Blog
Pioneering perspectives: “Customer feedback has shaped OTTO into the AMR leader it is today”
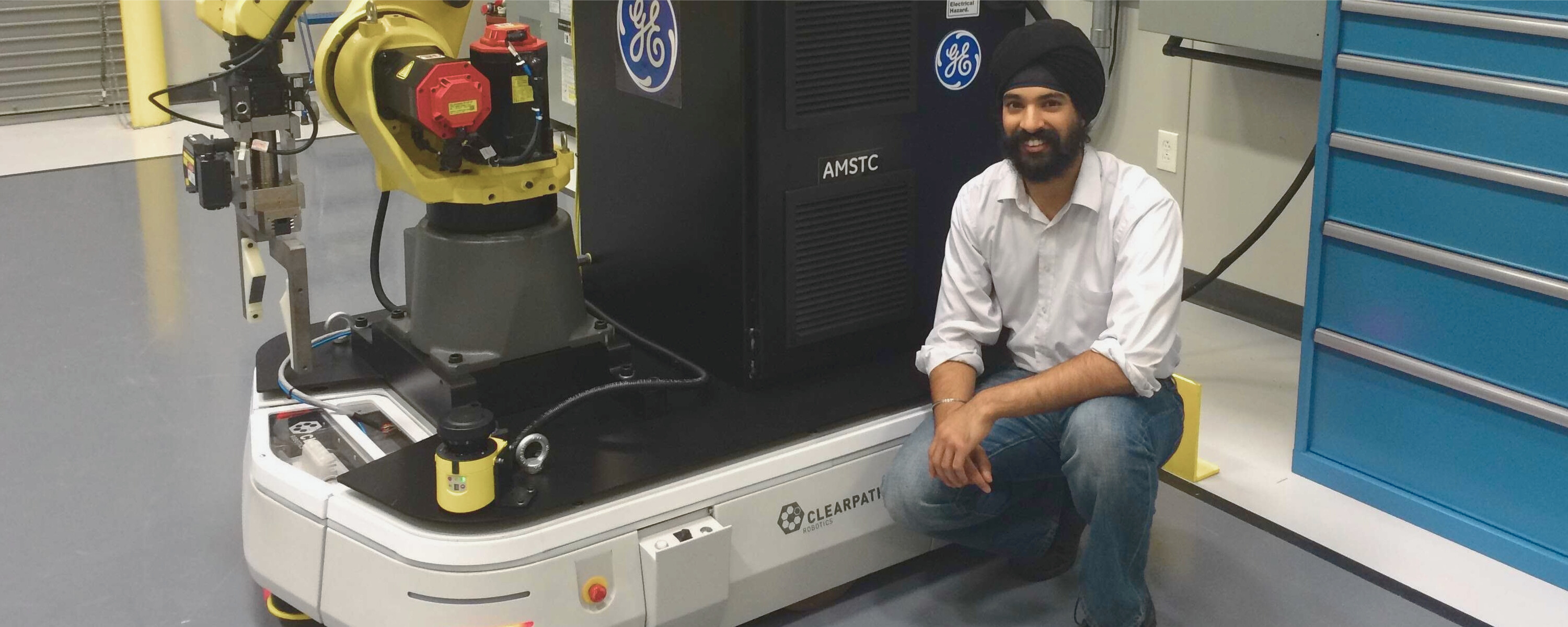
Written by Gurdayal, Strategic Ecosystem Solutions Architect at OTTO by Rockwell Automation.
I had a front row seat to witness OTTO’s trailblazing journey over the last ten years, first as an early OTTO customer, then as a systems integrator deploying and integrating OTTO AMRs for multiple clients, and now as an OTTO employee. This is that story.
