Blog
Largest AMR deployment for material handling: Q&A with Matthew Rendall and Matthew Chang
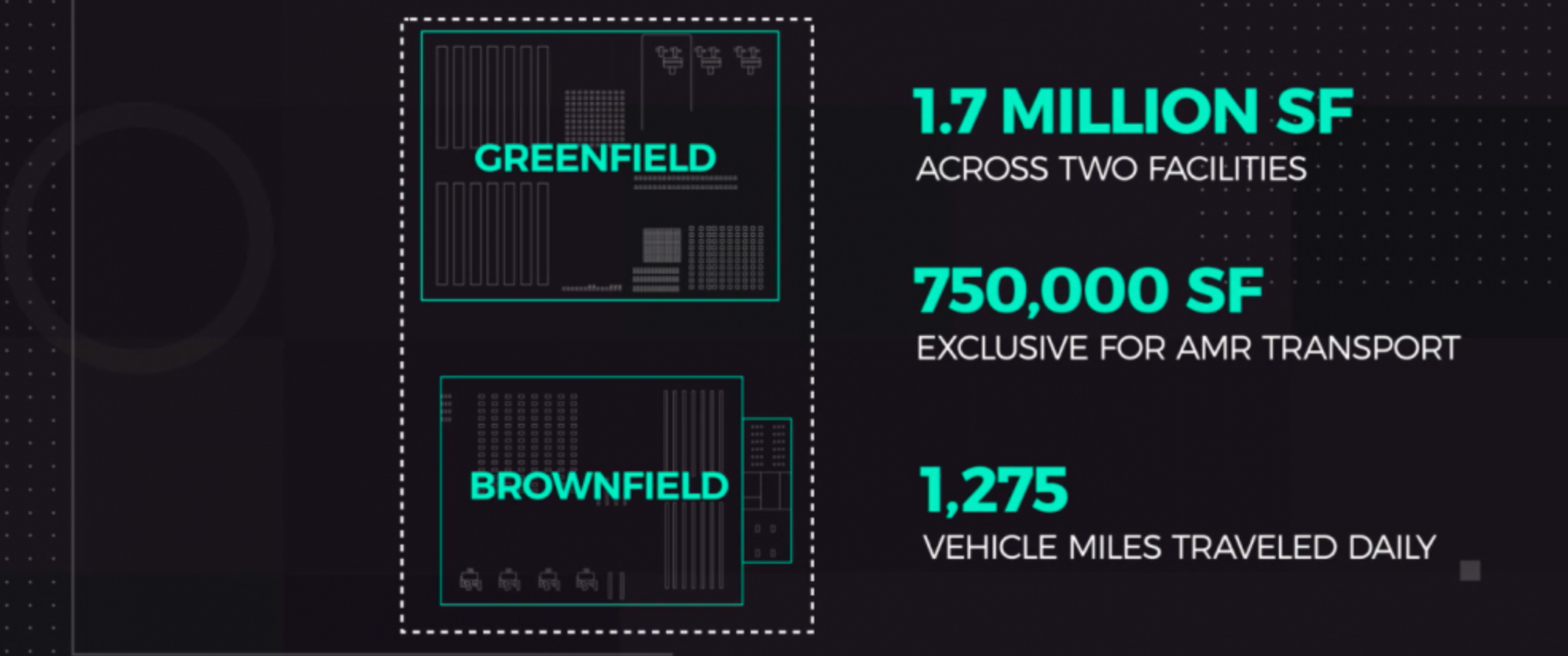
For years, Autonomous Mobile Robots (AMRs) have been considered a promising technology for materials movement because they provide the flexibility of human forklift, with the throughput and reliability of a fixed machine (like a conveyor) — all while being able to work safely alongside operators on a factory floor. However, to date, there have been few examples of AMRs being deployed ‘at scale’ within manufacturing facilities. Until now.
In an earlier webinar session, Matthew Rendall and Matthew Chang explored one of the world’s first ‘at scale’ AMR deployments. Using a real-world example of AMR deployment at an F500 company, OTTO Motors and PULSE Integration detailed the use cases and ROI associated with this installation. You can watch that webinar here.
Since then, questions have been pouring in from attendees asking about scalability, ROI, labor displacement, and many more. In this Q&A session, Matthew Rendall and Matthew Chang answered the most frequently asked questions about the latest AMR deployment.