Blog
How autonomous robots benefit the supply chain
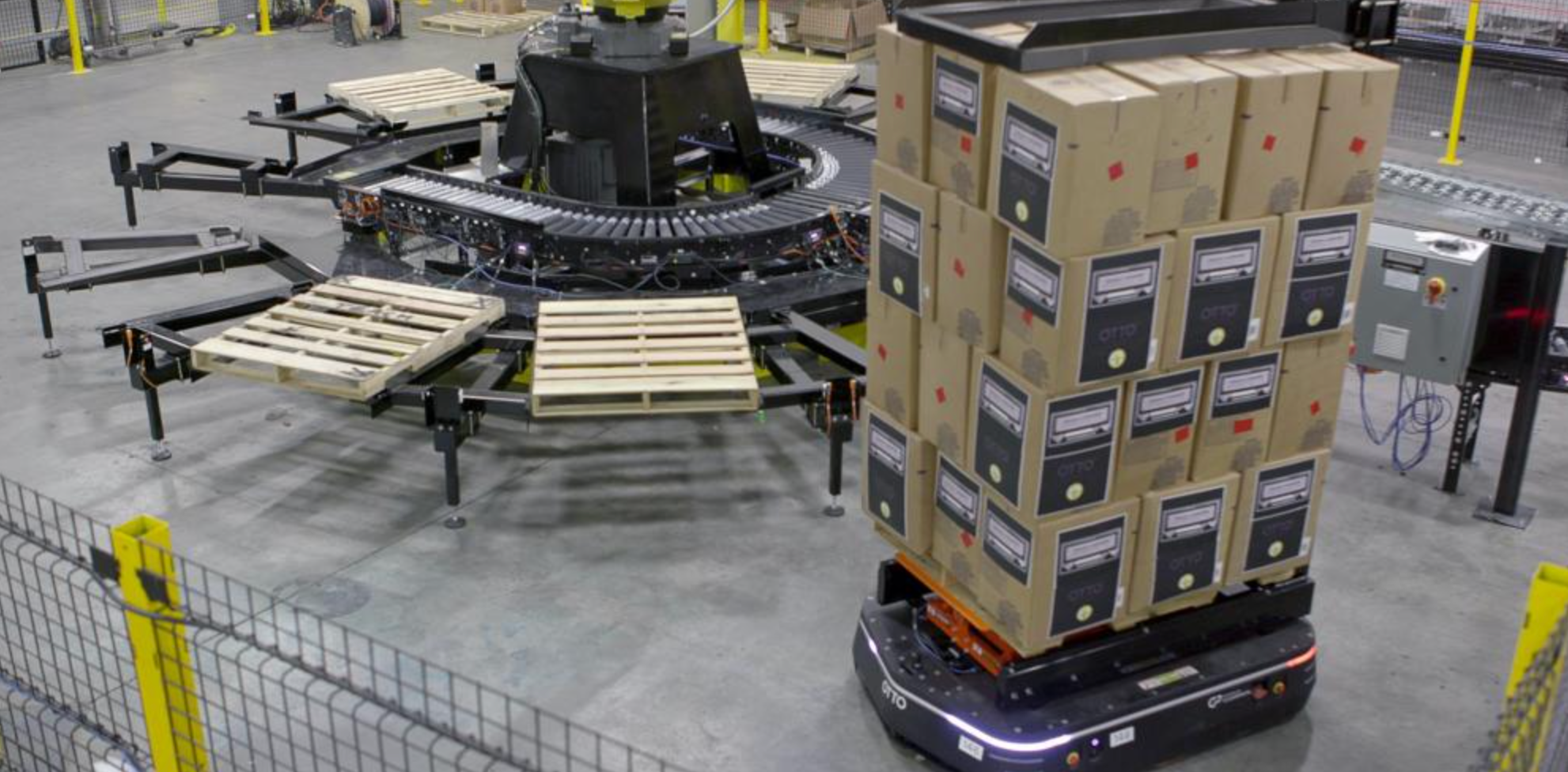
Manufacturers often struggle to find ways to improve their supply chain. Labour displacement, hiring challenges, and an increased need for safety all negatively impact productivity. However, investment in autonomous robots are on the rise — a report by ABI Research estimated that more than 50,000 robots will be working in warehouses by 2023, up from 4,000 in 2018. Gartner stated the autonomous mobile robots (AMRs) are "at peak" in its most recent report, Hype Cycle for Supply Chain Execution Technologies. Gartner also projected that "AMRs will continue to gain traction in complex distribution centers."
