Blog
Autonomous technology for your manufacturing facility
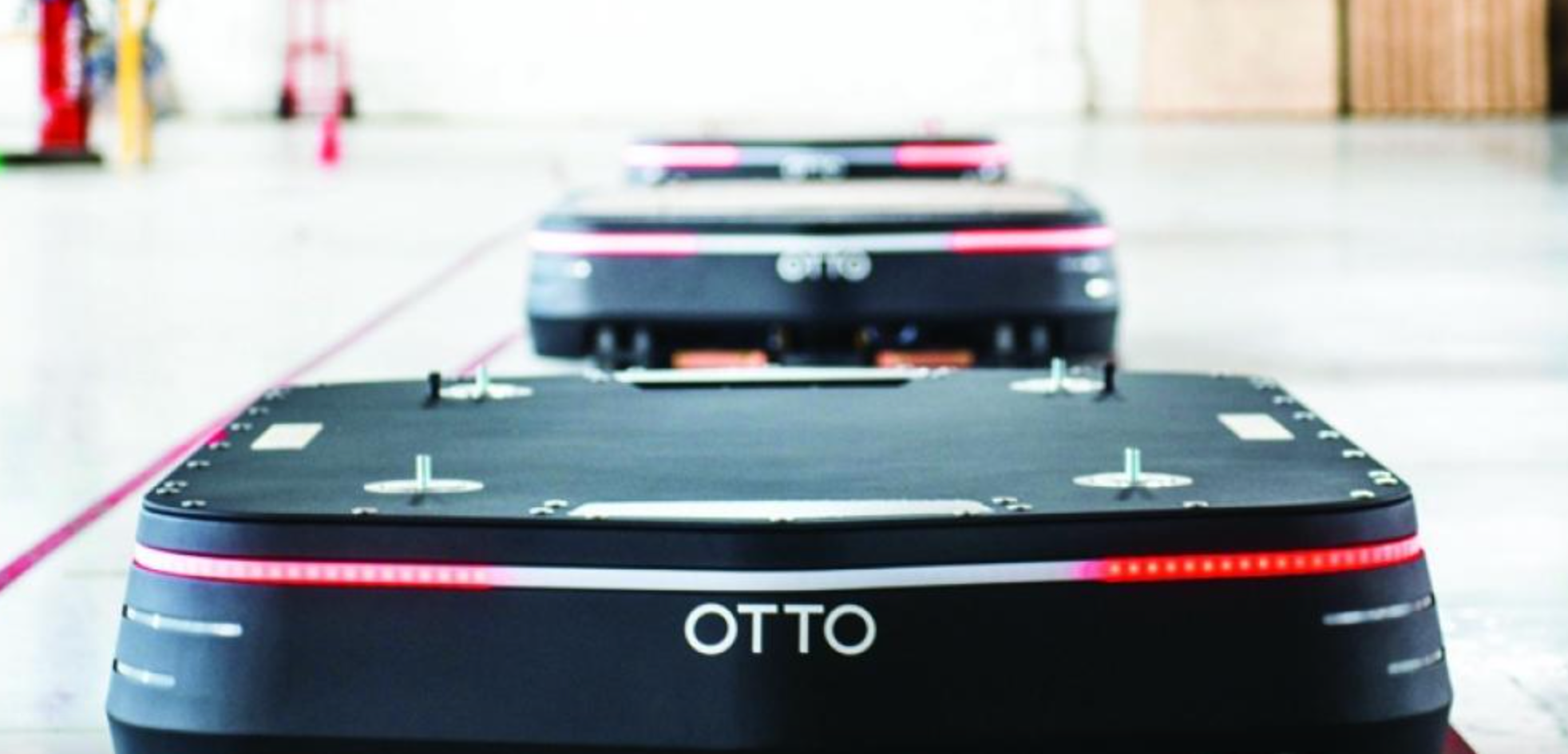
On September 27, 2017, leading manufacturers from across North America joined us for a live webinar on the current state of material handling, the challenges associated with it, and how self-driving technology can help make significant gains in a manufacturing facility. The following serves as an introduction to the information presented during the webinar.
Why the material handling problem is an opportunity for manufacturers
Inefficient material flow is a huge problem in manufacturing today but also presents a big opportunity for those manufacturers looking to make enormous improvements on the critical KPIs in their facility. Of all the changes and improvements that have happened in the past to improve the processes and operations of manufacturing, materials handling as a core competency has remained largely unchanged.
Though it is considered non-core, a recent university study found that up to 70% of the total cost of a good is made-up of material handling costs.
- 25% of the work-force
- 55% of the factory floor
- 30-70% of the total cost of a good
Material handling challenges
As non-value-added work, material handling has been particularly hit with some of manufacturing’s biggest challenges:
- Inconsistency,
- Lack of predictability,
- A constant battle of recruiting and retaining people to do these jobs, and,
- Keeping those who are in material handling roles safe and productive.
For years, continuous improvements through the lean methodology have helped manufacturers make incremental gains year over year. But as we enter a time of rapid acceleration in business, it has become necessary to take giant leaps forward rather than those small steps of yesterday.
Poll: “How do you move materials in your facility?”
