Blog
5 reasons to use material handling automation
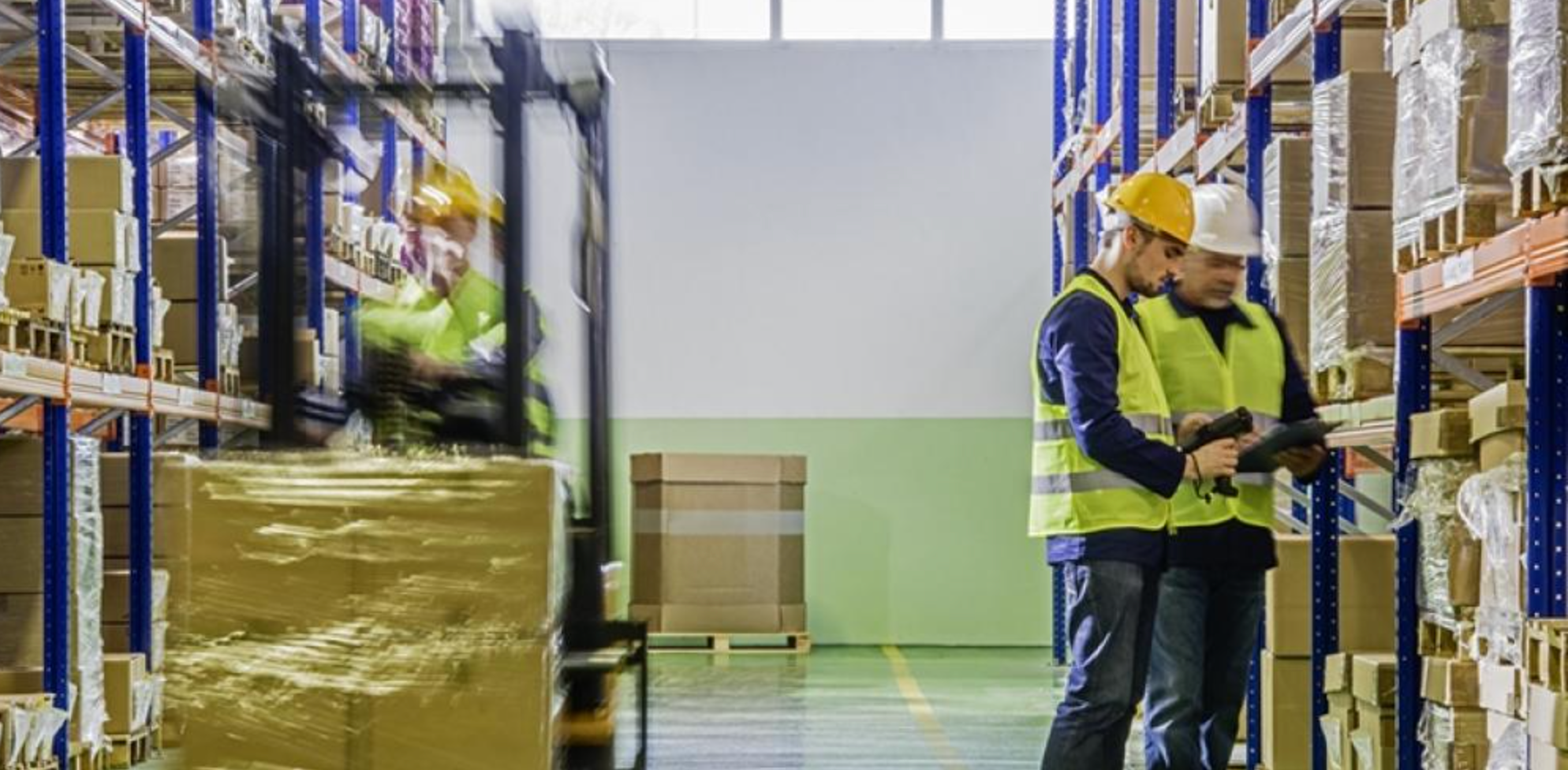
The concept of the last mile, and companies who are focused on making those deliveries, seem to get all the attention these days – largely thanks to Amazon and the talk about drone deliveries for the products people buy online. Many manufacturers, however, know that there is just as much value in optimizing the ‘first mile’ as there is in the last mile. Indoor material handling plays a critical role within every company’s entire production process and supply chain.
Reasons for material handling automation
Like most processes, optimizing the first mile is made possible by the use of technology, but it takes the right tools to fully enable automation in your manufacturing. Advanced equipment (such as Autonomous Mobile Robots - AMRs) and the Industrial IoT (Internet of Things) are two core technologies required to put this idea into practice.
Advanced manufacturers understand that automation, and the first mile, should begin with how materials are received, stored, and transported from the instant they enter a facility.
Manufacturers are under constant pressure to do things faster and cheaper (but never at the expense of quality). And of course, any investment in technology to meet these goals has to have the proper ROI.