It's been proven that material handling automation improves productivity, minimizes risks, and attracts workers to companies, benefiting supply chain and the bottom line.
A boost in supply chain productivity
In addition to the direct labor savings and increased productivity, there are indirect savings that only autonomous materials handling provide, such as no lost time due to routine breaks, vacation time, training, and cost of insurance and workers’ compensation. Autonomous robots allow for work to be done consistently around the clock, with no need to break from the repetition.
As pointed out by a 2017 Deloitte report on using autonomous robots to drive supply chain innovation, this means you can run them “around the clock with more consistent levels of quality and productivity.” Most AMR technologies only require one hour of charge for six hours of continuous work but are capable of operating for 8 hours, equaling to an entire shift without any breaks.
Another advantage is that autonomous robots are quick to train for new tasks, so it’s easy to implement more into the fleet when seasonal demands require it (and more comfortable than hiring, and subsequently firing, a bunch of human workers). Companies, like UPS, rely on automation to improve operations and meet labor demands during the holiday season. The UPS facility in Sandy Springs delivered more than 800 million packages during the busy holiday period, an increase from 762 million in the same period last year. Their second-largest ground hub, located in Atlanta, implemented various automated technologies to help fulfill their orders and are now able to process over 100,000 packages an hour or about 1,700 packages a minute.
UPS opened five new technology-enabled superhubs that have a 25% - 35% higher efficiency, the company previously said. An additional 18 automated hubs will open in 2019 — you can watch their process here.
Adding technology and automated capacity is absolutely the right approach for the future of our more efficient and flexible network.
Jim Barber
Chief Operating Officer, UPS
Safer for human workers
Robots can perform the same fine-tuned material handling task thousands of times without incurring any injury. Introducing robots to the supply chain is, therefore, a great way to reduce the risk to human workers of repetitive strain injuries and injuries caused by lifting heavy weights.
In an ABB case study, a Danish fish factory implemented automation in their packaging process because they "wanted to get rid of heavy, monotonous, repetitious work." They stated that their employees now enjoy a better working environment that is free from heavy lifting that could cause injury. Not only is their process safer after implementing automation but more efficient with a boost in production capacity by 60–70%.
OTTO Motors also helped improve the safety at HIROTEC America by automating their black oxide process. One of the most inefficient processes in spare parts production is the black oxide process, which involves moving parts repetitively from bucket to bucket in a sequence with delays in between while the parts become oxidized. With this process now fully automated, their employees can focus on safer and higher valued-added tasks.
See how OTTO reduced risk to HIROTEC America workers, in this webinar.
Improves corporate brand & attracts employment
With robots assuming the dull, dirty, and dangerous jobs, humans are free to focus on collaborative and strategic efforts that cannot be automated. Removing these mundane and dull tasks removes frustration from employees and results in higher employee satisfaction and engagement.
Automation offers the potential secondary (intangible) benefit of boosting your corporate brand by signalling leading-edge practices and implementation of innovative technology.
Deloitte
A recent survey from Smartsheet found that workers were excited to see automation introduced in the workplace because it allowed them to focus on work that was rewarding and challenging. Interestingly, two-thirds of those surveyed didn't view automation as a threat to their job but rather, thought it would improve it, as a result. CIO also covered the topic and concluded that "introducing automation tools demonstrates that you value individual contributions, and that you want to create more time for workers to make meaningful contributions."
According to MIT Sloan and Deloitte, companies in the early stages of digital maturity are in an chicken-and-egg situation "where they have a tremendous need for digital talent, yet their hesitancy to embrace a digital culture makes them less attractive to such talent." While it is true that some jobs will be at risk due to technology, the goal of automation is to allow employees to work on valuable activities and solve complex problems.
Subscribe to our newsletter
Stay in the loop on product news, case studies, upcoming events and more.