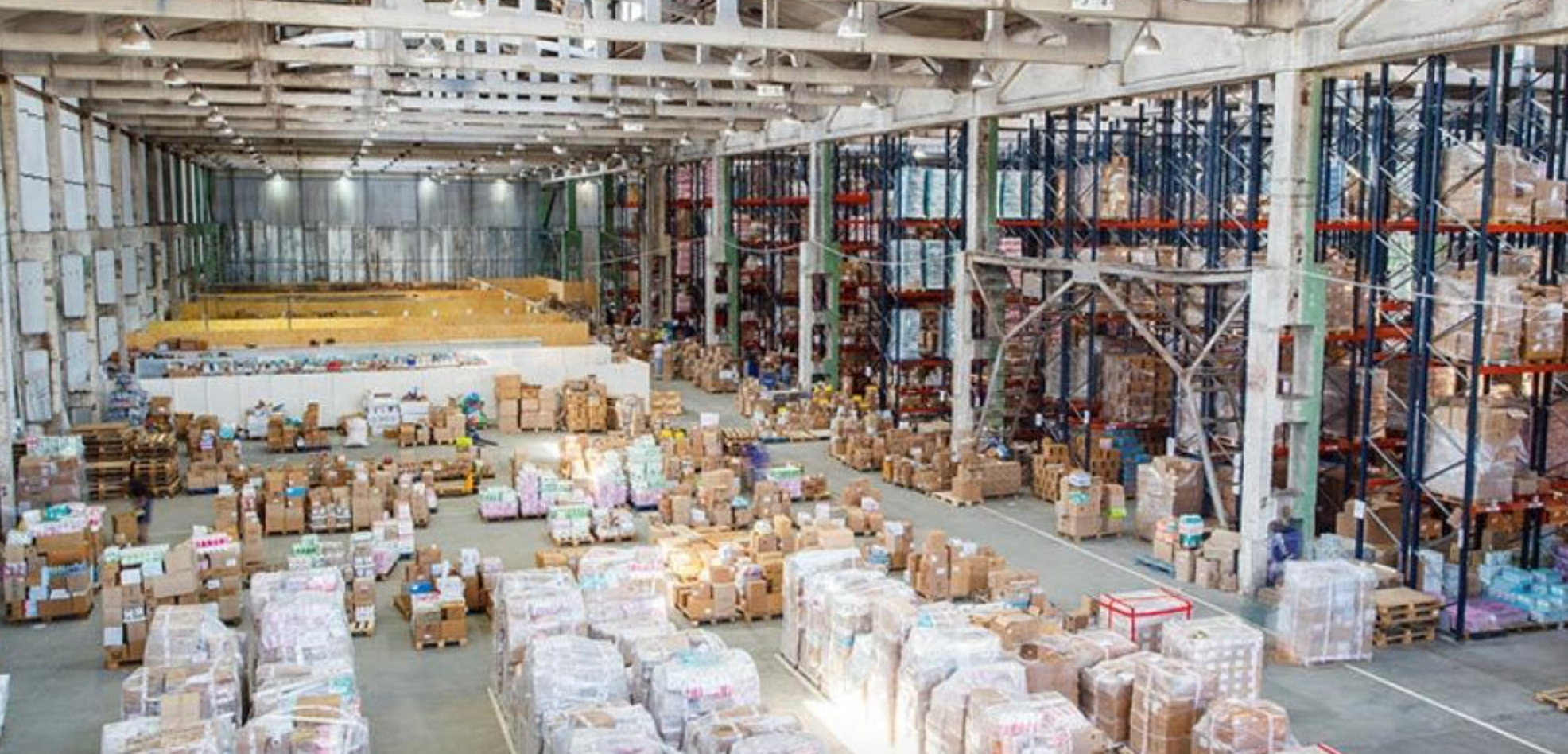
Manufacturers, warehouse operators and distribution centers continually look for ways to improve efficiency and productivity. Implementing lean material handling principles combined with increased use of automation and robotics has helped in many areas. A lone holdout, lineside delivery, remained a challenge. This post, Lineside Delivery is Broken, outlines some of the key environmental factors that impact material transport to the line:
- Governmental regulations affecting safety
- An inability to find and retain workers
- High wages
- Inefficient technology behind many automated delivery vehicle systems
- Increased mixed model manufacturing
These environmental factors are giving rise to the way that manufacturing operators order, store and handle inventory. How inventory is processed and moved to and from the assembly line is changing, and technology offers new ways of doing so efficiently.
