Blog
Technology and material handling equipment
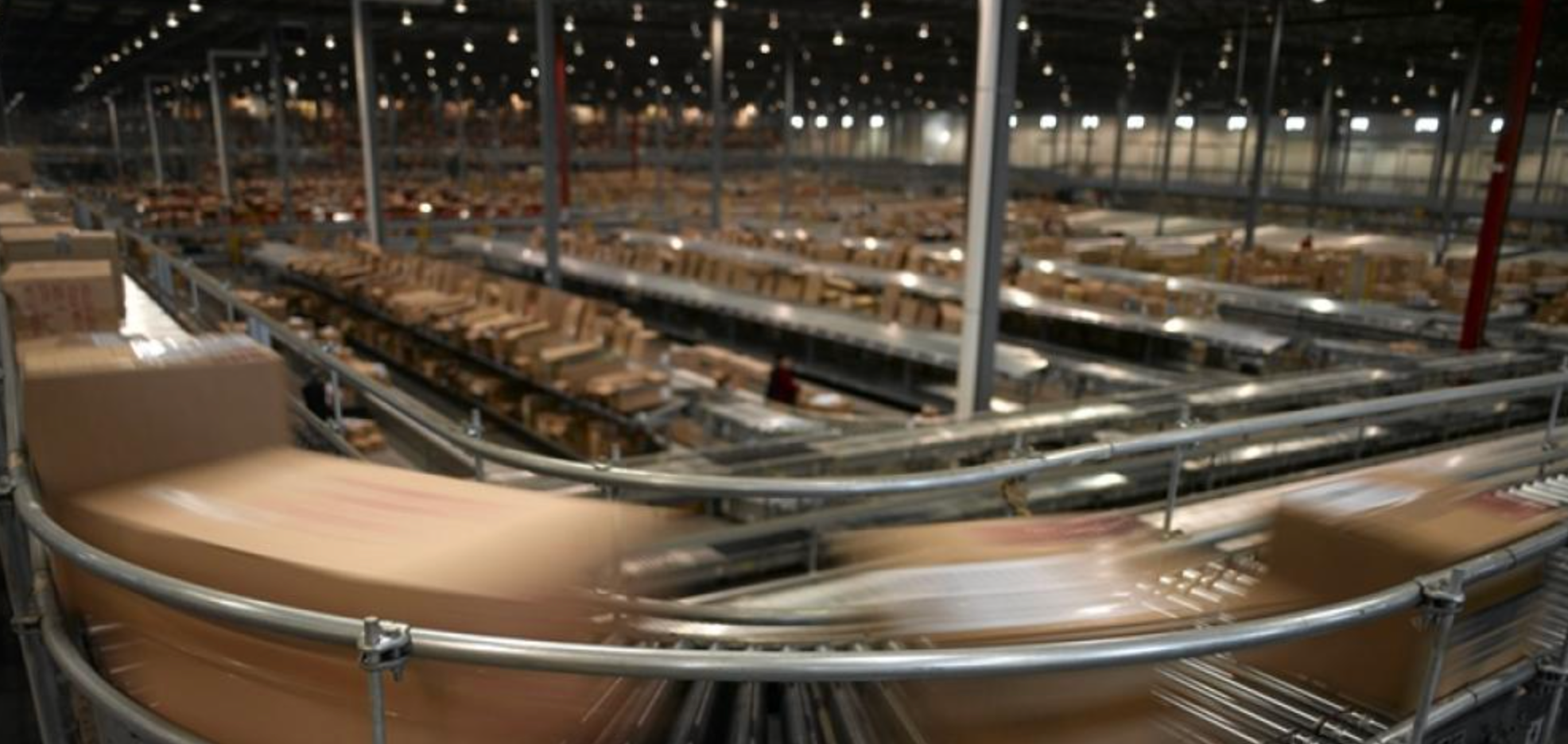
How efficiently materials move through a manufacturing or warehouse facility will affect the cost of production as much as any other part of the supply chain. Given its importance, companies have found ways to leverage technology to improve this process.
Because most manufacturing companies’ internal processes are on
ly visible to employees, a lot of people are unaware of how common and advanced the technology involved with the many parts of the production process really is.
