Blog
AMA: How do AMR vendors estimate fleet size for ROI?
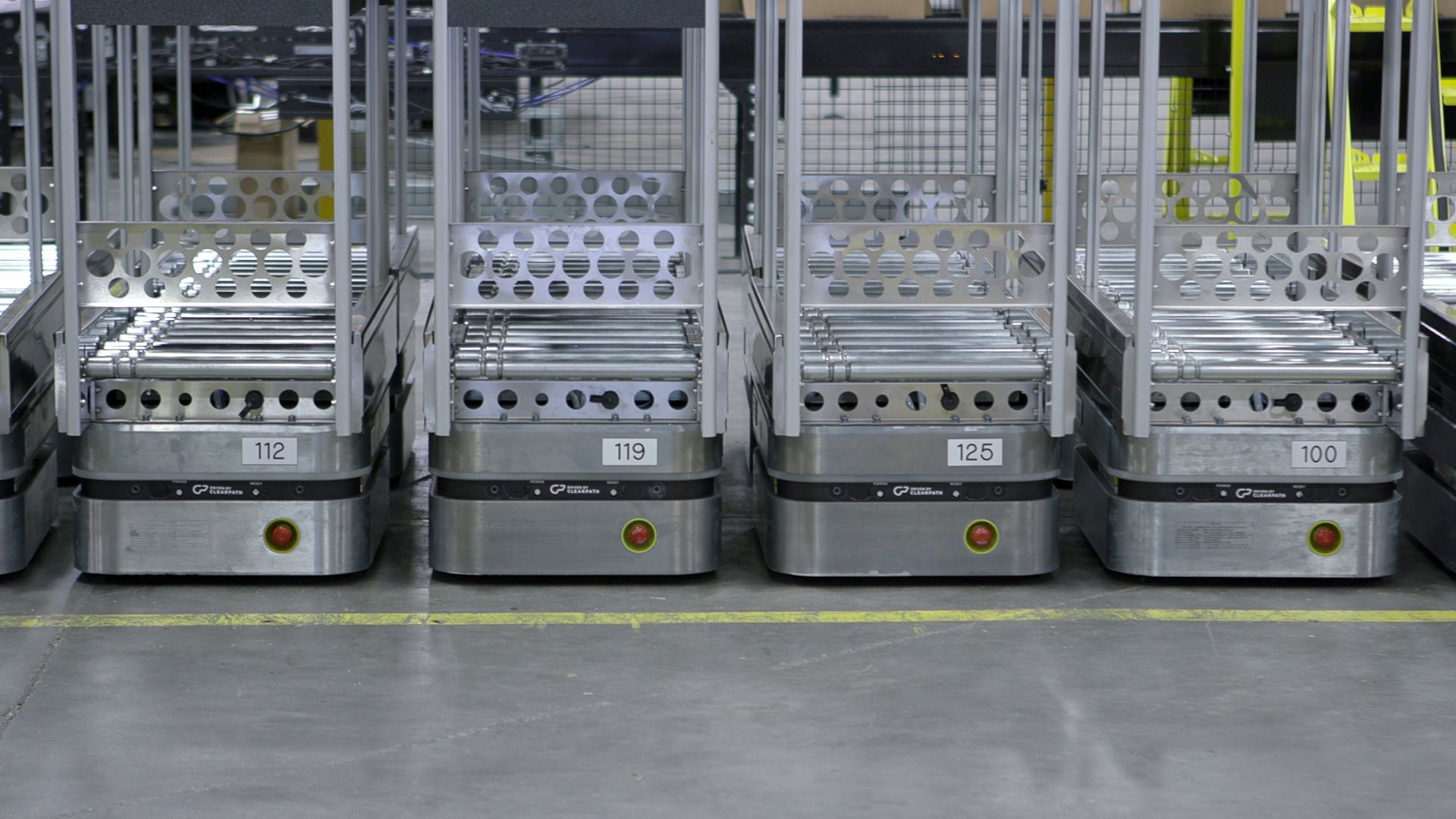
One of the most crucial steps in building a business case for autonomous mobile robots (AMRs) is generating an estimated ROI timeframe with your vendor. When calculating ROI, manufacturers compare the total cost of the new solution with the costs of the existing solution.
