Blog
AMA: What is the difference between the 5 AMRs in OTTO’s material handling solution?

In this blog series, manufacturing facilities and warehouses ask their top industry and product questions, and OTTO’s material flow experts answer them.
Manufacturers worldwide use autonomous mobile robots (AMRs) to solve workplace safety challenges, improve efficiency, and elevate employees into more fulfilling roles. As they assess which AMR vendor has the best solution to their material handling challenges, manufacturers are also looking to determine which AMR model is most suitable for their specific use cases.
At OTTO, we offer the industry’s most comprehensive, award-winning fleet of AMRs, from flatbed to forked, capable of moving up to 4,200 lb (1,900 kg), including:
- OTTO 100
- OTTO 600
- OTTO 1200
- OTTO 1500
- OTTO Lifter
OTTO 100
OTTO 100 is a strong and agile AMR, best suited to move lightweight payloads. Designed to be resilient in the most challenging manufacturing environments, OTTO 100 is resilient enough to withstand forklift collisions and carry on with its tasks.
- 150 kg (330 lb) payload capacity
- 740 x 550 x 308 mm footprint
- 2.0 m/s maximum travel speed
Equipped with an integrated lift, you can pair OTTO 100 with a Staging Cart or conveyor attachment to move boxes, bins, and other lightweight payloads through a wide range of person-to-person workflows, including workcell delivery, lineside delivery and work-in-progress transport.
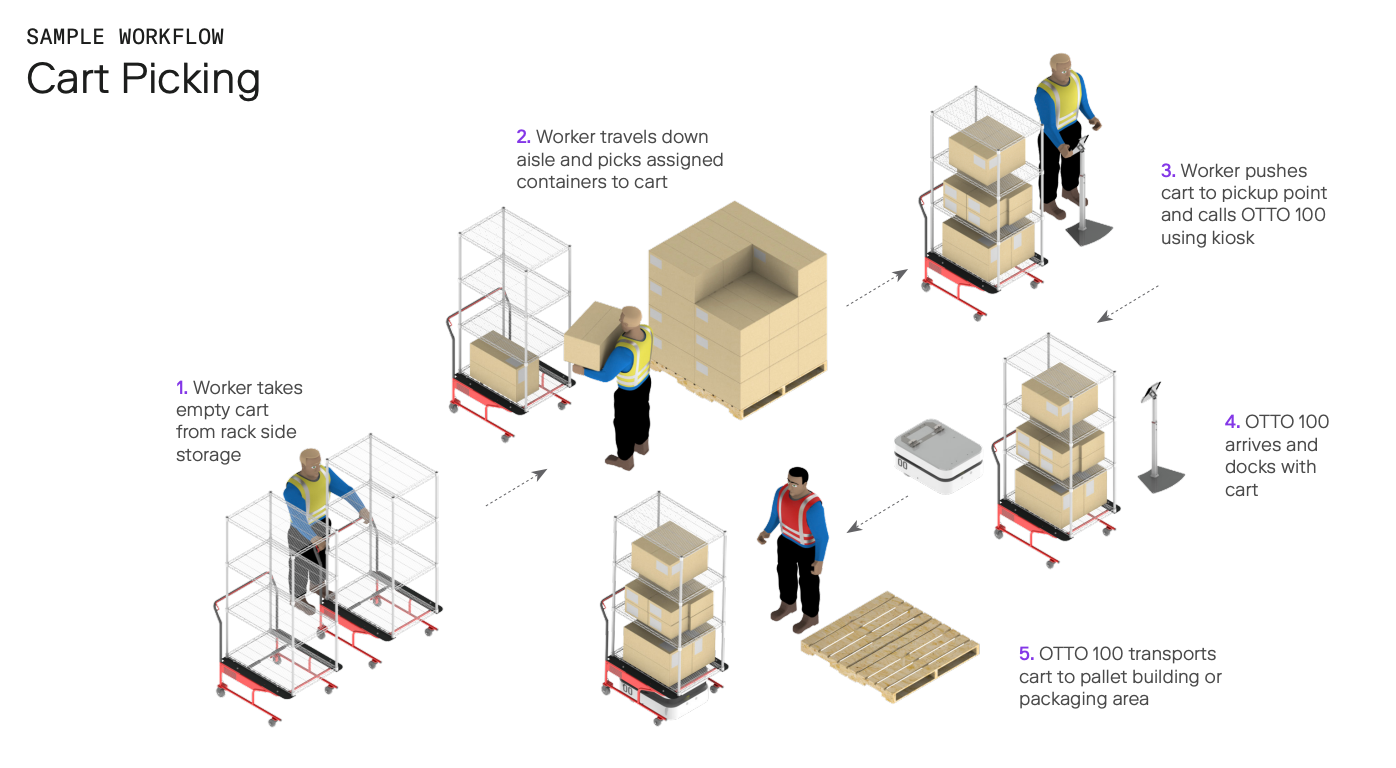
Image 1: A sample workflow for OTTO 100.
