Blog
Answering your top questions about autonomous material handling solutions
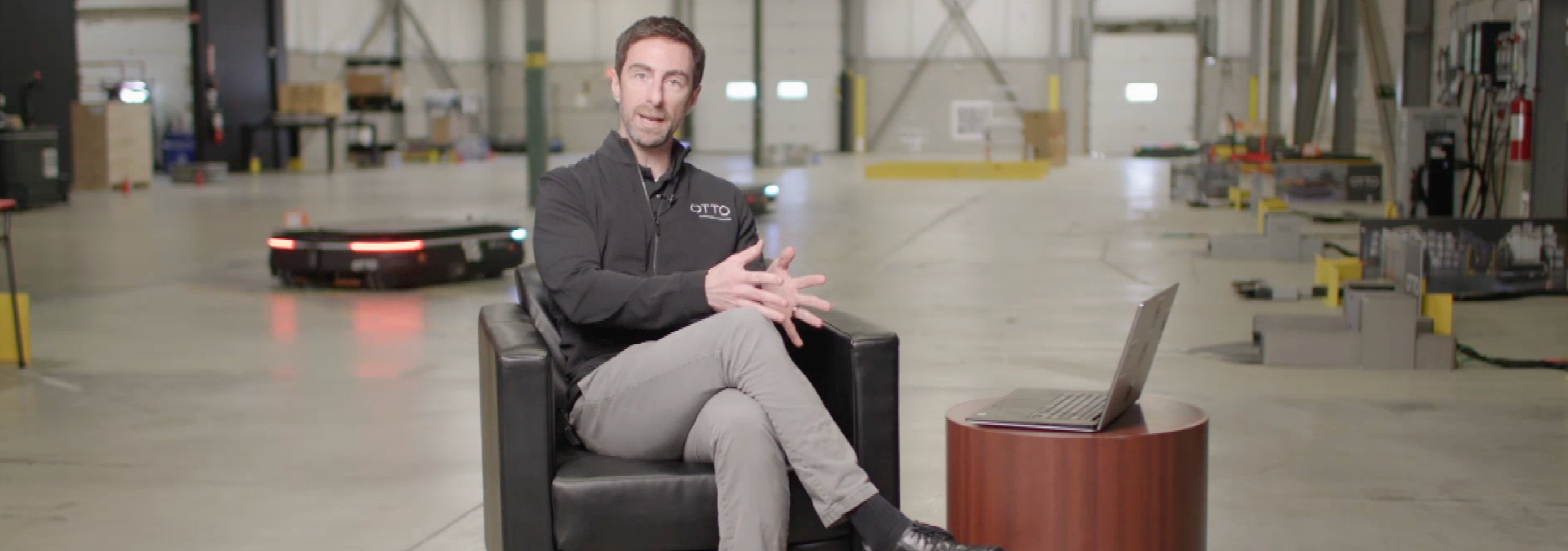
Over the last six years working at OTTO, I have received a lot of fantastic questions from manufacturers in various stages of their automation journey—some are just beginning to evaluate solutions and some are considering which vendor is best suited to meet their specific needs.
Inspired by the live Q&A sessions we host at trade shows, we wanted to bring this experience to a larger, virtual audience. I hosted a live ask me anything (AMA) webinar for manufacturers to receive tailored advice and insights that help inform their autonomous mobile robot (AMR) selection process.
We received dozens of great questions during the live AMA webinar. Here are the responses to three questions I think you’ll will find most helpful:
1. What needs to be taken into consideration for an AMR project?
When planning an AMR project, it’s crucial to assess the physical space available in your facility, including the width of your aisles and the space at pick-up and drop-off endpoints. By properly planning and optimizing the use of your space alongside your vendor, you can significantly improve robot performance, efficiency, and overall throughput.
Your facility is just one of the eight key considerations you should take into account when evaluating AMR vendors. Learn more about the other seven—including payload, service and support, and ease of use—in this white paper.
