Blog
Forget what you know about forklifts: NFSD 2022
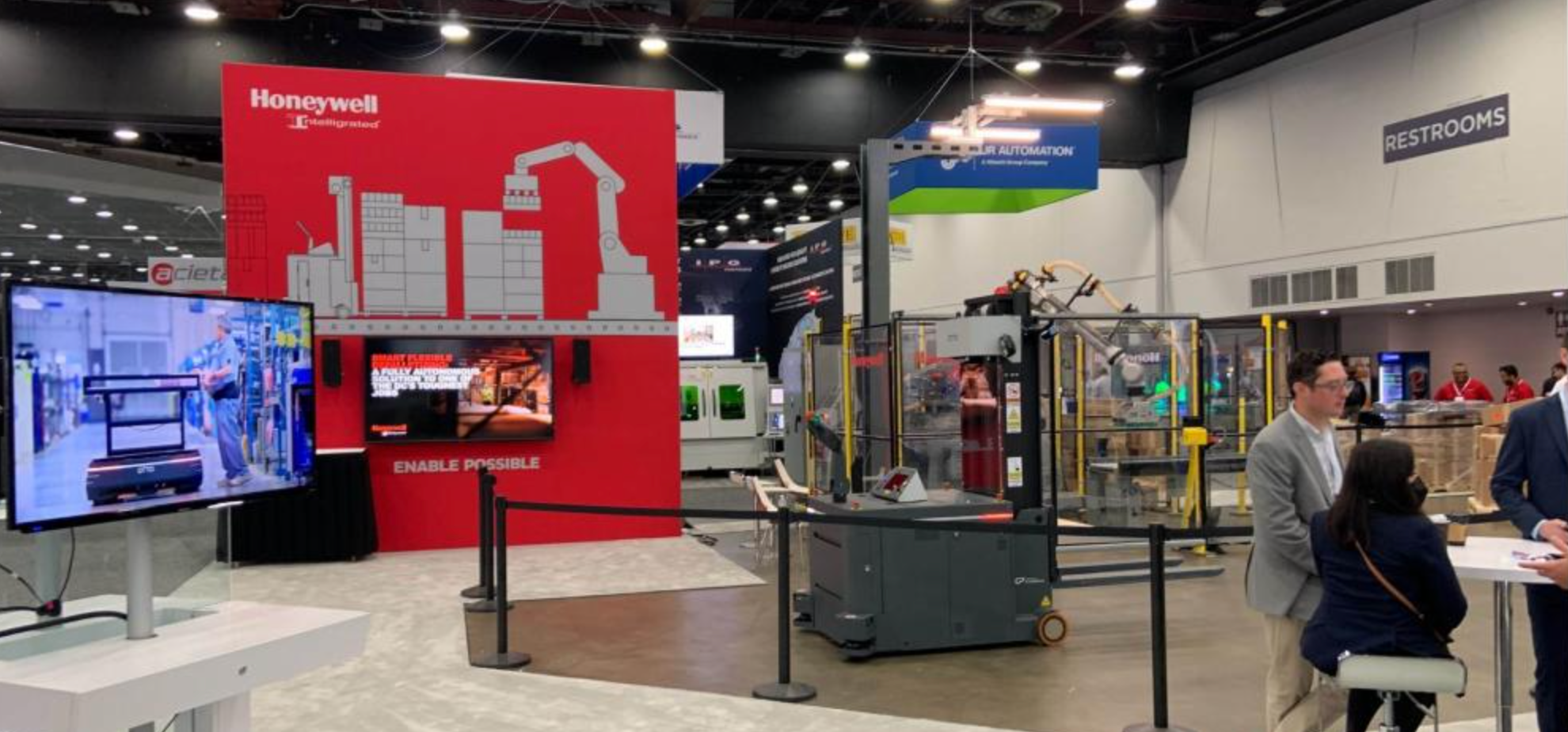
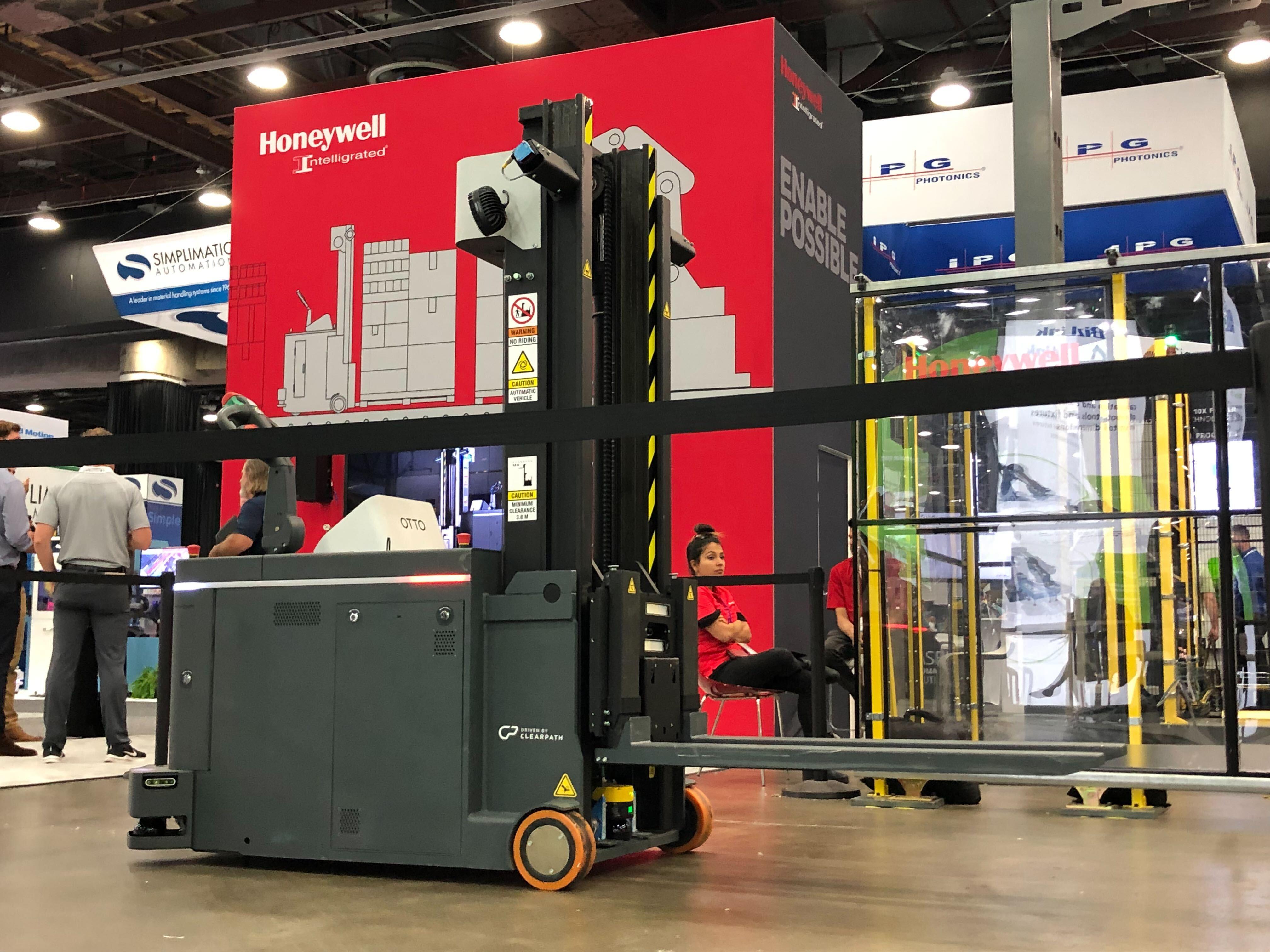
Honeywell Intelligrated hosts OTTO Lifter demo at AUTOMATE 2022.
This blog was originally posted by our partner, Honeywell Intelligrated. See original blog post here.
It goes without saying that forklifts are essential to warehouse operations. From the efficient movement of goods to exceptional lifting and loading capacities, the list of a forklift’s key benefits to a facility’s operations is extensive. However, traditional forklifts continue to cause serious injuries — and even fatalities.
Whether it’s due to the improper use of equipment, unsecured loads or pedestrians gone unseen in operators’ blind spots, forklifts accounted for 8,140 non-fatal injuries in 2019 — a number that’s increasing, according to the U.S. Labor of Statistics — and an average of 87 deaths in the U.S. every year, according to the Occupational Safety and Health Administration (OSHA).
