Blog
7 key considerations when assessing AMR software solutions
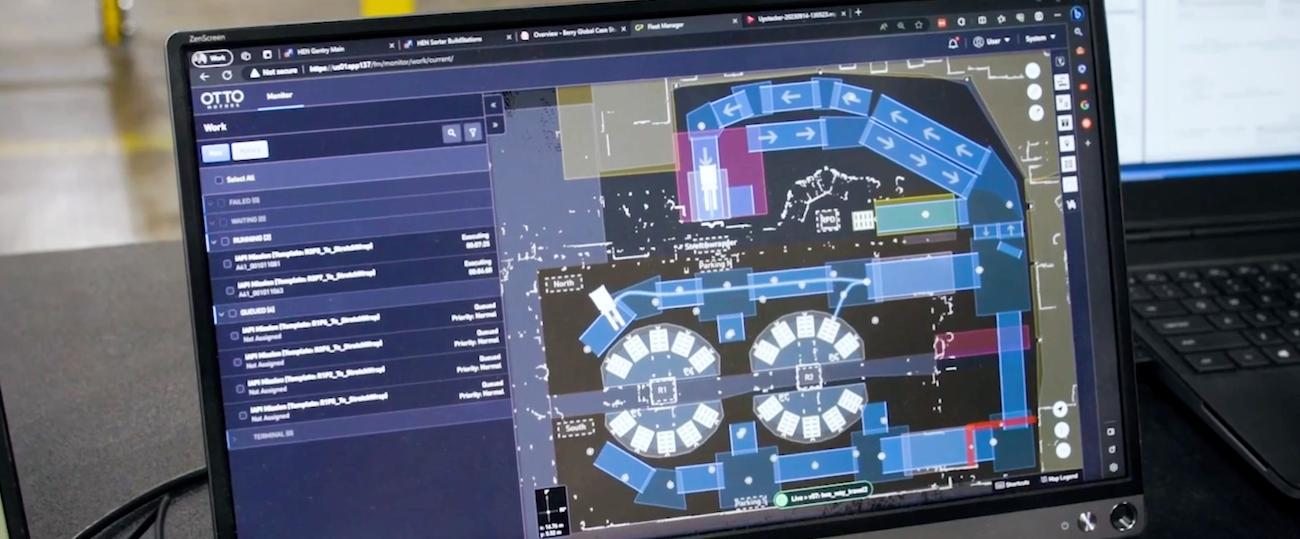
The software that powers autonomous mobile robot (AMR) deployments is key to achieving next-level efficiency. It’s essential to carefully evaluate AMR vendors’ software capabilities to ensure your solution achieves your goals both now and in the future.
To help assess your shortlisted vendors’ software solutions, look for these seven core capabilities.
1. Maximize both speed and safety
Manufacturers need to move as much material as possible, as quickly as possible, without compromising safety. The ideal AMR solution optimizes both productivity and safety by leveraging best-in-class autonomy software and safety technology.
To achieve this balance, OTTO uses adaptive fieldset technology. Working similarly to adaptive headlights on a performance car, the fieldsets shift and extend in the direction of travel, improving visibility and preventing unnecessary slow downs around corners, people and obstacles. Since introducing the technology, the average speed of OTTO 1500 has increased by up to 50%. Learn more in this blog.
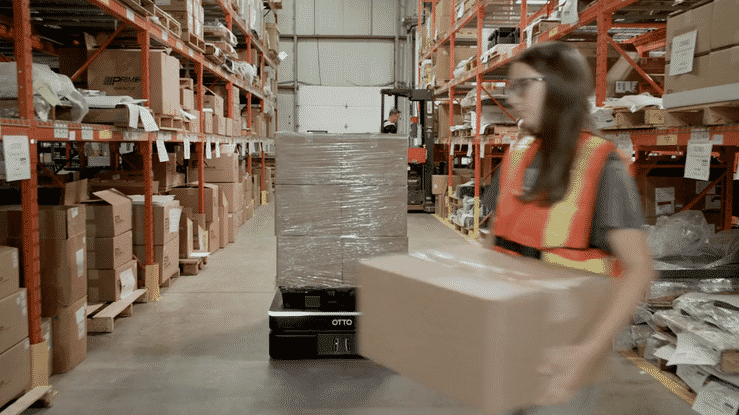
Image 1: High Performance Safety maximizes average speed without compromise to safety.
