Blog
Solving CPG's biggest challenges with integrated automation solutions: How AMRs play a critical role
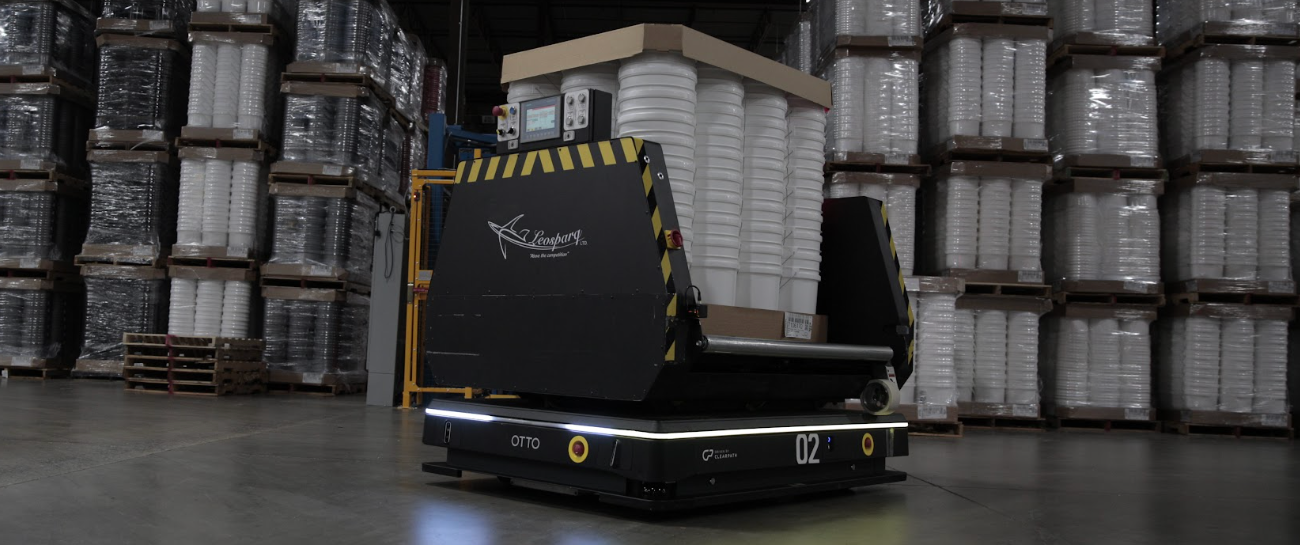
As market demand shifts and consumer preferences evolve, manufacturers in the Consumer Packaged Goods (CPG) industry are increasingly turning to automation to streamline operations, reduce costs, and improve production flexibility. In contrast to other industries, CPG manufacturers face some of the most unique challenges, and one of the easiest ways to solve them is through the implementation of autonomous mobile robots (AMRs).
AMRs work alongside existing automation solutions and business management systems in your facility to understand production schedules, help operators work more productively, and create new levels of efficiency.
Here are four ways AMRs—integrated with your existing solutions—can solve the most common challenges in the CPG industry.
Challenge #1: A high volume of low-cost products
Downtime has a significant impact on profit margins on high-volume production lines of low-cost products, making efficiency and reliability essential to any automation solutions introduced to the process.
AMRs are designed to get the right parts to the right place, at the right time, without compromising safety. Material handling is one of the most inefficient processes in manufacturing facilities and warehouses, accounting for 87% of production time.
Equipped with real-time decision making intelligence, AMRs get to their destination using the most efficient, optimal route to improve productivity.
When faced with unforeseen obstacles, such as static or dynamic objects, AMRs are able to detect and navigate around the blockage without triggering a safety stop—and can even autonomously replan their route if needed—to ensure a sustained speed and minimal downtime. By integrating with your facility’s MES, OTTO AMRs can receive production schedule information and reliably execute tasks on time, ensuring continuous productivity.
