Blog
Pioneering Perspectives: “A top 10 automotive OEM unlocked centralized control with FactoryTalk Optix for mobile robot management”
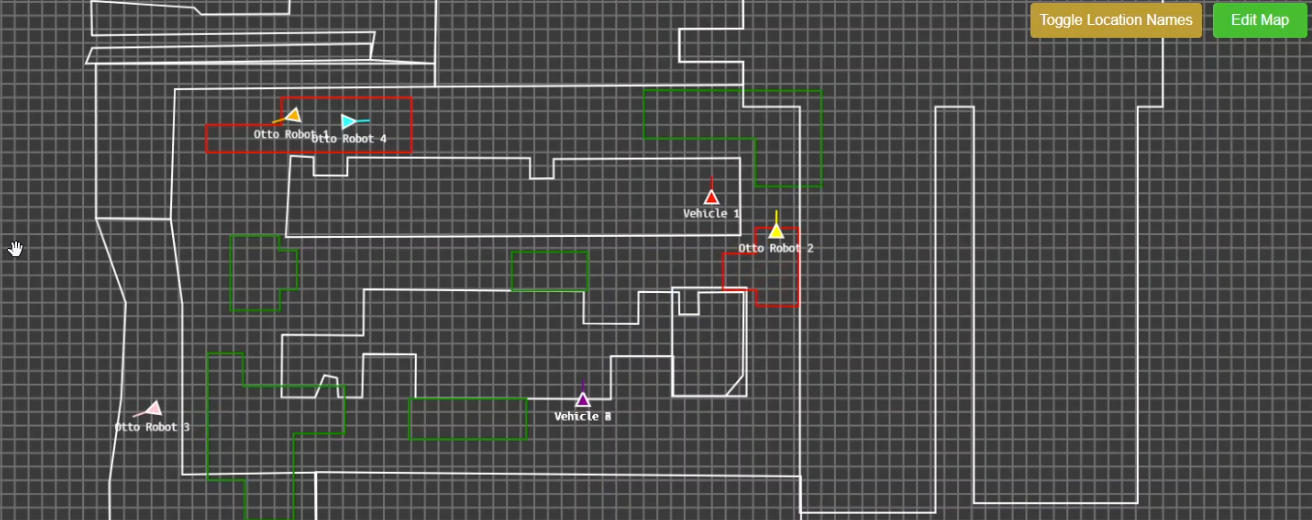
Update on April 8, 2025: This application won a 2025 RBR50 Robotics Innovation Award for "Application of the Year."
Written by Matt, Business Development Engineer at Powerhouse Controls.
I worked directly alongside the OTTO team to deliver a fully integrated solution for one of the largest automotive OEMs in the world. Working as the deployment’s system integrator, I saw firsthand how centralized control of multi-vendor material handling systems can boost visibility and efficiency for manufacturers in the automotive industry.
Why this Fortune 50 automotive OEM automated material handling with a mixed fleet
Searching for a more efficient, cost-effective way to move fenders around their Body in White facility, this truck and SUV plant opted to deploy a mix of automated guided vehicles (AGVs) and autonomous mobile robots to address unique workflow requirements.
In some areas of the facility, AGVs proved too inflexible for dynamic workflows. They needed a solution that could quickly drive long distances while managing interactions seamlessly with other automation technologies and robotic cells.