2. Maintain uninterrupted operations
Consistently ensuring the right part is in the right place at the right time is critical for business continuity. Without sophisticated software, AMRs can waste time on inefficient routes, traffic jams, and charging, impacting ROI.
Your chosen software should be able to auto-assign AMRs to specific jobs based on battery levels, minimal idle time, and maximum utilization. The software should also offer tools for effective traffic management, with low-code and easy-to-change rules such as speed limits, limited occupancy zones, and “do not enter” zones that keep operations running safely and efficiently. Learn more about OTTO’s rules of the road in this blog.
3. Future-proof operations by effectively supporting large, diverse fleets
Most AMR providers can put 100 robots in a list, but being productive at scale is the true challenge. Without sophisticated fleet supervision, AMRs can become stuck in traffic jams or simultaneously run out of battery leading to inefficiencies and unplanned manual interventions.
To determine if your shortlisted vendors can effectively support large, diverse fleets, ask which features ensure smooth bottleneck resolution and prevent congestion. Additionally, adding additional AMRs to the fleet should be effortless through the user-friendly software interface. With just a few clicks on OTTO Fleet Manager, each new robot inherits existing configurations and can quickly be put to work. Learn more in this blog.
4. Safeguard data and secure access against potential threats
AMRs have been improving efficiency in factories for decades, and like any technology entering a manufacturing environment, they must uphold rigorous security standards. As your fleet grows and further integrates with your existing systems, AMRs will likely interact with sensitive data, making a robust security framework crucial.
The software you select needs to protect factory operations. It should provide end-to-end data encryption to protect sensitive information and secure API access from unauthorized manipulation. Learn more in this blog.
5. Simplify the commissioning process
Sophisticated software is extremely valuable, but if only a few dedicated robot programmers can use it, it’s not practical. Overly complicated software can lead to costly errors, increased training time, and reliance on third-party assistance for small changes.
Your AMR software should provide intuitive dashboards for different user roles, offering simplified metrics for operators and advanced tools for engineers. It should feature a no-code interface and customizable templates to easily manage workflows, endpoints and robot tasks. Discover how one of our latest software updates helps users save 50% of set-up time in this blog.
6. Integrate seamlessly with your facility’s existing equipment and other solutions
For decades, the manufacturing industry has utilized technology to boost efficiency, but these solutions often existed in isolation, known as “islands of automation,” limiting visibility and creating inefficiencies. Choosing an AMR software that seamlessly integrates with your existing ERP, WMS, and production lines is essential.
Look for AMR software that uses APIs to connect with various business management systems, supporting standard protocols like OPC-UA, REST, and WebSockets. This minimizes the need for custom coding and centralizes logic execution. Additionally, it should be capable of communicating with other material handling robots, such as AGVs and AMRs from other providers, through an interoperability protocol. Learn more in this blog.
