Blog
How manufacturers are addressing the labor shortage and skills gap with smart manufacturing technology
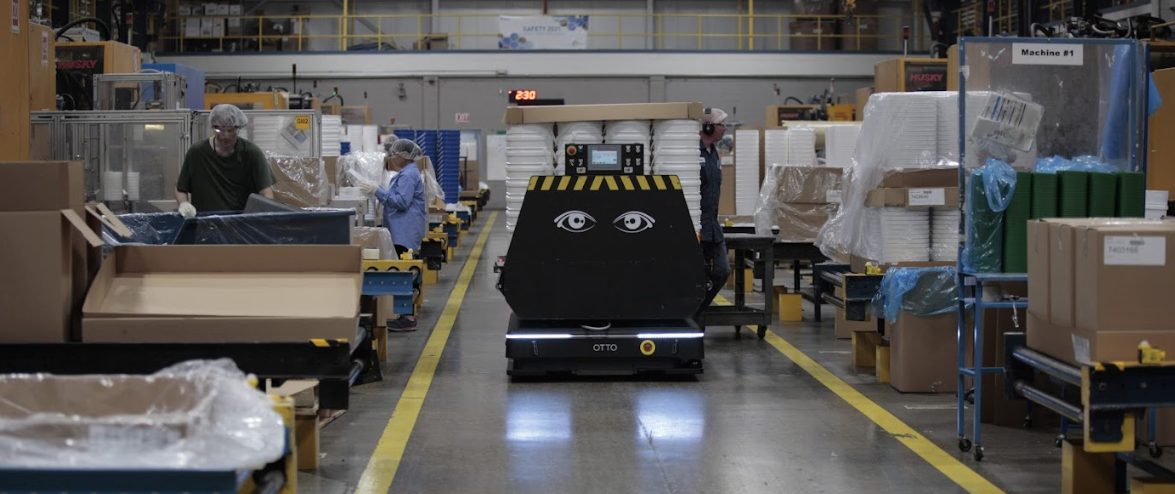
Over 1,500 manufacturers worldwide responded to Rockwell Automation’s 9th Annual State of Smart Manufacturing Report to provide insights into the industry’s current disruptors, including emerging technologies and their potential to alleviate the biggest challenges facing manufacturers today. In this blog, we’ll delve into a key trend outlined in the report: the global labor shortage and skills gap.
Today’s labor shortage and skills gap intensifies the difficulty of attracting, managing and retaining skilled workers. In fact, attracting employees with the desirable skill sets is the #1 internal obstacle to an organization’s growth, and a shortage of skilled workers is the 4th highest external obstacle—a challenge that was prominent in 2023 as well.
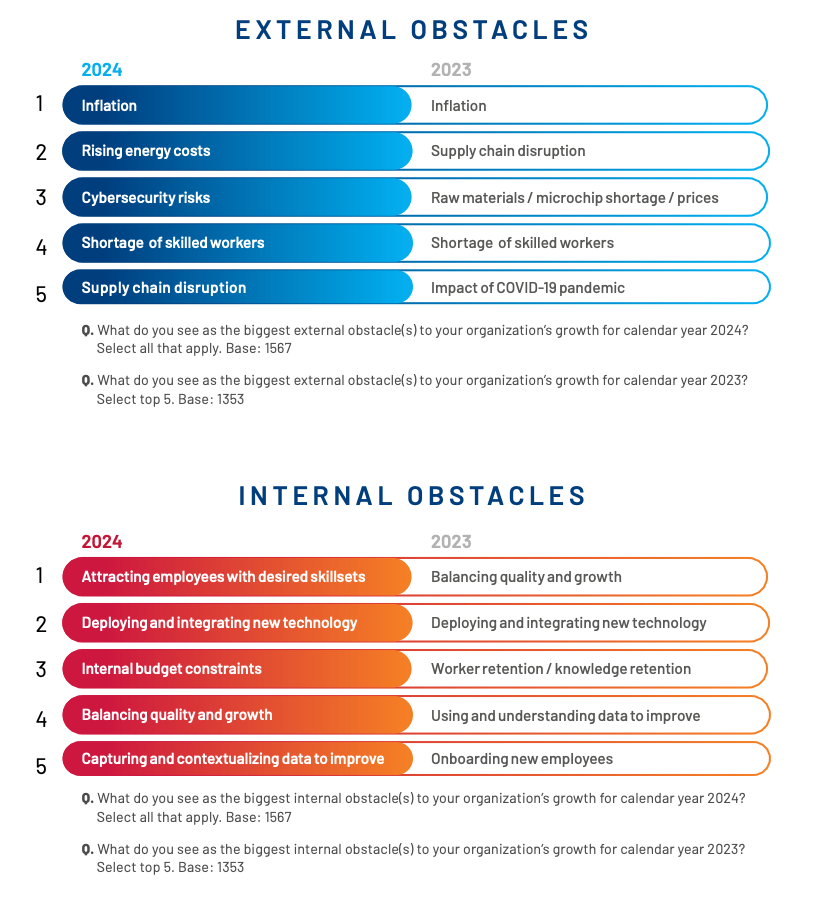
Image 1: Manufacturers’ biggest external and internal obstacles to growth for 2023 and 2024, according to the 9th Annual State of Smart Manufacturing Report.