Human error — often due to improper training or a lack of qualified labor to operate machinery — accounts for the most common cause of annual forklift accidents and fatalities. Today, as we amplify the importance of both the safe use of forklifts and proper operator training, it’s time to look to a safer, more productive future of warehouse operations, one with autonomous forklifts.
With autonomous forklifts, the operating and thinking are safely done for you. And with the expert ability to navigate autonomously using smart technology, this solution can handle tasks in a more safe and efficient way than humanly possible.
Operating smarter
Autonomous forklifts are smart enough to safely drive and independently operate in the most dynamic warehouse and manufacturing environments. With advanced safety sensors and class-leading autonomous driving capabilities, this forklift of the future efficiently transports materials and navigates safely in dynamic environments, autonomously avoiding workers, vehicles and obstacles.
By seamlessly connecting to warehouse management system (WMS) or manufacturing execution system (MES) software, autonomous forklifts have the unmatched abilities to optimize the movement of goods and adapt to changes in real time by continuously re-mapping dynamic areas, eliminating user errors and human wait times.
The results? Increased operational savings and fast return on investment (ROI) with predictable performance and consistent throughput.
Predictable performance and consistent throughput are critical to operating successfully in today’s fast-paced distribution environment. Even at peak performance, the throughput, speed and accuracy that can be achieved manually are limited. This is especially true in today’s unusually tight labor market.
A whopping 490,000 industry openings, as reported by the U.S. Department of Labor, understates the number of warehouse workers needed to operate today’s distribution facilities. With the addition of autonomous forklifts, facilities can repurpose scarce labor, enabling them to remove operators from repetitive and dangerous tasks like manual forklift operation.
Operating safer
The biggest benefit of autonomous forklifts? Safety. Forklift accidents are one of the most common categories among workplace fatalities.
According to OSHA, the root causes of forklift accidents are a lack of proper training and oversight and a lax compliance with forklift safety.
With the ability to autonomously transport materials and navigate safely in dynamic environments removing the human element, autonomous forklifts eliminate the possibility of the most common cause of annual forklift accidents and fatalities – human error.
As reported in the 2021 Mobile Robot Market Report, OSHA states that, accidents, injuries and fatalities due to incidents with manual industrial trucks are a major driver for replacement of equipment by automated solutions, which, are often never involved in accidents.
Honeywell’s commitment to the advancement of operational safety
As a premier material handling equipment (MHE) automation supplier, system integrator and developer of industry-specific software, Honeywell Robotics is proud to offer automation solutions that are enabling facilities to safely achieve peak operational performance.
In strategic collaboration with OTTO Motors — a developer of autonomous mobile robots (AMRs) for material handling inside manufacturing facilities and warehouses — Honeywell Robotics offers a complete line of AMRs, including the OTTO Lifter, an autonomous forklift.
Discover the OTTO Lifter
Like all OTTO AMRs, the OTTO Lifter easily integrates into existing systems in as little as a few hours with minimal infrastructural changes; no tape, markers, wires or other guidance are needed for navigation. The OTTO Lifter’s industry-leading design and analysis tools have been designed from first-principles to capture the realities of high-performance mobile robots.
Designed for dynamic environments, the OTTO Lifter reduces the material handling costs of pallet transport workflows, all while increasing workplace safety. It features an intelligent pallet detection system for skewed, off-centered pallets and stretch-wrap covered entry notches, in addition to multiple LiDAR sensors and five 3D obstacle-detection cameras, giving it the unrivaled capabilities to detect obstacles and reroute to reliably deliver goods.
With the OTTO Lifter, palleted material handling processes that rely on forklifts are safer. Its navigation system is completely aware of its own size, velocity or any turning constraints in which it may be operating. And with an IEC61508-based, multi-layered test and validation infrastructure, ongoing development is regression-tested by design.
The abilities to autonomously transport materials and navigate safely in dynamic environments make the benefits of autonomous forklifts like the OTTO Lifter invaluable and lifesaving.
To subscribe to the Honeywell Intelligrated blog and get exclusive communications and updates, click here.