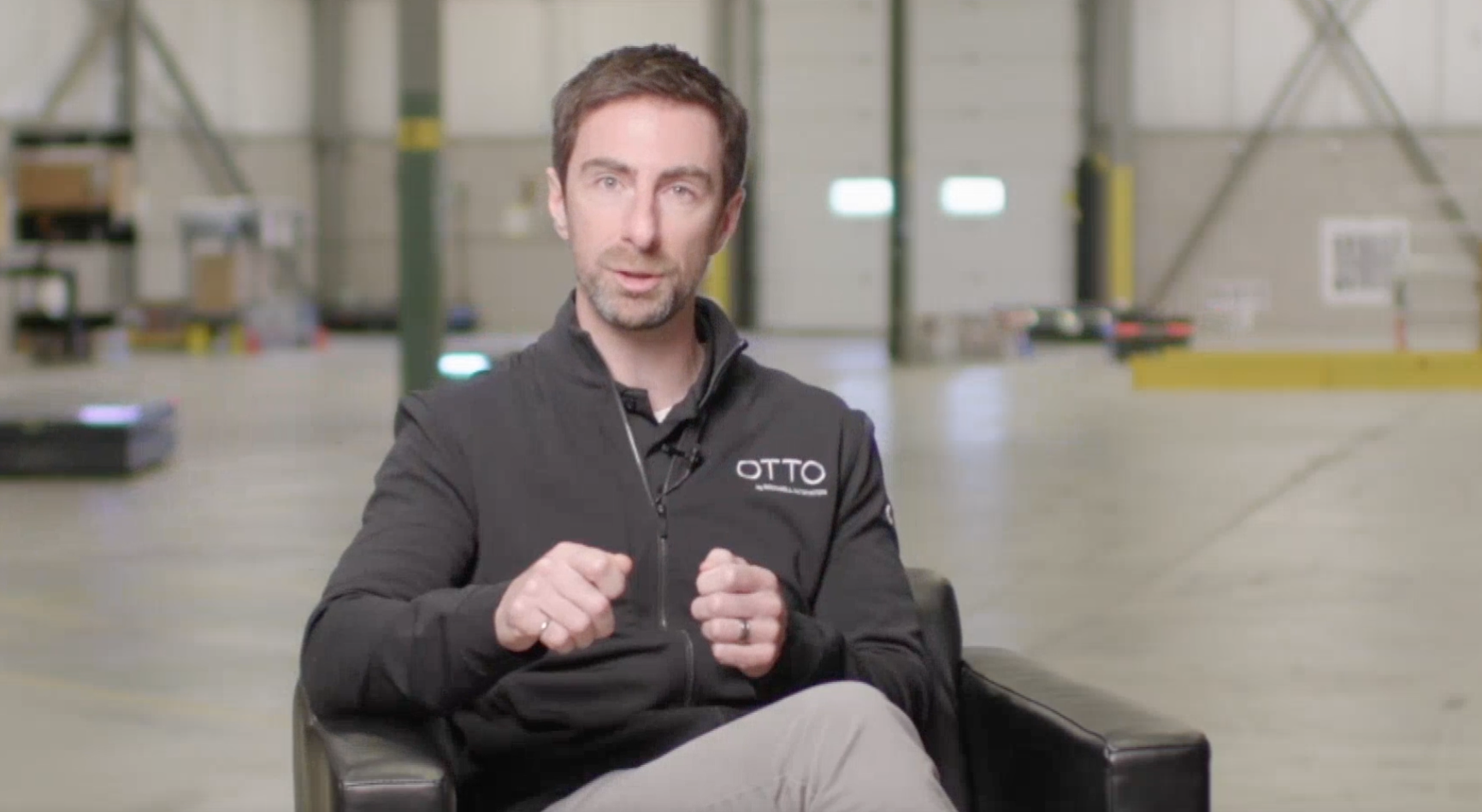
2. What safety measures should you keep in mind in areas where people and robots are sharing the same space?
When people and robots share the same space, safety relies on a collaborative approach—hardware enforces stop distances using safety-rated sensors, while software ensures the robot operates within those rules. To ensure maximum throughput, ask your vendor how they balance high productivity without sacrificing safety in shared spaces. At OTTO, we handle the complex testing and calculations upfront, delivering a system that’s safe out of the box so manufacturers don’t need to be robotics safety experts.
You can learn more about how AMRs operate safely around people in a blog I wrote on this very topic.