Automated vs. manual material handling equipment
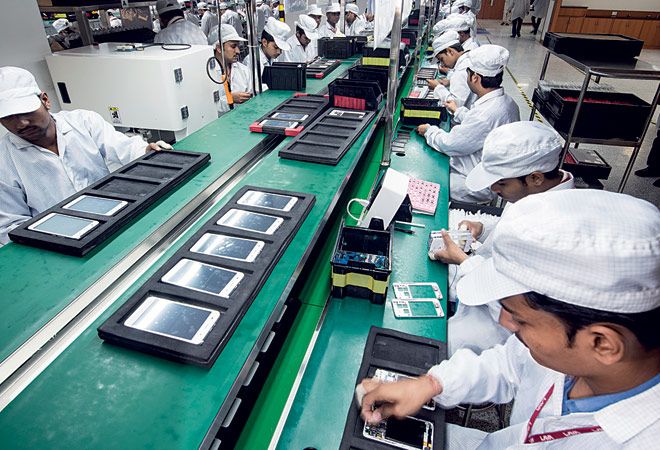
photo credit: businesstoday.in
Material handling equipment that's manual are those systems that use workers to pick goods and move them around a warehouse or bring them lineside for production. These types of warehouses might use equipment such as forklifts and conveyors to help the process along, however much of the work is done by humans. Automated warehouses use much more equipment to do the same processes. For example, equipment such as extensive conveyors, sortation machines, automated storage and retrieval systems (AS/RS), and AMRs (Autonomous Mobile Robots) are used as solutions to move goods.
There are several categories of material handling systems that are used in production. The technology used within each can be different – but overlap exists as well. Industrial trucks, storage and handling, and engineered systems are three general system types that are among the most impactful for a broad range of environments.
Engineered systems
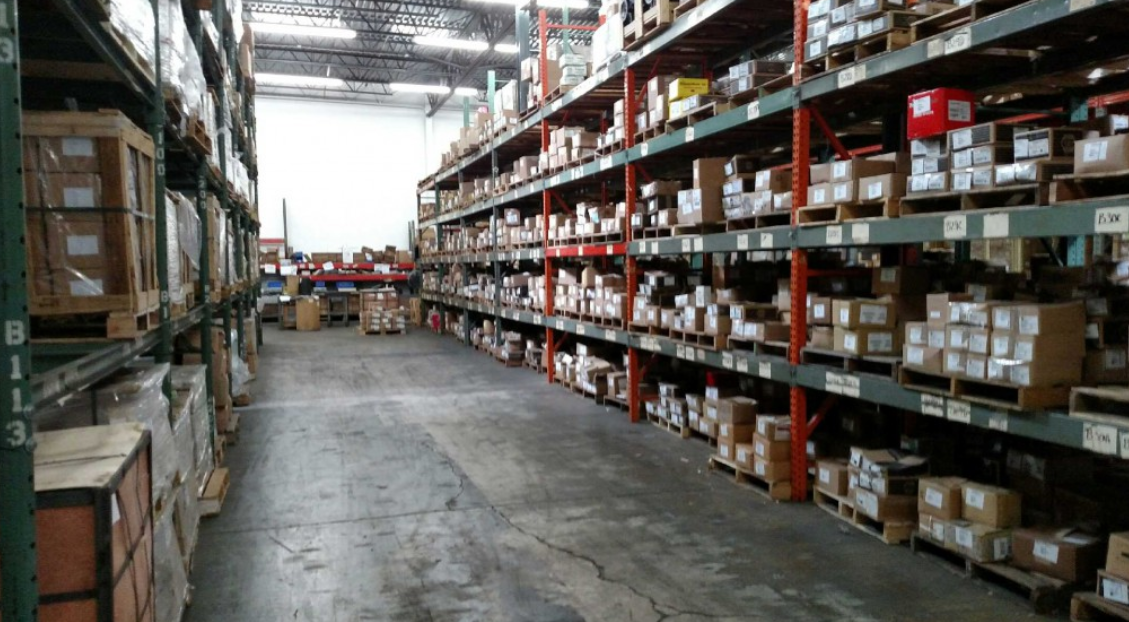
photo credit: distone.com
Engineered systems are typically a group of devices, tools, or machines that perform material handling tasks – like storage and retrieval - in an automated way. This can integrate other material handling equipment and infrastructure as well, like shelving and racks where product is stored. Integral to this process are often intelligent machines like autonomous mobile robots. AMRs enables companies to create flexible and adaptable material flows within their operation. When integrated into the IoT, they also enable better flow of inventory information and key production data that helps the entire facility operate better.
Industrial trucks
Industrial trucks serve the basic purpose of moving product or materials around a facility. Often simple, like small carts or lifts, they can also be powerful and complex machines. Technology is even giving people new superpowers as they work – many companies like Lowe’s are testing wearable exoskeletons employees use to assist them with daily tasks. With demand for speed and customization in manufacturing increasing, and the normal limitations of what a person can physically handle, this type of technology is one way for companies to remain competitive.
Storage equipment
Collectively, storage equipment can serve as a system that holds materials until they are ready to be picked or moved to another destination. A well-designed storage network increases production in the warehouse by maximizing space and minimizing handling costs. Some basic examples of storage and handling equipment include racks, frames, shelves, and bins and drawers. Most often, its technology and strict adherence to processes that makes efficient use of these assets possible.
There are a lot of ways to move raw materials, works in progress, and finished goods around a plant or warehouse. Although manual material handling operations will likely always be needed, many facilities are moving toward a more automated environment to increase speed and create a safer, more efficient operation.