Blog
Putting autonomous mobile robots to use in automotive manufacturing
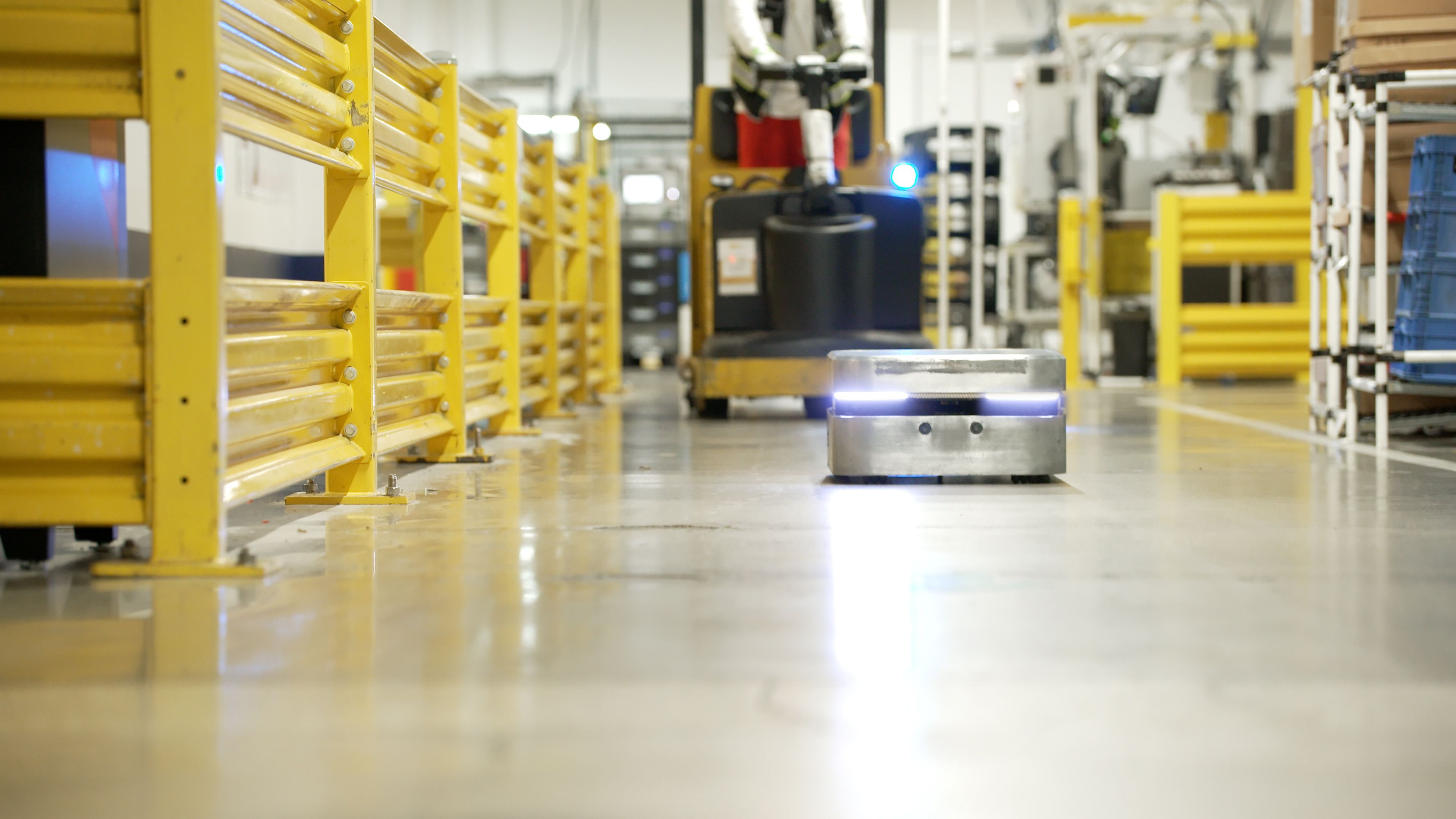
This manufacturer is an integral part of North America’s automotive manufacturing sector, supplying components for 1 in every 3 vehicles. They needed a reliable, small-footprint material handling solution to keep workflow humming in their many specialized cells.