OTTO 600
OTTO 600 is a tough and nimble AMR, designed to move mid-sized payloads quickly in space-constrained facilities. With the narrowest footprint in its class, OTTO 600 seamlessly moves materials in high-traffic, tight spaces at industry-leading average speeds. Just as with OTTO 1200, servicing OTTO 600 is simple with rapid-access drawers that enable quick maintenance that can easily be tackled by a single person. OTTO 600 and OTTO 1200 also share the same charging interface to optimize floor space.
- 600 kg (1,322 lb) payload capacity
- 1,050 x 700 x 320 mm footprint
- 30-minute charge time from 10% to 90%
OTTO 600 is capable of automating many workflows, including palletizer to stretch wrapper, lineside delivery, and work-in-progress transport.
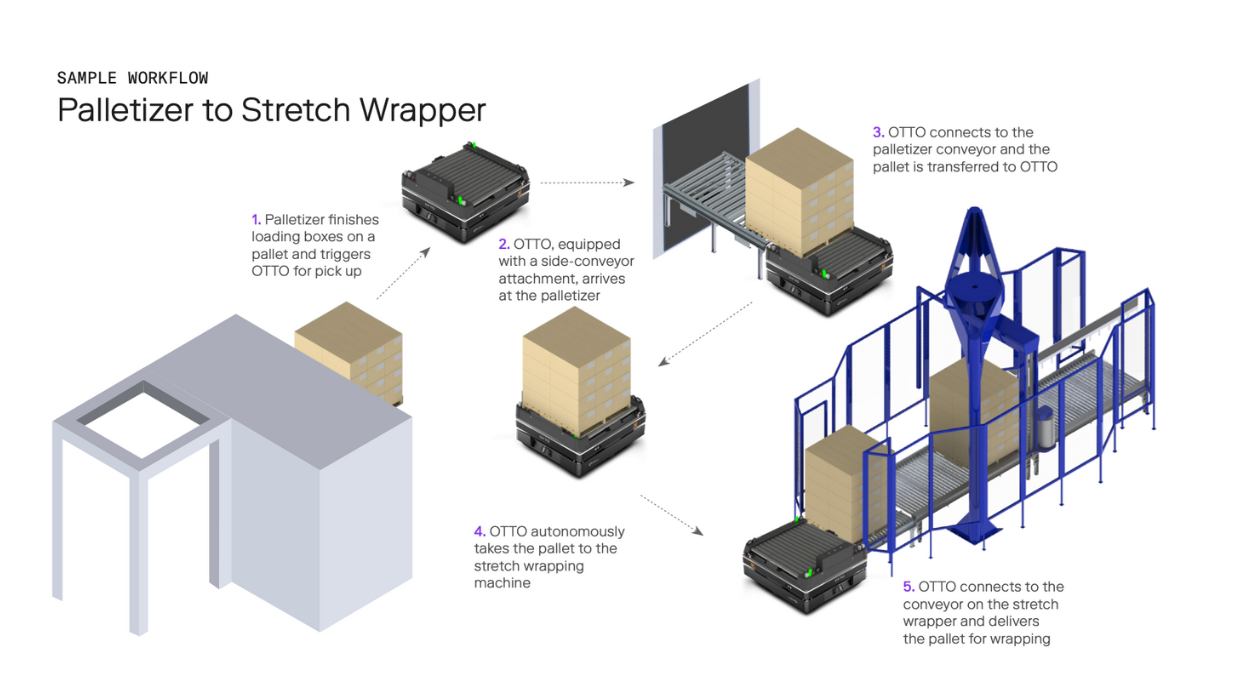
Image 2: A sample workflow for OTTO 600.
OTTO 1200
OTTO 1200 is a heavy-duty AMR, designed to move heavy payloads in tight spaces. With a narrow footprint and the same charging interface as OTTO 600, manufacturers can minimize aisle widths and required charging infrastructure to improve facility floor space utilization. Should you need to, servicing OTTO 1200 is simple with rapid-access drawers that enable quick maintenance that can be tackled by a single person.