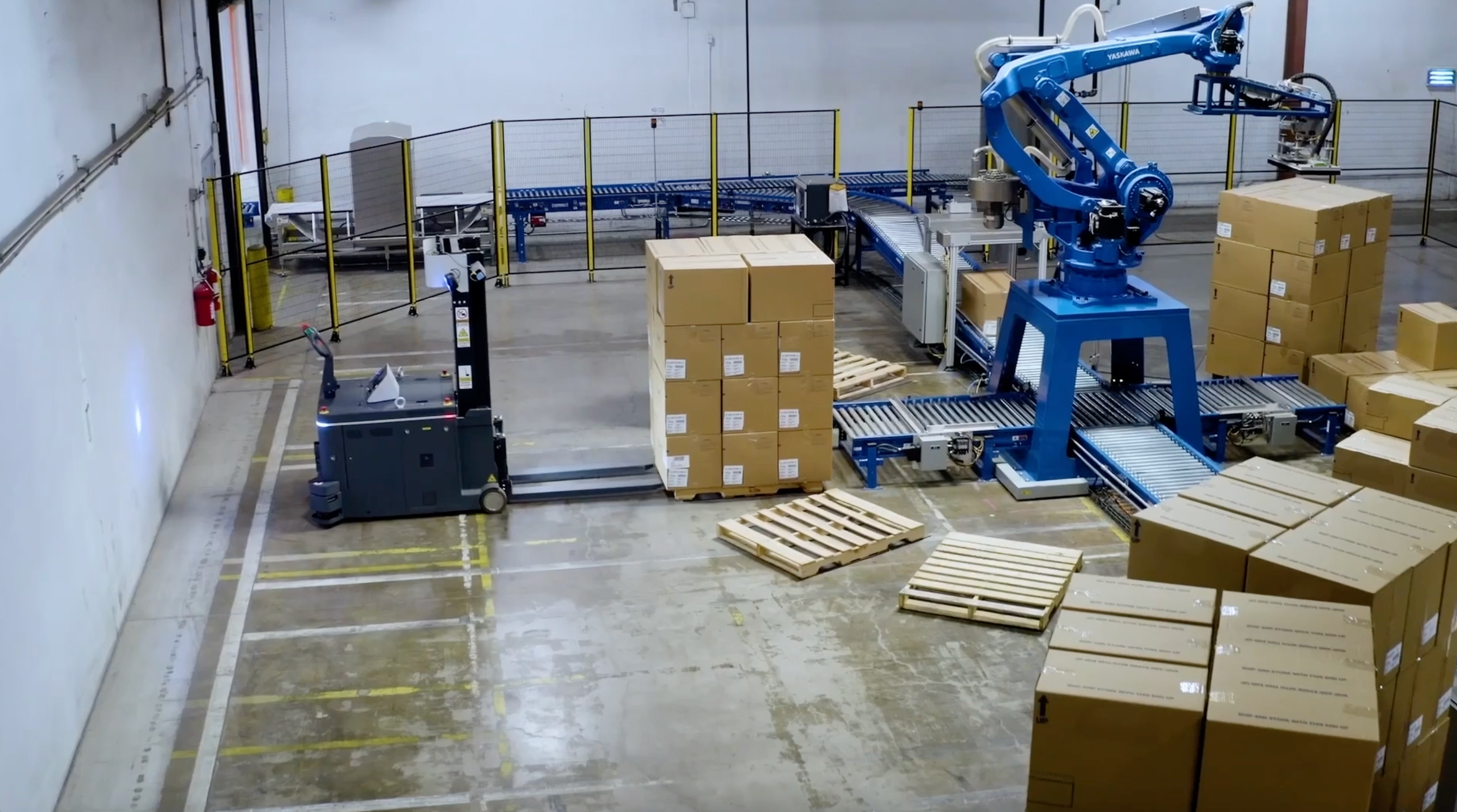
Video 1: AMRs, such as OTTO Lifter shown in this video, have the flexibility to autonomously navigate around people and obstacles, as well as connect to existing automation technologies.
How this automotive manufacturer deployed AMRs that seamlessly work alongside other material handling automation systems
The facility already had AGVs in operation, moving fenders from a cell to their production line, and had plans to implement AMRs from multiple vendors into the same workflow, starting with OTTO AMRs. In order to accomplish this, the customer needed a unified solution that could seamlessly manage various types of mobile robots across multiple vendors to avoid fragmenting operations and production inefficiencies. We were determined to not only add another layer of automation, but to revolutionize the way this facility operated.
Working together, OTTO and their systems integrator, Powerhouse Controls, needed to find a way for multiple types of mobile robots to speak the same language and understand the same rules of the road, despite being designed to operate independently.
Since we knew more vendors could be added to the facility in the future, we needed to determine how to deploy a solution on any AMR or AGV system by ensuring the robots can be referenced back to a common overarching language.
Rockwell Automation offered exactly what this customer needed: a powerful, high-level supervisory middleware platform called FactoryTalk Optix. Built to enhance human machine interface (HMI) and data visualization, FactoryTalk Optix expands capabilities in IIoT, edge computing, and data management.