Achieving lean material handling for inventory
Taking control of inventory and the method of delivery lineside continues to be a focal point with manufacturers. Many companies involved in lean programs are moving toward a central inventory location within a plant. “If inventory is stored in multiple locations in a plant, the manufacturer loses control,” according to Rick Harris, co-author of several books on lean material handling including, Making Materials Flow. “But once you have it in one location, the manufacturer gains control of the inventory.” This control aids in greater awareness of the materials available, and a need for these materials lineside. Centralized inventory also streamlines material transport to work cells using routes that are more efficient and often through a variety of delivery systems.
Consumption-based replenishment
A related trend to centralizing inventory is consumption-based replenishment. On a broad level, consumption-based replenishment aids in ensuring products manufactured are inline with demand of the consumer. However, the concept also is applicable in maintaining material delivery on the plant floor. Systems using technologies like RFID provide real-time inventory monitoring on the assembly line, while transportation modes like autonomous mobile robots provide information of how and when those parts are moved to and from the line. As parts are scanned and then used on the line, the part demand is monitored and information sent to inventory signalling the need for replenishment.
Centralized inventory combined with a consumption-based approach to material replenishment in theory should improve efficiency in delivery lineside, but current delivery methods prevent theory from becoming reality. Because kitting of parts is moving to a centralized location, delivery distances tend to increase. Then a consumption-based model adds to the challenge by requiring smaller quantities delivered lineside to match demand. This increases the number of deliveries to sub and final assembly work cells, causing an increase in the level of congestion in the aisles further adding to safety concerns.
Manual material handling vs. technology
The increasing number of skilled workers retiring is another trend driving change in lineside delivery. According to marketplace.org, new workers entering the job market will not replace the number of Baby Boomers retiring. Furthermore, technological advances cannot completely offset the shrinking workforce. This results in a need to maximize use of available human labor where jobs increase productivity while allowing technology to improve efficiency in other areas including lineside delivery.
Manufacturers have used robotics to augment industrial workflows for many years. Attempts to implement robots for material delivery have been met with mixed results. Since the 1950s, the material delivery standards have been designed around forklifts, tug vehicles, autonomous guided vehicles (AGVs) and people with pushcarts. These standards were built on the mindset of bringing the most material possible lineside in the least amount of trips. Because the line requires materials one at a time in regular intervals, the results add to congestion lineside and in the aisles. The addition of high mixed model manufacturing further exasperates the situation with the need for more frequent deliveries and intensifies the accident potential. Now, advances in technology are driving the trend to use robotic vehicles for lineside delivery in order to fill the labor shortage.
New technologies lead to lean material movement
Flexibility is required to accommodate these evolving processes and delivery materials lineside in the most efficient, and lean, way possible. Fortunately for the material handling industry, technology has evolved with our needs and is founded on new capabilities like artificial intelligence and sensors that enable new functionality.

Autonomous mobile robots (AMR) complement these tools and trends mentioned. What separates it from other robotic delivery systems currently used in material delivery is the SLAM technology, which enables the AMR to move freely about the plant floor mapping out the most direct route as it delivers components for use on the assembly line. Vehicles are not guided by magnetic strips or pre-programmed routes, meaning they will deliver parts where required without stopping at other locations. AMRs enable point-to-point delivery to the assembly line from a centralized location. This manner of material delivery also facilitates small quantity delivery lineside. The result is improved flow that meets lean principles. Additional benefits of material delivery using AMRs are reduced aisle congestion and elimination of safety risks, when compared to conventional material transport equipment like person-driven forklifts.
The AMR has the capability to receive a low inventory signal from the line, pick up the parts and deliver directly to the work cell according to the preferences of the line worker. Consequently, the AMR aids the implementation of lean processes and works in conjunction with other technologies to maximize productivity lineside and allow for better allocation of skilled workers in productive jobs.