Blog
AMA: What is AMR autonomy software and how does it differentiate AMRs from AGVs?
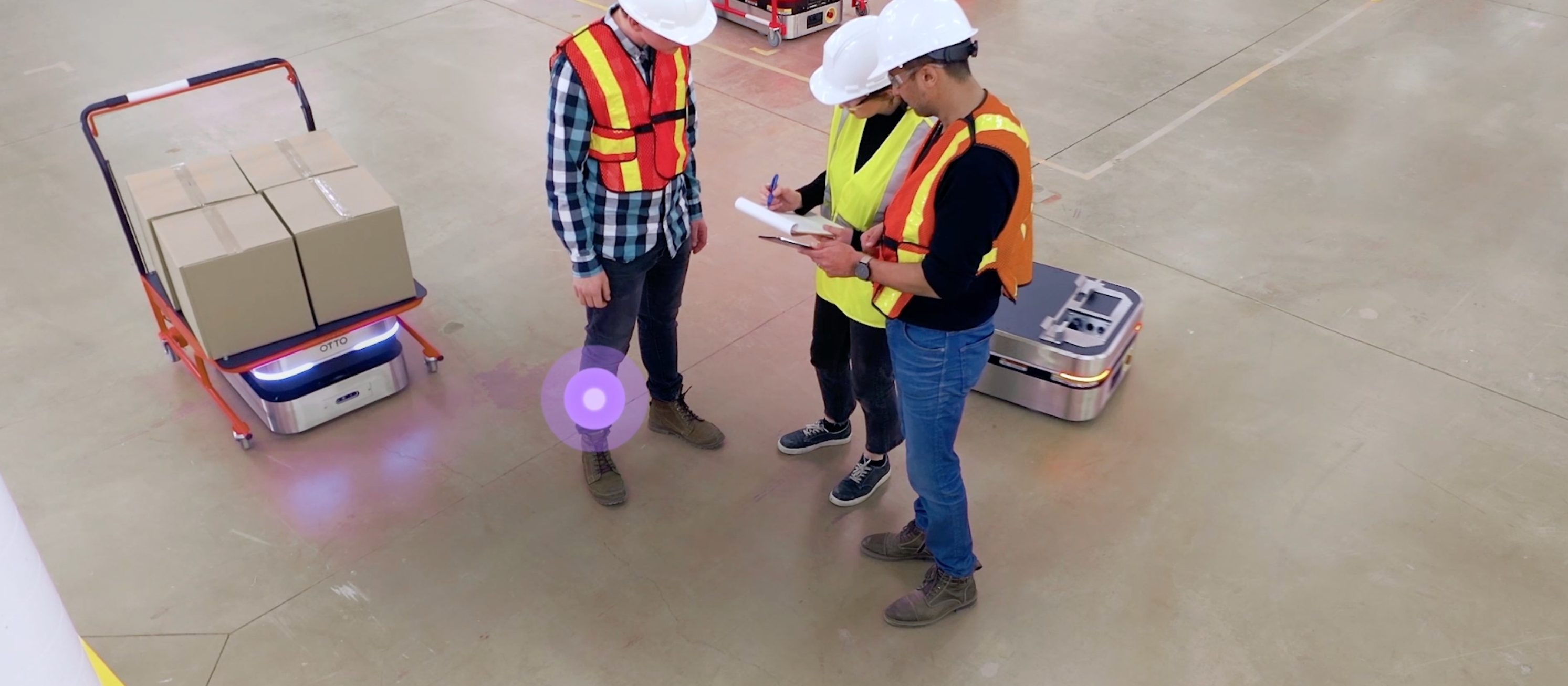
With manufacturers facing persistent labor shortages, rising safety concerns, and mounting inefficiencies in material handling, many are turning to autonomous mobile robots (AMRs) as a long-term solution. What truly sets AMRs apart from other material handling technologies is their autonomy software. This onboard intelligence transforms basic hardware into high-performing, autonomous robots capable of navigating dynamic environments with precision—redefining productivity on the factory floor.
If you're evaluating material handling automation technology for your facility, understanding what AMR autonomy software is—and how it's different from traditional technologies—is essential.
What is AMR autonomy software?
Autonomy software is essentially the robot’s brain. It is the onboard intelligence that enables the robot to perceive its environment, make decisions in real time, and safely navigate dynamic facilities—all without human intervention. Autonomy software allows the robot to reach its destination and complete its job by taking the best route, at the fastest possible speed, without compromising safety—even as it adapts to unexpected obstacles along the way.