FactoryTalk Optix acts like a traffic supervisor in this facility, setting the rules of the road and managing the flow of traffic for all mobile robots.
It coordinates job sequences, manages traffic at intersections, and oversees charge management, ensuring that all systems operate harmoniously without causing production disruptions.
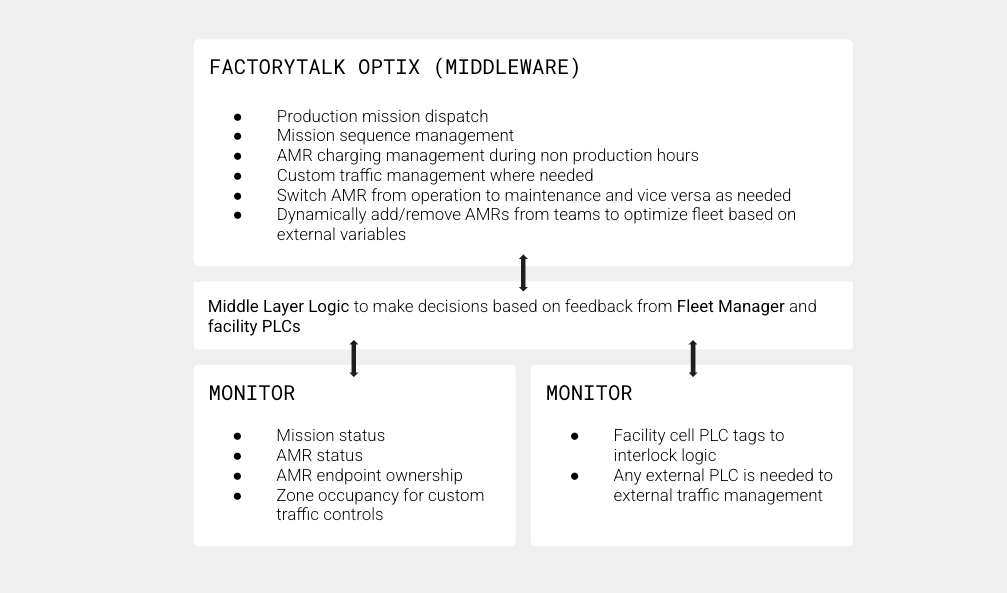
Image 1: FactoryTalk Optix is a middleware platform that speaks through a middleware layer logic to make decisions alongside Fleet Manager and facility PLCs.
Deployed in just two days, the automotive plant has seen major improvements to data management and plans to add 75 more AMRs in 2025
Picture a bustling factory where multiple types of autonomous vehicles, each from different vendors, are navigating the same complex environment, working together seamlessly. In August 2024, we deployed at the facility within just two days, with FactoryTalk Optix communicating within the mixed fleet to coordinate missions, safely interlock to robot cells, and manage traffic and charging.
This facility has deployed 9 OTTO AMRs to work seamlessly with multiple robot cells and AGV systems—three shifts per day, six days per week—in a mission-critical environment. They are now planning to expand with 75 additional OTTO AMRs, 10 more robot cells, and another AGV provider by summer 2025.
Before the integration, data was dispersed across the different software systems, causing challenges when the facility was trying to get a clear picture of operations. By centralizing data management, all critical information—whether from PLCs, AGV controllers, or AMR fleet management software—is available in one place, modeled and analyzed instantaneously to enable immediate action. This allows the plant’s operators to respond to dynamic situations with precision, including managing job sequences, overseeing charge levels, and controlling traffic at intersections.
With FactoryTalk Optix driving these innovations, the plant experienced a profound shift in operational efficiency. The customer now has access to a unified dashboard that consolidates data from various sources and vendors, enabling simplified coordination and code-free changes to their operations. This platform empowers the plant to expand its operations and integrate new vendors quickly and cost-effectively.
