Blog
AMA: How do I budget for AMRs?
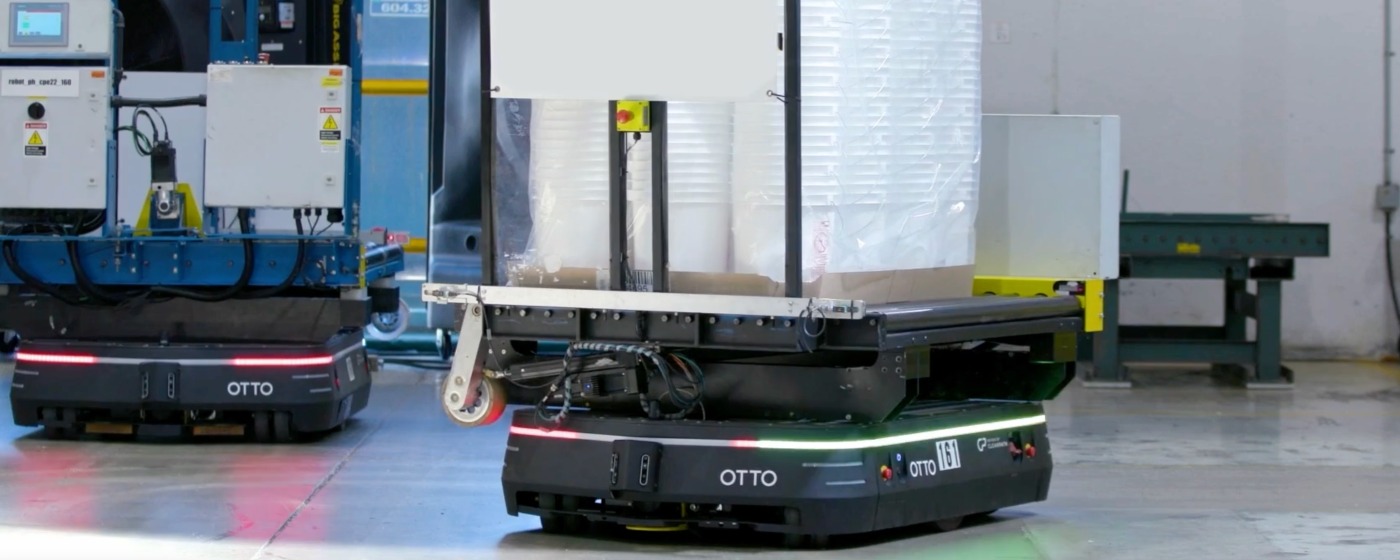
In this blog series, manufacturing facilities and warehouses ask their top industry and product questions, and OTTO’s material flow experts answer them.
Autonomous mobile robots (AMRs) are deployed in manufacturing facilities worldwide to improve material handling safety, increase efficiency and reallocate labor to more value-added tasks. Manufacturers establish key performance indicators (KPIs) to address these goals, such as reducing forklift incidents, optimizing cycle times, and reducing overtime by reallocating available labor to more rewarding work.
Manufacturers are turning to AMR solutions as they strategize how they can meet these critical KPIs next year. However, gaining executive approval requires a clear understanding of how to budget for this innovative technology. As you prepare next year’s budget, now is the ideal time to evaluate AMR solutions and their associated costs.
How do I budget for AMRs?
AMRs are an investment to help you meet your critical KPIs. The autonomous material handling solution has many factors which play into its final cost, including:
- Number of AMRs
- Cost of software
- Cost of attachments necessary for the workflow to succeed
- Cost of deploying the solution
- System integration costs
- Cost of needed chargers
- Training costs
- Post-implementation service and support costs
When budgeting for AMRs, the first step is to consider how many AMRs you will need.
The cost of your project will depend on how you plan to use the robots and the throughput that is required to meet your production goals. When consulting with an AMR vendor for a project quote, they will request details about your desired workflows to recommend which AMRs and attachments are needed, as well as the optimal number of AMRs for a turnkey solution.
Budgeting for AMRs involves more than just considering the cost of the robots and their accessories. The top priority is meeting your throughput requirements, which is accomplished by integrating the robots, their attachment, and their chargers, all coordinated through an advanced software solution that minimizes the need for additional hardware.
There are four considerations to determine the number of AMRs you need for your project:
- Payload specifications: What is the weight of the payload? What are its dimensions?
- Number of required jobs per hour: How many missions must be completed per hour to meet your throughput goals?
- Mission distance: How many feet/metres would the AMR need to travel between your starting point and each of the points of interest, or endpoints, within your facility?
- Facility layout: How is your facility designed? Where are the aisles and how wide are they?
Your shortlisted vendors will be happy to walk you through where and how to find this information.
Manufacturers need to consider the cost of not automating, or more simply, the ROI of a potential project.To determine your potential payback period, consider:
- The number of material transport personnel you have working at your facility per shift
- The full cost to employ the material transport personnel, including wages, taxes, benefits, supplies, and other expenses, also known as the total burden rate or cost.
- The number of hours per shift and shifts per week
- Your operating days per week and weeks per year
With this information, you can begin to understand your payback period and your Internal Rate of Return. Based on your facility’s specific situation, AMRs may completely transform not only your efficiency, safety, and labor force, but your cost of material handling as well. To evaluate your ROI based on the considerations above, use OTTO’s ROI Calculator.
Deploying AMRs will elevate your material handling, saving you substantial costs and resources which can be better used in more value-added areas of your facility. As we approach the end of the year, now is the time to consider budgeting for the innovative technology next year. Use OTTO’s ROI Calculator to get an estimate of your projected payback period, and reach out to OTTO’s team to understand how many AMRs you need and what costs are associated with your specific solution.
Written by Wes, Business Development Manager at OTTO by Rockwell Automation.
If you’d like to submit a question for our material flow experts to answer, please fill out the form below.
Ask a question
Subscribe to our newsletter
Stay in the loop on product news, case studies, upcoming events and more.