Case Study
GE HealthCare achieves lean efficiency in Milwaukee facility
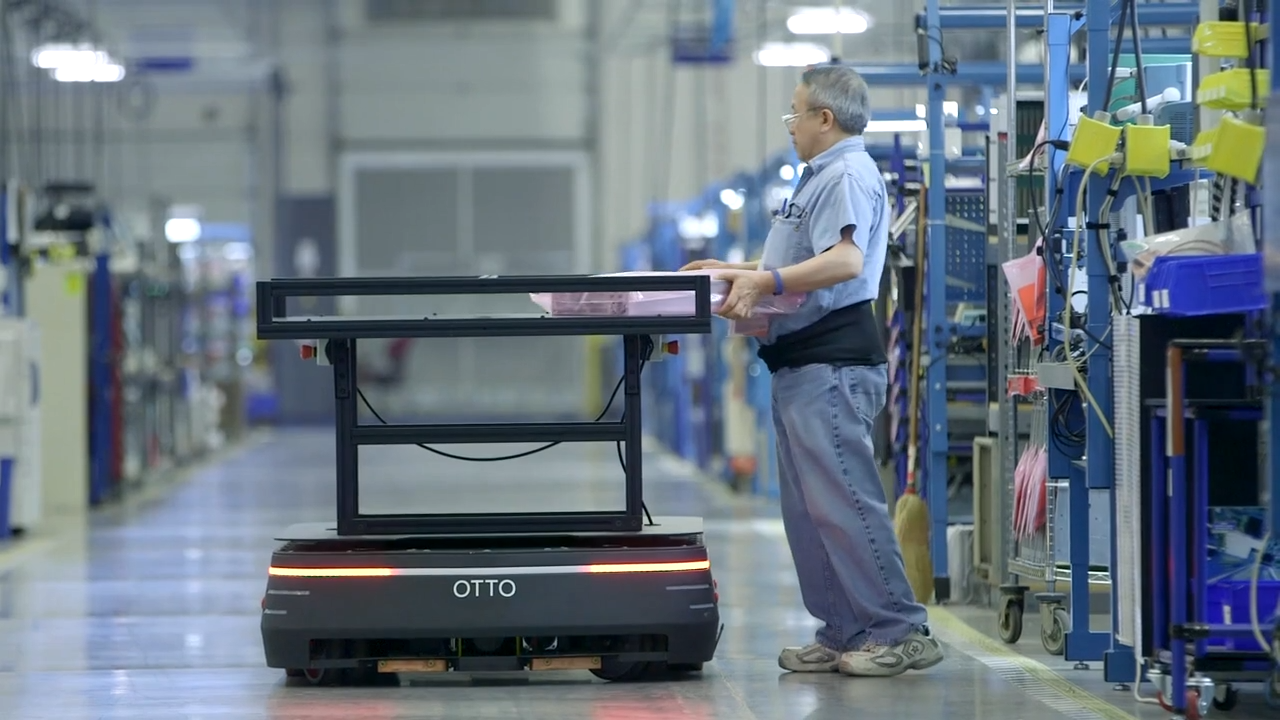
0%
floorspace saved
0%
reduction in repair cell size
0
robots deployed
The task: Delivering medical equipment
GE HealthCare’s 280,000 square foot facility in Milwaukee is a mega center for medical equipment repairs. Multiple U.S.-based repair operations have consolidated into this site, and it now functions as a showcase for the use of advanced technology to improve process in material handling. The facility upholds lean manufacturing principles as a way to achieve their mission: to provide customers with reliable, consistent, fast and quality repairs so that hospitals can restore operations quickly and focus on providing the best patient care. For this reason, efficiency must be at the core of all operations.
In previous repair centers technicians pushed carts to move equipment between repair cells, shipping and other technicians. This manual process worked in batches, making material flow inefficient. Finished repairs would be added to other types of equipment on the nearest cart, which was pushed around to pick up other finished repairs before proceeding to shipping. The time taken for finished repairs to reach shipping was dependent on what other types of equipment were in for repair, which led to delays.
Additionally, other facilities suffered from wasted floor space due to the need for bulky carts and fixed infrastructure. This reduction of productive floorspace decreased the number of repair cells and limited throughput. GE needed a better material handling solution that fit the demands of their team.
“We needed to find an on-demand solution for moving materials throughout the facility,” says Patricio Espinosa (Director, Americas Repair Operations, GE Healthcare). “OTTO Inventory Movement Platform is a perfect solution because it gets materials where they need to be, when they need to be there.”
Today, OTTO's software and OTTO 1500 autonomous mobile robots are used to deliver parts for over 2,000 medical equipment repairs per week.
The solution: Moving to lean manufacturing principles
Implementing the OTTO Inventory Movement Platform enabled the repair center to improve their material flow and find new efficiencies in the repair process. Instead of batching parts to travel in a variety of directions, the automated material handling solution enables pull-type supply chain management. Repairs are finished quickly, despite short lead times, because the automated material movement is based on actual demand. Instead of encumbering throughput by batching all material movement regardless of priority, OTTO delivers repairs to their destinations in an optimized workflow:
- When a technician is finished with repairing a part, they call an OTTO autonomous mobile robot.
- OTTO brings a new part to be repaired, and takes the finished part to shipping.
GE HealthCare’s material handling is not easily standardized. The facility receives differently sized parts for repair every day, and many are non-conveyable. Additionally, different parts need to be delivered to different repair cells.
The OTTO autonomous mobile robot has the ability and flexibility to move without infrastructure like magnetic strips or conveyors. The system can make a decision to turn and take different routes, which was essential for us. Our process changes every day depending on what parts come in for repair, but OTTO can accommodate all of them with its flexible attachments for different loads.
Patricio Espinosa
Director - Americas Repair Operations, GE HealthCare
The effetcs: Unlocking floor space and new metrics for improvement
GE’s Milwaukee facility is a human-dense environment with hundreds of repair technicians, but it didn’t take long for them to get used to working alongside OTTO.
OTTO makes our jobs easier. Space is a shortage in our work areas, so it’s helpful that we call OTTO on demand and have it come pick up our parts. The pick up times are really quick, and it allows us to switch to the next part more quickly. Occasionally we meet up with OTTO in the aisle-ways and it goes right around us.
Joe Germait
Manufacturing Technician, GE HealthCare
Space is vital not just in repair work areas, but in the overall facility. Milwaukee center’s repair cells are 40% smaller since implementing OTTO because there was no need for extra physical infrastructure or large material movement equipment. This enabled GE to raise their throughput per square foot, and there has been a 66% increase in productive floor space.
OTTO’s software also provides Espinosa and his team with capabilities for process analytics. Kyle Smith (Repair Process Engineer, GE Healthcare) explains, “We can analyze the habits of our employees with the data that’s provided by the OTTO platform. This is the kind of vital information that we need to help improve our operations to deliver repairs as quickly as possible.”
OTTO 1500 delivering repaired medical equipment at GE HealthCare.
01/03