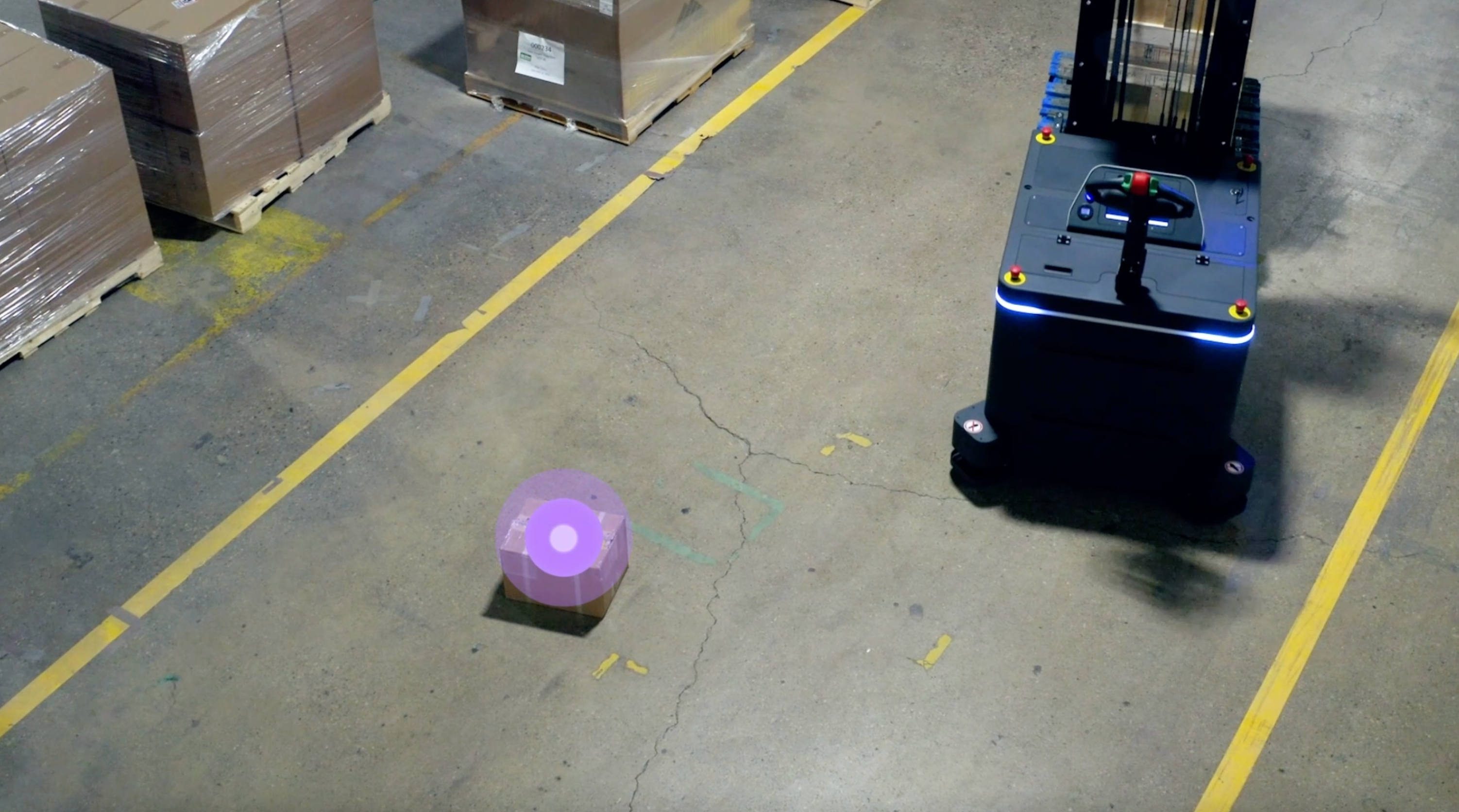
Video 1: Autonomy software enables AMRs to make real-time decisions and navigate autonomously around expected and unexpected obstacles.
While autonomy software governs local, real-time decisions on the robot itself, it works hand-in-hand with an AMR solution’s fleet management software. Fleet management software sets the “rules of the road”—defining and assigning the jobs that need to be completed. Together, autonomy and fleet management software ensure that every robot not only knows where to go, but also how to get there—safely and efficiently.
How does autonomy software differentiate AMRs from AGVs?
Autonomy software plays a major role in what makes an AMR fundamentally different from a traditional automated guided vehicle (AGV).