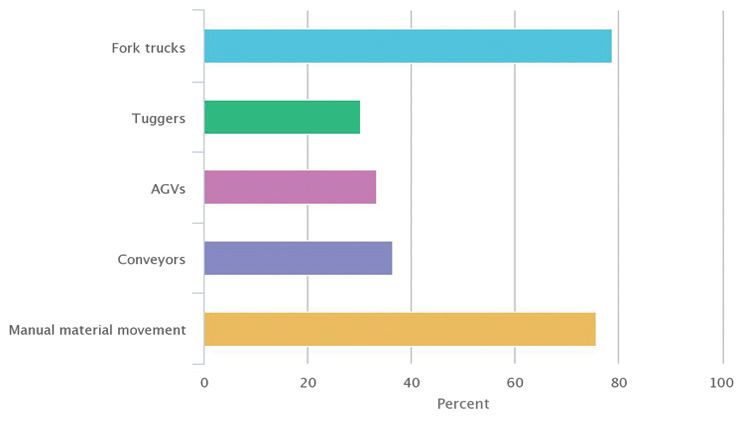
The unpredictability of material handling
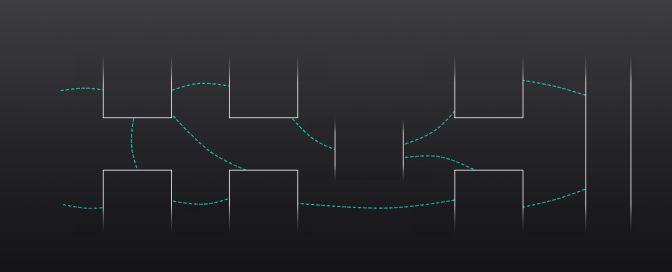
As materials move unpredictably throughout a plant, controlling the costs becomes a problem. These costs, along with other metrics, are critical to the overall measures for the success of the business. Material movement connects processes and keeps production moving. And when production is able to continue moving, significant savings are made.
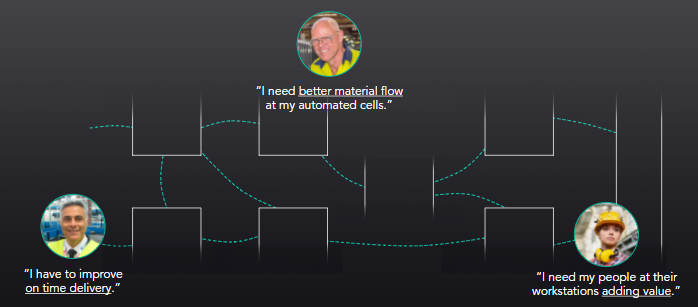
Many manufacturers have similar issues with material flow:
- Replenishing automated cells.
- Replenishing workstations with kits.
Evening out flow so packing and shipping aren’t overrun at the end of the day.
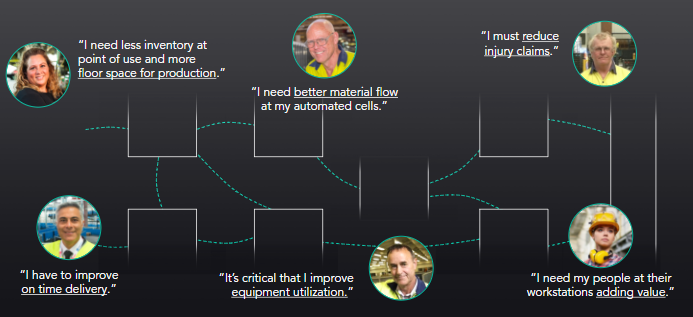
And it is not only those sections directly on the plant floor that can be affected by inefficient material flow and handling practices.
Poll: “Have you looked into automating material handling?”
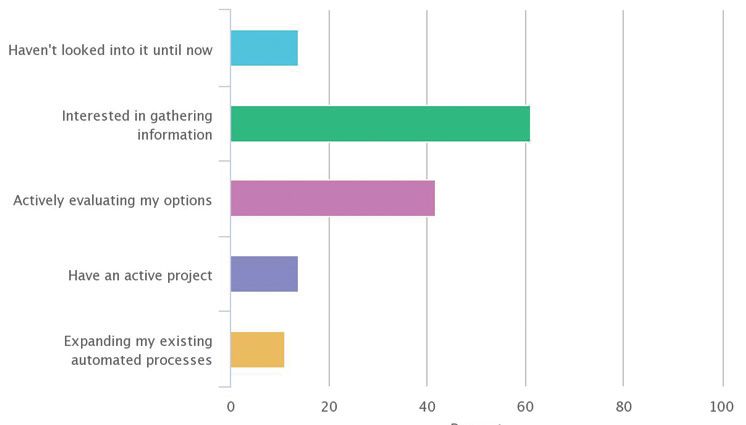
Many people say automation is the answer. But where do you start?
Big investments have already been made by so many manufacturers into automated products that promised to help with inefficiencies. But for many plants, material flow is still determined by people.
Finding, training and scaling people is a constant battle for manufacturers yet human labour remains the default for material movement in manufacturing. This makes people the most valuable yet variable resource. Especially when those people are tasked with the non-value-added work of simply moving materials. People cannot continue to play such a key role in one of the most non-value-added areas of manufacturing.
To date, the technologies offered to solve the human equation of the material handling problem have been restrictive and lacking in the flexibility and adaptability that modern manufacturers require. AGVs have a very limited use in most facilities and sadly, significant investments have been made in them by manufacturers only to be pushed aside to a dusty corner because of inflexibility and unreliability.
When first introduced to autonomous mobile robots such as OTTO, many manufacturers immediately compare them to AGVs. But the differences are many.
To find out more about the differences between AGVs and AMRs, check out our comparison guide here.
Start your engines for a different kind of material flow
Autonomous mobile robots don’t just do the same thing over and over again. OTTO is not limited to programmed repetitive work. It’s not just driverless, it’s autonomous and intelligent.
Because of the flexible, adaptable autonomous technology of OTTO, it is capable of many different applications inside of a warehouse, distribution, and manufacturing environments.
To find out more about the many applications for OTTO in your manufacturing facility, and to hear how OTTO is able to perform, the various capabilities of the OTTO 100 and OTTO 1500 and to hear how some of our customers are currently utilizing self-technology in their facilities, check out the full recording of the Meet OTTO webinar here.