Blog
Bridging the gap between AMRs and AGVs to deliver predictability and flexibility
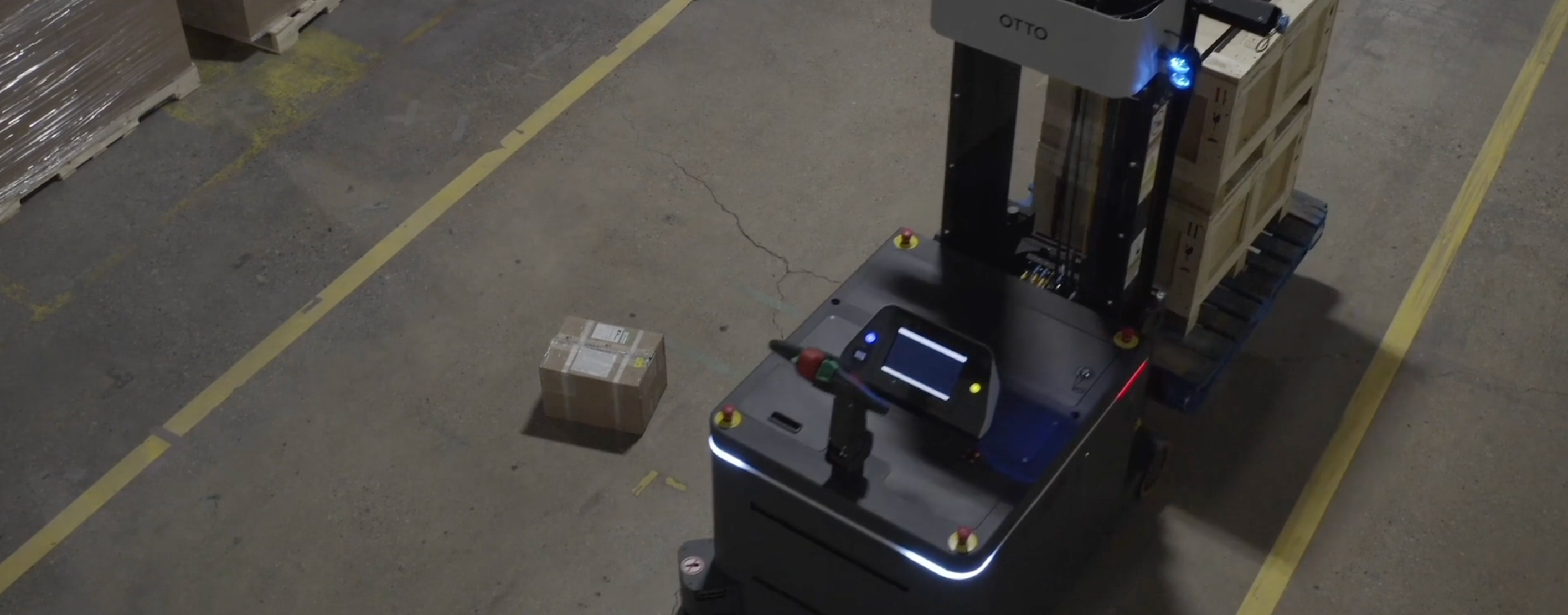
On December 15th, managers from across North America joined us for a live webinar to discuss how manufacturers can unlock the productivity of both AGVs and AMRs. Dave Northup, our Director of Product Management, explored new trends that have helped manufacturers experience the benefits of both technologies, without the tradeoffs.
Credit: OTTO Lifter product video; OTTO Motors. AGV video; ek robotics
Worldwide, the terms “Automated Guided Vehicle” (AGV) and “Autonomous Mobile Robot” (AMR) are frequently used interchangeably but they are, in fact, inherently different both in technology and application. However, these two technologies can come together to deliver the benefits of both.
What is an AGV?
An AGV is a computer-controlled machine that can perform a set of defined tasks by following specific instructions with minimal or no human intervention. The technology, which was introduced to the industry in the early 1950s, relies on guidance devices such as magnetic tape, beacons, barcodes or predefined laser paths that the AGV localizes against to travel on fixed routes.
There is no concept of local replanning or global replanning; the vehicle just follows the path that it was instructed to take.
David Northup
Director of Product Management, OTTO by Rockwell Automation
Lasers and sensors detect obstacles in the AGVs path and trigger the vehicle to safely stop immediately and automatically. However, when the AGV does stop, it cannot continue moving until the obstacle is removed through human intervention, sometimes resulting in a loss in productivity.
While AGVs offer repeatability and predictability, which are often desired traits in a highly controlled environment with predictable workflows, they can be limiting. When facilities need to change an AGV’s route, infrastructure modifications are often required. Thus, facilities that use AGVs are locked into one particular workflow that cannot be changed without expensive investments.
What is an AMR?
The AMR was introduced to the industry about 15 years ago and is often considered an advancement of an AGV due to its enhanced flexibility. AMRs utilize laser-based perception and navigation algorithms to dynamically move through facilities, infrastructure free. AMRs make use of existing infrastructure in a facility as points of reference for mapping their localization and path planning. Sensors built into the AMR are all that it needs.