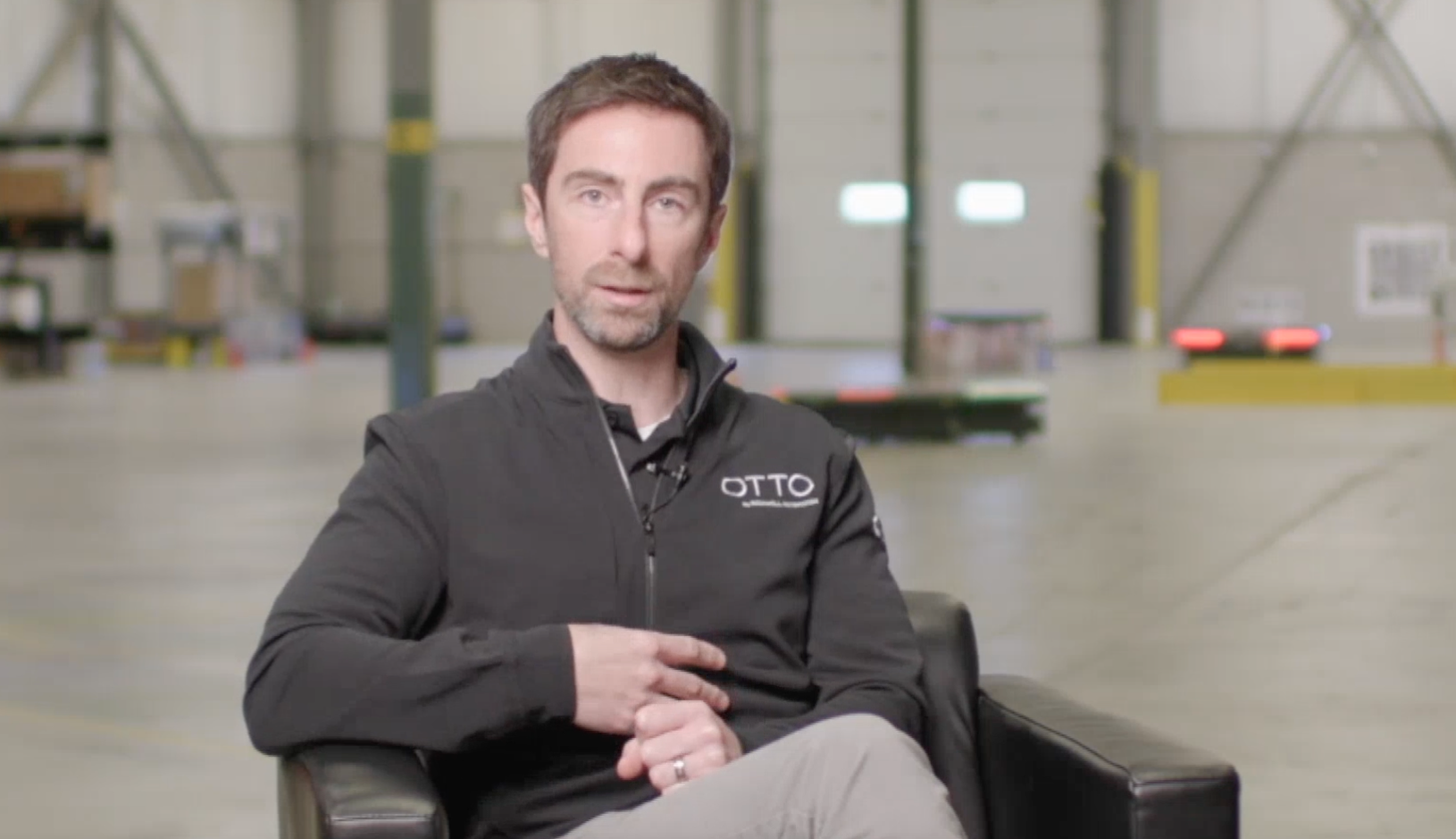
3. How does the robot know when to go pick up materials?
The robot knows when to pick up materials based on triggers that can be configured to the way your operators work. These can be manual from a tablet or button, or automated from a schedule, business management system, sensors, or PLC signals. OTTO Fleet Manager supports multiple methods, giving you flexibility to trigger work for OTTO AMRs when and how it makes the most sense for your facility and operation.
The simplicity of commissioning work is one of the most important considerations when evaluating AMR software solutions. Overly complicated software can lead to costly errors, increased training time, and reliance on third-party assistance for small changes. Learn what else you should look for when assessing AMR software in this blog.
