Blog
AMA: What is an autonomous mobile robot (AMR)?
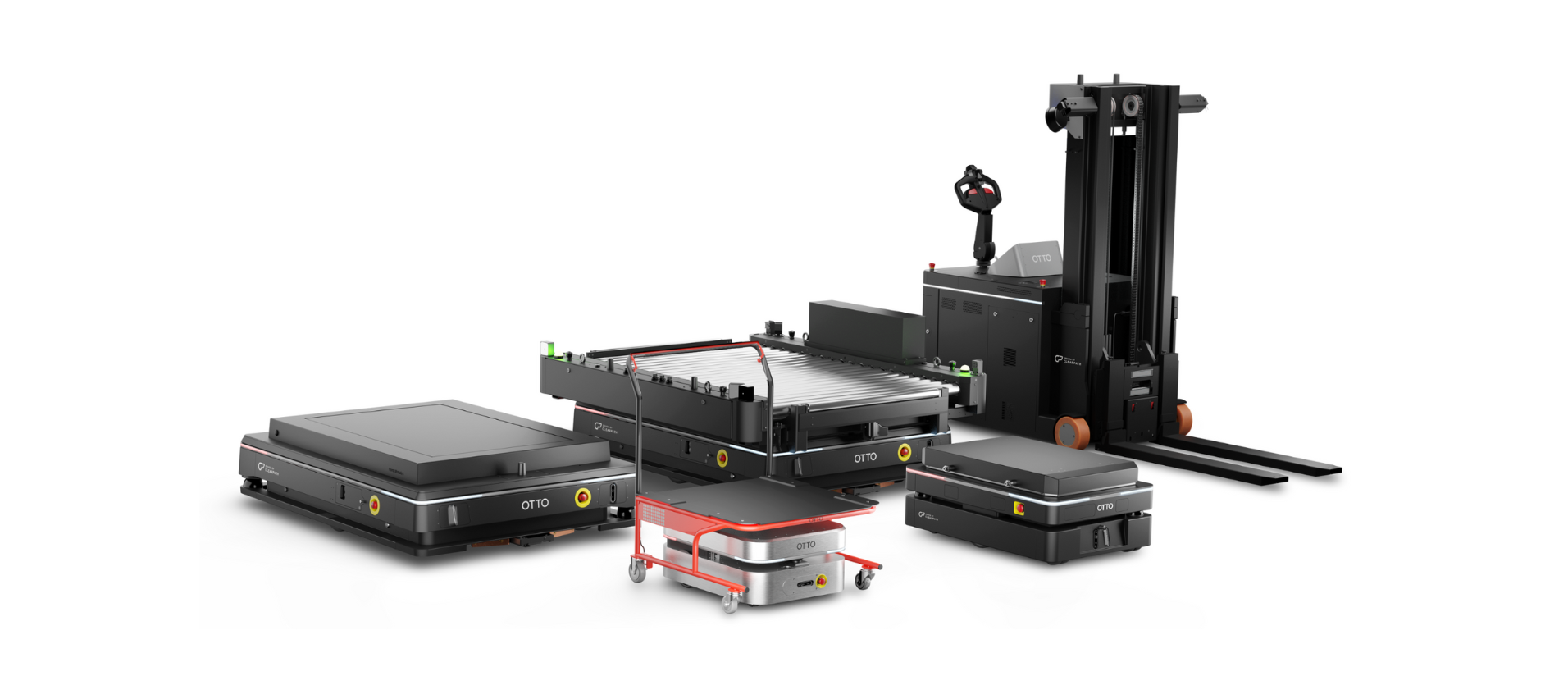
In this blog series, manufacturing facilities and warehouses ask their top industry and product questions, and OTTO’s material flow experts answer them.
Autonomous mobile robots, or AMRs, are robots that can move through their environment without direct driver input or pre-configured scripts to control the steering, acceleration, and braking. AMRs utilize laser-based perception and navigation algorithms to dynamically move through facilities, infrastructure-free. They use existing infrastructure as points of reference for mapping their localization, and path planning to efficiently and safely move from point A to point B.
A similar material transport technology, automated guided vehicles (AGVs), differ in many ways. AGVs are discrete and repeatable, offering a predictable solution. However, they lack the flexibility needed in dynamic, mission-critical factories with lots of vehicle and pedestrian traffic. While in this blog we’ll focus more on AMRs themselves, you can learn more about the difference between AGVs and AMRs in our recent AMA blog titled “When Should I Implement an AMR Versus an AGV in My Facility?”
What is an AMR?
- AMRs are a technology designed to improve the efficiency of material movement inside manufacturing facilities and warehouses. They help solve safety and labor shortage challenges associated with traditional material handling. Together, humans and AMRs work collaboratively to build safer and more fulfilling workplaces.
- AMRs are built to deliver the right part to the right place at the right time. They are currently used by Fortune 500 companies around the world to improve productivity and safety, and minimize required floor space. AMRs can have a flatbed or forked form factor. For example, OTTO offers 4 flatbed AMRs—OTTO 100, OTTO 600, OTTO 1200 and OTTO 1500—and one forked AMR (or autonomous forklift)—OTTO Lifter.
- The “automated” in AGV typically means “doing the same thing over and over again based on a simple cue.” An AMR, however, is “autonomous,” which indicates an added awareness of its surroundings to overcome unexpected challenges. For AMRs, this means the ability to drive around unexpected obstacles in its path or to generate a new route to its destination completely independently.
- AMRs also safely interact with people in a shared space. Safety-rated LiDAR sensors, speed sensors, 3D depth-sensing cameras and more ensure the unwavering safety of people and equipment in the facility.
- AMRs can be outfitted with attachments to integrate into a facility seamlessly. These attachments often include carts, lifts and conveyors.
- The applications best suited to AMRs include bringing materials to and from people, bringing materials to and from automation equipment, bringing materials to and from racks and near the floor, and transporting pallets to and from the floor and stands.
- AMRs do not require external infrastructure for navigation and can be operational in less than one day. The fleet operates from a centrally controlled map on a fleet manager, which is responsible for coordinating the right robot for the right task at the right time, and configuring traffic rules for robots to follow.
Now that you understand what an AMR is, it’s important to evaluate if the technology would be useful in your facility. Discover the differences between AGVs and AMRs in this in-depth look at the two technologies. From flexibility to usability, AGVs and AMRs differ in many ways, and it’s important to understand which is right for your facility and your workflows.
Written by Graham, Product Enablement Manager at OTTO.