To estimate fleet size effectively, your vendor may make a few key assumptions, such as:
- Average speed
- Time needed for docking at endpoints
- Driving distance
- Charging times
- Evenly distributed throughput
- Rules of the road
- Efficiency factor
1. Average speed
Your vendor will determine the estimated average speed that AMRs will be able to drive in your facility, based on previously discussed considerations, such as aisle widths, payload stability, and expected traffic. For example, if your facility has narrow aisles or frequent congestion, the average speed will decrease, impacting how many AMRs you need to maintain throughput.
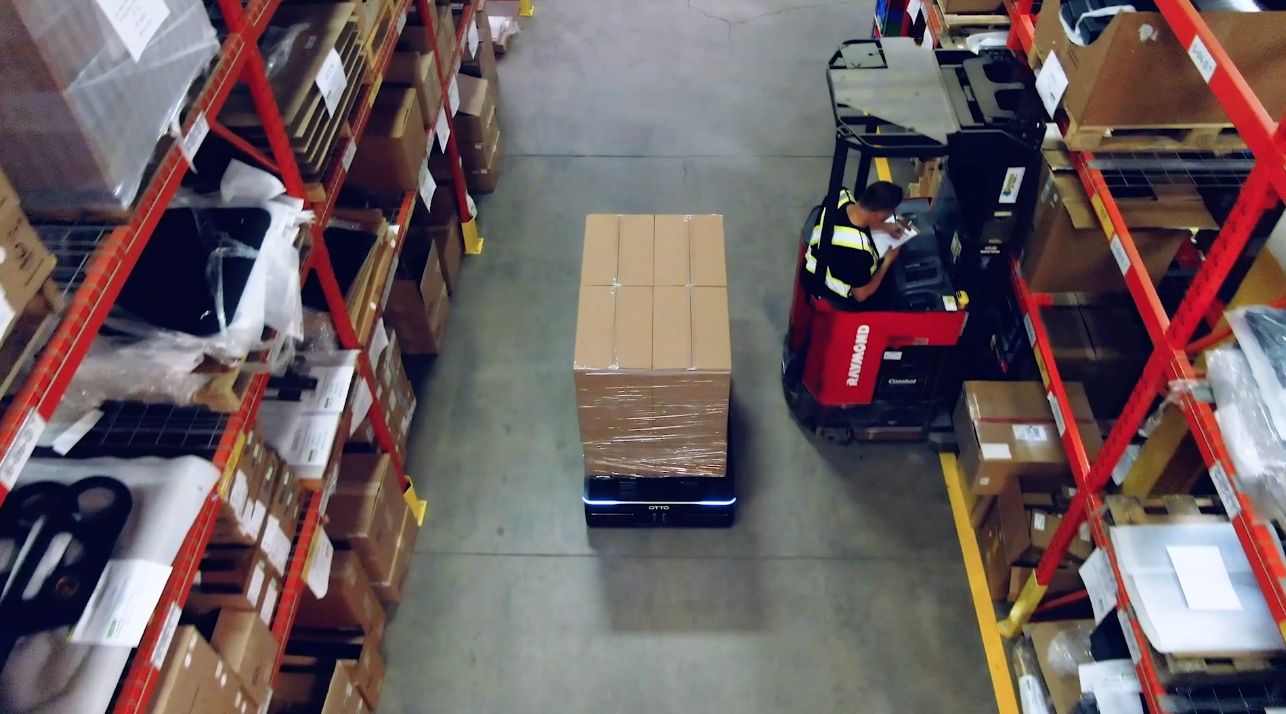
Video 1: OTTO 1200 is built to drive quickly and safely in narrow aisles, ensuring maximum throughput even in the most space-constrained facilities.
2. Time needed for docking at endpoints
Every AMR vendor will know how long it takes for their AMRs to enter the payload drop-off zone, dock to it, transfer the payload, and back out. The type of attachment (conveyor, cart, or lift), the approach angle, and the nearby traffic, as a few examples, can alter these times.
3. Driving distance
Your vendor will likely request a CAD drawing of your facility, and together, you’ll discuss where AMR endpoints, parking, and charging stations will be. Based on this, the vendor will calculate how far each AMR needs to travel. Longer distances will increase the time spent per task, which can impact the fleet size.
4. Charging times
Most AMRs will require some downtime to recharge—whether autonomously or manually—and this must be factored into the fleet size estimate. Vendors will allocate time for charging based on the AMRs' battery life and how many jobs it needs to complete to reach throughput targets.