To overcome these obstacles, manufacturers around the world are implementing smart technologies that augment their workforce and empower their employees to work effectively alongside them.
Manufacturers are implementing smart technology to augment their workforce
These internal and external obstacles are prominent across the manufacturing industry and are especially challenging as demand continues to grow. For two years in a row, manufacturers have cited a lack of a skilled workforce as the top reason they will struggle to outpace their competition.
To solve these challenges, investment in innovative manufacturing technology has increased 30% year-over-year, from 23% of operating budget in 2023 to 30% in 2024.
Adoption of technology is seen by manufacturers as the best way to mitigate against both external and internal risks.
The 9th Annual State of Smart Manufacturing Report, page 9
According to the report, the top way manufacturers are specifically addressing the industry’s labor shortage and skills gap is by increasing automation (42%).
Other ways include:
- Introducing AI / ML technologies (37%)
- Leveraging remote work to access a wider talent pool (34%)
- Introducing flexible scheduling (working hours as-able, short shifts, etc.) (34%)
- Adding / using technology to create more engaging jobs (33%)
Increasing automation is also the top way manufacturers are planning to drive positive business outcomes over the next five years (43%), followed by adopting smart manufacturing technology (42%).
Examples of smart manufacturing technology which can be used to address the labor shortage include industrial control systems, asset performance management solutions, manufacturing execution systems (MES), and production logistics solutions such as autonomous mobile robots (AMRs). AMRs are among the top three technologies that manufacturers plan to invest in over the next 12 months.
GenAI and casual AI, cobots and AMRs have already been adopted by manufacturers to enhance and complement the workforce, while reducing errors, increasing speed to value and improving quality.
The 9th Annual State of Smart Manufacturing Report, page 24
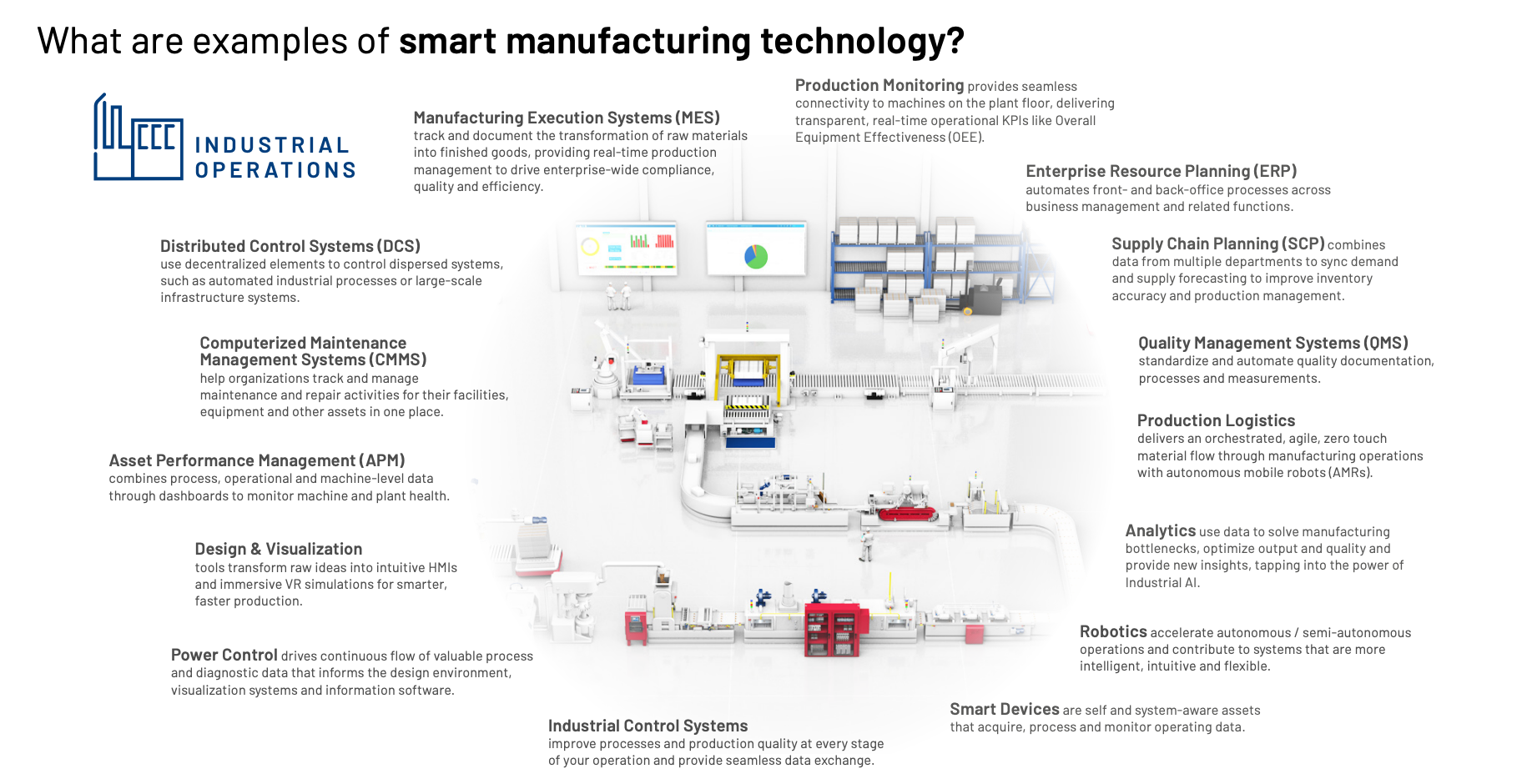
