Blog
What skills are needed for workers to thrive in today’s manufacturing facilities?
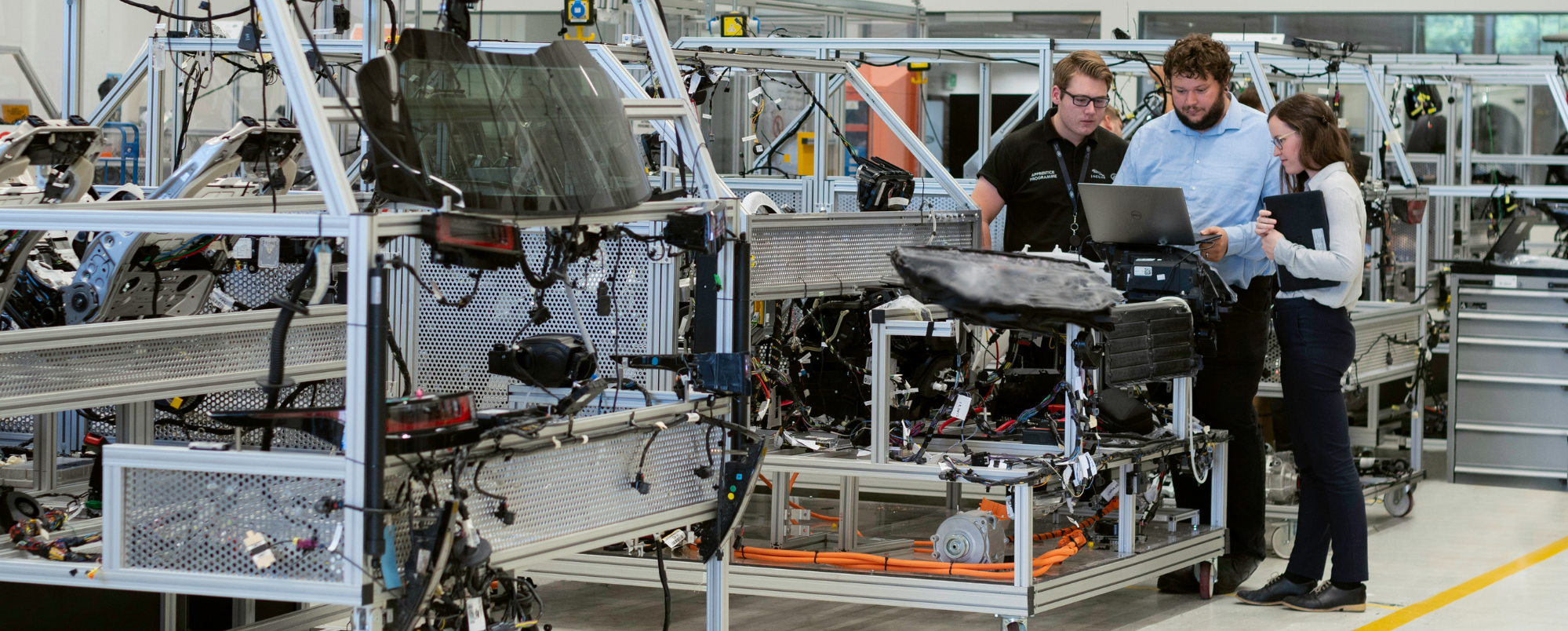
Today’s manufacturing facilities are rapidly changing, and the skills needed to thrive in this environment are evolving with them. With the introduction of new technologies on the rise, companies are increasingly investing in upskilling or reskilling their employees to keep up with the ever-changing industry.
Companies are deploying various 10-year strategies to prepare for the disruption that comes with the increasing adoption of innovative technologies.