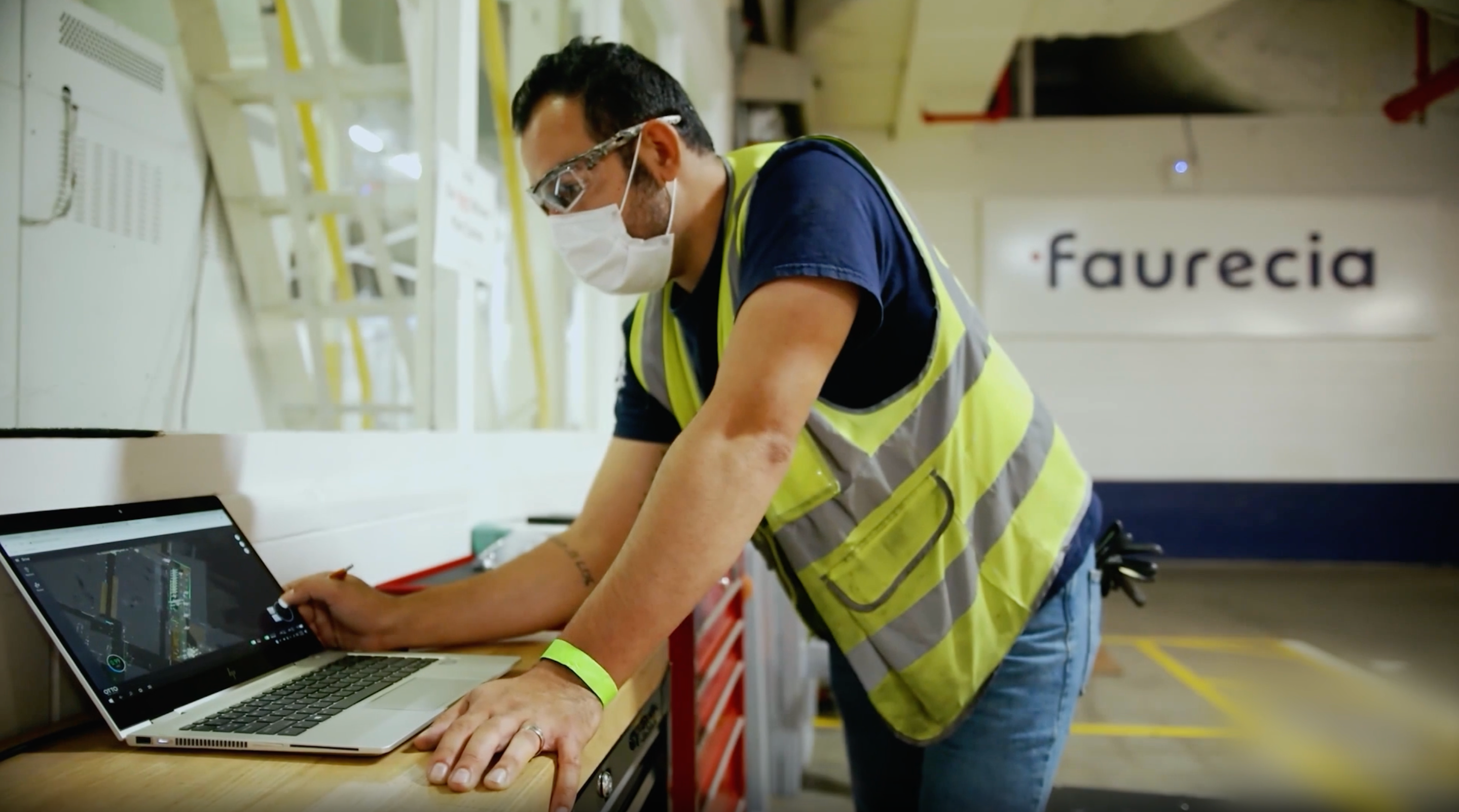
Video 1: An overview of how centralized AMR integrations transform material handling.
7. Optimize operations and enable data-driven decisions
Without a robust analytics solution to contextualize data, organizations may struggle to identify systemic issues and missed opportunities for optimization.
Your AMR vendor should offer a fleet analytics tool to track KPIs with real-time, comprehensive dashboards displaying fleet performance and enabling you to proactively make targeted enhancements to improve ROI and throughput. OTTO offers the ability to drill down into specific bottlenecks—per mission, task, robot, time, and place—so you can proactively resolve issues. Learn more about OTTO Fleet Analytics here.