The problem
There is a wide range of specialized work cells at this automotive parts plant in Fraser, Michigan. These cells involve processes such as injection molding, painting, laser scoring, several types of welding, as well as assembly. However, operations were being constantly interrupted because human operators ran out of materials.
The existing material handling system consisted of manual high-lows (often referred to as forklifts). This did not allow consistent, timely delivery of materials, in part because the high-lows needed to be kept away from workers for safety reasons.
The manufacturer sought an autonomous solution that would:
- enable constant, easy delivery of small batches at the correct times (uninterrupted workflow)
- improve the existing near-miss incident rate (improved employee safety)
- integrate well with existing systems and reduce operator interaction (higher productivity)
- adapt to ongoing changes in the plant (minimized downtime related to material handling)
The solution
The planning team, led by a Director of Engineering, looked at automated high-lows, magnetic AGVs, manual cart systems and other potential solutions. Those involving magnetic strips were quickly rejected due to the downtime required to change routes and the physical infrastructure costs.
For their high level of flexibility, precision and safety, the manufacturer chose and deployed Autonomous Mobile Robots (AMRs) from OTTO Motors. The deployment began with 8 AMRs and is currently expanding its OTTO fleet to 12 robots. OTTO AMRs safely work alongside their operators to supply each cell with the requisite material. Additionally, the AMRs were employed to move finished goods out of cells, preventing pileups and reducing the footprint required for each cell.
At the manufacturer's Fraser plant, the OTTOs:
- Pick a different path when blocked, and safely navigate the shared space with the existing material handling system – “The OTTOs have safety features that allow them to coexist with a tugger, an operator, people crossing its path, people standing in front,” says the Engineering Director. “If there's a different condition with the plant where someone would put a box in the middle of the aisle for example, they are able to navigate.”
- Allow rapid adaptation to plant changes – Continued: “We wanted something that was totally flexible and OTTO gave us that ability where we can just reprogram. In fact, we moved a couple of cells in the plant a couple weeks ago and within 45 minutes, we had a new ‘parking lot’ and a new route for the OTTOs.”
- Maximize worker productivity – “We wanted the least amount of operator interaction in order to get the efficiency from the automation. OTTOs delivered that exact thing. They deliver a specific amount of parts to a specific location at a specific time only when requested.”
- Allow new efficiencies, including better-organized tugger routes – “We started automating where we were just delivering from cells. Now we're going to the point where we're delivering to cells and from the same cell, the next stage of our OTTO evolution, so to speak…We're also going to be doing different things with OTTOs, like delivering kit parts to the middle of an assembly cell.”
The results
The manufacturer proudly reports that implementing OTTO has resulted in:
- ROI of 11 months
- 15% reduction in work cell size
- Zero safety or near-miss incidents
- Standardized process that supports their 5S system
Cell operators are definitely more focused on their work requirements and that is a huge benefit. Any time spent working is efficiency gains. We do notice a big difference and to be honest, the operators absolutely like the OTTOs. Hands down, they actually prefer OTTOs to the old delivery system.
Senior Controls Engineer, automotive parts manufacturer
With OTTO Fleet Manager, I'm able to see where the OTTO is, how long it's taking, but also where I'm able to assist with re-map of certain areas. Things change in a plant all the time. So it's good to put in a zone remap, put in another zone, put in new routes. That aspect really comes into play.
AMR Coordinator, automotive parts manufacturer
With OTTO, we've been able to reduce the size of our floor space, and increase our manufacturing efficiency to make a better, cheaper product in order to bring home the profitability.
Director of Engineering, automotive parts manufacturer