Ramping up to industry 4.0
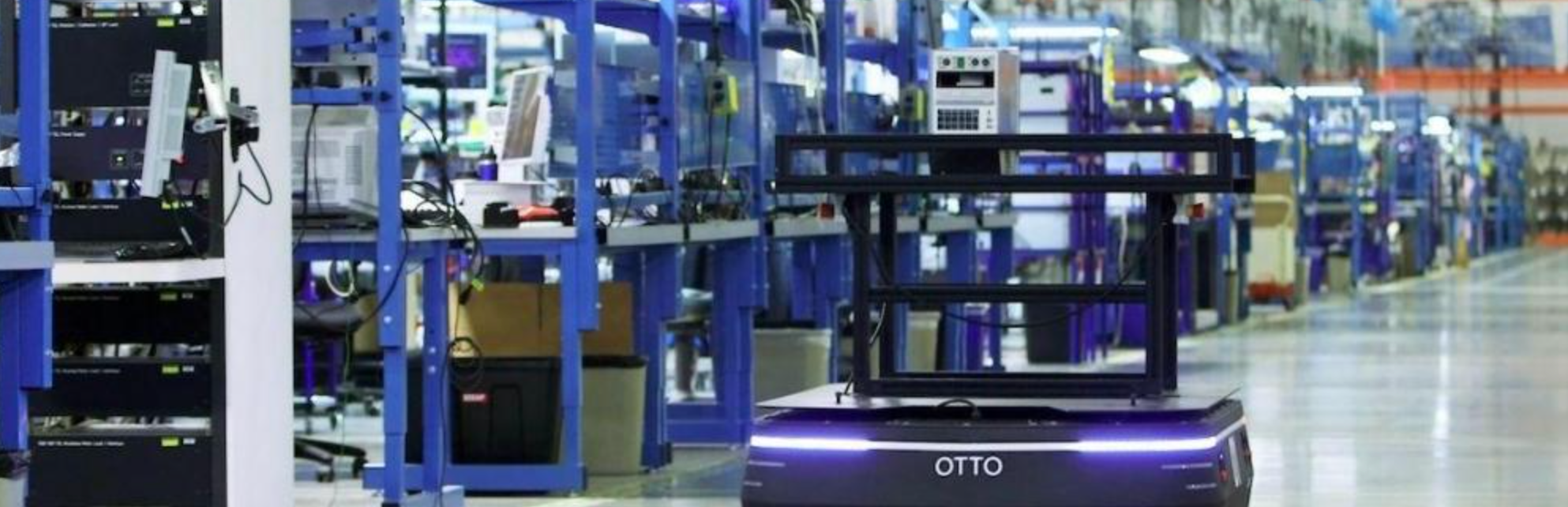
So what really is Industry 4.0 and why should you be excited? Industry 4.0 is the next leap in manufacturing. It combines our quest for using large quantities of data; translating it (computing power) into meaningful information; sharing it across a large network allowing people and machines (such as robotics and additive manufacturing) to create a product faster, more efficiently and at less cost.
That is the theory. The reality is we are not there yet. But we are getting much closer.
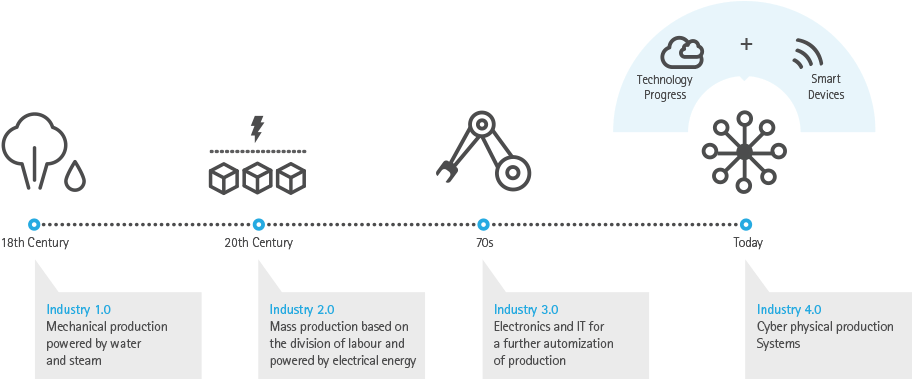
Ramp up to Industry 4.0. (Photo: accenture.com)
Most factories already use robotics to some degree, some more than others. You will find robotics in welding operations and on applications requiring cutting or grinding. Robots work on the assembly line, painting products, verifying tolerance levels, picking orders, packaging and of course, material transport. Each of these functions and others all produce large amounts of information that generally goes unused.
How the Warehouse Works Today
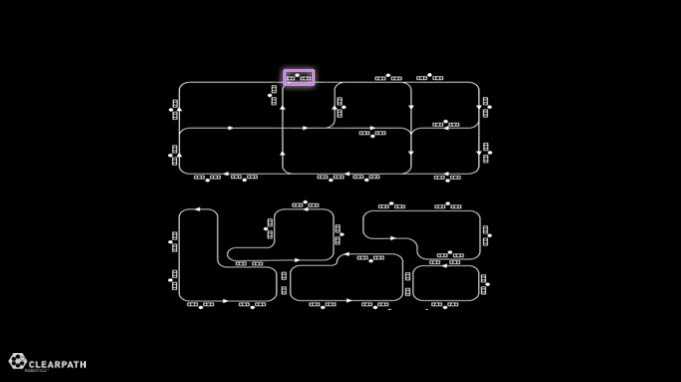
Consider the following scenario. A robotic station on the assembly line is running low on parts. The robot alerts the operator, who then calls to have more parts delivered. A materials scheduler contacts the order picker in the warehouse to find and make ready the next load. The order picker has an idea where the parts are, but spends several minutes locating it.
Meanwhile, a forklift driver receives an alert to pick up and deliver the parts. The driver must find where the parts are located in the warehouse and deliver the next pallet. Did the forklift get to station before the robot ran out of parts? Maybe. It depends on variables including speed of communication, locating the product, human accuracy and aisle congestion.
How the Warehouse Works Tomorrow

Industry 4.0 speeds the process while improving productivity. Because the factory—people and machines—are connected via Wi-Fi, machines now share the data more effectively. The machines talk with each other and with human operators. As a result, the previous scenario now looks like this:
The assembly line workstation still runs low on parts. Instead of sounding an alert for the operator, the robot communicates directly to the manufacturing resource-planning computer. This computer notifies an order picker in the warehouse to prepare the load of parts. That person scans a barcode to identify which aisle the parts are located and then, wearing augmented reality glasses is easily able to find the specific parts bay.
Meanwhile the computer signals a nearby autonomous mobile robot within the warehouse fleet to pick up, and then deliver the required materials to the workstation. Because the autonomous mobile robot doesn’t rely on magnetic strips or a fixed path programming system like their AGV predecessors, the materials arrive exactly when needed in spite of an aisle closed while employees install a new machine. The autonomous mobile robot receives the real-time warning about the closed aisle and automatically re-routes its path.
Working Smarter with Connectivity
Machines connected and communicating with each other and with human operators via the Internet:
- Leverage the speed of changeovers
- Avoid overproduction
- Provide increased traceability, predictability of manufacturing
- Virtually eliminate accidents caused by human error
- Improves aisle space utilization and overcrowding
- Creates a manufacturing environment focused on increased density of production and capacity.
That is what manufacturers have to look forward to and it’s almost here.
We can help you prepare for Industry 4.0 with real world material handling solutions for today. Contact us to learn more.