- How do they navigate? AGVs follow fixed, predefined paths using either physical indicators—like floor-embedded wires and magnetic tape—or virtual markers that define their route. AMRs, powered by autonomy software, use safety-rated LiDAR sensors to build a map of the facility and continuously determine their position within it—enabling them to navigate autonomously and adapt to changes in their environment.
- Where is their intelligence located? AGVs rely on a centralized controller to direct their actions, including their route, speed, and schedule. AMRs’ intelligence is stored onboard the robot and is capable of making real-time routing decisions independently.
- How do they respond to unexpected obstacles in their path? AGVs stop and wait when something blocks their path, requiring manual intervention to resume their work. AMRs can not only detect obstacles, but can also autonomously replan their route around them, continuing to their final destination with minimal interruption.
- What type of environments can they operate in? AGVs work best in repetitive, structured environments where there is minimal traffic and low interaction with people and other equipment. AMRs are best suited to tasks in dynamic environments where workers share the same space. The flexibility of AMRs enables them to also be easily redeployed in other workflows or facilities.
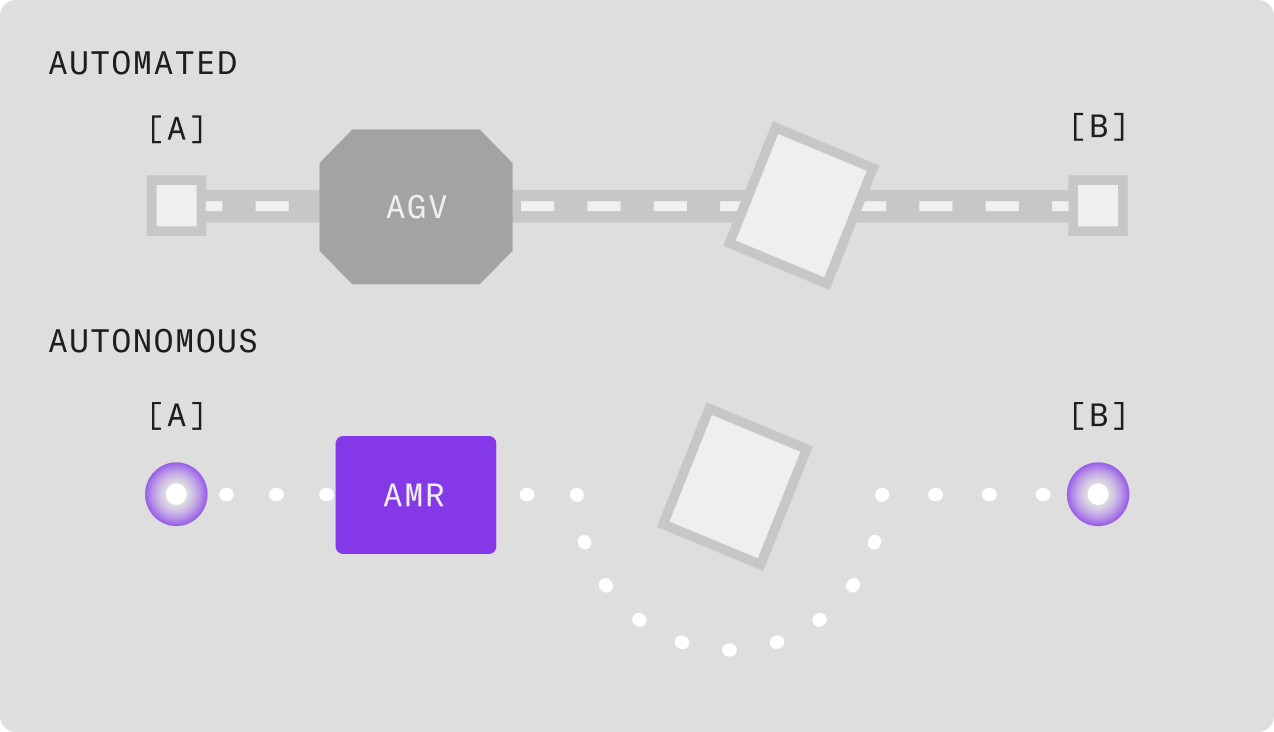
Image 1: It is the solution’s software that dictates whether a robot’s behavior is autonomous or automated, and how much control–if any–the robot has in completing its job.
Autonomy software is the key to unlocking the full potential of AMR deployments, enabling them to perceive, plan, and act independently—so your operations stay flexible and efficient, without compromising on safety.
Curious how autonomy software works in practice? Watch the webinar to see a live demonstration of the process behind making smart, precise decisions in real time.
Subscribe to our newsletter
Stay in the loop on product news, case studies, upcoming events and more.