- 1,200 kg (2,645 lb) payload capacity
- 1,350 x 910 x 320 mm footprint
- 30-minute charge time from 10% to 90%
OTTO 1200 is built to automate many workflows, including ASRS to lineside, inbound to storage, and finished goods takeaway.
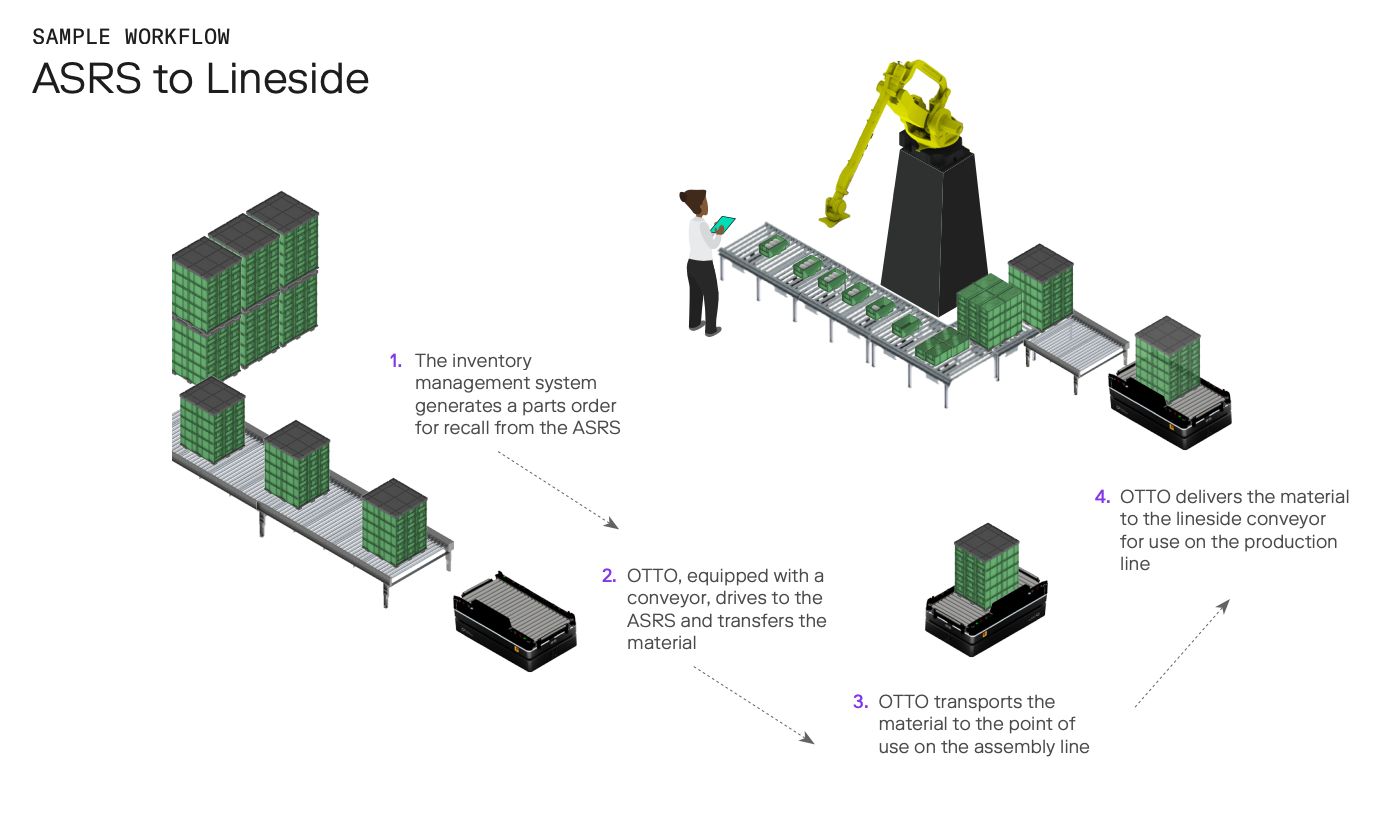
Image 3: A sample workflow for OTTO 1200.
OTTO 1500
OTTO 1500 is a heavy-duty AMR designed to move the heaviest payloads at top speeds, even around turns, to deliver needed maneuverability in the toughest, most dynamic environments. As the highest capacity AMR moving at industry-leading speeds, OTTO 1500 delivers higher ROI by moving materials in fewer and quicker trips, using fewer robots.