For example, when Mauser Packaging Solutions implemented AMRs integrated with their existing systems, they saw a 6x throughput increase.
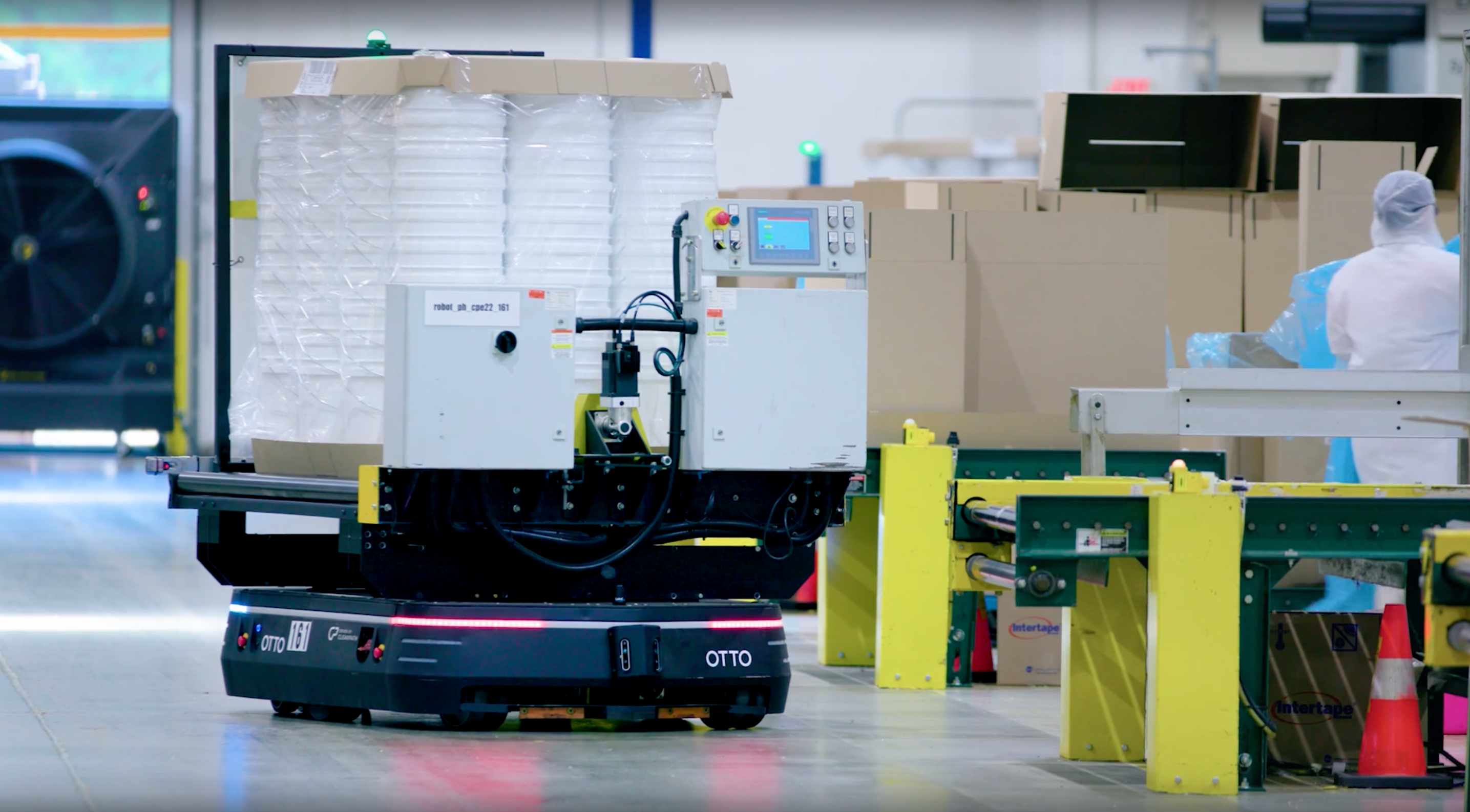
Material handling can also account for 25% of the workforce. By allocating available workers to more value-added tasks and allowing automation to move goods around the factory floor, CPG manufacturers can increase production and lower costs. AMRs are also able to consistently perform tasks with precision, reducing human errors and delivering unmatched reliability.
