Blog
How AMR technology improves predictability in your value stream
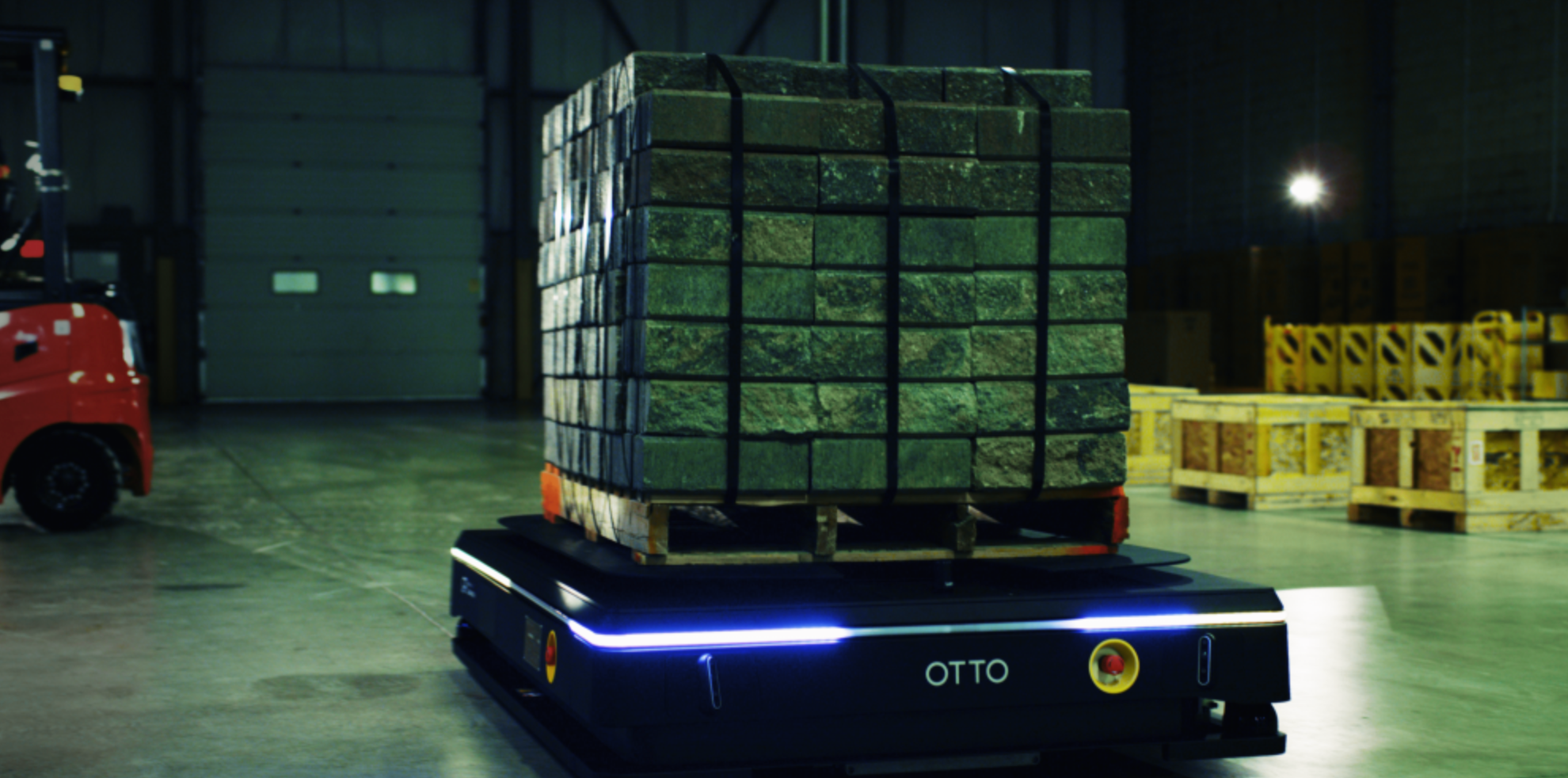
A manufacturing facility’s lifeblood is its value stream. In order for a facility to be successful, that value stream must move quickly, efficiently, and predictably. This means knowing when and where products will be, and who or what will be delivering on those steps on any given day.
In a manufacturing setting, the value stream has a critical dependance on the internal movement of parts and consumables. Large or small, assembly lines are focused on the smooth motion of the product, with parts being delivered around or beside the line. How parts get delivered to the assembly line has long been a challenge and traditionally handled by direct manual labor.
However, manual material handling can be extremely dangerous. According to the US Department of Labor, manual material handling is the leading cause of compensable injuries in the American workplace. Manual labor is best suited to the parts of the value stream that require critical thinking, such as handling transition points, effectively solving or preventing problems before they occur, and planning ahead. With worldwide hiring challenges, direct manual labor is wasted on pushing a cart.