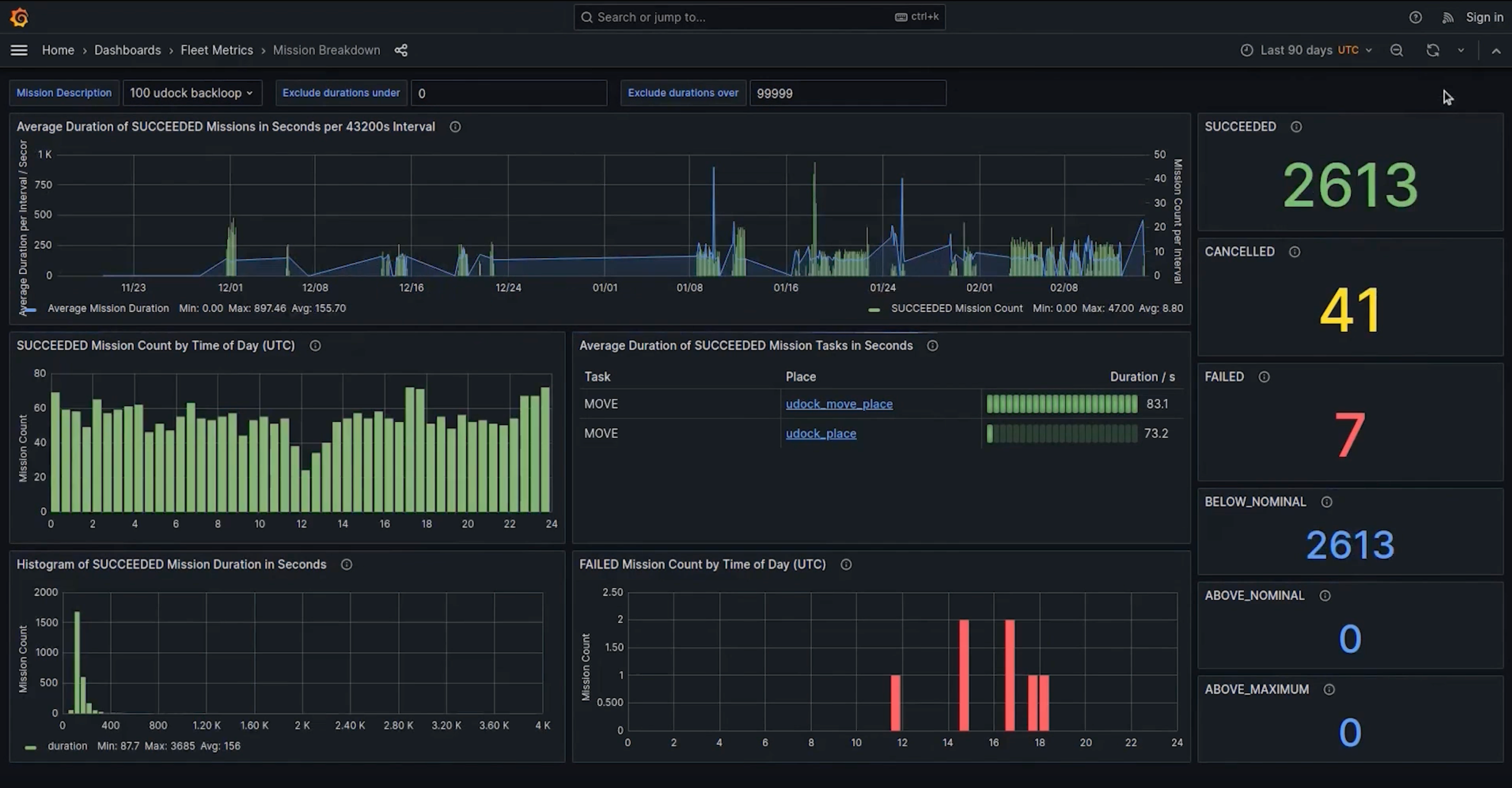
Video 2: Fleet Analytics
These seven key considerations for assessing AMR software can help you maximize your investment and fleet performance. Alongside the capabilities above, your vendor also needs to continuously update its software to evolve your fleet performance, long after the initial implementation. Regular software upgrades increase the value of your autonomous material handling solution by addressing your most common challenges with new features that improve efficiency, safety, and cost-effectiveness. Ask your shortlisted vendors about their most recent software upgrades and learn more about how to evaluate vendors in this questionnaire.
Subscribe to our newsletter
Stay in the loop on product news, case studies, upcoming events and more.