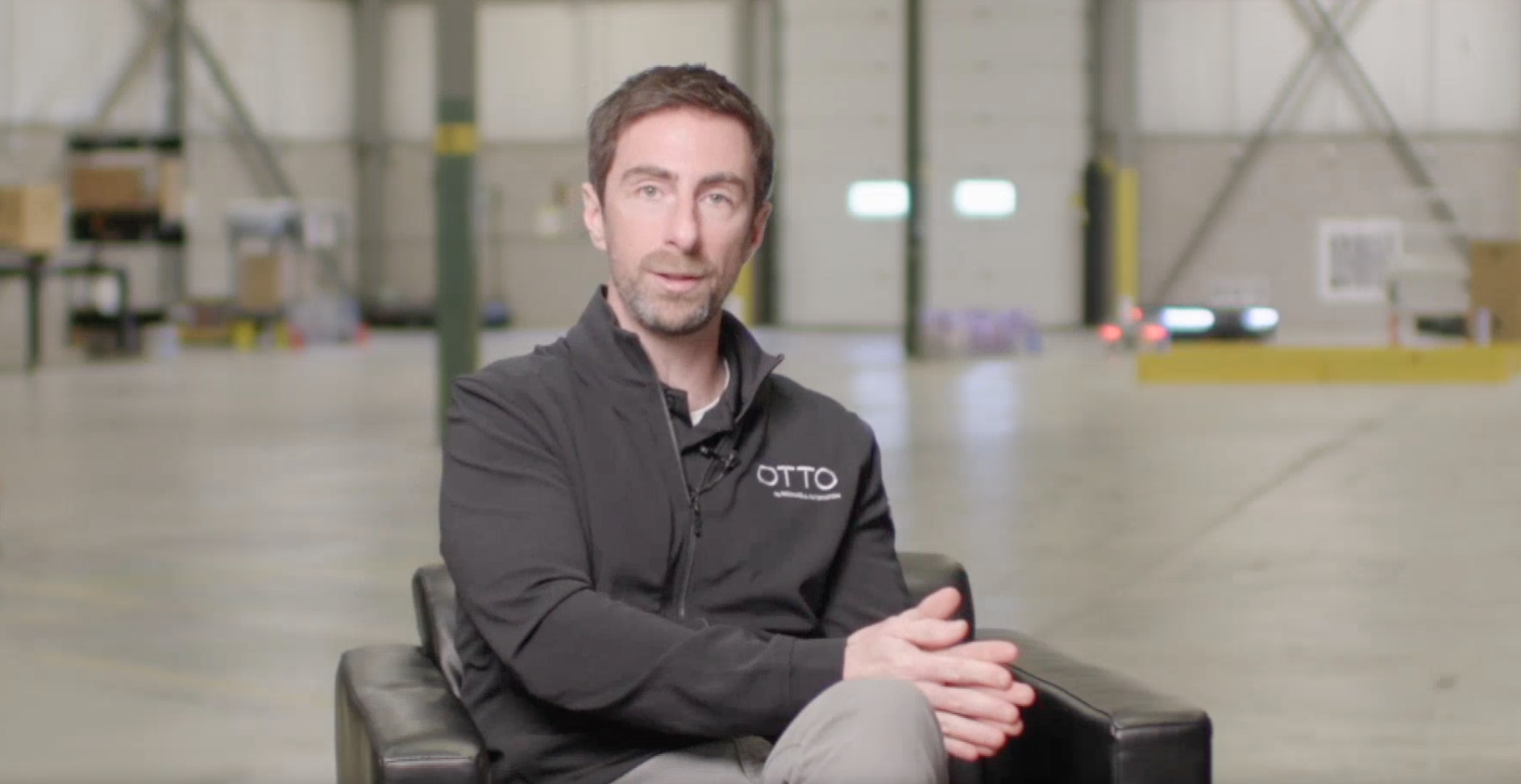
Manufacturers asked dozens of great questions during this live AMA webinar. You can watch the full recording and hear all the answers by watching the full webinar here: “I’m a Product Manager for an award-winning AMR solution, ask me anything.”
Written by Adrian, Senior Product Manager at OTTO by Rockwell Automation.
Subscribe to our newsletter
Stay in the loop on product news, case studies, upcoming events and more.