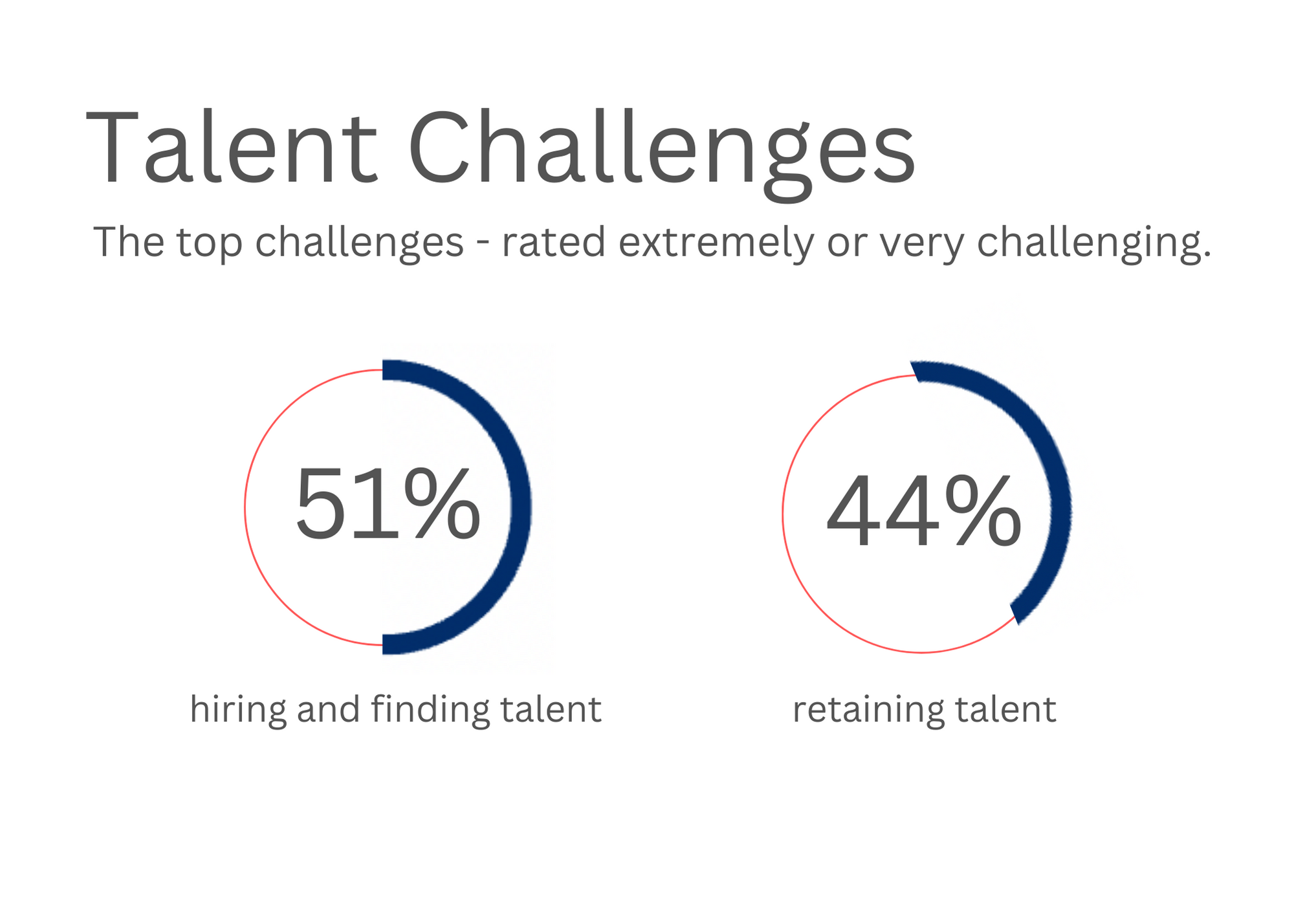
According to the 2022 MHI Annual Industry Report, 51% of companies rate hiring and find talent extremely or very challenging, while 44% find retaining talent difficult.
AMR technology fulfills value chain needs
Autonomous Mobile Robot (AMR) technology is able to perform mundane tasks like pushing a cart to enable workers to refocus on the more value-adding tasks in the value stream. Assembly lines are kept well stocked, which lowers stress levels for the operators and keeps operations running smoothly. AMRs move material quickly, efficiently, and predictably to ensure your value stream is profitable.
OTTO Motors' AMRs never sacrifice safety for speed
Value streams need a quick, productive operation. Even when dull material handling is replaced with AMRs, facilities still require quick operations to get the job done. OTTO Motors' AMRs have a top speed of up to 2m/s (~4.5mph), and utilize 13+ years of autonomy design improvements to maintain as high an average speed as is safely possible. With our adaptable and powerful OTTO Fleet Manager software, you can design your facility map to smoothly and safely integrate AMRs with existing traffic.
AMRs drive efficiency in your facility
AMRs follow the rules of the road set by your facility and plot the quickest allowable route to its destination. If something blocks the route, such as a box or person, AMRs can detect it, and change course to navigate around it autonomously, unlike Automated Guided Vehicles.
The AMR will deliver parts, materials, finished goods, and more to the indicated drop off location efficiently. If the assembly line needs to change, AMR drop-off-points can be moved with a click of a mouse. This is done through our easy-to-use OTTO Fleet Manager software, where a few clicks can enable small or large facility map changes, and job or robot changes too.
AMRs also share the space with other users of the aisleway, including workers. The facility does not need isolated, confined lanes which can easily get backed up and block efficiency. See how GE Healthcare increased floorspace productivity by 66% with OTTO Motors AMRs.
Predictability in manufacturing facilities
Once a job has been triggered by the OTTO Fleet Manager software, the AMR will execute that job without distraction. The robot will solve its way around obstacles and blockages throughout the facility until it arrives at its destination. The technology optimizes charging times against queued jobs so you’ll always have a worker when you need one.
During a labor shortage crisis, when your most valuable resource is your staff, wasting their critical thinking skills on repetitive, dull tasks should be automated.