Blog
How one of the world’s largest automotive OEMs boosted productivity with autonomous mobile robots
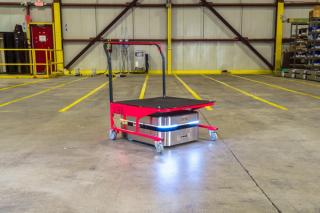
Driven by consumer and regulatory demands for electric vehicles and more sustainable solutions, automotive OEM manufacturers are rethinking how their entire operations can evolve to stay competitive in this new era. By adopting innovative technologies such as autonomous mobile robots (AMRs), these manufacturers can improve the predictability of material movement, reduce overall cost inputs per product, and combat their labor shortage. This is the story of how one automotive OEM transformed their facility with innovative AMRs.
This top 10 automotive OEM deployed AMRs to boost productivity along their assembly line
Amid constant industry pressure to improve efficiency, this Fortune 50 automotive OEM deployed an autonomous material handling solution that empowered them to optimize their workforce and floor space utilization.
The manufacturer deployed four OTTO 100 AMRs equipped with custom, integrated carts capable of moving up to 150 kg in the toughest environments. In this facility, the AMRs autonomously move bearings for engines to the assembly line when an operator requests a part through an integrated, user-friendly tablet. By transitioning three line operators to higher-value tasks, the plant improved productivity and reduced operational costs.
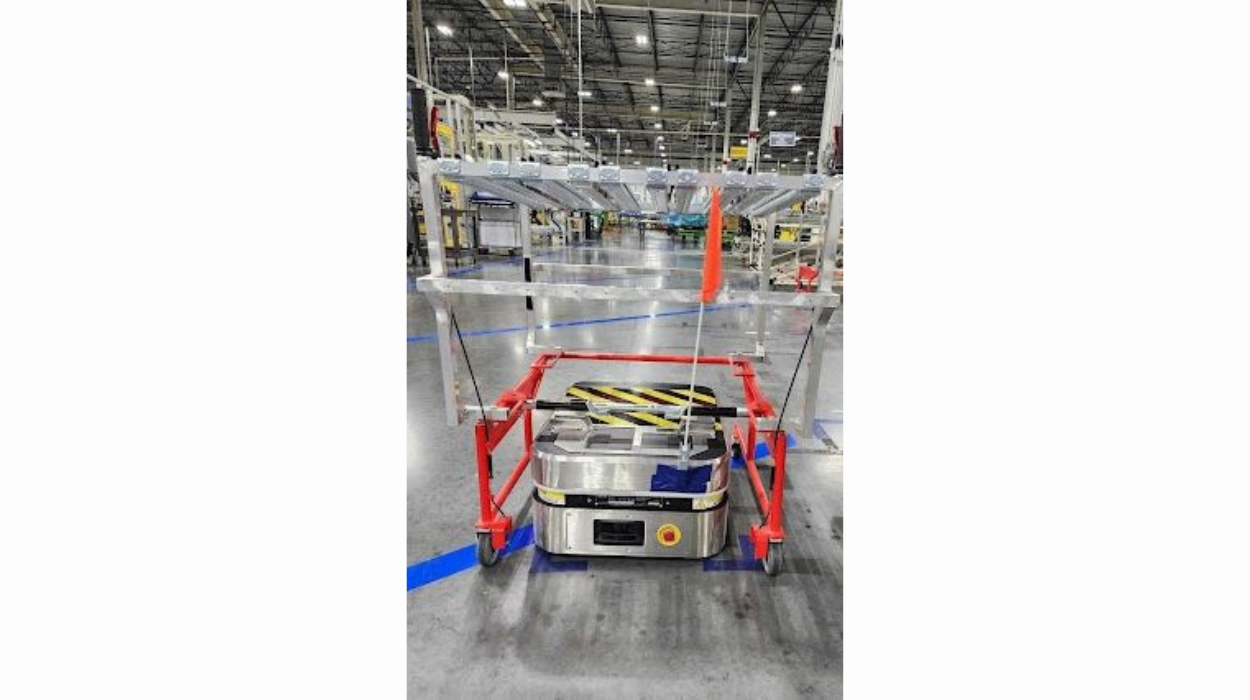
Image 1: An OTTO 100 AMR with a custom cart in the automotive facility.
In order to optimize space and improve efficiency at pick up points, the OTTO 100 AMRs reversed into endpoints, a unique feature that was quickly approved by the facility’s safety team.
The AMRs also needed to drive in pedestrian-only zones where previous material handling equipment—including automated guided vehicles (AGVs) and manually-operated forklifts—could not operate due to safety concerns and limited space. Equipped with safety-rated LiDAR sensors and 3D depth sensing cameras, the deployed OTTO AMRs were the best solution to operate in this space productively and without compromising safety.
Deployed in only 4 days, the plant plans to triple their AMR fleet
The chosen autonomous material handling solution was operational in only four days after a quick and seamless installation. Since the AMRs and the operators can coexist in the same area of the facility, the OEM is able to save space and improve safety.
Due to the simplicity of commissioning and managing the fleet, the manufacturer has not opened any support tickets with the AMR provider, demonstrating smooth operations.
Following the success of this pilot deployment, the facility plans to expand their autonomous material handling solution, adding ten OTTO 600 AMRs in two additional areas of the facility.
To discover how other leading automotive OEMs and tier suppliers are using OTTO in their applications, watch the webinar “Driving efficiency: How AMRs are advancing the automotive industry.”
Subscribe to our newsletter
Stay in the loop on product news, case studies, upcoming events and more.