If you are an experienced operator, you can come in and take an OTTO AMR, deploy it in your facility where it has never been before, and get a map made and a workflow going in 5 to 10 minutes.
David Northup
Director of Product Management, OTTO by Rockwell Automation
AMRs have the intelligence to safely adapt and modify their behavior when faced with new or unexpected situations. Machine learning capabilities enable the robot to become more efficient and learn as they encounter new situations. When an AMR encounters a blockage the robot reroutes autonomously and safely around the obstacle without human intervention, unlike an AGV. This ensures more throughput and less disruptions to your workflow.
Additionally, while an AGV chooses from a set of preconfigured options for path planning, AMRs generate their own path, assessing and calculating options instantaneously based on a map of the facility, traffic management rules in effect and its current position. The robot decides how to get where it needs to go most efficiently and safely.
It knows where it is, it knows where it has to go; it decides how to get there on its own.
David Northup
Director of Product Management, OTTO by Rockwell Automation
Since workflows can be changed at a moment’s notice, AMRs are needed for high-mix, dynamic manufacturing where flexibility and adaptability are essential.
Bridging the gap between flexibility and predictability
Both AGVs and AMRs bring their own benefits to different applications. AGVs bring predictability and repeatability to dense environments with highly controlled workflows, while AMRs bring adaptability and flexibility to dynamic environments with evolving workflows.
In the webinar, Dave Northup compared an AGV to a train on a set of tracks. The train can only go where the physical infrastructure allows, and cannot continue if an obstacle blocks its track. Conversely, AMRs are like an ATV. They have free navigation with the ability to drive wherever they want, and can simply navigate around any obstacle in their path.

AMRs typically use a search-based path planning algorithm, where the robot will find the most efficient path to its destination, sometimes causing a lack of predictability as it is difficult to understand where exactly the AMR will be and when.
Instead, OTTO Motors provides the option to use a graph-based path planning algorithm, where particular lanes and nodes are introduced that instruct the AMR to follow the provided route to the destination unless an obstacle blocks the path. If there is a blockage, the AMR will resort back to a search-based algorithm and will find an alternative path to the destination.
This ensures that your vehicles are behaving in a more human-like driving capacity where you have explicit intersection management and more prescriptive behaviors for the robots to follow. [This allows you to] gain more of that predictability that you’re looking for while retaining the flexibility that you need in your facility.
David Northup
Director of Product Management, OTTO by Rockwell Automation
David Northup described this balanced type of AMR as similar to a truck. The truck will drive on the road, following particular paths, but it can deviate from the path when there is a blockage, such as a road closure.
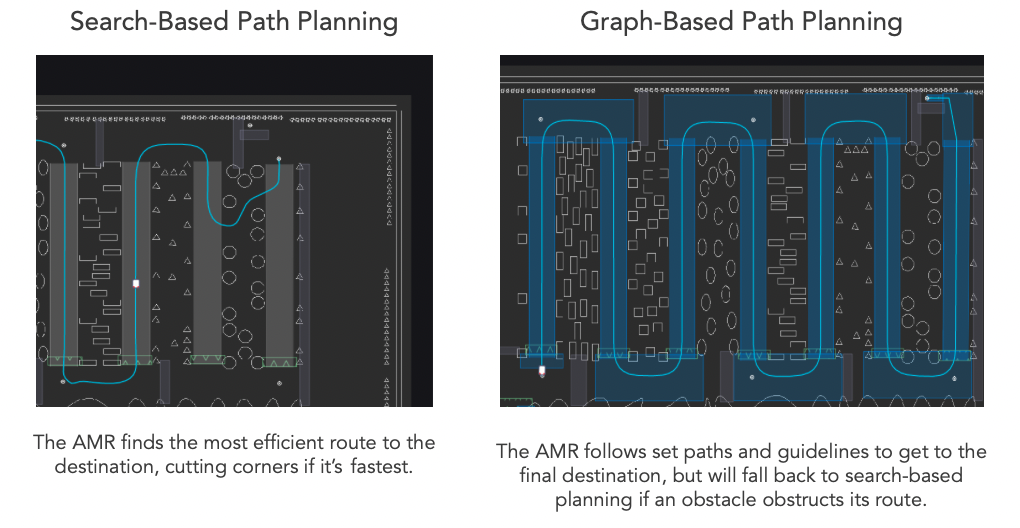
There might be special cases where an AMR must follow a guided path like an AGV does for a short distance. In certain docking scenarios and spaces where millimeter level precision in narrow aisles is needed, an AMR can attach itself to an AGV guide like magnetic tape to navigate the tight space. Once through the narrow aisle or after the tight docking maneuver, the AMR disconnects from the magnetic tape and resumes navigating on its own.
When an AMR utilizes graph-based path planning, manufacturing facilities experience the benefits of both traditional AGVs and AMRs, without sacrificing the safety that both technologies emphasize. It is truly the best of both worlds: operations experience the predictability and repeatability of an AGV with route planning rules, and the flexibility and adaptability that comes with an AMR.
The combination of these innovative technologies in your manufacturing facility helps your workflow become Industry 4.0 ready. This informative webinar will help you understand the value of both technologies both independently and as a collaborative algorithm.