Case Study
Cober Solutions implements AMRs to improve employee fulfillment and productivity
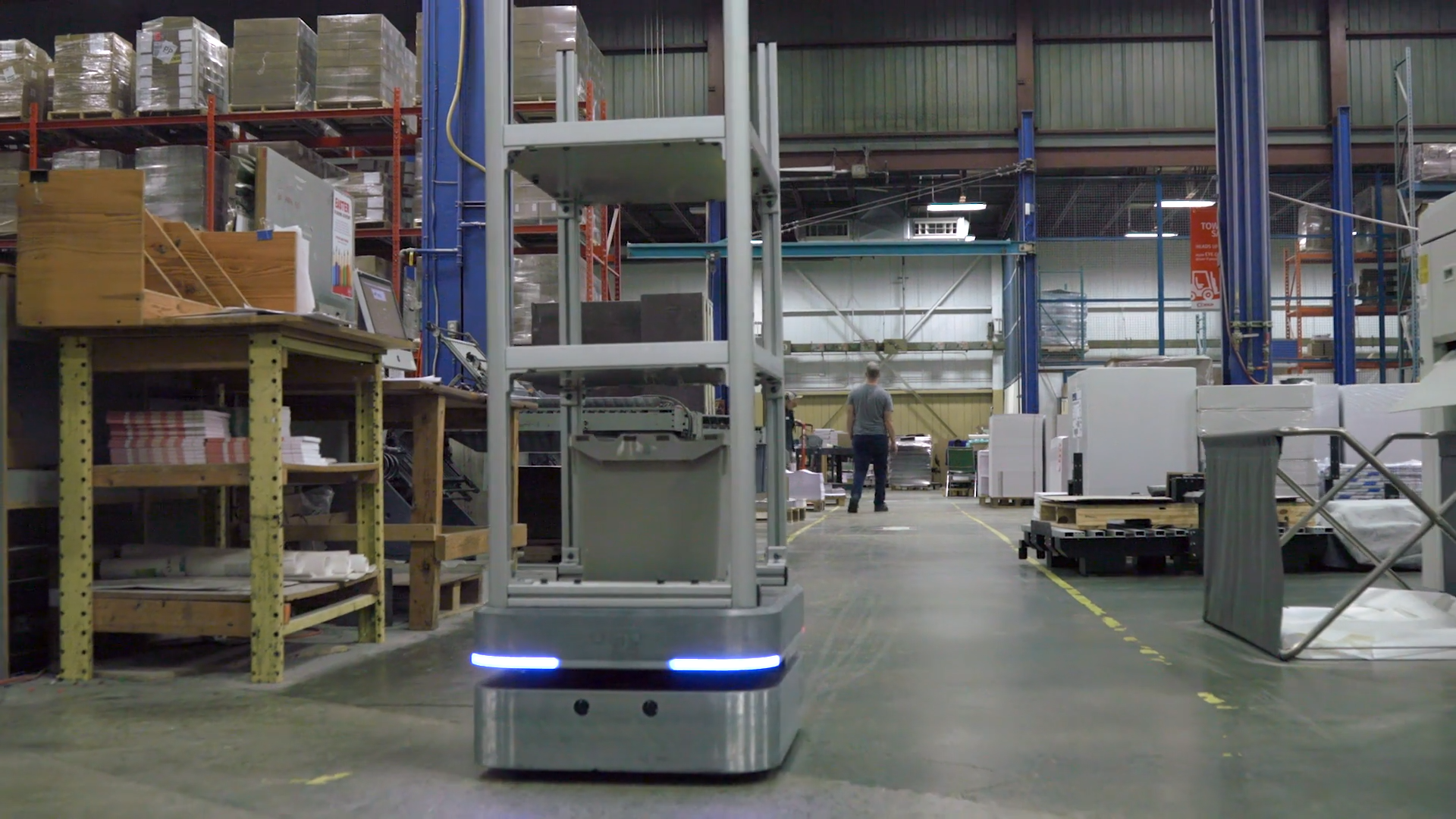
0%
REDUCTION IN CYCLE TIMES
0x
INCREASE IN THROUGHPUT
Modern printing company makes material handling automation a competitive differentiator
For over 100 years, Cober Solutions has thrived in the commercial printing business while the industry as a whole has declined. A key part of Cober’s success is their culture of innovation, which puts team efficiency and technology at the heart of the company.
Cober’s production floor is a classic example of a job shop - each work order is unique and there is high variability in the processes required to complete each job. Hundreds of jobs move through the facility in unique paths every day, connecting machines and workstations operated by skilled technicians. As a result, efficient material handling is a must-have critical competency for Cober to meet customer demand.
As Cober evolved to meet the changing demands of the print industry, the company made significant investments into high-tech automation. However, no material handling automation system met the requirements of Cober’s random, non-linear material flows. This left the responsibility of progressing jobs to the next step in the work order to the same skilled technicians and operators responsible for production - a problem made worse as the nature of print work changes from large print runs to a greater number of smaller, customized jobs.
Traditionally, print jobs used to be huge jobs. Huge stacks of paper. As we customize jobs, the run lengths get smaller and smaller and there are more pieces of the puzzle to move through the plant. Instead of 20 jobs a day, we're doing 700. Having a way to automate that and move 700 jobs around the plant on a daily basis - we needed help [...] We have excellent people that can do the work on the machinery, but we needed a way to move [the jobs] through the plant.
Sam Mueller
Director of Manufacturing, Cober Solutions
Cober chose OTTO autonomous mobile robots to automate the non-linear flow of materials between job processes because OTTO can handle dynamic environments without requiring fixed infrastructure such as wires, guides, or predefined paths. Before OTTO, automating material was simply not possible because of the amount of change on their production floor.
As Mueller continues,
"Our facilities are constantly changing. Being able to have a piece of equipment that can change on the fly is very important to us. Having conveyors in our industry doesn't really work in our industry because, depending on the seasonality of our work, there are skids all over the place. Having a piece of technology that can work in that environment is very important to us."
Since implementing OTTO, Cober management has seen an improvement in employee productivity and engagement with their work. As Mueller goes on to explain, the Cober management team has,
“seen improvement with how quickly jobs can move from place to place. It's freed up our cutters and our mailroom. Rather than moving around the plant looking for specific jobs, they are able to focus on the job at hand. They are not getting distracted from the very important tasks they are working on by looking for jobs that may be spread out throughout the plant. It's brought to them now."
Nic Driever is the technician at Cober who is primarily responsible for material flow automation with OTTO. Nic explains that OTTO helps the production staff focus on tasks that they are trained to do keeps overall equipment effectiveness metrics high.
Prior to OTTO being there, those operators would have to stop their machine and take their finished good from that machine onto the next station and that takes away 10-15 minutes every time they're doing that. Now with OTTO, it's 30 seconds. I load my printed material onto OTTO and send it off and I get to keep the machines running a lot longer. It makes the company more efficient as well as it keeps the people on task with what they're trained to do and what they're good at doing.
Nic Driever
Technician, Cober Solutions
“Our goal is to be more efficient than anyone else in our industry,” says Todd Cober, vice president of Cober. “Whether you're a printing company, a warehousing company, or an auto parts company OTTO can still add value. For us, high efficiency printing is really high efficiency material handling.”
OTTO 100 driving through Cober's facility.
01/03