The impact of innovation in material transport technology
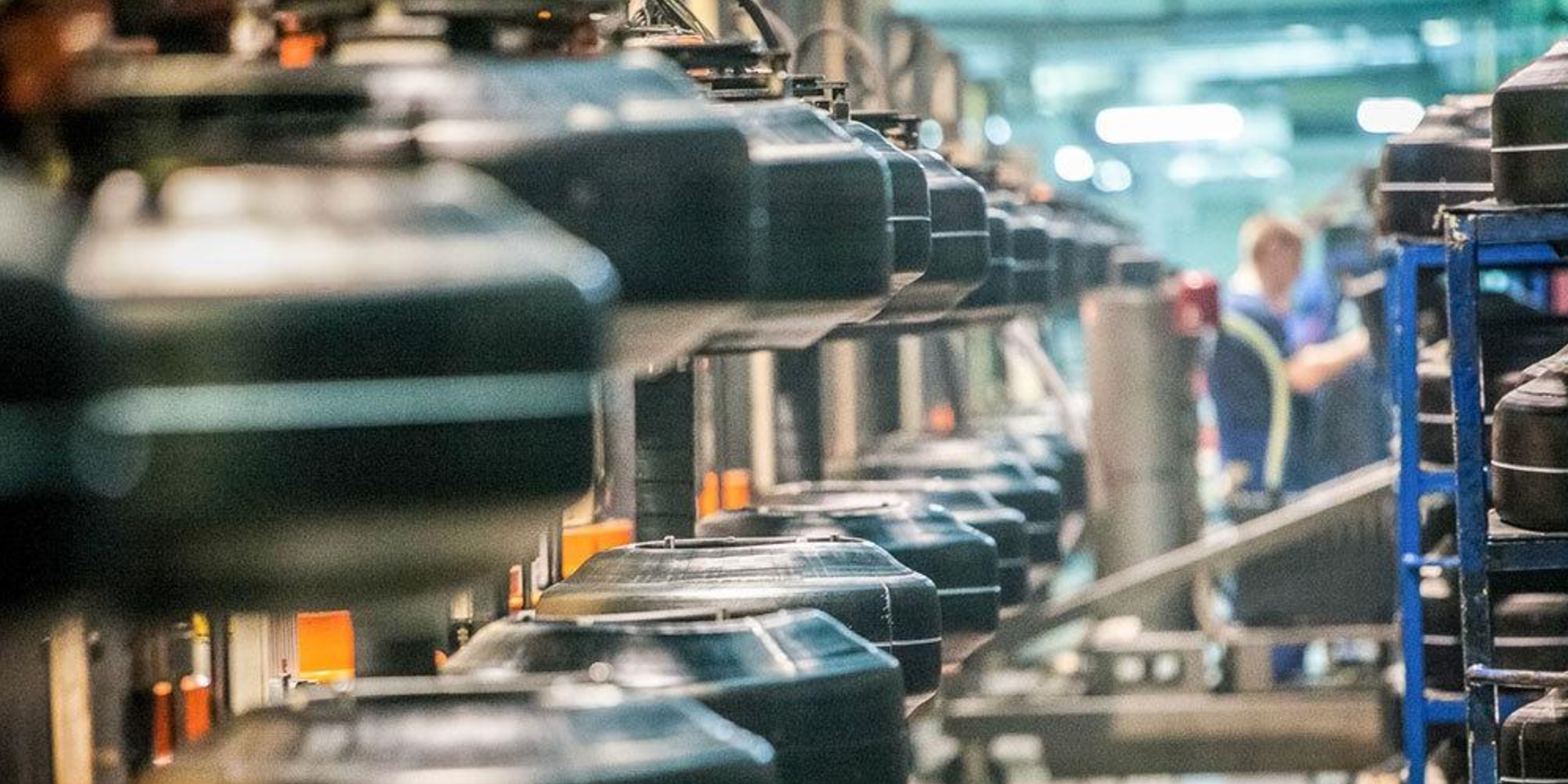
While largely unnoticed by people outside the industry, an area significantly impacted by new technology is the material transport function of manufacturing. Changes to material transport technology are changing the way materials move throughout the manufacturing process. The result for companies has been greater operating efficiency, improved access to data, and more optimized business operations as a whole.
Did Material Transport Technology Kill Just-In-Time?
There are a lot of market forces at play driving innovation in the space. Manufacturers and their supply chains are under constant pressure to do more, faster – and with less cost. Because of this, the JIT model of the past is no longer good enough for every situation today. This said, JIT is not dead, but it does require complementing processes to ensure optimization.
It’s common now for manufacturers to employ BTO (Build to Order) or ATO (Assemble to Order) models as a part of JIT, in which a portion, or all manufacturing, is driven by customer demand. And of course, technology and automation in the factory (including advancements with 3D printing) play a big role in this trend.
Robotics and Automation
According to a recent Wall Street Journal article on automation in the manufacturing environment, robots are going to ‘change the economic calculus for manufacturing’. By reducing labor costs, they could in fact make U.S. manufacturers competitive against other countries again. This is no small claim for obvious reasons.
The use of robots on the manufacturing floor once sounded like something from a sci-fi movie, but has already transformed the industry. Many forward looking factories and warehouses operate with a fraction of the crew needed in the past. This is not all about reducing employee count either – robotics handle many dangerous and repetitive tasks that are simply too difficult or unsafe for people.
Sensors and the IOT
Over a third of U.S. manufacturers are currently using smart sensors technology to collect data to enhance their manufacturing processes. Communication sensors are being used to track items, signal maintenance upgrades, and make decisions about orders and shipments. Sensors are able to monitor production issues at the plant level, leading to less damaged materials and increased customer satisfaction.
IoT (Internet of Things) technologies gives manufacturers instant information to optimize speed in the warehouse without adding costs. It is entirely feasible that every step of the supply chain and manufacturing process will connect directly to the internet in the near future.
Predictive Analytics
Figuring out ways to leverage supply chain analytics is one of the top trends in the industry - and one changing things at the materials management level as well. Better data collection enables machine learning and predictive analytics which can be put to good use.
Leading manufacturing companies are now able to better predict demand during peak seasons, product trends, and optimize their entire manufacturing and distribution network. Suffice it to say, the availability of this data is changing the way manufacturing businesses are making decisions about materials, supplies, staffing, and shipping.
The Trend Will Continue
The use of automated material transport and other technologies will continue to grow in the manufacturing industry. As material transport technology advances, it will also become more specialized and accessible to a broader range of manufacturing companies. The cost savings and operating efficiency provided by new technologies are already reshaping the world’s manufacturing landscape, becoming a primary driver of the total cost of manufacturing. This is an evolution sure to continue.