Challenge #2: Short product life cycles and quick production cycles
Due to the fast-paced nature of changing consumer preferences and trends, the CPG industry has always had quick production cycles and products with short life cycles. The challenge lies in balancing efficiency with flexibility; manufacturers must optimize production processes to minimize downtime while also being able to pivot quickly when new trends emerge.
AMRs offer unparalleled flexibility, enabling manufacturers to easily adapt to changes in processes, workflows and floor layouts. Since these mobile robots aren’t on a fixed navigation path—like most automated guided vehicles (AGVs) and conveyors—manufacturers can easily adjust material movement workflows as operational needs change. Paired with easy-to-use software, AMRs can quickly and effortlessly adapt to changing facility layouts and production schedules as they balance efficiency and flexibility.
Through MES integration, the AMRs are able to access live data about your products being manufactured, enabling them to know where to pick up or deliver materials. This capability allows them to move materials across multiple product lines without needing to manually reprogram the system. This flexibility enables CPG manufacturers to quickly repurpose floor space, increasing operational efficiency even with changing production layouts or schedules.
Additionally, AMRs do not require any infrastructure to operate, unlike AGVs and conveyors. Since material handling can account for 55% of a factory floor, it's imperative that manufacturers implement solutions that use limited floor space to improve facility flexibility and maximize productive space.
When GE HealthCare implemented AMRs, they were able to increase usable floor space by 66%.
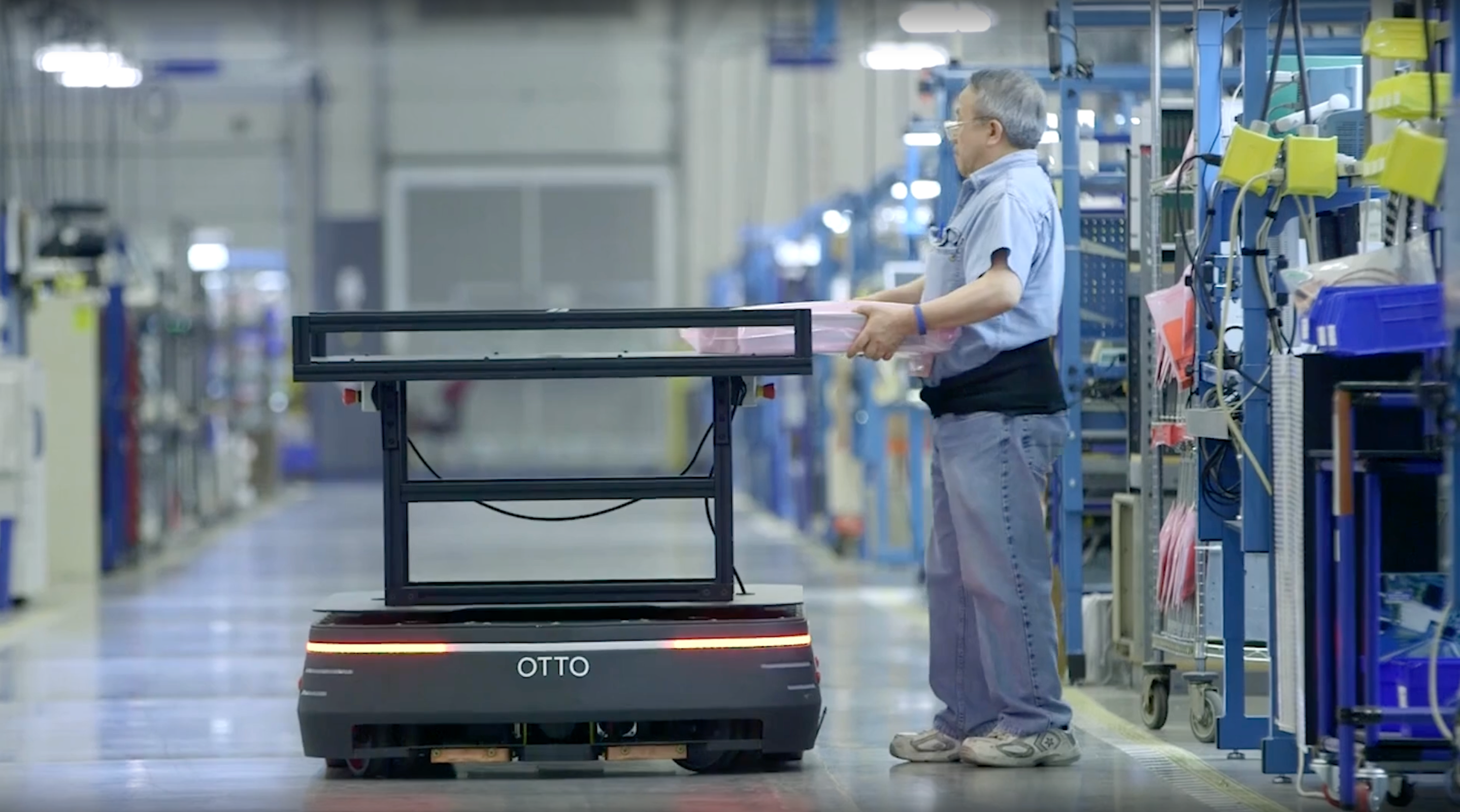
Challenge #3: Unpredictable fluctuations in product demand
CPG products are often characterized by surges in demand for specific products. For example, holiday seasons can spike sales for specific household items, such as decorations and even unique scents. Manufacturers must maintain flexibility in their production processes to optimize how they use their facility throughout the year.