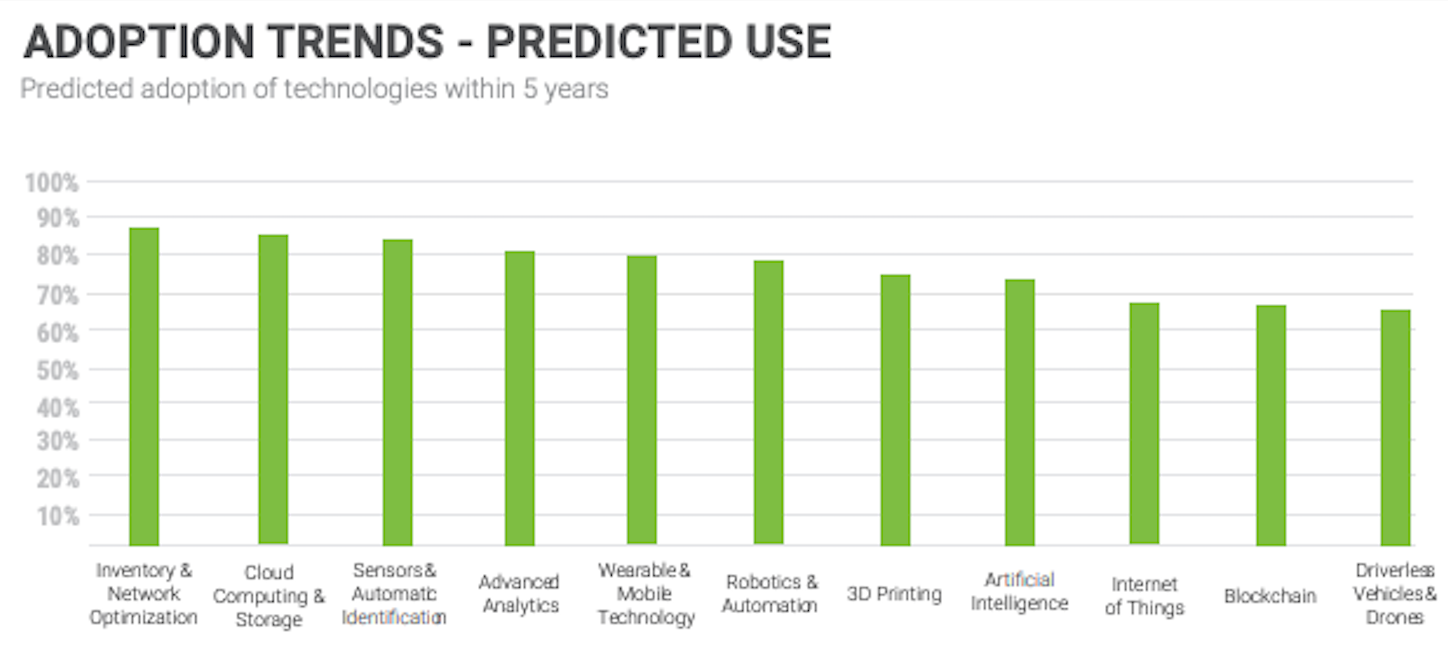
Image 1: Actions taken in preparation for the changes in the next 10 years.
Most efforts underway involve piloting new technologies, retraining employees, or hiring workers who have the desired tech-centric skill sets. With high-tech manufacturing solutions becoming commonplace in facilities around the world, these 10-year strategies can help members of the workforce anticipate what changes are to come.
A 2021 World Economic Forum report has predicted that over half of all employees worldwide will need to reskill or upskill by 2025. Companies that invest in their employees are more likely to attract and retain the talent they need. In fact, a Gallup report states that almost 90% of Millennials—currently the largest worker segment in the United States—greatly value opportunities for professional development and career growth.
The way you are going to retain this generation is not by training, but rather by developing them. Developing your people says, 'I want to help you achieve what you want to achieve,' and that fosters greater loyalty.
