Blog
LEAN manufacturing: Tackling the 7 muda in materials handling
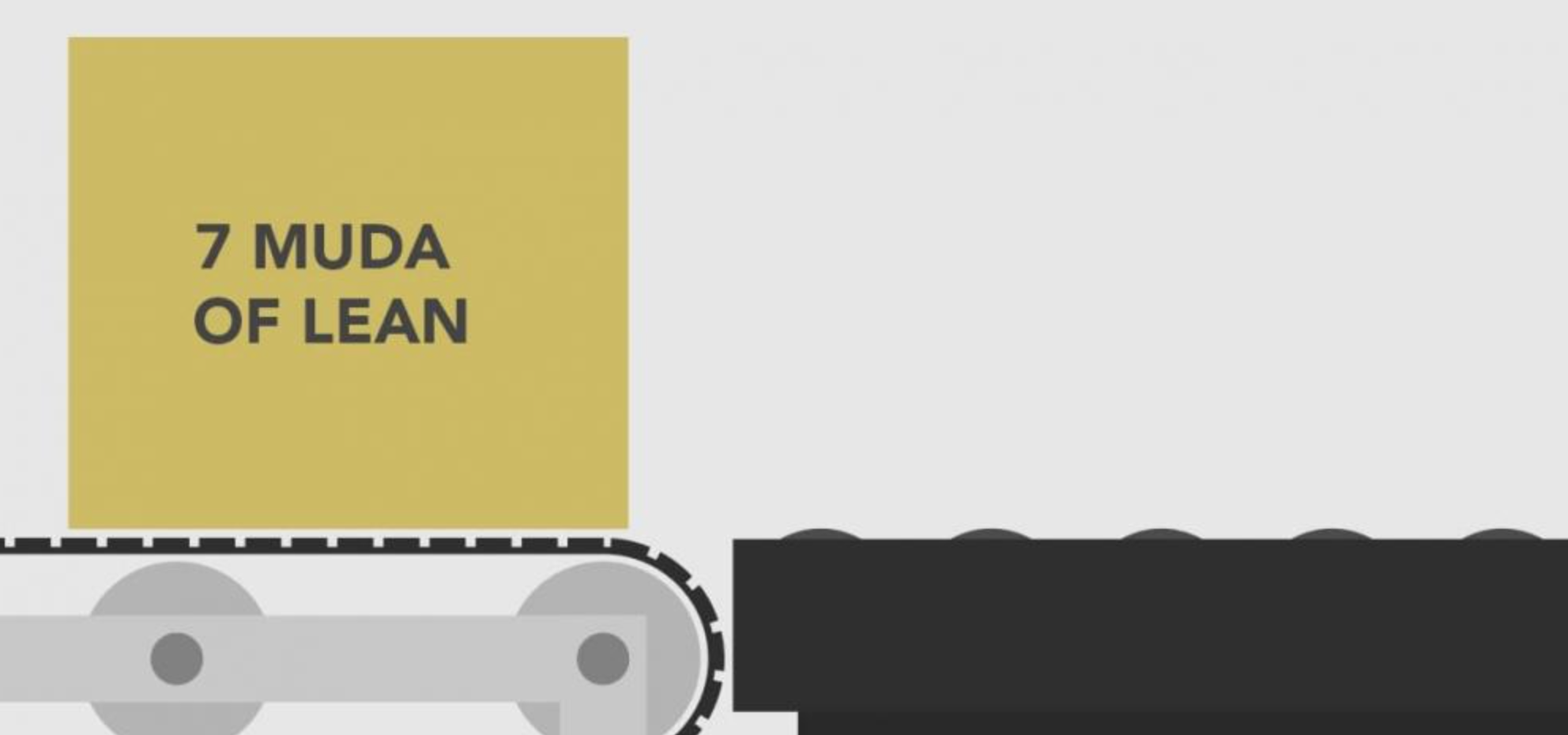
Muda (無駄) is a Japanese word meaning "wasteful" and is a key concept in the Toyota Production System (TPS), the precursor to LEAN Manufacturing. According to Toyota, Muda is a process that does not add value. The customer is only willing to pay for work that adds value. Therefore, reducing or eliminating Muda is an effective way to increase profitability and is a fundamental philosophy to LEAN manufacturing practices.
The system identifies and classifies 7 major Muda:

Muda #1 - Transport
Each time a product is moved it stands the risk of being damaged, lost, or delayed, on top of being a cost for no added value. Transportation does not make any transformations to the product that the consumer is willing to pay for.
Muda #2 - Motion
Not to be confused with Transport, Motion refers to the damage that the production process inflicts on the equipment or person that creates the product, not the damage to products themselves. For example, discrete events, like accidents that injure workers and damage equipment, or even wear and tear, are also part of the consideration.
Muda #3 - Waiting
Time is always of the essence in production. Whenever goods are not in transport or being processed, they are in a stand still waiting for the next production step. In traditional processes, goods spend a large part of their individual product life waiting to be worked on.
Muda #4 - Inventory
Inventory, in the form of raw materials, work-in-process (WIP), or finished goods, represents a capital outlay that has not yet produced an income either by the producer or for the consumer. Any of these three items not being actively processed to add value is a waste.
Muda #5 - Over-production
Over-production occurs when more product is produced than is required at that time by your customers. In many cases when a large amount of inventory is stock-piled, part of that inventory gets wasted because consumer demands change over time.
Muda #6 - Over-processing
Over-processing results from poor tool or product design creating unnecessary activity. This Muda occurs any time more work is done on a piece beyond what is required by a customer. This also includes using components that are more precise, complex, higher quality or expensive than absolutely required. Think about the scraps that often result from poor product or process design – that's over processing.
Muda #7 - Defects
Whenever defects occur, extra costs are incurred in reworking the part, rescheduling production, etc. This results in additional labor costs, more time in the "Work-in-progress" stage. Defects, in practice, can sometimes double the cost of a product. This should not be passed on to the consumer and should be taken as a loss.
Where to begin
If left unchecked, these seven Muda will erode your yield, your product rate and your profits. Of course implementing processes into operations in order to eliminate waste is something easier said than done. This blog series will explore ways in which new technologies can eliminate four of the seven deadly muda. Why four? Because they are known to be the most challenging of the seven to address in materials handling environments.
Read on to learn how you can achieve lean manufacturing:
Part 2: How to gain time on the assembly line.
Part 3: Changing excess inventory from too much to just right