Blog
LEAN manufacturing: Eliminating the transportation muda
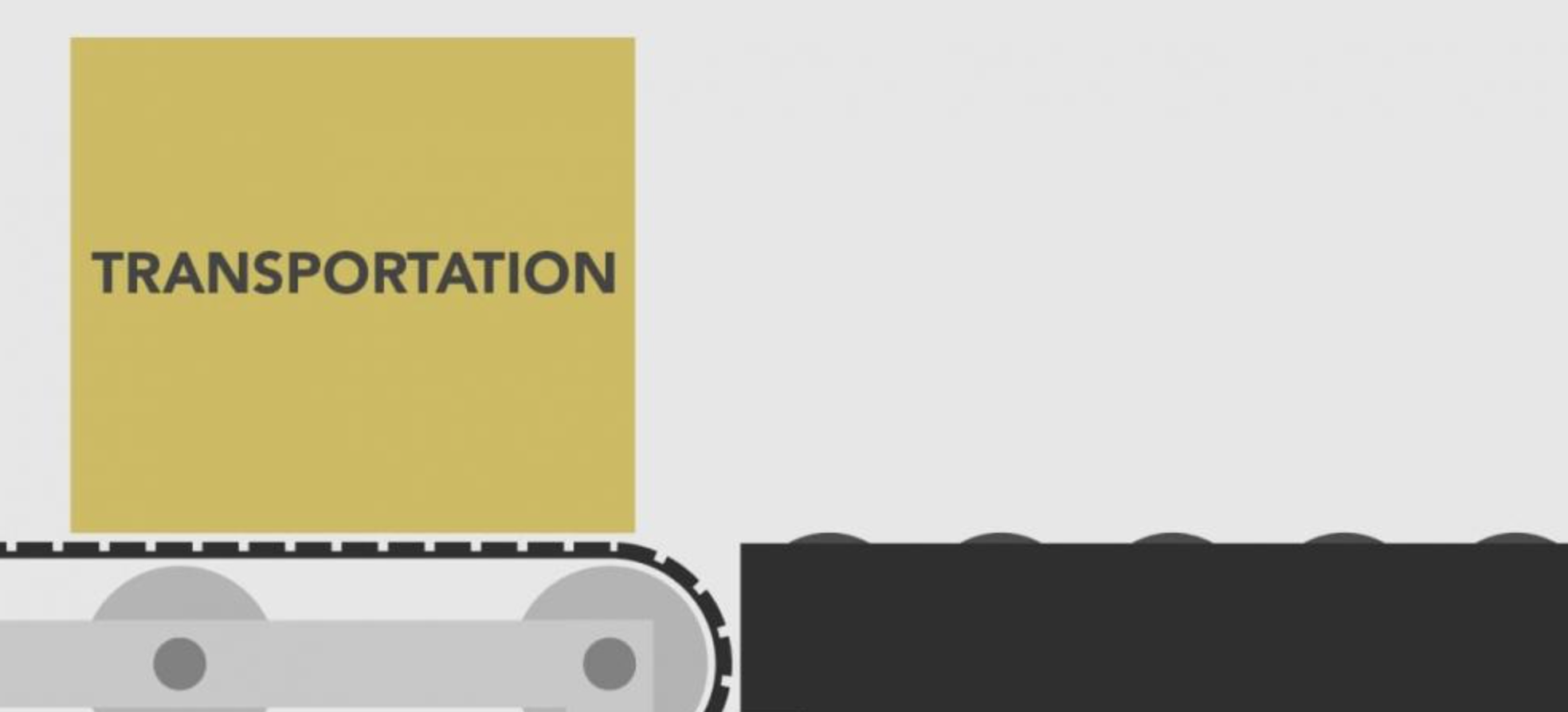
Manufacturing is broken and the transport of materials is responsible. There are of course other problems within manufacturing, but they often start with transport of material. Transportation is one of the mudas (wastes) in lean manufacturing and can raise its ugly head in many situations. Moving in-process parts from one manufacturing facility to another is an example of transportation muda, as is supplying too many raw materials to the line and returning unused materials to storage. This waste of transportation is an impediment to achieving a lean manufacturing operation.
Let’s focus on transportation muda on the assembly line. Transportation often becomes waste in a traditional assembly line. The assembly line may work adequately if a company manufactures one product with no variations (think Henry Ford’s quote, “Any customer can have a car painted any colour that he wants, so long as it is black.” However, many companies produce multiple models of products and do so on the same line. This translates into shorter runs and requires more materials in smaller quantities.
Adding to the pain of the transportation muda
Shorter runs with more materials in smaller quantities are a great nuisance for plant managers who are committed to lean. Why? The standard practice of delivering pallet loads of materials creates excess inventory on the line when only one-third of that amount is needed. Materials not used get in the way. As a result, the unused materials go back to inventory. You can see how this translates into a lot of waste when multiplied by the number of product models assembled on the line. Chalk up another victory for transportation muda.
Several attempts to eliminate this waste have gone nowhere. Some companies have changed the delivery of pallet loads from forklift to carts and tuggers. This may initially appear to resolve the issue, but it does not. The labor costs associated with workers delivering materials to the assembly line continue to increase, threatening competitive advantages. Others turn to “high tech” solutions such as using Autonomous Guided Vehicles (AGVs).
AGVs can’t get there from here
The AGV eliminates the need for dedicated material delivery workers; materials are loaded onto the AGV and it dutifully heads for the assembly line ...but it never quite gets there. Consider this scenario to understand why: suppose you had a meeting at a hotel in downtown Chicago. Your flight arrives at O’Hare and you decide to live like a local take the “L” (Chicago’s elevated train system).
There’s a station at O’Hare for the “L” and you get on only to learn that if you want to get to the hotel, you need to walk and transfer to a different train line. Then after getting that train, you learn you still need to walk several blocks because the train doesn’t take you directly to the hotel. To make matters worse, it’s raining and the train is delayed for several hours because of an issue further down the track.
This is what happens with AGVs. The equipment does eliminate the costs of workers delivering materials. However, because AGVs follow a fixed path (using a magnetic strip on the floor or a route programmed into its memory), materials come close but not delivered exactly where required. Furthermore, delays will occur if something is blocking the AGV path.
The cure for transportation muda
You still have transportation muda issues, and the AGV appeared to be the best option until now. Enter the autonomous mobile robot (AMR). As its name implies, the AMR operates much like a person. This material handling solution operates unencumbered using mapping technology that allows it the ability to deliver materials directly to the work cell without the need to follow a designated path or infrastructure. This is how AMRs work. So, using our Chicago example:
The flight lands at O’Hare and you still need to attend a meeting at the hotel in downtown Chicago. Knowing the “L” will not drop you at the hotel door, you use the Uber. The Uber picks you up at my terminal and takes the expressway towards downtown. An accident ahead has the potential to delay you, but the driver knows another way and goes around the traffic, dropping you at the front door of the hotel, on time. That’s what an AMR does. It delivers exactly what is needed on the line, AND when it’s needed. Its internal mapping technology finds alternative routes in real-time in the event of blockage.
AMRs deliver a viable alternative to transportation muda while delivering impressive ROI. Learn more about AMRs and their impacts on Industry 4.0.