Randy Bradley
Assistant Professor of Information Systems and Supply Chain Management, The University of Tennessee
As more and more manufacturing facilities adopt innovative technology, workers can grow with their companies by adapting their skill sets. Here are some examples of highly sought-after skills in the manufacturing industry:
1. Openness to change
The adoption of innovative technologies is already underway and rising quickly. The 2023 MHI Report predicts that the use of robotics and automation technologies in the supply chain will reach almost 80% within the next 5 years, saying that the technology “has become table stakes for operations to remain competitive.”
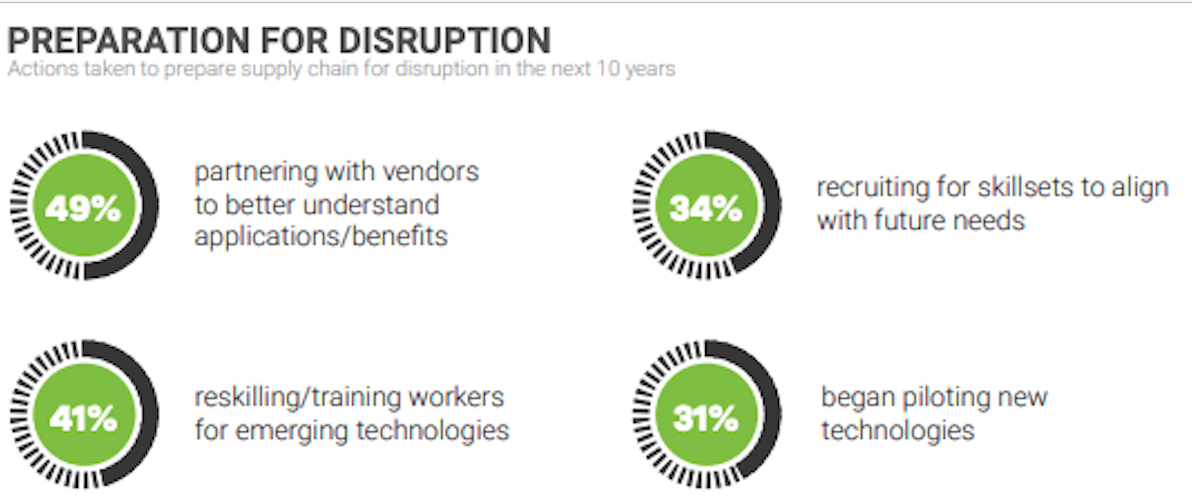
Manufacturers are looking for workers that embrace new technologies and look forward to what the future holds. Employees with a growth mindset will thrive in an evolving environment by remaining open to learning how to operate new technologies and working alongside robot co-workers.
2. Problem solving & critical thinking
As supply chains grow more complex, employees who tap into their problem solving and critical thinking skills will unlock new opportunities for themselves at work. Innovative solutions need internal champions who are willing to learn how the systems work and can find new ways to improve efficiency through data analysis.
Creativity and adaptability just can’t be automated, particularly when it comes to problem-solving.
Michael DiTullio
President, Digital Thread, PTC
3. Interpersonal skills
Robotics and automation are capable of many repetitive tasks, but the key to successful manufacturing operations is the interpersonal approach people bring to the floor. People possess the unique capabilities of creativity, leadership, collaboration, and managing conflict, all of which are skills necessary in manufacturing environments.
Soft skills are vitally important to our business. Manufacturing is a people business and we need leaders that can connect with people.
Tamberlin Golden
Executive Director of Diversity, Equity and Inclusion, General Motors
In fact, compared to both all-human teams and fully-automated factories, manufacturing processes are faster, more efficient, and more cost-effective when people and robots work together. Veo Robotics found idle time was reduced by 85% when compared to all-human teams. When people and robots work side-by-side, they reach an ideal middle ground between speed and versatility. The unique skill set of workers and the efficiency of robots make up for any shortcomings on either side alone.
Subscribe to our newsletter
Stay in the loop on product news, case studies, upcoming events and more.