Image 2: Examples of smart manufacturing technology on page 8 of the 9th Annual State of Smart Manufacturing Report.
AMRs and other smart manufacturing technologies are helping to supplement and amplify the workforce, not to replace it. In fact, through increased use of smart manufacturing technology, 94% of manufacturers expect to hire more workers or repurpose workers to new or different roles, up from 89% in 2023.
For example, plastic rigid container manufacturer, Mauser Packaging Solutions, implemented smart manufacturing technology—specifically AMRs—to help solve labor challenges at two of their facilities. By deploying OTTO AMRs to move finished goods to the stretch-wrapper, Mauser was able to re-allocate three laborers to higher value-added roles while generating a 6x throughput increase.
Manufacturers are proactively up-skilling employees to increase engagement
Successful manufacturers today are helping their workforce adapt to incoming changes, empowering them to work effectively in ever-changing environments.
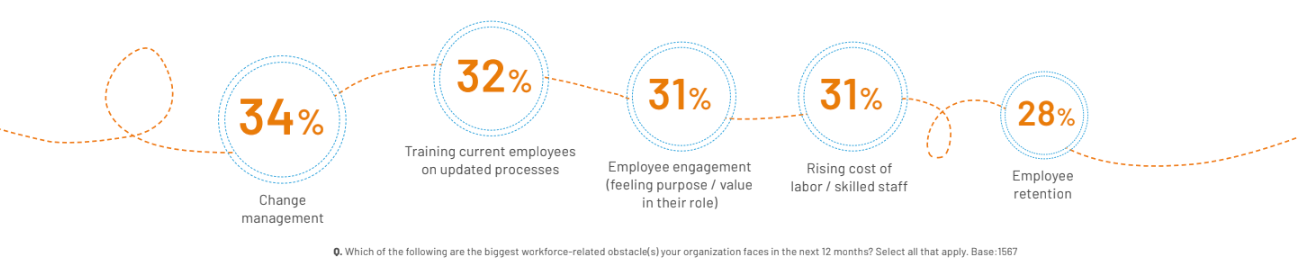
Image 3: The top 5 workplace-related obstacles manufacturers will face in the next 12 months, according to the 9th Annual State of Smart Manufacturing Report.
By training current employees on updated processes, they can feel better prepared to thrive in today’s manufacturing facilities. This change management initiative can enable employees to develop new capabilities, working alongside their new smart technology co-workers. Many smart technologies such as AMRs focus on the unsafe, repetitive work so manufacturers can focus their available workers on high value-added, fulfilling tasks that require uniquely human skills. By proactively preparing the workforce for these new technologies, manufacturers can better retain their employees and keep them engaged.
The global labor shortage and skills gap are certainly challenges that have been prevalent for many years, and will be prevalent for many years to come. However, Rockwell’s 9th Annual State of Smart Manufacturing Report helps us understand how investing in smart manufacturing technologies can help solve these challenges and better prepare our workforce for the future. Learn more in the full report.