- 1,900 kg (4,188 lb) payload capacity
- 2.0 m/s maximum travel speed
- 10-hour runtime from 90% to 10% battery
Equipped with a conveyor or lift attachment, OTTO 1500 is well-suited for a variety of workflows that connect islands of automation, including outbound to storage, palletizer to stretch wrapper, and bulk delivery to lineside.
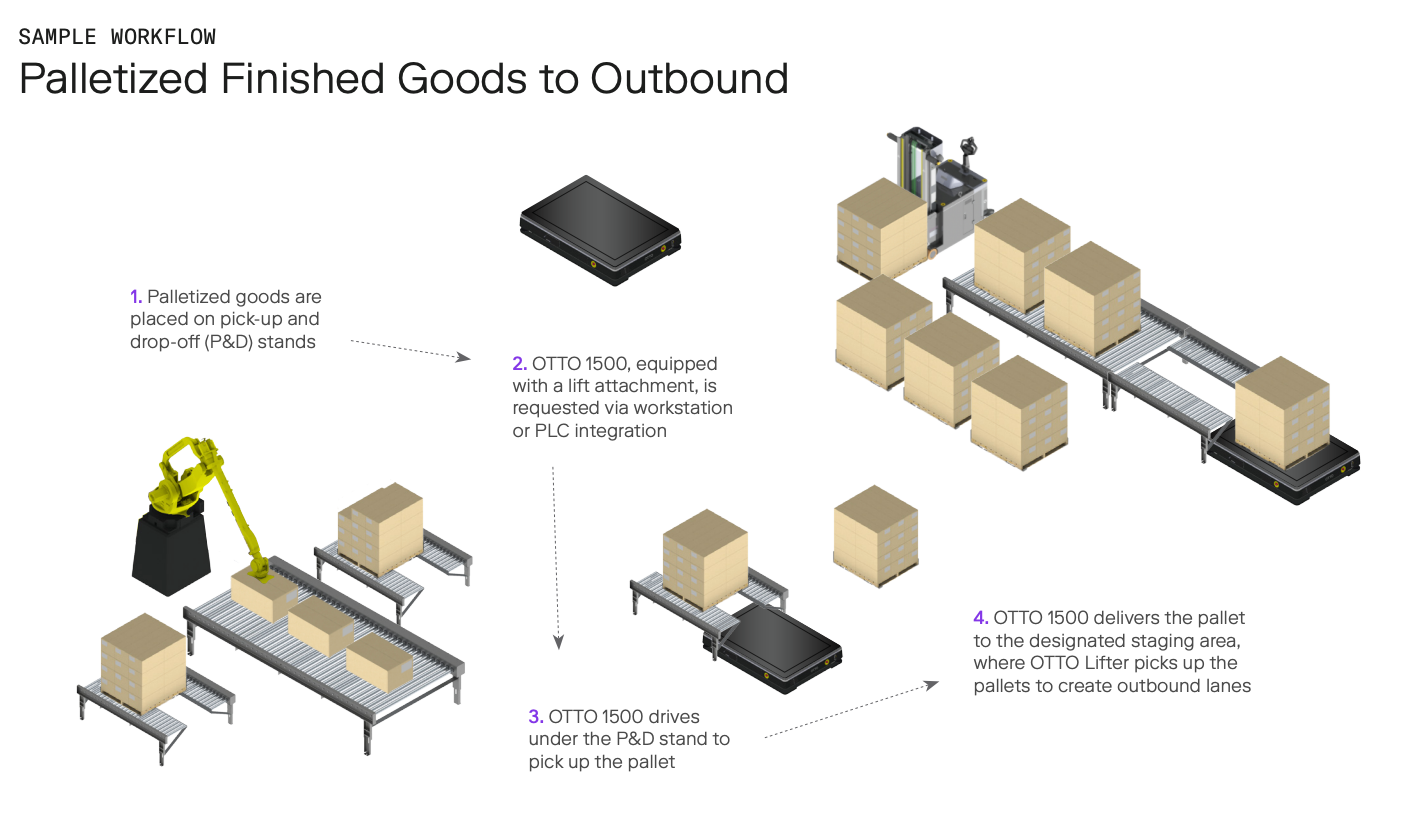
Image 4: A sample workflow for OTTO 1500.