Using LiDARs, 3D cameras, and other safety-rated sensors, AMRs navigate your facility quickly and safely. The software can be programmed to deliver parts or finished goods more frequently to certain areas of the plant to meet demand fluctuations. Sophisticated AMR software is also able to quickly and easily shift to new workflows, even across the plant, as product demand shifts. While fixed automation such as conveyors can only take products with uniform dimensions, AMRs and their attachments are able to transport these non-conveyable materials that are unique due to customizations. By integrating with your MES, AMRs are able to understand where and when the custom products are coming off the line and where they need to be delivered.
Sunview Patio Doors introduced AMRs to meet rising customer expectations for faster delivery times, lower price points, and more customized products. The flexibility of their autonomous material handling solution enabled them to transform their production into a lean manufacturing model and reach ROI within 16 months.
Every single choice a customer makes when designing their product means a change to our manufacturing flow. This must be accounted for in the process layout, which makes it very complex to manage. We knew this logistical challenge could only be solved with autonomous mobile robots.
Kurt Oberparleiter, VP Operations, Sunview Patio Doors

Challenge #4: Complex inventory management
Product variety in the CPG industry demands a sophisticated inventory management system to efficiently handle unique shelf lives, storage needs, and demand patterns. Thus, optimizing just-in-time (JIT) inventory practices are essential to ensure the right part gets to the right place at the right time, preventing waste and shortages.
Sophisticated AMR software solutions auto-assign the right robot to the right job to deliver materials efficiently and on time, increasing average cycle times. Their real-time data integration with inventory management systems can enable better tracking of inventory levels and demand patterns, reducing the likelihood of waste. This integration with your existing inventory management systems, such ERP or WMS, ensures materials are delivered as needed, reducing bottlenecks and optimizing overall efficiency within the facility.
To learn more about how CPG manufacturers are staying ahead of evolving consumer demands with AMRs, watch the webinar “A practical guide to AMRs in CPG manufacturing”.
Subscribe to our newsletter
Stay in the loop on product news, case studies, upcoming events and more.