5. Evenly distributed throughput
Vendors typically assume that your throughput is consistent across each hour of the day when calculating fleet size. If your facility experiences peak periods, inform your vendor so they can adjust the estimate accordingly.
6. Rules of the road
Your vendor may assume that their AMRs will be given the right of way at intersections, can operate bi-directionally, and that any and all doorways are open. If there are any restrictions—like waiting for clearance at intersections or doorways—this will impact throughput and potentially fleet size. Let the vendor know so they can add these assumptions to their fleet estimate.
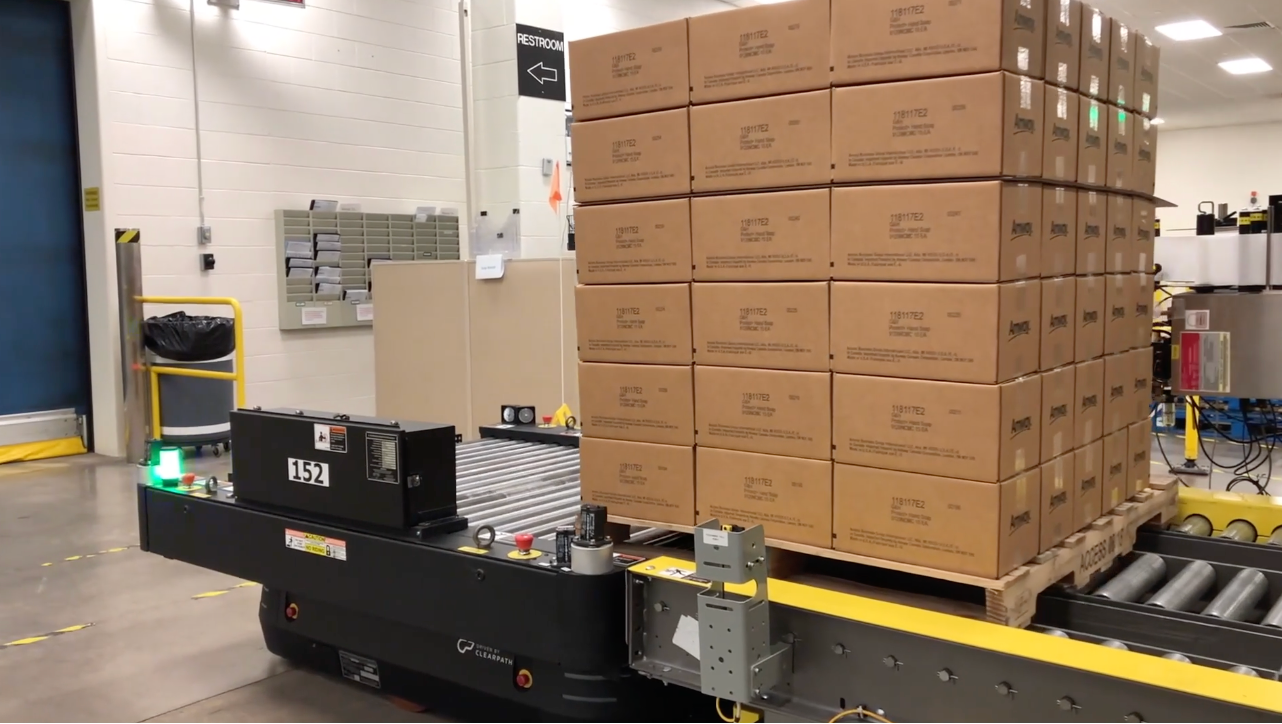
Video 2: Amway has automated the staging to dock loading application in their facility. OTTO 1500 delivers a pallet of finished goods from the production line to the shrink wrap, and then to shipping, integrated with door control for seamless transport.
7. Efficiency factor
Most vendors will also factor in an efficiency margin (such as 10%) to account for time when the AMRs are not actively working.
To learn more about calculating ROI timeframes for an AMR deployment, and about the entire buying journey, download the full eBook, “The manufacturer’s playbook for AMR selection: A 5-stage guide.”
To have more of your top autonomous material handling questions answered, register for our upcoming webinar, “I’m a product manager for an award-winning AMR solution, ask me anything.” On April 23rd at 1pm ET, Adrian Ennis will be hosting a live AMA session to provide you with tailored insights that will help inform your decisions throughout the AMR selection process.
Subscribe to our newsletter
Stay in the loop on product news, case studies, upcoming events and more.