A decade ago, I was working at GE as a robotics engineer developing industrial robot cells and innovative material handling solutions for various divisions and applications, like machining 20-30kg nozzles in CNC machining centers. At GE Aerospace, highly skilled operators spent much of their time moving material around the facility. They needed a scalable solution that could both move and manipulate parts around the facility and into machines. I had thus become responsible for developing a mobile manipulator and had to find a compatible mobile robotic platform.
GE had already been working with OTTO’s research platforms and I heard that OTTO was expanding from research into industrial applications. After evaluating multiple AMR vendors—and even considering building one on our own!—we established that OTTO was best suited to tackle GE’s needs. In 2016, we deployed one of the first OTTO 1500 AMRs at another GE facility. In fact, we had unit 002, back when the robot’s colorway was white.
Built with an industrial manipulator on top, it was one of the most beautiful things I had ever seen.
GE Aerospace saw the solution in action, and loved it, but they didn’t need such a big robot to manipulate small parts inside jet engines. OTTO was already listening, launching a smaller AMR, OTTO 100, right on cue. In order to provide dedicated support for the increasing number of mobile projects, my colleague, Thomas Post, and I founded Capriol in 2017, a designer of integrated robotic mobility solutions. Capriol deployed the OTTO 100 with a mobile manipulator and a custom cart at GE Aerospace in Asheville, North Carolina.
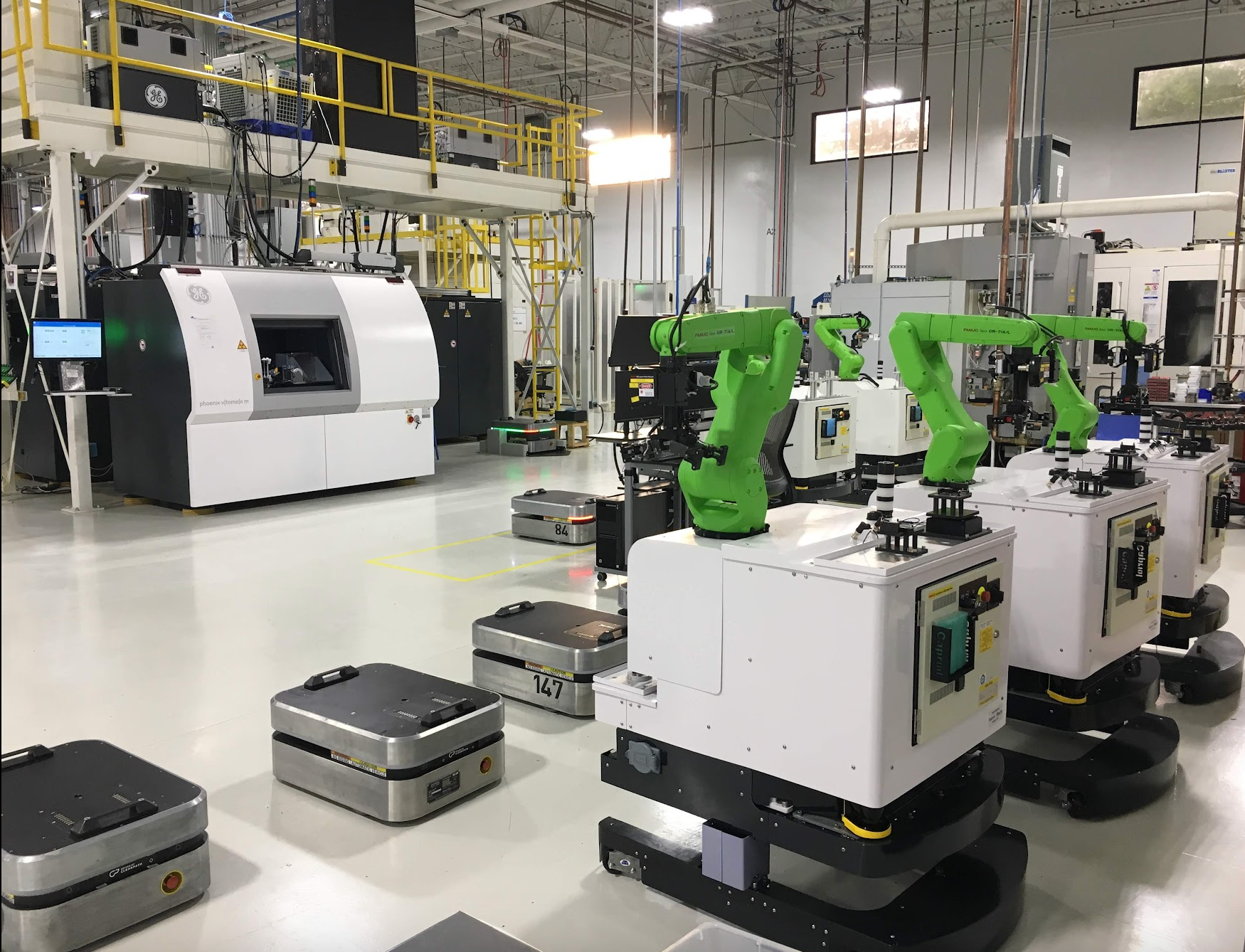