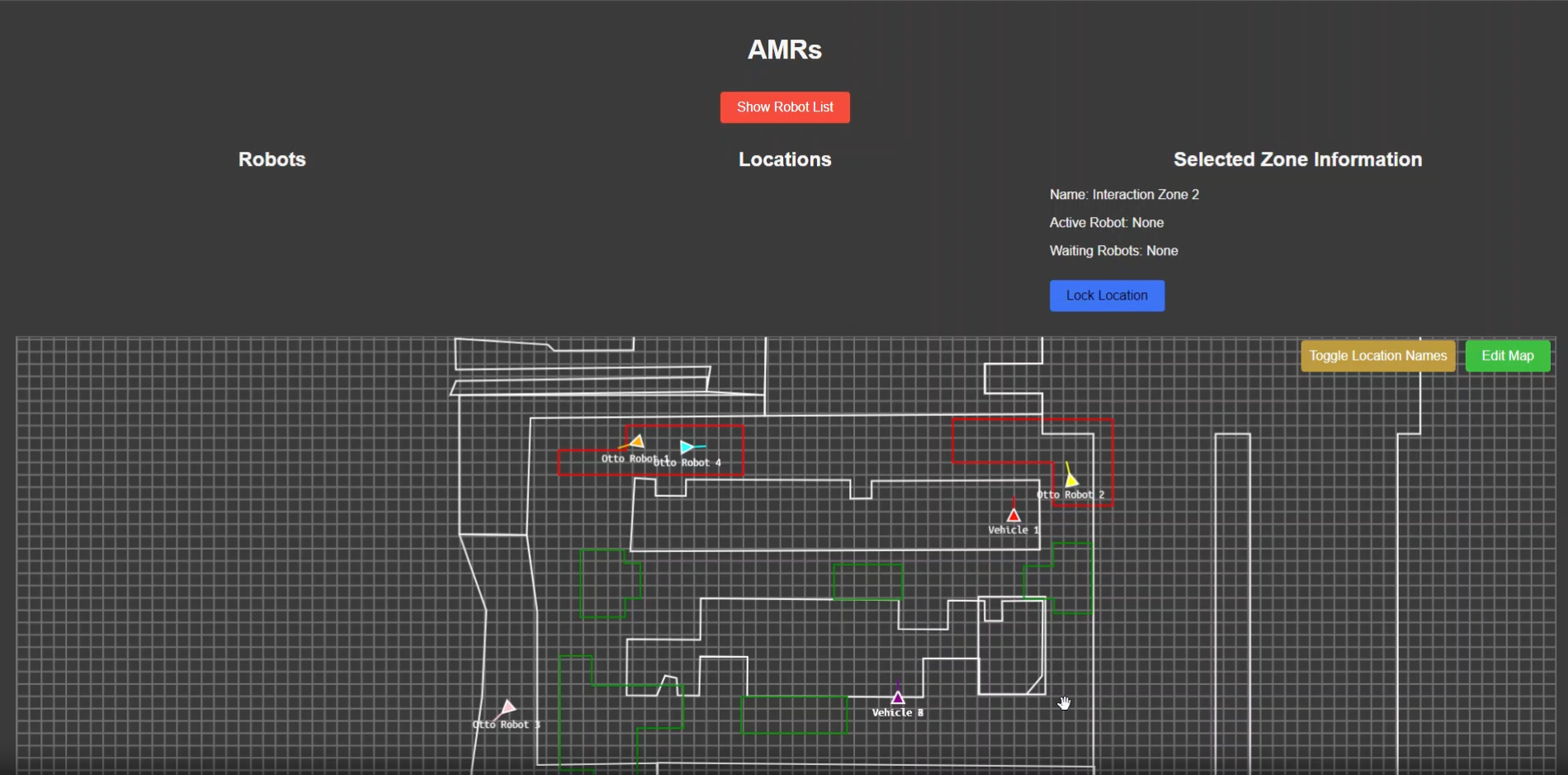
Video 2: In this example, FactoryTalk Optix is setting traffic rules for all material handling systems to follow. By prioritizing certain robots over others—in this case, OTTO AMRs—FactoryTalk Optix prevents congestion at intersections to maximize productivity.
To learn more about how automotive OEMs and tier suppliers such as this Fortune 50 customer are using AMRs and integration software to boost productivity, watch the webinar “Driving Efficiency: How AMRs are advancing the automotive industry.”
Discover more
Subscribe to our newsletter
Stay in the loop on product news, case studies, upcoming events and more.