Blog
Material handling process best practices
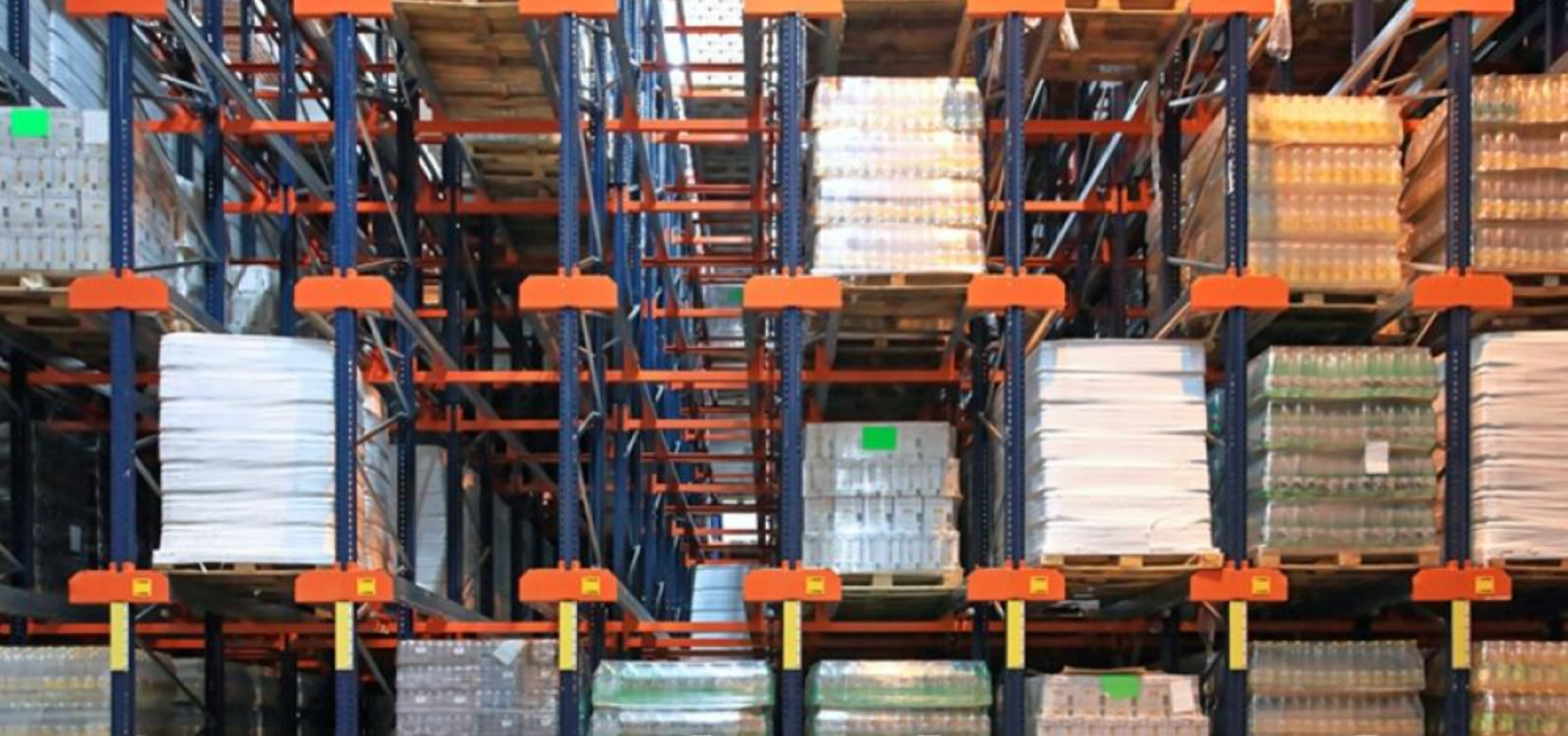
The foundation of warehouse efficiency is set by the material handling process. Inefficiencies in the handling of goods result in decreased performance throughout the warehouse operations, which in turn risks the loss of business to competitors. Customers demand instant availability, service without errors, and customized products, and it is imperative to keep an open mind about the resources available to solve these issues. Many distribution professionals adopt best practices in their material handling processes to drive higher productivity and lower costs.
Automation systems / material handling robots
Automation is the catalyst for process improvement and drives efficiency in the warehouse environment. Companies that use flexible material handling processes find that they are able to match the needs of their business with the appropriate automation devices. Material handling automation includes equipment such as RF devices to direct warehouse personnel, conveyor systems, AGV Technology (Automated Guided Vehicles) and AMRs (Autonomous Mobile Robots), and automated storage and retrieval systems (AS/RS).
Put-away processes
Another best practice is the direct put-away. Products are put away the day they are received to alleviate space issues, cut down on transaction mistakes, and reduce the chance for damage. They are moved directly from receiving to their final location, bypassing staging. Allocating the proper amount of resources towards this task ensures that product will be in the pick rack to be picked and shipped, which results in better order-fill rates.
Warehouse Management Systems (WMS)
A WMS system that can assign locations for inbound materials by way of the ASN (Advanced Shipping Notification) or upon receipt is needed for direct put-away programs. Automated conveyor systems that sort and divert are another technology that assists in the put-away process. These systems also aid in tracking travel time from receiving to storage so the best and fastest route is used. Since most WMS systems can also support task interleaving, the non-productive travel time is also reduced.
Radio-frequency Identification (RFID)
RFID serves to identify products from almost any position. Radio-frequency identification uses electromagnetic fields to automatically identify and track tags attached to objects. Each tag can hold a lot of information that can be changed as products move throughout the warehouse facility. The use of RFIDs along with other technologies, such as sensors, can facilitate real-time tracking within the warehouse.
Organized warehouse
A warehouse that is clean, organized, and neat will result in a more efficient material handling process. Poor work conditions can cause product damage, safety issues, and waste as time is spent searching for materials. A disorganized warehouse has a direct correlation to the time it takes to put items away. The latest technology is useless unless the warehouse is clean and organized so it can work efficiently.
Expedited materials
Many warehouses have a special process for items that need to be expedited once they are received. The WMS system allows for cross-docking, which is moving certain products to satisfy an open order or replenishment request. It flags the item by matching it to the open order when the ASN is received. The product should be moved as quickly as possible with minimal handling.
The goal of any material handling process is to make sure goods travel quickly and safely from the time they enter the facility to the time they exit. The receiving of materials and products affects many areas of the warehouse downstream, so getting a solid process in place will keep other operations on track. Failure to implement a best practices approach when it comes to material handling will result in inefficiencies in the operations of the entire warehouse.