Image 1: OTTO 100 with a custom cart and mobile manipulator at the GE Aerospace facility in Asheville.
One of my favorite memories working on the Asheville project was when we couldn’t figure out why the robots wouldn’t dock at their stations. We thought maybe the lighting in the facility was not compatible with the robot’s LiDARs, so we sent the OTTO team lighting samples and together we made cardboard covers for the floor and chargers. Then, one of OTTO’s field services team members came to the facility and wiped off the LiDAR. It turns out, after all that experimenting, the LiDAR was simply dirty. Inspired by this instance, cleaning the LiDARs once per shift was added to OTTO’s operations manual.
I worked with OTTO fairly regularly over the next few years, and I never shied away from telling them what we needed. For example, I asked for a general-purpose input/output (GPIO) for the attachment interface, and OTTO built one for us. I requested an output trigger for when the robot entered a certain area, and OTTO built it.
Over the years, I requested many software and hardware features. Rather than avoiding these challenges, they continually pushed their boundaries to ensure they were meeting customer needs.
The first thing I did when I joined the team at OTTO was go through my old feature and service requests, and there were a lot. Looking back, though I feel like I gave the OTTO services team such a hard time with my many requests, they were extremely receptive to feedback from customers and partners. They recognized the value we brought, and knew that implementing the feedback was the best way to transform the industry.