OTTO Lifter
OTTO Lifter is an autonomous forklift designed to help manufacturers move pallets between stands, machines and floor locations. Using specialized sensors to ensure the payload is within limits, OTTO Lifter reliably assesses and picks up pallets autonomously, even when they’re misplaced or wrapped in stretch film. Equipped with a manual tiller to quickly and easily toggle between autonomous and manual mode, OTTO Lifter is built with a user-friendly design.
- 1,200 kg (2,645 lb) payload capacity
- 1 meter autonomous lift height
- Compatible with a variety of pallet types, including Wood and Grade A pallets: CHEP, PECO, Block and/or GMA Orbis HDMC 48-45
Safety-rated technology prevents pallet collisions and keeps pallets stable during quick turns as OTTO Lifter moves materials to and from racks and near the floor. The autonomous forklift is well-suited for many workflows, including palletizer to stretch-wrapper, stretch-wrapper to storage and storage to outbound / inbound to storage.
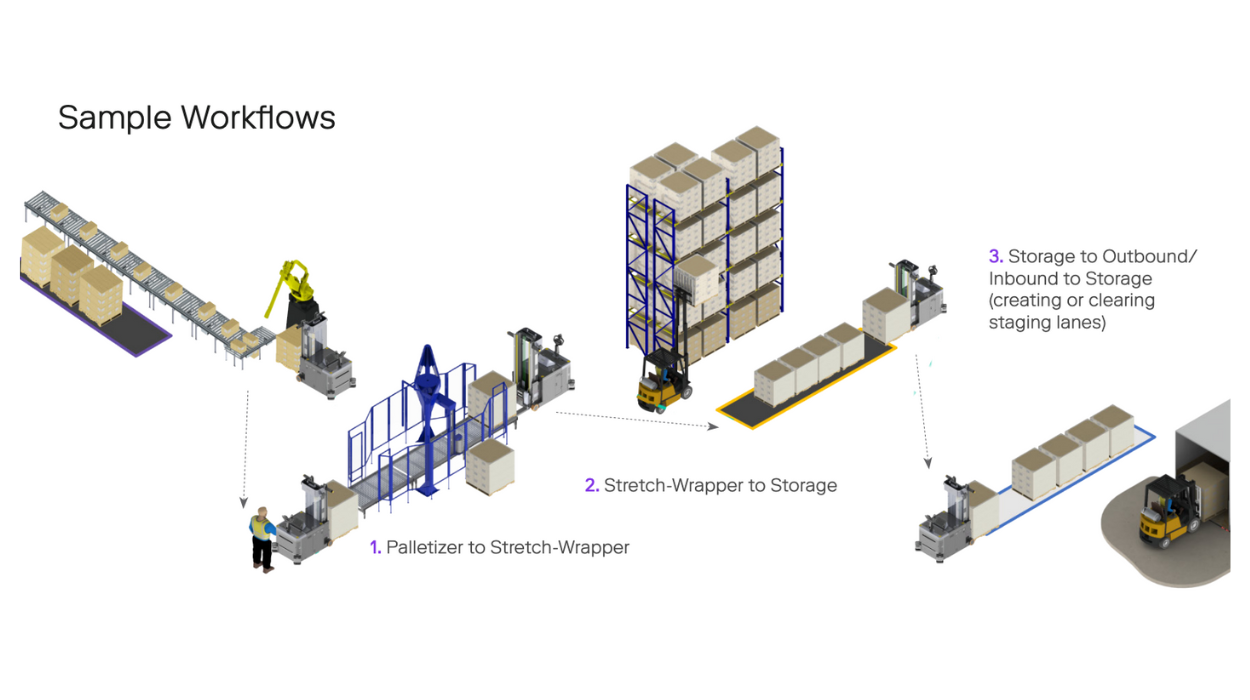
Image 4: A sample workflow for OTTO Lifter.
Each OTTO AMR has unique specifications that align well with different manufacturers’ needs. For example Mauser Packaging Solutions, selected OTTO 1500 to move large, plastic rigid containers from finished goods to the stretch-wrapper to achieve a 6 times increase in throughput.
While the robots themselves can help manufacturers decide between AMR vendors, true differentiation comes from a vendor’s software capabilities. This is what powers your fleet’s performance and delivers productivity at scale. To learn more about OTTO’s fleet management software, watch this webinar.
Written by Jess, Content Marketing Specialist at OTTO by Rockwell Automation.
If you’d like to submit a question for our material flow experts to answer, please fill out the form below.
Ask a question
Subscribe to our newsletter
Stay in the loop on product news, case studies, upcoming events and more.