5 benefits of using material transport technology
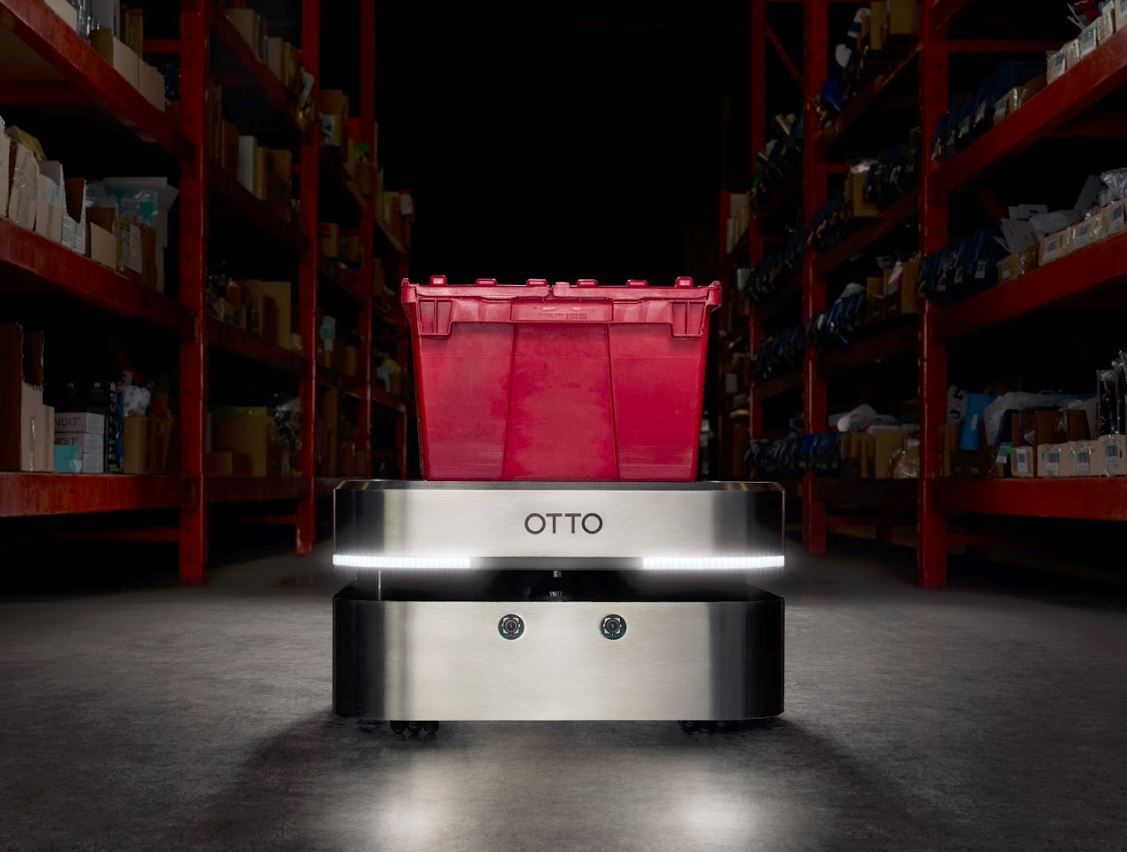
Automated material handling technology can provide manufacturers many obvious and measurable benefits, such as decreased operating costs and increased throughput of materials, but they can extend further. Here are 5 additional examples of how manufacturing automation technology can benefit manufacturers by improving the first mile.
1. Better manufacturing KPIs
Connected technology in the plant provides real-time access to data. When enabled from the beginning, data gathered and shared in the crucial first mile allows the full manufacturing lifecycle to be benchmarked and more complete KPIs established.
2. Better labor management
The benefits also translate to better management of the human workforce. For one, with AMRs in use, employees can be repositioned to higher-value roles that require more specialized skills or the ability to handle complex tasks. In most cases, manual material movement from storage to line-side is not a high value-add activity. With this capability served by an AMR, manufacturers are less exposed to repercussions of labor shortages or high turnover common to those jobs.
3. A connected factory
Technology in the first mile can also connect ‘islands of automation’ within the factory. Collecting and sharing data through sensors allows information to move up or downstream within the operation - just in time manufacturing - enabling other parts of the factory to better plan and anticipate delays or changes.
4. Flexible manufacturing
The ability to leverage complete data also allows on-demand flexibility throughout the manufacturing process since materials can be delivered, in advance, to the exact spot they are needed. This saves the time required for line personnel to retrieve materials from a centralized pick location.
5. Improved customer experience
Optimizing the first mile using material handling automation will improve company profitability and customer satisfaction. Servicing customers starts with manufacturing that runs on time, and the first mile is key to that equation. The cost reductions and operating efficiency gained by automating the first mile enables companies to offer more competitively priced products, while certainty around production completion enables better delivery performance.
The importance of the last mile in the supply chain will never be lost, but manufacturers realize there is no last mile without out the first. Applying the right material handling technology produces measurable cost savings while bringing an immediate ROI.