Some of the OTTO employees I worked with back then are still with the company today, including Matt Lacroix who now manages field services, Roydyn Clayton who now heads the strategic alliances division, and Bryce Vondervoort who now leads OEM partnerships, and so many more! It’s so wonderful to be team members now in a different capacity.
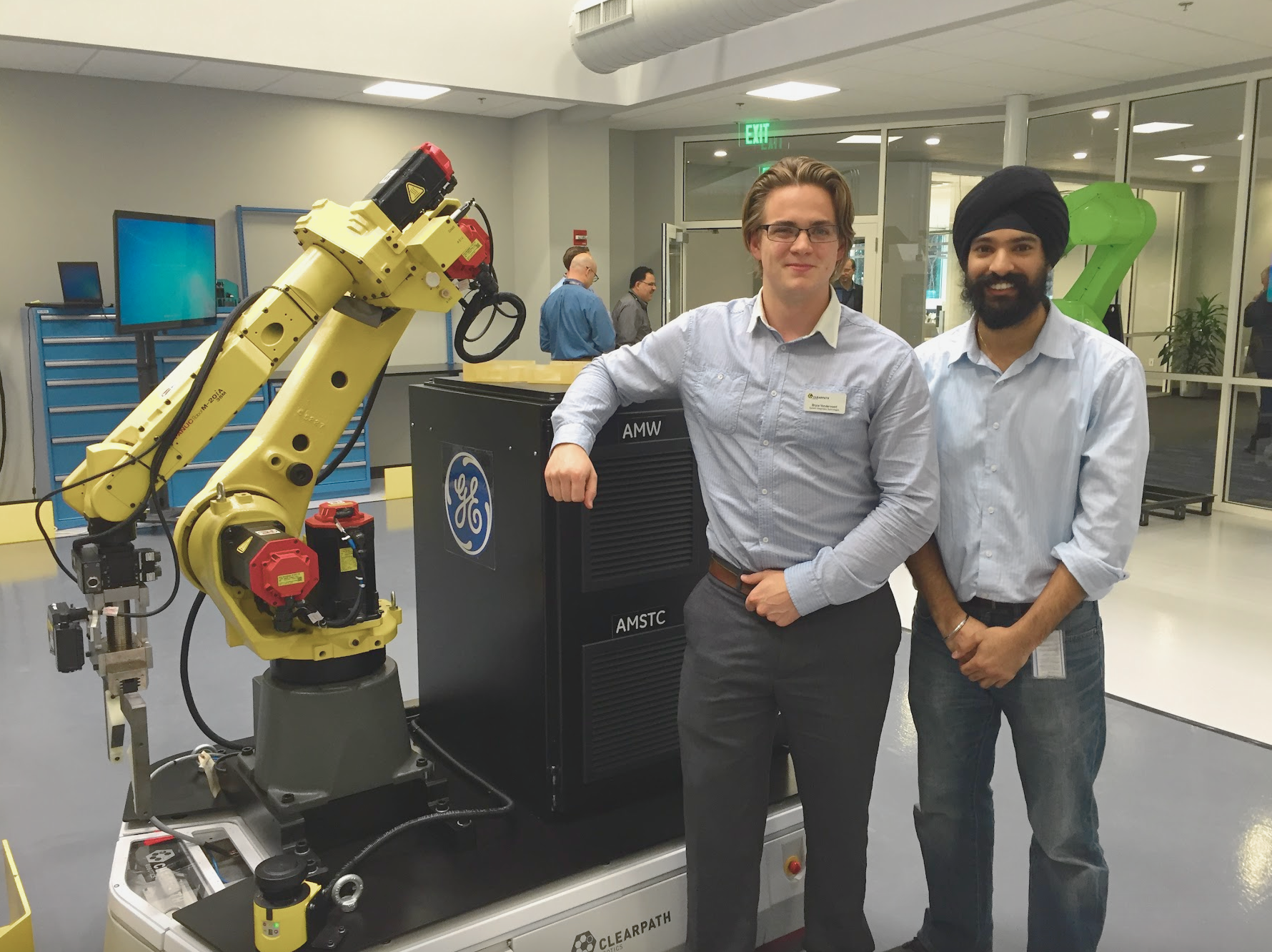
Image 2: Bryce Vondervoort from OTTO (left) and I (right) with a white OTTO 1500 in 2015.
The GE Aerospace project was a huge success, and I was very excited to be a part of it. Within one year, GE was able to save $1.3 million while reducing the direct labor going into the part by 20% and keeping skilled operators focused on what they were trained to do. GE was one of the early adopters of OTTO technology and throughout their many years working with OTTO, the team at GE was extremely impressed with how mature the solution and the company had become in such a short period of time. GE Aerospace was excited to grow alongside OTTO and quickly expand their fleet.
I, too, was impressed with how quickly OTTO grew from the industrial division of a research company to the global AMR leader that it is today. That’s why, in 2023, I signed onto the OTTO team to be part of the growth they’ll continue to experience alongside Rockwell Automation. I saw firsthand as a systems integrator how committed the team at OTTO was to problem solving and their dedication to customers, and I am excited to help them continue bringing connected factories to life, only now, on the other side of the coin.
Interested in a career at OTTO? Apply today.
Discover more
Subscribe to our newsletter
Stay in the loop on product news, case studies, upcoming events and more.